Understanding PCB Flux and Its Importance in Electronics Manufacturing
Printed Circuit Boards (PCBs) are essential components in modern electronics, providing a platform for electrical connections and mechanical support for various components. During the PCB Assembly process, flux is used to facilitate soldering and ensure proper bonding between components and the board. However, after soldering, residual flux can cause issues if not properly cleaned. In this comprehensive guide, we will discuss the importance of PCB Flux Cleaning and provide step-by-step instructions on how to effectively clean flux from PCBs.
What is PCB Flux?
PCB flux is a chemical compound used during the soldering process to improve the wetting properties of molten solder, allowing it to flow more easily and adhere to the PCB and component surfaces. Flux also helps to remove oxides and other contaminants from the surfaces being soldered, ensuring a strong and reliable bond.
Types of PCB Flux
There are three main types of PCB flux:
- Rosin-based flux
- Water-soluble flux
- No-clean flux
Each type of flux has its own characteristics, advantages, and disadvantages, as summarized in the table below:
Flux Type | Characteristics | Advantages | Disadvantages |
---|---|---|---|
Rosin-based | – Contains rosin, a natural resin derived from pine trees – Requires cleaning after soldering |
– Provides excellent wetting and soldering performance – Suitable for high-reliability applications |
– Leaves residue that must be cleaned – Cleaning process can be time-consuming and costly |
Water-soluble | – Contains organic acids and other water-soluble compounds – Requires cleaning after soldering |
– Easy to clean using water or mild solvents – Provides good wetting and soldering performance |
– Residue can cause corrosion if not thoroughly cleaned – Not suitable for all PCB materials |
No-clean | – Contains a low level of solid residue – Does not require cleaning after soldering |
– Eliminates the need for post-soldering cleaning – Reduces manufacturing time and costs |
– May not provide as strong a bond as other flux types – Some residue may still be present on the PCB |
Why is PCB Flux Cleaning Important?
Cleaning flux from PCBs is crucial for several reasons:
-
Preventing corrosion: Flux residue can be corrosive, especially if exposed to moisture or high humidity. Over time, this corrosion can lead to component failure and reduce the overall reliability of the PCB.
-
Improving electrical performance: Flux residue can act as an insulator, causing issues with electrical performance, such as increased resistance or signal interference.
-
Enhancing visual inspection: Clean PCBs are easier to visually inspect for defects, ensuring higher quality control standards.
-
Meeting industry standards: Many industries, such as aerospace, military, and medical, have strict cleanliness requirements for PCBs to ensure optimal performance and reliability.
PCB Flux Cleaning Methods
There are several methods for cleaning flux from PCBs, each with its own advantages and disadvantages. The most common methods include:
1. Manual Cleaning
Manual cleaning involves using a brush, swab, or lint-free cloth to apply a cleaning solution to the PCB and remove flux residue. This method is suitable for small-scale production or prototyping, as it is relatively inexpensive and does not require specialized equipment.
To manually clean flux from a PCB:
- Select an appropriate cleaning solution based on the type of flux used (e.g., isopropyl alcohol for rosin-based flux, deionized water for water-soluble flux).
- Dip a brush, swab, or lint-free cloth into the cleaning solution.
- Gently scrub the PCB surface, focusing on areas with visible flux residue.
- Use a clean, lint-free cloth to wipe away the cleaning solution and dissolved flux residue.
- Allow the PCB to air dry completely before further handling or processing.
2. Ultrasonic Cleaning
Ultrasonic cleaning uses high-frequency sound waves to agitate a cleaning solution, creating microscopic bubbles that implode and release energy, effectively removing flux residue and other contaminants from the PCB surface.
To clean a PCB using an ultrasonic cleaner:
- Fill the ultrasonic cleaner with a suitable cleaning solution, such as deionized water or a specialized PCB Cleaning solution.
- Place the PCB into the cleaning solution, ensuring it is fully submerged.
- Set the ultrasonic cleaner to the appropriate time and temperature settings, as recommended by the manufacturer or cleaning solution supplier.
- After the cleaning cycle is complete, remove the PCB from the solution and rinse it with deionized water to remove any remaining cleaning solution.
- Allow the PCB to air dry completely or use a clean, lint-free cloth to gently dry the surface.
3. Spray Cleaning
Spray cleaning involves using a pressurized spray of cleaning solution to remove flux residue from the PCB surface. This method is suitable for larger-scale production and can be automated for increased efficiency.
To clean a PCB using a spray cleaner:
- Place the PCB into a spray cleaning machine or onto a suitable surface for manual spray cleaning.
- Select an appropriate cleaning solution based on the type of flux used and the recommendations of the spray cleaning equipment manufacturer.
- Apply the cleaning solution to the PCB surface using the spray cleaner, ensuring even coverage.
- Allow the cleaning solution to dwell on the surface for the recommended time, as specified by the manufacturer or cleaning solution supplier.
- Rinse the PCB with deionized water to remove any remaining cleaning solution and flux residue.
- Allow the PCB to air dry completely or use a clean, lint-free cloth to gently dry the surface.
Selecting the Right Cleaning Solution
Choosing the appropriate cleaning solution is crucial for effectively removing flux residue from PCBs. The selection process should consider factors such as the type of flux used, the PCB material, and the cleaning method employed.
Some common cleaning solutions for PCBs include:
- Isopropyl alcohol (IPA): Suitable for removing rosin-based flux residue and general cleaning of PCBs.
- Deionized water: Effective for cleaning water-soluble flux residue and is safe for most PCB materials.
- Specialized PCB cleaners: Commercially available solutions designed specifically for removing flux residue and other contaminants from PCBs. These cleaners may be tailored for specific flux types or PCB materials.
When selecting a cleaning solution, always consult the manufacturer’s recommendations and safety data sheets (SDS) to ensure compatibility with your specific PCB and flux combination.
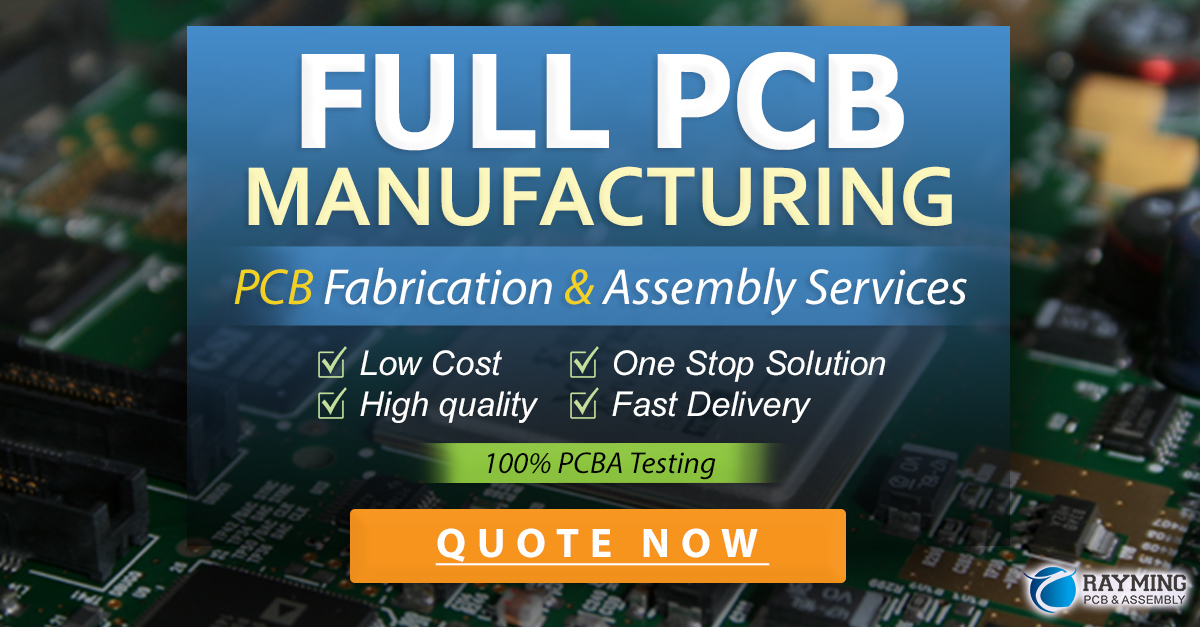
Best Practices for PCB Flux Cleaning
To ensure optimal results and maintain the integrity of your PCBs during the flux cleaning process, consider the following best practices:
-
Use the appropriate cleaning method and solution: Select a cleaning method and solution that is compatible with your PCB material and flux type to avoid damage and ensure effective cleaning.
-
Follow manufacturer recommendations: Adhere to the manufacturer’s guidelines for cleaning solution concentration, exposure time, and temperature to achieve the best results and prevent PCB Damage.
-
Wear personal protective equipment (PPE): Always wear appropriate PPE, such as gloves and safety glasses, when handling cleaning solutions and performing PCB cleaning to protect yourself from potential hazards.
-
Ensure thorough drying: Allow PCBs to dry completely after cleaning to prevent moisture-related issues, such as corrosion or electrical shorts.
-
Regularly maintain cleaning equipment: Keep your cleaning equipment in good working order by following the manufacturer’s maintenance guidelines and replacing worn or damaged parts as needed.
-
Monitor cleanliness levels: Regularly assess the cleanliness of your PCBs using visual inspection or specialized testing methods to ensure that your cleaning process is effective and meets the required standards.
Frequently Asked Questions (FAQ)
-
Q: Can I use household cleaners to clean flux from my PCBs?
A: It is not recommended to use household cleaners for PCB flux removal, as they may contain ingredients that can damage the PCB or leave residues that interfere with electrical performance. Always use cleaning solutions specifically designed for PCBs and flux removal. -
Q: How often should I clean flux from my PCBs?
A: The frequency of flux cleaning depends on factors such as the type of flux used, the PCB application, and the industry cleanliness standards. In general, it is best to clean flux residue as soon as possible after soldering to prevent corrosion and ensure optimal performance. -
Q: Can I reuse my PCB cleaning solution?
A: Reusing PCB cleaning solutions is not recommended, as the solution may become contaminated with dissolved flux residue and other particles over time, reducing its effectiveness and potentially leading to cross-contamination of PCBs. Always use fresh cleaning solution for each cleaning session. -
Q: How do I know if my PCBs are adequately cleaned?
A: Visual inspection is often sufficient to determine if a PCB is free of flux residue. However, for critical applications or to meet specific industry standards, specialized testing methods such as ionic contamination testing or surface insulation resistance (SIR) testing may be required. -
Q: Can I use an ultrasonic cleaner for all types of PCBs?
A: While ultrasonic cleaning is generally safe for most PCBs, some delicate components or PCB materials may be sensitive to the high-frequency vibrations. Always consult the PCB manufacturer’s recommendations and test the cleaning method on a small, non-critical area of the PCB before applying it to the entire board.
Conclusion
Cleaning flux from PCBs is a critical step in the electronics manufacturing process, ensuring the reliability, performance, and longevity of the final product. By understanding the different types of flux, cleaning methods, and best practices, you can effectively remove flux residue and maintain the integrity of your PCBs. Always select the appropriate cleaning solution and method for your specific PCB and flux combination, and follow manufacturer recommendations to achieve the best results. Regular cleaning and monitoring of cleanliness levels will help you maintain the highest quality standards for your PCBs and end products.
Leave a Reply