Introduction: The Importance of Choosing the Right Solder
Soldering is a crucial process in the world of electronics, as it allows for the connection and assembly of various components on printed circuit boards (PCBs). The choice between lead-free and lead solder can significantly impact the quality, durability, and environmental impact of electronic devices. In this comprehensive guide, we will delve into the differences between lead-free and lead solder, their advantages and disadvantages, and help you make an informed decision when selecting the appropriate solder for your projects.
What is Solder?
Solder is a metal alloy used to create electrical and mechanical connections between electronic components. It is typically composed of tin and lead, although lead-free alternatives have gained popularity in recent years due to environmental and health concerns. The primary function of solder is to provide a conductive pathway for electrical current and to hold components securely in place on a PCB.
The History of Lead Solder
Lead solder has been the standard in the electronics industry for decades. The most common lead solder alloy is 63/37, which consists of 63% tin and 37% lead. This combination offers several advantages, such as:
- Low melting point (183°C)
- Excellent wetting properties
- Good electrical conductivity
- Strong mechanical bonds
However, the use of lead in solder has come under scrutiny due to its toxicity and potential harm to human health and the environment.
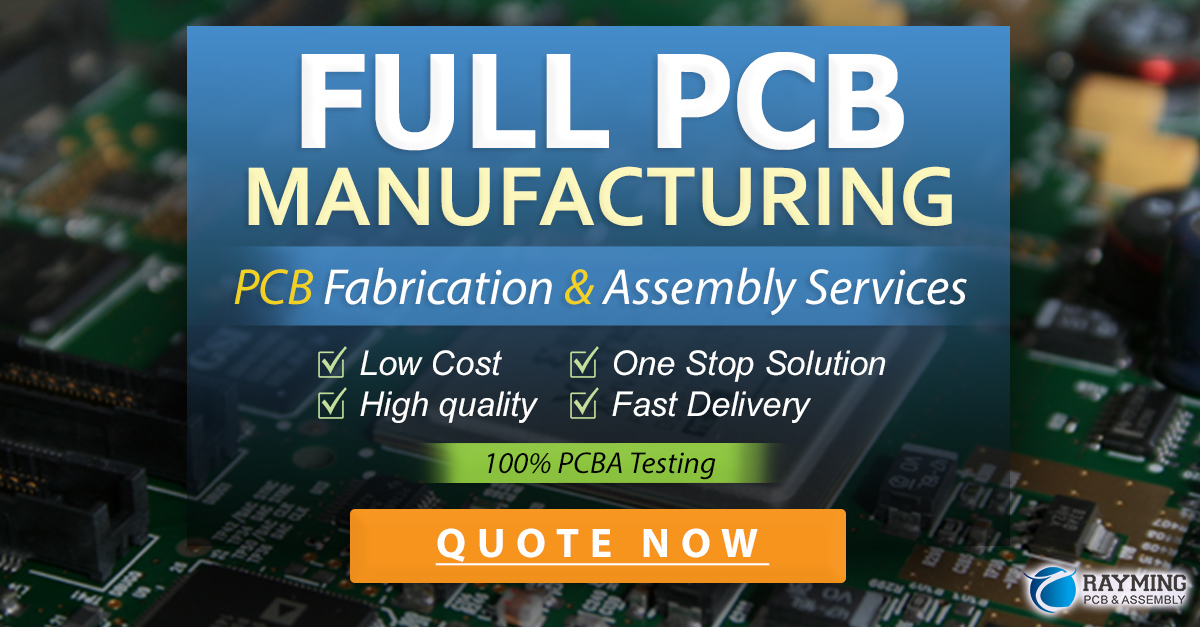
The Rise of Lead-Free Solder
In response to growing concerns about the use of lead, the electronics industry has shifted towards lead-free solder alternatives. The European Union’s Restriction of Hazardous Substances (RoHS) directive, introduced in 2006, played a significant role in this transition by restricting the use of lead and other hazardous materials in electronic products.
The most common lead-free solder alloys include:
- SAC305 (96.5% tin, 3% silver, 0.5% copper)
- SN100C (99.3% tin, 0.7% copper, with a small amount of nickel and germanium)
- SnCu (99.2% tin, 0.8% copper)
These alloys offer comparable performance to lead solder while minimizing the environmental and health risks associated with lead.
Advantages of Lead-Free Solder
1. Environmental Benefits
The primary advantage of lead-free solder is its reduced environmental impact. Lead is a toxic heavy metal that can accumulate in soil, water, and living organisms, causing harm to ecosystems and human health. By eliminating lead from solder, the electronics industry can minimize its contribution to lead pollution and promote a more sustainable future.
2. Compliance with Regulations
As mentioned earlier, the RoHS directive has made lead-free solder a requirement for many electronic products sold in the European Union. By adopting lead-free solder, manufacturers can ensure compliance with these regulations and avoid potential fines or legal issues.
3. Improved Reliability
Some lead-free solder alloys, such as SAC305, have been shown to offer better thermal cycling performance and improved resistance to tin whisker growth compared to lead solder. This can result in more reliable and durable electronic assemblies, particularly in harsh operating conditions.
Disadvantages of Lead-Free Solder
1. Higher Melting Point
Lead-free solder alloys generally have higher melting points than lead solder. For example, SAC305 has a melting point of 217-220°C, compared to 183°C for 63/37 lead solder. This higher melting point can lead to increased energy consumption during the soldering process and may require adjustments to soldering equipment and techniques.
2. Increased Cost
Lead-free solder alloys often contain more expensive materials, such as silver and copper, which can increase the overall cost of production. Additionally, the transition to lead-free solder may require investments in new equipment, training, and process optimization, further adding to the cost.
3. Compatibility Issues
Some lead-free solder alloys may not be compatible with certain components or PCB Finishes, leading to potential reliability issues. For example, tin-silver-copper alloys can be more prone to forming brittle intermetallic compounds with certain surface finishes, such as nickel-gold. Careful selection of materials and process optimization is necessary to mitigate these compatibility concerns.
Advantages of Lead Solder
1. Lower Melting Point
The lower melting point of lead solder (183°C for 63/37) can be advantageous in some situations. It requires less energy to melt and can be more forgiving when soldering temperature-sensitive components. The lower melting point also allows for faster soldering cycles, which can improve production efficiency.
2. Better Wetting Properties
Lead solder generally has better wetting properties than lead-free alternatives, meaning it flows and adheres to surfaces more easily. This can result in more consistent and reliable solder joints, particularly when working with less-than-ideal surface finishes or soldering conditions.
3. Established Process Knowledge
Lead solder has been used in the electronics industry for many years, and there is a wealth of knowledge and experience associated with its use. This can make it easier for manufacturers to troubleshoot issues and optimize their soldering processes when using lead solder.
Disadvantages of Lead Solder
1. Environmental and Health Risks
The primary disadvantage of lead solder is its toxic nature. Lead exposure can cause serious health problems, including damage to the nervous system, kidneys, and reproductive system. When electronic devices containing lead solder are improperly disposed of, the lead can leach into the environment, contaminating soil and water sources.
2. Regulatory Restrictions
As mentioned earlier, the use of lead in electronic products is restricted by the RoHS directive in the European Union and similar regulations in other parts of the world. Non-compliance with these regulations can result in fines, legal issues, and damage to a company’s reputation.
3. Limited Future Availability
As the electronics industry continues to shift towards lead-free solder, the availability of lead solder may become more limited in the future. This could lead to increased costs and supply chain challenges for manufacturers who continue to rely on lead solder.
Comparison of Lead-Free and Lead Solder Properties
Property | Lead-Free Solder (SAC305) | Lead Solder (63/37) |
---|---|---|
Melting Point | 217-220°C | 183°C |
Tensile Strength | 50-60 MPa | 40-50 MPa |
Electrical Conductivity | 6.8-7.2 μΩ·cm | 14.5-15.5 μΩ·cm |
Wetting Angle | 30-45° | 20-35° |
Thermal Cycling Performance | Better | Good |
Tin Whisker Resistance | Better | Good |
Environmental Impact | Lower | Higher |
Cost | Higher | Lower |
Choosing Between Lead-Free and Lead Solder
When deciding between lead-free and lead solder, several factors should be considered:
- Environmental and health considerations
- Regulatory requirements
- Performance requirements (e.g., thermal cycling, tin whisker resistance)
- Compatibility with components and PCB finishes
- Cost and availability
- Existing equipment and process knowledge
In most cases, lead-free solder is the preferred choice due to its reduced environmental impact and compliance with regulations. However, there may be specific applications where lead solder is still necessary, such as in high-reliability aerospace or military electronics.
Best Practices for Soldering with Lead-Free and Lead Solder
Regardless of the type of solder used, following best practices can help ensure high-quality, reliable solder joints:
- Use appropriate soldering equipment and tools
- Control soldering temperature and time
- Maintain clean and oxide-free surfaces
- Use proper fluxes and cleaning agents
- Provide adequate ventilation and personal protective equipment
- Regularly inspect and test solder joints for quality
By adhering to these best practices and carefully selecting the appropriate solder for each application, manufacturers can produce reliable, high-performance electronic assemblies while minimizing environmental and health risks.
Frequently Asked Questions (FAQ)
1. Is lead-free solder as reliable as lead solder?
In most cases, lead-free solder can provide comparable or even better reliability than lead solder, particularly in terms of thermal cycling performance and tin whisker resistance. However, the specific performance will depend on the alloy composition, soldering process, and application requirements.
2. Can I mix lead-free and lead solder?
Mixing lead-free and lead solder is generally not recommended, as it can lead to inconsistent melting temperatures, poor wetting, and reduced joint reliability. It is best to use either lead-free or lead solder consistently throughout an assembly.
3. How do I dispose of electronic devices containing lead solder?
Electronic devices containing lead solder should be disposed of through proper e-waste recycling channels. Many municipalities and electronics retailers offer e-waste recycling programs that ensure the safe handling and recycling of lead-containing components.
4. Are there any exemptions to the RoHS directive for lead solder use?
Yes, there are some exemptions to the RoHS directive that allow for the continued use of lead solder in specific applications, such as high-reliability aerospace and military electronics. However, these exemptions are limited and subject to periodic review.
5. Can I use the same soldering equipment for lead-free and lead solder?
In most cases, soldering equipment designed for lead solder can be used with lead-free solder, but some adjustments may be necessary to accommodate the higher melting temperatures of lead-free alloys. It is important to consult the equipment manufacturer’s guidelines and conduct thorough testing to ensure compatibility and optimal performance.
Conclusion
The choice between lead-free and lead solder is an important decision that can have significant implications for the environmental impact, regulatory compliance, and performance of electronic assemblies. While lead-free solder has become the preferred choice in most applications due to its reduced environmental and health risks, there may still be specific cases where lead solder is necessary.
By understanding the advantages, disadvantages, and properties of each type of solder, and following best practices for soldering processes, manufacturers can make informed decisions and produce reliable, high-quality electronic products while minimizing negative impacts on the environment and human health.
As the electronics industry continues to evolve, it is likely that lead-free solder will become increasingly prevalent, driven by stricter regulations and growing environmental awareness. By staying informed about the latest developments in solder technology and adapting their processes accordingly, manufacturers can remain competitive and contribute to a more sustainable future.
Leave a Reply