What are Medical PCBs?
Medical PCBs are specialized printed circuit boards designed and manufactured specifically for use in medical electronic devices. These PCBs must adhere to strict quality standards and regulations to ensure the safety and effectiveness of the medical devices they are used in. Medical PCBs are typically more complex than standard PCBs, as they often incorporate advanced features such as high-density interconnects, fine-pitch components, and specialized coatings to protect against harsh environments.
Classification of Medical PCBs
Medical PCBs are classified into three categories based on their intended use and the level of risk associated with their failure:
-
Class 1 Medical PCBs: These PCBs are used in non-critical medical devices that do not come into direct contact with patients, such as medical monitors and patient beds. Class 1 PCBs have the lowest risk associated with their failure and are subject to less stringent manufacturing requirements compared to Class 2 and Class 3 PCBs.
-
Class 2 Medical PCBs: Class 2 PCBs are used in medical devices that come into contact with patients but do not have a direct impact on their health or well-being. Examples of Class 2 medical devices include powered wheelchairs and dental equipment. These PCBs have higher manufacturing requirements than Class 1 PCBs but are not as stringent as Class 3 PCBs.
-
Class 3 Medical PCBs: Class 3 PCBs are used in critical medical devices that have a direct impact on a patient’s health and well-being. These devices include life support systems, implantable devices, and surgical equipment. Class 3 PCBs are subject to the most stringent manufacturing requirements and must undergo extensive testing and certification to ensure their reliability and safety.
Class 3 Circuit Boards: The Highest Standard for Medical PCBs
Class 3 circuit boards are the highest standard for medical PCBs, as they are used in critical medical devices that directly impact patient safety and well-being. These PCBs must be designed and manufactured to the highest quality standards to ensure their reliability and longevity.
Design Considerations for Class 3 Circuit Boards
When designing Class 3 circuit boards, several key factors must be considered to ensure their performance and reliability:
-
Material Selection: Class 3 PCBs must be constructed using high-quality, medical-grade materials that can withstand the harsh environments and sterilization processes common in medical settings. Common materials used in Class 3 PCBs include polyimide, FR-4, and ceramic substrates.
-
Component Selection: The components used in Class 3 PCBs must be of the highest quality and reliability. These components must be able to withstand the rigors of medical use and maintain their performance over extended periods. Commonly used components in Class 3 PCBs include high-reliability capacitors, resistors, and integrated circuits.
-
Layout and Routing: The layout and routing of Class 3 PCBs must be carefully designed to minimize signal interference, ensure proper grounding, and facilitate efficient heat dissipation. High-density interconnects and fine-pitch components are often used in Class 3 PCBs to maximize space efficiency and functionality.
-
Coatings and Finishes: Class 3 PCBs may require specialized coatings and finishes to protect against moisture, chemicals, and other environmental factors. Conformal coatings, such as parylene and silicone, are commonly used to provide an additional layer of protection for sensitive components.
Manufacturing Requirements for Class 3 Circuit Boards
The manufacturing process for Class 3 circuit boards is subject to stringent quality control measures and regulations to ensure the highest level of reliability and safety. Some of the key manufacturing requirements for Class 3 PCBs include:
-
Clean Room Environment: Class 3 PCBs must be manufactured in a clean room environment to minimize the risk of contamination and ensure the highest level of quality control. Clean rooms are classified based on the number of particles per cubic meter, with Class 100 being the most stringent standard for medical device manufacturing.
-
Automated Assembly: To minimize the risk of human error and ensure consistent quality, Class 3 PCBs are often assembled using automated equipment such as pick-and-place machines and reflow ovens. This automation helps to ensure precise component placement and soldering, reducing the likelihood of defects and failures.
-
Inspection and Testing: Class 3 PCBs undergo rigorous inspection and testing throughout the manufacturing process to identify and correct any defects or issues. Common inspection methods include automated optical inspection (AOI), X-ray inspection, and electrical testing. Additionally, Class 3 PCBs may be subjected to environmental stress testing to ensure their reliability under various operating conditions.
-
Traceability and Documentation: Detailed documentation and traceability are essential for Class 3 PCBs to ensure that any issues can be quickly identified and addressed. Manufacturers must maintain detailed records of the materials, components, and processes used in the production of each PCB, as well as any testing and inspection results.
Applications of Class 3 Circuit Boards in Medical Electronic Devices
Class 3 circuit boards are used in a wide range of critical medical electronic devices, where their high reliability and safety are essential. Some common applications of Class 3 PCBs include:
-
Life Support Systems: Class 3 PCBs are used in life support systems such as ventilators, heart-lung machines, and dialysis equipment. These devices require the highest level of reliability, as any failure could have severe consequences for the patient.
-
Implantable Devices: Implantable medical devices, such as pacemakers, defibrillators, and neurostimulators, rely on Class 3 PCBs to ensure their long-term performance and safety. These PCBs must be designed to withstand the harsh environment of the human body and maintain their functionality for extended periods.
-
Surgical Equipment: Class 3 PCBs are used in various surgical equipment, including electrosurgical units, surgical robots, and endoscopic devices. These PCBs must be able to withstand the rigors of the operating room environment and provide precise control and monitoring of the surgical instruments.
-
Diagnostic Imaging Equipment: Medical imaging devices, such as X-ray machines, CT scanners, and MRI systems, use Class 3 PCBs to ensure high-quality image acquisition and processing. These PCBs must be designed to handle the high data rates and complex signal processing required for medical imaging applications.
Table: Examples of Class 3 PCB Applications in Medical Electronic Devices
Device Category | Specific Devices | Key PCB Requirements |
---|---|---|
Life Support Systems | Ventilators, Heart-Lung Machines, Dialysis Equipment | High reliability, long-term performance, environmental resistance |
Implantable Devices | Pacemakers, Defibrillators, Neurostimulators | Biocompatibility, miniaturization, low power consumption |
Surgical Equipment | Electrosurgical Units, Surgical Robots, Endoscopic Devices | Precision control, environmental resistance, high-speed data processing |
Diagnostic Imaging Equipment | X-ray Machines, CT Scanners, MRI Systems | High data rates, complex signal processing, noise reduction |
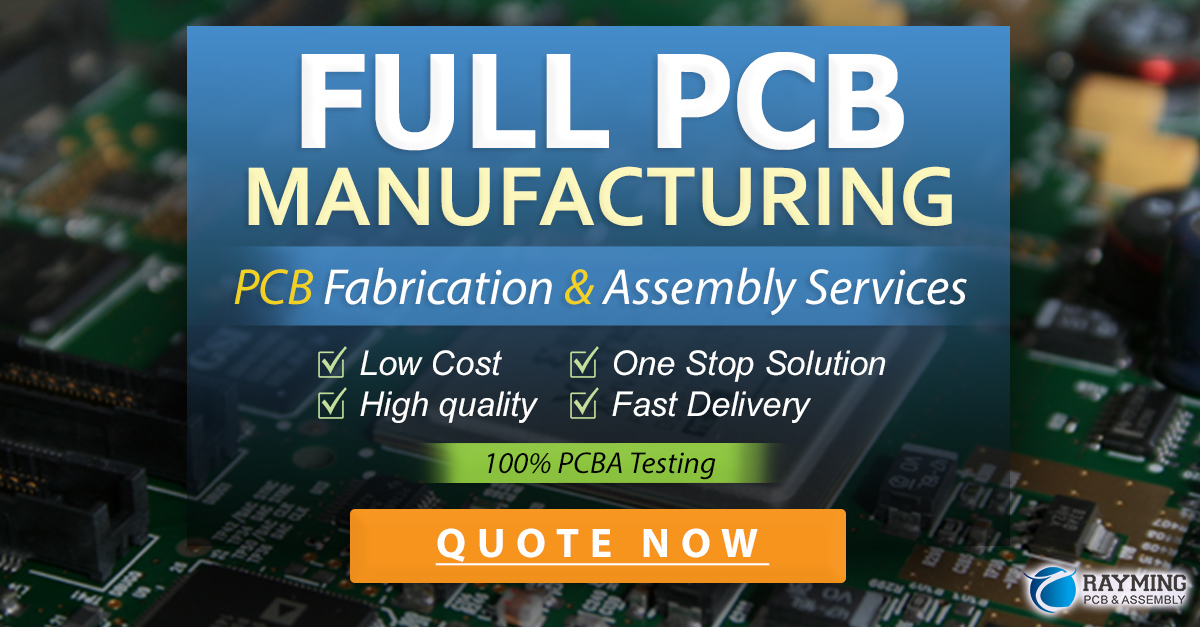
Challenges and Future Trends in Medical PCB Design and Manufacturing
As medical technology continues to advance, the design and manufacturing of Class 3 circuit boards face several challenges and opportunities for innovation.
Challenges in Medical PCB Design and Manufacturing
-
Miniaturization: As medical devices become smaller and more compact, PCB designers must find ways to incorporate more functionality into smaller form factors. This requires advanced manufacturing techniques and innovative component packaging solutions.
-
Regulatory Compliance: Medical PCBs are subject to strict regulatory requirements, which can vary by country and region. Keeping up with changing regulations and ensuring compliance can be a significant challenge for PCB manufacturers.
-
Cost Pressures: The high cost of medical devices is a concern for healthcare providers and patients alike. PCB designers and manufacturers must find ways to reduce costs without compromising quality or reliability.
Future Trends in Medical PCB Design and Manufacturing
-
Flexible and Stretchable PCBs: The development of flexible and stretchable PCBs is expected to revolutionize the design of wearable and implantable medical devices. These PCBs can conform to the shape of the human body and provide greater comfort and functionality for patients.
-
Wireless Connectivity: The integration of wireless connectivity, such as Bluetooth and Wi-Fi, into medical PCBs is becoming increasingly common. This allows for remote monitoring and control of medical devices, improving patient care and convenience.
-
Additive Manufacturing: Additive manufacturing techniques, such as 3D printing, are being explored for the production of medical PCBs. This technology has the potential to enable faster prototyping, greater design freedom, and more cost-effective manufacturing of complex PCB structures.
Frequently Asked Questions (FAQ)
-
Q: What is the difference between Class 2 and Class 3 medical PCBs?
A: Class 2 medical PCBs are used in devices that come into contact with patients but do not have a direct impact on their health or well-being, while Class 3 PCBs are used in critical devices that directly impact patient safety and well-being. Class 3 PCBs are subject to more stringent manufacturing requirements and testing than Class 2 PCBs. -
Q: What materials are commonly used in Class 3 medical PCBs?
A: Common materials used in Class 3 medical PCBs include polyimide, FR-4, and ceramic substrates. These materials are chosen for their high reliability, durability, and ability to withstand harsh medical environments. -
Q: Why is traceability important for Class 3 medical PCBs?
A: Traceability is crucial for Class 3 medical PCBs because it allows manufacturers to quickly identify and address any issues that may arise. By maintaining detailed records of the materials, components, and processes used in the production of each PCB, manufacturers can ensure the highest level of quality control and patient safety. -
Q: What are some of the challenges faced in the design and manufacturing of medical PCBs?
A: Some of the key challenges in medical PCB design and manufacturing include miniaturization, regulatory compliance, and cost pressures. As medical devices become smaller and more complex, PCB designers must find ways to incorporate more functionality into smaller form factors while ensuring compliance with strict regulatory requirements and managing costs. -
Q: How are flexible and stretchable PCBs expected to impact the medical device industry?
A: Flexible and stretchable PCBs have the potential to revolutionize the design of wearable and implantable medical devices. These PCBs can conform to the shape of the human body, providing greater comfort and functionality for patients. As this technology advances, it is expected to enable the development of new and innovative medical devices that improve patient care and outcomes.
Conclusion
Class 3 circuit boards represent the highest standard for medical PCBs, ensuring the reliability, safety, and performance of critical medical electronic devices. The design and manufacturing of these PCBs are subject to stringent quality control measures and regulations, requiring the use of high-quality materials, advanced manufacturing techniques, and rigorous testing and inspection processes.
As medical technology continues to evolve, the development of innovative PCB solutions, such as flexible and stretchable PCBs, wireless connectivity, and additive manufacturing, will play a crucial role in shaping the future of the medical device industry. By staying at the forefront of these technological advancements, PCB designers and manufacturers can contribute to the development of safer, more effective, and more accessible medical devices that improve patient care and outcomes.
Leave a Reply