Introduction to Multilayer PCBs
In the rapidly evolving world of electronics, multilayer printed circuit boards (PCBs) have emerged as a game-changing technology. These complex boards, consisting of multiple layers of conductive and insulating materials, have revolutionized the way electronic devices are designed and manufactured. As the demand for smaller, faster, and more powerful electronic devices continues to grow, multilayer PCBs have become an indispensable component in the industry.
What are Multilayer PCBs?
Multilayer PCBs are printed circuit boards that consist of three or more conductive layers, separated by insulating layers. These layers are interconnected through small holes called vias, which allow electrical signals to pass between the different layers. The conductive layers are typically made of copper, while the insulating layers are made of materials such as FR-4, a glass-reinforced epoxy laminate.
Advantages of Multilayer PCBs
Multilayer PCBs offer several advantages over traditional single or double-layer boards:
- Increased Density: By utilizing multiple layers, designers can pack more components and circuitry into a smaller space, resulting in more compact and efficient devices.
- Improved Signal Integrity: The use of dedicated signal layers and ground planes in multilayer PCBs helps to reduce electromagnetic interference (EMI) and crosstalk, ensuring cleaner and more reliable signal transmission.
- Enhanced Thermal Management: The presence of multiple layers allows for better heat dissipation, as the copper layers can act as heat sinks, preventing overheating and improving the overall reliability of the device.
- Reduced Cost: Although the initial manufacturing cost of multilayer PCBs may be higher than single or double-layer boards, the increased density and functionality often lead to cost savings in the long run, as fewer boards and components are required.
Applications of Multilayer PCBs
Consumer Electronics
Multilayer PCBs have become ubiquitous in consumer electronics, from smartphones and tablets to laptops and gaming consoles. The ever-increasing demand for smaller, more powerful devices has driven the adoption of multilayer PCBs in this sector. For example, modern smartphones often feature boards with 8 or more layers, allowing for the integration of advanced components such as high-resolution cameras, 5G modems, and powerful processors.
Automotive Electronics
The automotive industry has also embraced multilayer PCBs, as vehicles become increasingly reliant on electronic systems for safety, performance, and entertainment. Multilayer boards are used in various automotive applications, including:
- Engine control units (ECUs)
- Advanced driver assistance systems (ADAS)
- Infotainment systems
- Vehicle networking and communication
The robust nature of multilayer PCBs, combined with their ability to handle high-speed signals and withstand harsh environmental conditions, makes them ideal for automotive applications.
Medical Devices
Multilayer PCBs have found extensive use in medical devices, where reliability and precision are of utmost importance. From diagnostic imaging equipment to wearable monitoring devices, multilayer boards enable the development of compact, high-performance medical electronics. The use of multilayer PCBs in medical devices has led to improved patient care, faster diagnosis, and more effective treatment options.
Aerospace and Defense
In the aerospace and defense industries, multilayer PCBs are used in a wide range of applications, including:
- Avionics systems
- Radar and surveillance equipment
- Satellite communication devices
- Missile guidance systems
The ability of multilayer PCBs to withstand extreme temperatures, vibrations, and other harsh environmental conditions makes them essential for these critical applications.
Manufacturing Process of Multilayer PCBs
The manufacturing process of multilayer PCBs is more complex than that of single or double-layer boards, involving several stages:
-
Design and Layout: The process begins with the design and layout of the board using specialized CAD software. The designer determines the number of layers, component placement, and routing of the traces.
-
Layer Fabrication: Each conductive layer is fabricated separately, typically using a photolithographic process. The desired pattern is transferred onto the copper-clad laminate using a photomask and then etched away, leaving only the desired traces.
-
Lamination: The individual layers are stacked together with insulating layers in between, and the entire stack is subjected to high pressure and temperature to bond the layers together.
-
Drilling and Plating: Holes are drilled through the board to create vias and component mounting holes. The holes are then plated with copper to establish electrical connections between the layers.
-
Solder Mask and Silkscreen: A solder mask is applied to the outer layers to protect the traces and prevent short circuits. A silkscreen layer is added to provide labels and markings for components.
-
Surface Finishing: The exposed copper areas are coated with a protective finish, such as HASL (Hot Air Solder Leveling), ENIG (Electroless Nickel Immersion Gold), or OSP (Organic Solderability Preservative), to prevent oxidation and improve solderability.
-
Electrical Testing: The completed board undergoes a series of electrical tests to ensure that all connections are correct and that there are no short circuits or open connections.
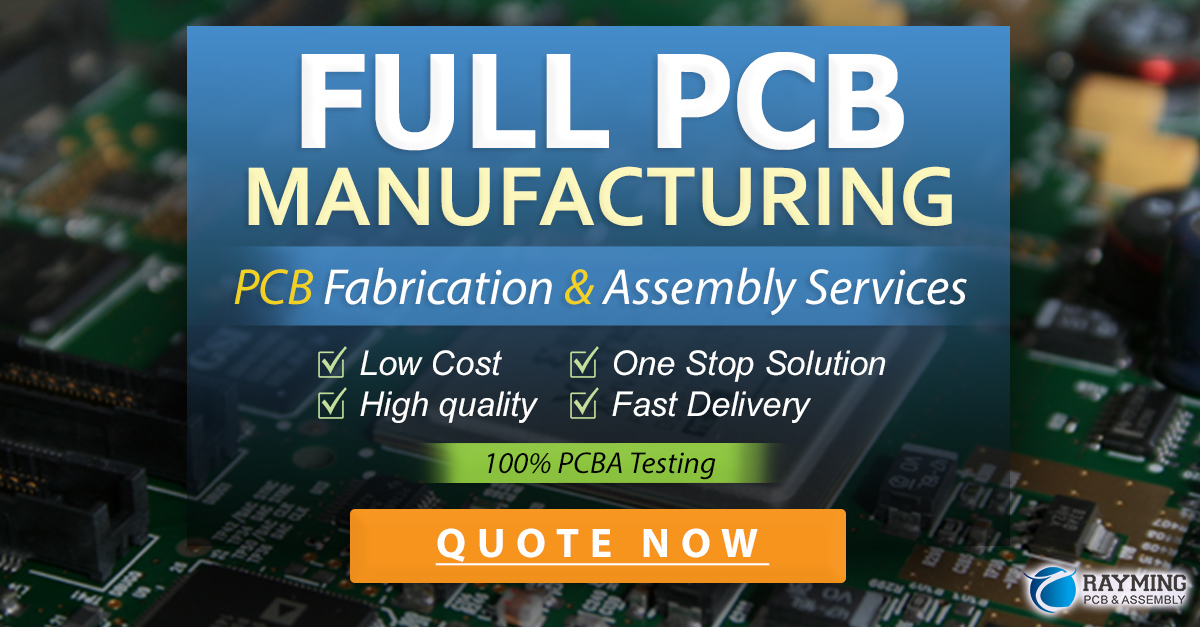
Challenges and Future Developments
Despite the numerous advantages of multilayer PCBs, there are still challenges that need to be addressed:
Signal Integrity
As the number of layers and the complexity of the board increase, maintaining signal integrity becomes more challenging. Designers must carefully consider factors such as impedance matching, crosstalk, and EMI to ensure reliable signal transmission.
Thermal Management
With the increasing power density of modern electronic components, thermal management becomes a critical issue. Designers must incorporate effective heat dissipation techniques, such as the use of thermal vias and heat spreaders, to prevent overheating and ensure the long-term reliability of the device.
Manufacturing Complexity
The manufacturing process of multilayer PCBs is inherently more complex than that of single or double-layer boards, requiring specialized equipment and expertise. This complexity can lead to higher manufacturing costs and longer lead times.
Despite these challenges, the future of multilayer PCBs looks bright. Ongoing research and development efforts are focused on addressing these challenges and pushing the boundaries of what is possible with multilayer PCB technology. Some of the key areas of focus include:
- Advanced materials: The development of new, high-performance materials, such as low-loss dielectrics and high-conductivity copper alloys, can help to improve signal integrity and thermal management.
- 3D printing: The use of 3D printing techniques, such as selective laser sintering (SLS) and stereolithography (SLA), can enable the creation of complex, three-dimensional multilayer structures, opening up new possibilities for electronic device design.
- Embedded components: The integration of passive components, such as resistors and capacitors, directly into the PCB layers can further increase density and reduce the overall size of the device.
- High-frequency applications: As the demand for high-speed, high-frequency devices continues to grow, multilayer PCBs will play an increasingly important role in enabling the development of 5G networks, millimeter-wave radar, and other advanced applications.
FAQ
- What is the difference between a multilayer PCB and a single or double-layer PCB?
-
A multilayer PCB consists of three or more conductive layers, separated by insulating layers, while a single or double-layer PCB has only one or two conductive layers, respectively. Multilayer PCBs offer increased density, improved signal integrity, and better thermal management compared to single or double-layer boards.
-
How many layers can a multilayer PCB have?
-
The number of layers in a multilayer PCB can vary depending on the application and the complexity of the design. Commonly, multilayer PCBs can have anywhere from 4 to 12 layers, but some high-end applications may require boards with 20 or more layers.
-
Are multilayer PCBs more expensive than single or double-layer PCBs?
-
Yes, the initial manufacturing cost of multilayer PCBs is generally higher than that of single or double-layer boards due to the increased complexity of the manufacturing process. However, the increased density and functionality of multilayer PCBs often lead to cost savings in the long run, as fewer boards and components are required.
-
What are some common applications of multilayer PCBs?
-
Multilayer PCBs are widely used in various industries, including consumer electronics (smartphones, laptops, gaming consoles), automotive electronics (engine control units, infotainment systems), medical devices (diagnostic imaging equipment, wearable monitoring devices), and aerospace and defense (avionics systems, radar and surveillance equipment).
-
What are the main challenges in designing and manufacturing multilayer PCBs?
- The main challenges in designing and manufacturing multilayer PCBs include maintaining signal integrity, ensuring effective thermal management, and dealing with the increased complexity of the manufacturing process. Designers must carefully consider factors such as impedance matching, crosstalk, and EMI, while manufacturers must have specialized equipment and expertise to produce high-quality multilayer boards.
Conclusion
Multilayer PCBs have revolutionized the electronics industry, enabling the development of smaller, faster, and more powerful devices. From consumer electronics to medical devices, automotive electronics, and aerospace and defense applications, multilayer PCBs have proven to be an essential component in driving technological advancements.
As the demand for more complex and high-performance electronic devices continues to grow, the importance of multilayer PCBs will only increase. Ongoing research and development efforts in areas such as advanced materials, 3D printing, embedded components, and high-frequency applications promise to push the boundaries of what is possible with multilayer PCB technology.
While challenges remain in terms of signal integrity, thermal management, and manufacturing complexity, the future of multilayer PCBs looks bright. As designers and manufacturers continue to innovate and overcome these challenges, multilayer PCBs will undoubtedly play a crucial role in shaping the future of electronics.
Leave a Reply