What is a Medical PCB?
A medical printed circuit board (PCB) is a specialized type of PCB designed and manufactured for use in medical devices and equipment. Medical PCBs are crucial components in a wide range of medical applications, from patient monitoring systems and diagnostic tools to implantable devices and surgical instruments.
Medical PCBs differ from standard PCBs in several key aspects, including:
- Reliability: Medical PCBs must be highly reliable and able to function consistently in critical, life-saving applications.
- Durability: These PCBs must withstand harsh environments, such as exposure to bodily fluids, chemicals, and sterilization processes.
- Regulatory compliance: Medical PCBs must adhere to strict regulatory standards, such as the FDA’s Quality System Regulation (QSR) and ISO 13485.
- Miniaturization: Many medical devices require compact, miniaturized PCBs to fit within small form factors.
Types of Medical PCBs
There are several types of medical PCBs, each designed for specific applications and requirements. Some common types include:
1. Flexible PCBs
Flexible PCBs, or flex PCBs, are made from flexible materials like polyimide, allowing them to bend and conform to various shapes. They are often used in wearable medical devices, such as patient monitoring systems and hearing aids.
2. Rigid-Flex PCBs
Rigid-flex PCBs combine both rigid and flexible sections, offering the benefits of both types of PCBs. They are ideal for applications that require both stability and flexibility, such as endoscopes and catheter-based devices.
3. High-Density Interconnect (HDI) PCBs
HDI PCBs feature fine pitch traces and small vias, enabling higher component density and miniaturization. They are commonly used in implantable devices, such as pacemakers and neurostimulators.
4. Multilayer PCBs
Multilayer PCBs consist of multiple layers of conductive and insulating materials, allowing for more complex circuitry and higher component density. They are used in a wide range of medical devices, from diagnostic imaging equipment to surgical robots.
Medical PCB Assembly Process
The medical PCB assembly process involves several key steps to ensure the highest quality and reliability:
1. Design and Layout
The first step in medical PCB assembly is designing the PCB layout. This involves creating a schematic diagram, selecting components, and determining the optimal placement and routing of traces. The design must adhere to regulatory standards and consider factors such as signal integrity, electromagnetic compatibility (EMC), and thermal management.
2. PCB Fabrication
Once the design is finalized, the PCB is fabricated using a multi-step process:
- Substrate preparation: The PCB substrate, typically made from FR-4 or polyimide, is cleaned and prepared for the subsequent steps.
- Copper cladding: A thin layer of copper is laminated onto the substrate.
- Patterning: The copper layer is selectively removed to create the desired circuit pattern, using photolithography and etching processes.
- Drilling: Holes are drilled through the PCB for through-hole components and vias.
- Plating: The holes are plated with copper to establish electrical connections between layers.
- Solder mask application: A protective solder mask is applied to the PCB surface, leaving exposed areas for component soldering.
- Silkscreen printing: Text and symbols are printed onto the PCB for component identification and assembly guidance.
3. Component Placement
After PCB fabrication, the components are placed onto the board using automated pick-and-place machines or manual placement for larger or more complex components. The placement process must be precise and accurate to ensure proper electrical connections and avoid component damage.
4. Soldering
The placed components are then soldered to the PCB using one of two primary methods:
- Wave soldering: The PCB is passed over a wave of molten solder, which flows onto the component leads and pads, creating electrical connections.
- Reflow soldering: Solder paste is applied to the pads, and the components are placed onto the paste. The PCB is then heated in a reflow oven, melting the solder and securing the components to the board.
5. Inspection and Testing
After soldering, the assembled PCB undergoes thorough inspection and testing to ensure quality and functionality. This may include:
- Visual inspection: The PCB is visually inspected for any defects, such as poor soldering, component misalignment, or damage.
- Automated optical inspection (AOI): An automated system uses cameras and image processing software to detect assembly defects.
- X-ray inspection: X-ray imaging is used to inspect solder joints and internal connections that are not visible from the surface.
- In-circuit testing (ICT): The PCB is connected to a test fixture that verifies the functionality of individual components and circuits.
- Functional testing: The assembled PCB is tested in its intended application to ensure proper operation and performance.
6. Conformal Coating and Potting
In some cases, the assembled medical PCB may require additional protection from environmental factors, such as moisture, chemicals, or physical damage. Conformal coating involves applying a thin, protective layer over the PCB surface, while potting involves encapsulating the PCB in a protective resin.
7. Sterilization
For medical PCBs that will be used in sterile environments or implanted in the body, sterilization is a critical step. Common sterilization methods include:
- Ethylene oxide (EtO) sterilization: The PCB is exposed to EtO gas, which kills microorganisms.
- Gamma radiation sterilization: The PCB is exposed to high-energy gamma radiation, which sterilizes the device.
- Autoclave sterilization: The PCB is subjected to high-pressure steam sterilization, suitable for devices that can withstand high temperatures and humidity.
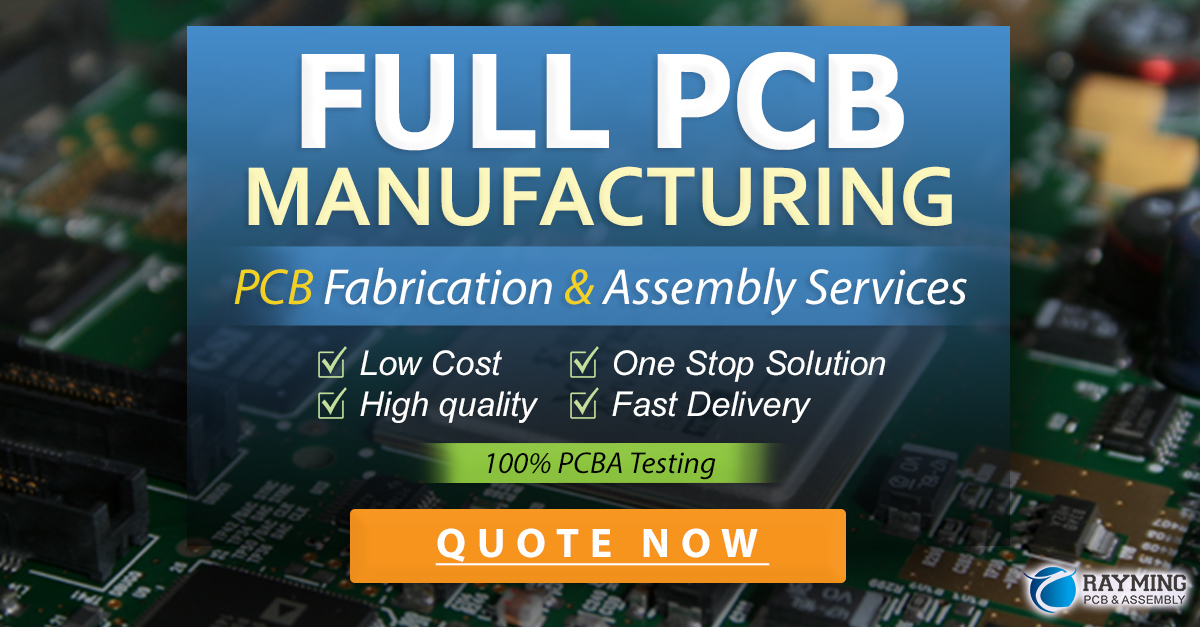
Challenges in Medical PCB Assembly
Medical PCB assembly presents several unique challenges compared to standard PCB assembly:
1. Regulatory Compliance
Medical PCBs must comply with strict regulatory standards, such as the FDA’s Quality System Regulation (QSR) and ISO 13485. These standards require rigorous documentation, traceability, and quality control throughout the assembly process.
2. Miniaturization
Many medical devices require compact, miniaturized PCBs to fit within small form factors. This can present challenges in component placement, soldering, and inspection, as well as thermal management and signal integrity.
3. Reliability and Durability
Medical PCBs must be highly reliable and durable, able to withstand harsh environments and function consistently in critical applications. This requires careful component selection, robust design, and thorough testing.
4. Supply Chain Management
Medical PCB assembly often involves specialized components and materials that may have longer lead times or limited availability. Effective supply chain management is crucial to ensure timely and cost-effective production.
Choosing a Medical PCB Assembly Partner
When selecting a medical PCB assembly partner, consider the following factors:
- Experience: Look for a partner with extensive experience in medical PCB assembly and a proven track record of success.
- Quality management: Ensure that the partner has a robust quality management system in place, including ISO 13485 certification and adherence to FDA regulations.
- Capabilities: Verify that the partner has the necessary equipment, expertise, and processes to handle your specific medical PCB assembly requirements.
- Communication and collaboration: Choose a partner that values open communication, transparency, and collaboration throughout the assembly process.
FAQ
1. What is the difference between a medical PCB and a standard PCB?
Medical PCBs are designed and manufactured to meet the specific requirements of medical devices and equipment, including high reliability, durability, regulatory compliance, and miniaturization. Standard PCBs may not be subject to the same rigorous standards and requirements.
2. What regulatory standards apply to medical PCB assembly?
Medical PCB assembly must comply with several regulatory standards, including the FDA’s Quality System Regulation (QSR), ISO 13485, and IEC 60601-1. These standards ensure the safety, efficacy, and quality of medical devices.
3. What types of medical devices use PCBs?
PCBs are used in a wide range of medical devices, including patient monitoring systems, diagnostic tools, imaging equipment, surgical instruments, implantable devices, and wearable medical technology.
4. How do I choose the right medical PCB assembly partner?
When selecting a medical PCB assembly partner, consider factors such as experience, quality management, capabilities, and communication. Look for a partner with a proven track record in medical PCB assembly, ISO 13485 certification, and the necessary equipment and expertise to meet your specific requirements.
5. What sterilization methods are used for medical PCBs?
Common sterilization methods for medical PCBs include ethylene oxide (EtO) sterilization, gamma radiation sterilization, and autoclave sterilization. The choice of sterilization method depends on the specific device, materials, and application requirements.
Conclusion
Medical PCB assembly is a complex and highly regulated process that requires specialized knowledge, equipment, and processes. By understanding the unique requirements and challenges of medical PCB assembly, and selecting the right assembly partner, medical device manufacturers can ensure the highest quality, reliability, and performance of their products.
As medical technology continues to advance, the demand for innovative, miniaturized, and highly reliable medical PCBs will only continue to grow. By staying at the forefront of medical PCB assembly best practices and technologies, manufacturers can position themselves for success in this dynamic and essential industry.
Leave a Reply