What is Immersion Gold?
Immersion gold, also known as electroless nickel immersion gold (ENIG), is a surface finishing process used in the production of printed circuit boards (PCBs). This process involves depositing a thin layer of gold over a nickel substrate through a chemical process, without the use of electrical current.
The immersion gold process typically consists of the following steps:
- Cleaning: The PCB surface is thoroughly cleaned to remove any contaminants or oxides.
- Microetching: A mild etching solution is used to roughen the surface and improve adhesion.
- Catalyzation: The surface is treated with a catalyst, usually palladium, to facilitate the deposition of nickel.
- Electroless nickel plating: A layer of nickel is deposited onto the surface through an autocatalytic chemical reaction.
- Immersion gold plating: The nickel-plated surface is immersed in a gold solution, where a thin layer of gold is deposited through a displacement reaction.
The resulting immersion gold finish is typically 0.05 to 0.2 microns thick and provides several benefits:
- Excellent solderability
- Good oxidation resistance
- Compatibility with Wire Bonding
- Flat and uniform surface finish
Advantages of Immersion Gold
- Provides a solderable surface without the need for additional surface preparation
- Offers good shelf life and oxidation resistance
- Suitable for fine-pitch components and wire bonding
- Produces a flat and uniform surface finish
Disadvantages of Immersion Gold
- Higher cost compared to other surface finishes
- Limited shelf life compared to gold plating
- Potential for black pad formation due to excessive nickel corrosion
- Not suitable for high-temperature applications
What is Gold Plating?
Gold plating, also known as electroplating or electrolytic gold plating, is a process where a layer of gold is deposited onto a conductive surface using an electric current. This process is widely used in the electronics industry for creating conductive and corrosion-resistant surfaces on PCBs, connectors, and other components.
The gold plating process involves the following steps:
- Cleaning: The surface is cleaned to remove any contaminants or oxides.
- Activation: The surface is treated with an activator solution to improve adhesion.
- Electroplating: The component is immersed in a gold plating solution and connected to the negative terminal of a Power Supply, while an anode is connected to the positive terminal. An electric current is applied, causing gold ions to migrate from the anode to the cathode (the component being plated), forming a layer of gold on the surface.
Gold plating can be applied directly onto copper or over a nickel underplate for improved durability and adhesion. The thickness of the gold layer can be controlled by adjusting the plating time and current density, typically ranging from 0.5 to 2.5 microns.
Advantages of Gold Plating
- Excellent conductivity and corrosion resistance
- Longer shelf life compared to immersion gold
- Suitable for high-temperature applications
- Thickness can be easily controlled and customized
- Lower cost compared to immersion gold
Disadvantages of Gold Plating
- Requires additional surface preparation for solderability
- May exhibit a less uniform surface finish compared to immersion gold
- Potential for porosity and nodule formation
- Not suitable for fine-pitch components and wire bonding
Key Differences Between Immersion Gold and Gold Plating
Parameter | Immersion Gold | Gold Plating |
---|---|---|
Process | Chemical deposition without electric current | Electrodeposition using electric current |
Thickness | Typically 0.05 to 0.2 microns | Typically 0.5 to 2.5 microns |
Solderability | Excellent, without additional surface preparation | Requires additional surface preparation |
Shelf Life | Limited, due to potential nickel corrosion | Longer, due to thicker gold layer |
Surface Finish | Flat and uniform | Less uniform, potential for porosity and nodules |
Suitability | Fine-pitch components and wire bonding | High-temperature applications |
Cost | Higher | Lower |
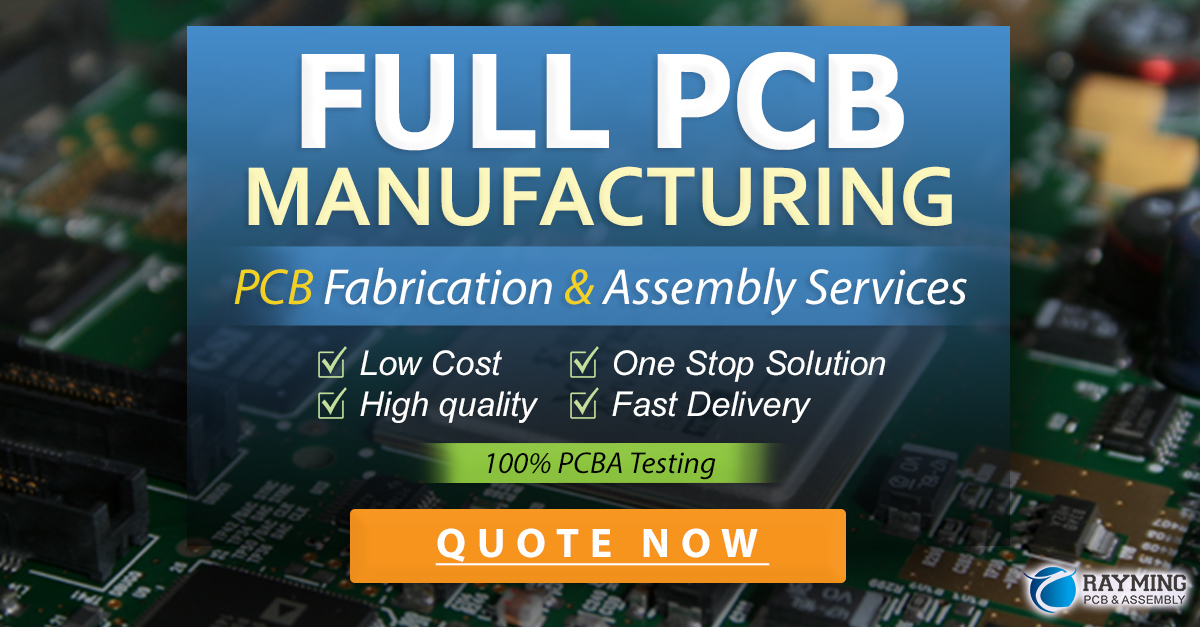
Distinguishing Between Immersion Gold and Gold Plating
To distinguish between immersion gold and gold plating, consider the following factors:
-
Visual appearance: Immersion gold typically has a more uniform and matte appearance, while gold plating may exhibit a brighter, more reflective finish.
-
Thickness measurement: Use non-destructive methods such as X-ray fluorescence (XRF) or beta backscatter to measure the gold thickness. Immersion gold is typically thinner (0.05-0.2 microns) compared to gold plating (0.5-2.5 microns).
-
Solder wettability test: Perform a solder wettability test to assess the solderability of the surface. Immersion gold generally exhibits excellent solderability without additional surface preparation, while gold plating may require surface preparation for optimal solderability.
-
Cross-sectional analysis: If destructive testing is possible, perform a cross-sectional analysis of the plated surface using microscopy techniques such as scanning electron microscopy (SEM) or energy-dispersive X-ray spectroscopy (EDS). This can reveal the presence of a nickel underplate in the case of immersion gold, and the overall thickness and uniformity of the gold layer.
-
Documentation: Refer to the manufacturing specifications or documentation provided by the PCB or component manufacturer, which should indicate the type of surface finish used.
Frequently Asked Questions (FAQ)
-
Q: Can immersion gold be used for high-temperature applications?
A: Immersion gold is not recommended for high-temperature applications due to its limited thermal stability and potential for nickel diffusion. Gold plating is a better choice for high-temperature applications. -
Q: Is it possible to apply gold plating over immersion gold?
A: Yes, it is possible to apply gold plating over immersion gold. However, this is not a common practice and may not provide significant benefits. It is essential to ensure proper adhesion and compatibility between the two finishes. -
Q: Which surface finish is better for fine-pitch components?
A: Immersion gold is generally preferred for fine-pitch components and wire bonding applications due to its flat and uniform surface finish. Gold plating may not provide the same level of surface uniformity required for these applications. -
Q: How does the cost of immersion gold compare to gold plating?
A: Immersion gold is typically more expensive than gold plating due to the additional processing steps involved, such as electroless nickel plating. However, the cost difference may vary depending on the specific application and production volume. -
Q: Can immersion gold and gold plating be used interchangeably?
A: While both immersion gold and gold plating provide a conductive and corrosion-resistant surface finish, they have distinct properties and are not always interchangeable. The choice between the two depends on the specific application requirements, such as solderability, shelf life, thermal stability, and surface uniformity.
Conclusion
Immersion gold and gold plating are two popular surface finishing processes used in the electronics industry, each with its own advantages and disadvantages. Immersion gold offers excellent solderability, surface uniformity, and suitability for fine-pitch components, but has a higher cost and limited shelf life. Gold plating, on the other hand, provides a thicker gold layer, longer shelf life, and lower cost, but may require additional surface preparation for solderability and is not suitable for fine-pitch applications.
To distinguish between immersion gold and gold plating, consider factors such as visual appearance, thickness measurement, solder wettability, cross-sectional analysis, and manufacturing documentation. Understanding the key differences between these two surface finishes is crucial for selecting the most appropriate option based on the specific application requirements and constraints.
Leave a Reply