What is OSP PCB?
OSP (Organic Solderability Preservative) PCB is a type of surface finish applied to printed circuit boards (PCBs) to protect the exposed copper from oxidation and enhance solderability. The OSP coating is a thin, transparent layer of organic compounds that forms a protective barrier on the copper surface, preventing it from reacting with the environment and ensuring excellent solderability during the assembly process.
Advantages of OSP PCB Surface Finish
OSP PCB surface finish offers several advantages over other surface finishes, such as:
- Cost-effective: OSP is one of the most economical surface finishes available, making it an attractive option for budget-conscious projects.
- Flat surface: The thin OSP coating maintains a flat surface, which is essential for fine-pitch components and high-density designs.
- Excellent solderability: OSP provides excellent solderability, ensuring reliable connections between components and the PCB.
- Environmentally friendly: Unlike some other surface finishes, OSP is RoHS compliant and does not contain hazardous substances like lead or nickel.
- Quick assembly: OSP-coated PCBs are ready for immediate assembly, as the surface finish does not require additional preparation steps.
Comparison of OSP with Other Surface Finishes
Surface Finish | Cost | Shelf Life | Solderability | Environmental Impact |
---|---|---|---|---|
OSP | Low | 6-12 months | Excellent | Low |
ENIG | High | 12+ months | Excellent | Moderate |
HASL | Low | 6-12 months | Good | Moderate |
Immersion Tin | Moderate | 6-12 months | Good | Low |
Immersion Silver | Moderate | 6-12 months | Excellent | Low |
As seen in the table above, OSP offers a balance of cost, solderability, and environmental impact compared to other surface finishes.
The OSP PCB Surface Finish Process
The OSP PCB surface finish process involves several steps to ensure a high-quality protective coating on the exposed copper surfaces.
Step 1: Cleaning
Before applying the OSP coating, the PCB undergoes a thorough cleaning process to remove any contaminants, such as dirt, grease, or oxide layers. This step is crucial to ensure proper adhesion of the OSP coating to the copper surface.
Step 2: Micro-etching
After cleaning, the PCB is subjected to a micro-etching process, which slightly roughens the copper surface. This process helps to improve the OSP coating’s adhesion and ensures a more uniform coverage.
Step 3: OSP Application
The OSP coating is applied to the PCB using either a spraying or immersion method. In the spraying method, the OSP solution is sprayed onto the PCB surface, while in the immersion method, the PCB is dipped into a bath containing the OSP solution. Both methods result in a thin, uniform coating of the organic compounds on the exposed copper surfaces.
Step 4: Drying
After the OSP application, the PCB is dried using hot air or an infrared oven. This step ensures that any excess solution is removed and the OSP coating is fully cured, forming a stable protective layer on the copper surface.
Factors Affecting OSP PCB Performance
Several factors can influence the performance and reliability of OSP PCBs, including:
Storage Conditions
OSP PCBs are sensitive to environmental factors, such as humidity and temperature. Proper storage conditions are essential to maintain the OSP coating’s integrity and ensure optimal solderability. Ideally, OSP PCBs should be stored in a controlled environment with a relative humidity of 30-50% and a temperature range of 20-30°C.
Shelf Life
The shelf life of OSP PCBs is typically shorter compared to other surface finishes, such as ENIG or immersion silver. The organic compounds in the OSP coating can degrade over time, leading to reduced solderability and potential assembly issues. Generally, OSP PCBs have a shelf life of 6-12 months when stored under proper conditions.
Handling and Contamination
Proper handling of OSP PCBs is crucial to prevent contamination of the surface finish. Contaminants, such as skin oils, dirt, or dust, can compromise the OSP coating’s integrity and lead to solderability issues during assembly. It is recommended to handle OSP PCBs with gloves and store them in clean, dust-free environments.
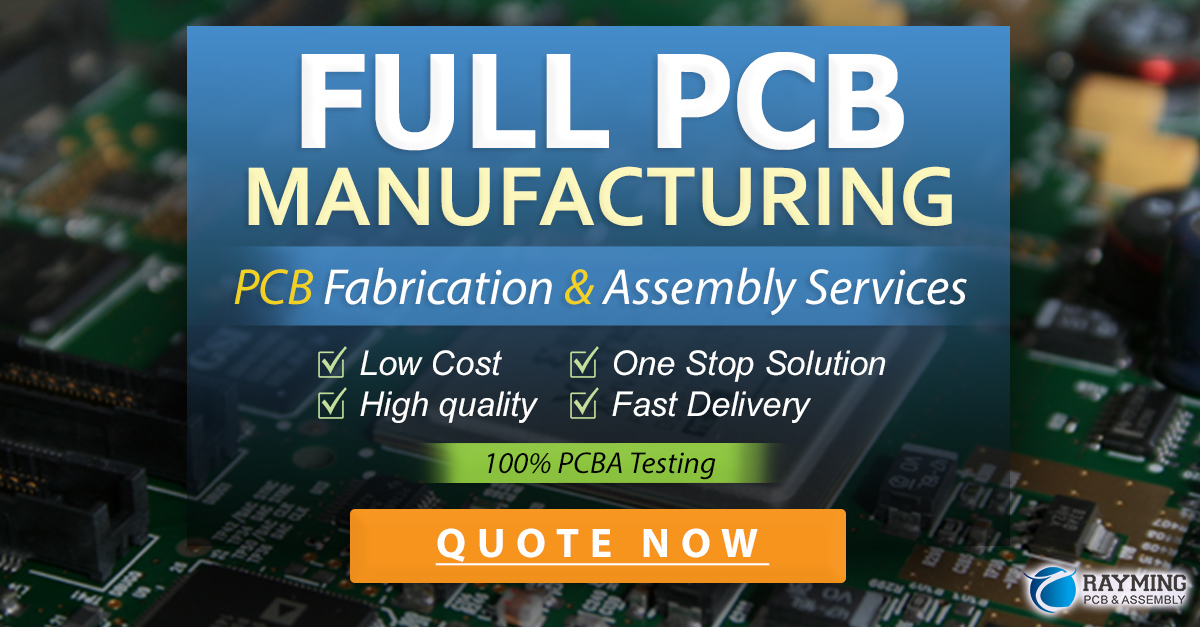
Soldering Considerations for OSP PCBs
When soldering components onto OSP PCBs, it is essential to consider several factors to ensure reliable connections and prevent assembly issues.
Solder Paste Selection
Selecting the appropriate solder paste is crucial for achieving optimal soldering results on OSP PCBs. The solder paste should be compatible with the OSP surface finish and have the correct particle size and flux composition. It is recommended to use a no-clean, lead-free solder paste with a moderate activation level to minimize the risk of solder defects and ensure proper wetting.
Soldering Temperature Profile
The soldering temperature profile plays a significant role in the success of the assembly process for OSP PCBs. It is essential to follow the recommended temperature profile provided by the solder paste manufacturer and consider the specific requirements of the components being soldered. A well-optimized temperature profile helps to minimize thermal stress on the components and ensures proper solder joint formation.
Reflow Process
During the reflow process, the OSP coating volatilizes, allowing the molten solder to wet the exposed copper surfaces and form reliable connections with the components. It is crucial to control the reflow process parameters, such as peak temperature, time above liquidus, and cooling rate, to achieve optimal solder joint quality and prevent defects like bridging or insufficient wetting.
Common Defects in OSP PCB Assembly
Despite the advantages of OSP PCBs, several common defects can occur during the assembly process if proper precautions are not taken.
Solder Bridging
Solder bridging is a defect where excess solder forms an unintended connection between two or more adjacent pads or traces. This defect can be caused by incorrect solder paste application, excessive solder volume, or improper reflow temperature profile. To prevent solder bridging, it is essential to control the solder paste deposition process and optimize the reflow temperature profile.
Insufficient Wetting
Insufficient wetting occurs when the molten solder does not adequately spread and adhere to the copper surface, resulting in weak or incomplete solder joints. This defect can be caused by contamination of the OSP surface, incorrect solder paste selection, or improper reflow temperature profile. To prevent insufficient wetting, it is essential to maintain a clean OSP surface, use compatible solder paste, and follow the recommended reflow temperature profile.
Dry Joints
Dry joints, also known as cold solder joints, are characterized by a dull, grainy appearance and poor mechanical strength. This defect can be caused by insufficient heat during the reflow process, contamination of the OSP surface, or improper solder paste selection. To prevent dry joints, it is crucial to ensure adequate heat transfer during reflow, maintain a clean OSP surface, and use compatible solder paste.
Frequently Asked Questions (FAQ)
-
Q: What is the shelf life of OSP PCBs?
A: The shelf life of OSP PCBs is typically 6-12 months when stored under proper conditions, such as a controlled environment with a relative humidity of 30-50% and a temperature range of 20-30°C. -
Q: Can OSP PCBs be reworked?
A: Yes, OSP PCBs can be reworked, but it is essential to follow proper rework procedures to ensure the integrity of the surface finish. Rework should be performed using compatible solder and flux, and the reworked area should be cleaned thoroughly to remove any residue. -
Q: How does OSP compare to other surface finishes in terms of cost?
A: OSP is one of the most cost-effective surface finishes available, making it an attractive option for budget-conscious projects. In comparison, ENIG (Electroless Nickel Immersion Gold) is more expensive, while HASL (Hot Air Solder Leveling) is similarly priced. -
Q: Is OSP suitable for high-temperature applications?
A: OSP PCBs are not recommended for high-temperature applications, as the organic compounds in the coating can degrade at elevated temperatures. For high-temperature applications, surface finishes like ENIG or immersion silver are more suitable. -
Q: Can OSP PCBs be used for fine-pitch components?
A: Yes, OSP PCBs are suitable for fine-pitch components due to the thin, flat nature of the surface finish. The OSP coating maintains a flat surface, which is essential for proper placement and soldering of fine-pitch components.
Conclusion
OSP PCB surface finish is a cost-effective and reliable option for protecting exposed copper surfaces and ensuring excellent solderability. By understanding the OSP process, storage requirements, and soldering considerations, manufacturers can optimize their assembly processes and minimize the risk of common defects. When properly implemented, OSP PCBs offer a balance of cost, performance, and environmental friendliness, making them a popular choice for a wide range of applications.
Leave a Reply