Introduction to Wire-to-Board Connections
Connecting wires to a circuit board is a fundamental skill in electronics. Whether you’re a hobbyist or a professional, knowing how to properly wire-to-board can save you time and ensure your projects function correctly. In this comprehensive guide, we’ll cover everything you need to know about making wire-to-board connections.
What is a Wire-to-Board Connection?
A wire-to-board connection is a method of attaching a wire to a printed circuit board (PCB). This connection allows electrical signals and power to flow between the wire and the components on the board. Wire-to-board connections are used in a wide range of electronic devices, from simple DIY Projects to complex industrial systems.
Why are Wire-to-Board Connections Important?
Wire-to-board connections are critical for several reasons:
- They provide a secure, reliable way to connect wires to a PCB.
- They ensure proper electrical contact between the wire and the board.
- They help prevent short circuits and other electrical issues.
- They make it easier to troubleshoot and repair electronic devices.
Types of Wire-to-Board Connections
There are several methods for making wire-to-board connections, each with its own advantages and disadvantages. Here are the most common types:
Through-Hole Soldering
Through-hole soldering involves inserting the wire into a hole drilled in the PCB and soldering it in place. This method provides a strong, reliable connection but requires more time and skill than other methods.
Surface Mount Soldering
Surface mount soldering involves attaching the wire directly to a pad on the surface of the PCB. This method is faster and easier than through-hole soldering but may not be as secure.
Wire Wrapping
Wire wrapping involves wrapping the wire tightly around a square post on the PCB. This method provides a secure connection without soldering but can be time-consuming and may not be suitable for all applications.
Crimping
Crimping involves attaching a terminal to the end of the wire and then inserting the terminal into a connector on the PCB. This method is fast and easy but requires specialized tools and connectors.
Tools and Materials Needed for Wire-to-Board Connections
To make wire-to-board connections, you’ll need the following tools and materials:
- Soldering iron and solder
- Wire strippers
- Wire cutters
- Pliers
- Flux (optional)
- Heat shrink tubing (optional)
- PCB with appropriate connection points
- Wires of appropriate gauge and length
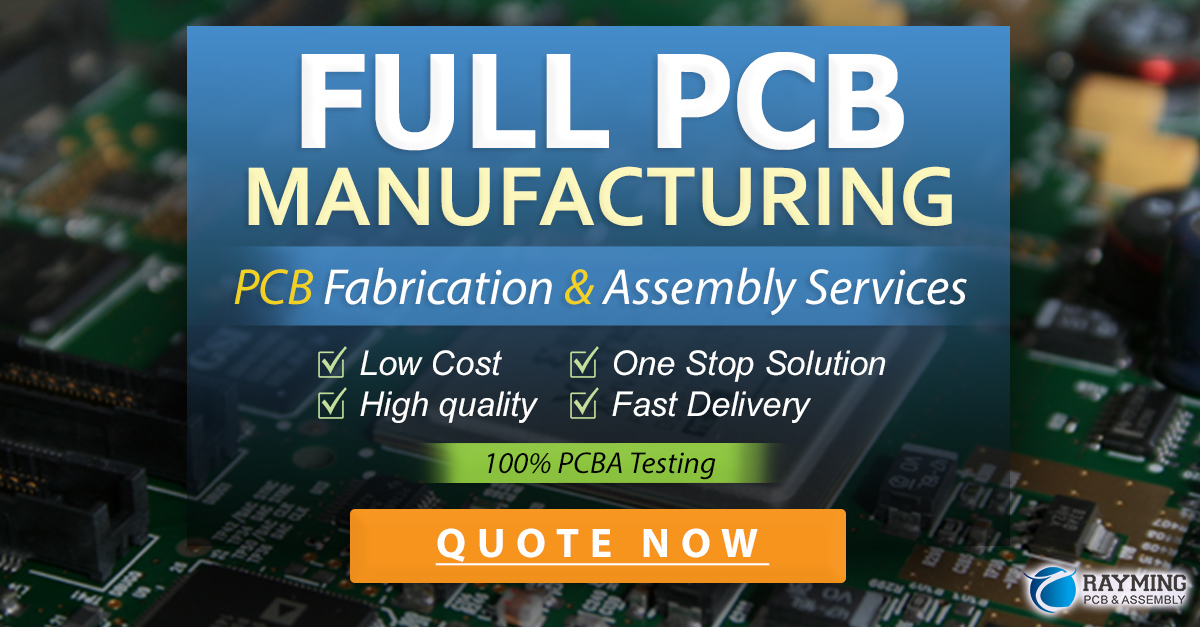
Step-by-Step Guide to Making Wire-to-Board Connections
Now that you know the basics of wire-to-board connections, let’s walk through the process step-by-step.
Step 1: Prepare the Wire
- Cut the wire to the appropriate length, leaving some extra for strain relief.
- Strip the insulation from both ends of the wire using wire strippers. Be careful not to nick or damage the conductor.
- If using stranded wire, twist the strands together to prevent fraying.
- Apply flux to the stripped ends of the wire (optional).
Step 2: Prepare the PCB
- Identify the appropriate connection point on the PCB (e.g., through-hole, surface mount pad, etc.).
- Clean the connection point with isopropyl alcohol to remove any dirt or oxidation.
- Apply a small amount of solder to the connection point (optional).
Step 3: Make the Connection
The specific steps for making the connection will depend on the type of connection you’re using.
Through-Hole Soldering
- Insert the stripped end of the wire into the hole in the PCB.
- Hold the wire in place with pliers or a helping hand tool.
- Touch the soldering iron to the wire and the pad simultaneously.
- Apply solder to the joint, allowing it to flow around the wire and pad.
- Remove the soldering iron and let the joint cool.
Surface Mount Soldering
- Bend the stripped end of the wire into a small hook.
- Place the hook on the surface mount pad.
- Touch the soldering iron to the wire and pad simultaneously.
- Apply solder to the joint, allowing it to flow around the wire and pad.
- Remove the soldering iron and let the joint cool.
Wire Wrapping
- Strip a longer length of insulation from the end of the wire (about 1 inch).
- Bend the stripped end of the wire at a 90-degree angle.
- Insert the bent end of the wire into the hole in the square post.
- Wrap the wire tightly around the post, making several turns.
- Trim the excess wire with wire cutters.
Crimping
- Insert the stripped end of the wire into the barrel of the terminal.
- Use a crimping tool to compress the barrel around the wire.
- Insert the terminal into the appropriate connector on the PCB.
- Ensure the terminal is fully seated and secure.
Step 4: Inspect and Test the Connection
- Visually inspect the connection to ensure it is secure and free of defects.
- Use a Multimeter to test the continuity between the wire and the PCB.
- Apply heat shrink tubing over the connection for added insulation and strain relief (optional).
Tips and Best Practices for Wire-to-Board Connections
Here are some tips and best practices to keep in mind when making wire-to-board connections:
- Always use the appropriate gauge wire for the current and voltage requirements of your project.
- Keep wire lengths as short as possible to minimize resistance and signal degradation.
- Use different colors of wire to help identify connections and make troubleshooting easier.
- When soldering, use a temperature-controlled soldering iron and high-quality solder.
- Avoid overheating the wire or PCB, as this can damage components or cause short circuits.
- Use flux when soldering to help the solder flow more easily and create a stronger joint.
- When wire wrapping, use a wire wrapping tool to ensure consistent tension and a secure connection.
- Always double-check your connections before applying power to the circuit.
- Label wires and connections clearly to make future maintenance and troubleshooting easier.
Common Mistakes to Avoid in Wire-to-Board Connections
Here are some common mistakes to avoid when making wire-to-board connections:
- Using the wrong gauge wire for the application
- Stripping too much or too little insulation from the wire
- Applying too much or too little solder to the joint
- Overheating the wire or PCB during soldering
- Failing to secure the wire properly, leading to strain on the joint
- Not testing the connection before applying power to the circuit
- Forgetting to label wires and connections for future reference
Troubleshooting Wire-to-Board Connection Issues
If you encounter issues with your wire-to-board connections, here are some steps you can take to troubleshoot the problem:
- Visually inspect the connection for any obvious defects or damage.
- Use a multimeter to test the continuity between the wire and the PCB.
- Check for any loose or broken wires or terminals.
- Ensure the wire gauge is appropriate for the application.
- Reflow the solder joint if necessary, adding flux if needed.
- Check for any short circuits or unintended connections between components.
- Consult the schematic or wiring diagram for your project to ensure connections are correct.
Advanced Wire-to-Board Connection Techniques
Once you’ve mastered the basics of wire-to-board connections, you may want to explore some more advanced techniques, such as:
- Using crimp terminals and housings for a more modular and reusable connection system
- Employing IDC (insulation displacement connector) for fast and solderless connections
- Utilizing edge connectors for connecting multiple wires to a PCB simultaneously
- Implementing cable assemblies and harnesses for organizing and routing multiple wires
- Applying strain relief techniques, such as using cable ties or cable glands, to prevent damage to connections
Frequently Asked Questions (FAQ)
- What is the best method for connecting a wire to a PCB?
-
The best method depends on the specific requirements of your project, such as the current and voltage levels, the available space on the PCB, and the desired level of reliability. Through-hole soldering is often considered the most secure and reliable method, but surface mount soldering, wire wrapping, and crimping can also be effective in certain situations.
-
Can I use any type of wire for wire-to-board connections?
-
No, it’s important to choose the appropriate gauge and type of wire for your application. Factors to consider include the current and voltage requirements, the operating temperature, and the environmental conditions (e.g., moisture, vibration, etc.). Using the wrong type of wire can lead to poor performance, overheating, or even fire hazards.
-
How much insulation should I strip from the wire?
-
The amount of insulation to strip depends on the type of connection you’re making. For through-hole soldering, you typically want to strip about 1/4 to 1/2 inch of insulation. For surface mount soldering, you may only need to strip about 1/8 inch. When wire wrapping, you’ll need to strip a longer length, about 1 inch, to provide enough wire to wrap around the post securely.
-
What should I do if my soldered joint is weak or prone to breaking?
-
If your soldered joint is weak, you may need to reflow the solder and add more to create a stronger bond. Make sure to apply flux to help the solder flow more easily. If the joint is still weak, you may need to use a larger gauge wire or a different type of connection altogether. Also, ensure that you’re not putting too much strain on the joint, which can cause it to break over time.
-
Can I use wire-to-board connections for high-current applications?
- Wire-to-board connections can be used for high-current applications, but you need to choose the appropriate gauge wire and connection method. Through-hole soldering with a large gauge wire is often the best choice for high-current applications. You may also need to use multiple wires in parallel to distribute the current and prevent overheating. Always consult the specifications for your components and the relevant safety standards when designing high-current circuits.
Conclusion
Wire-to-board connections are a critical skill for anyone working with electronics. By understanding the different types of connections, the tools and materials required, and the best practices for making secure and reliable connections, you can ensure your projects function correctly and safely. Remember to choose the appropriate connection method for your application, use the right gauge wire, and always test your connections before applying power. With practice and attention to detail, you can master the art of wire-to-board connections and take your electronics projects to the next level.
Additional Resources
- Soldering Tutorial for Beginners
- Wire Wrapping Techniques
- Crimping Techniques for Wire-to-Board Connections
- PCB Design Guidelines for Wire-to-Board Connections
Connection Method | Advantages | Disadvantages |
---|---|---|
Through-Hole Soldering | Strong, reliable connection | Time-consuming, requires soldering skills |
Surface Mount Soldering | Faster and easier than through-hole | May not be as secure |
Wire Wrapping | Secure connection without soldering | Time-consuming, may not be suitable for all applications |
Crimping | Fast and easy, requires no soldering | Requires specialized tools and connectors |
Leave a Reply