Flexible printed circuit boards (flex PCBs or flex circuits) are made from flexible dielectric materials with conductive copper traces on one or both sides. The copper thickness can vary based on the application requirements. This article explores the typical copper thickness used in flex PCBs and the factors that determine the appropriate thickness.
Typical Copper Thickness in Flex PCBs
The most common copper thickness used for flex PCBs is 1⁄2 oz (18 μm) or 1 oz (35 μm) copper.
Typical Copper Thickness Used in Flex PCBs
Copper Thickness | Microns | Ounces |
---|---|---|
18 μm | 1⁄2 oz | |
35 μm | 1 oz |
Thinner 1⁄4 oz (9 μm) copper may be used for simple flex circuits with minimal current requirements. Thicker 1⁄2 oz or 2 oz copper is sometimes used for high current applications.
Here is a quick overview of the typical copper thickness ranges used in flexible PCBs:
- 1⁄4 oz (9 μm) – Simple low power flex circuits
- 1⁄2 oz (18 μm) – Most common thickness for typical flex PCBs
- 1 oz (35 μm) – Also very common for many flex circuit designs
- 2 oz (70 μm) – For high current flex PCBs
Factors That Determine Copper Thickness
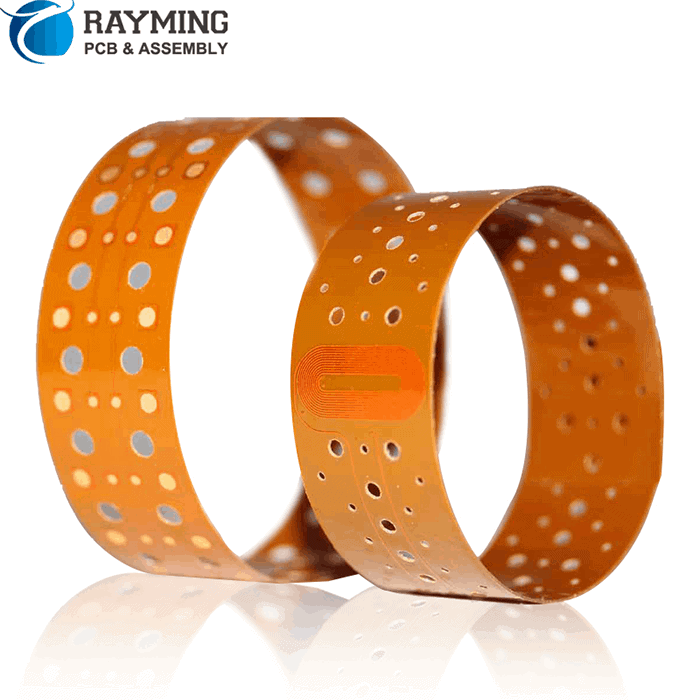
Several factors go into determining the appropriate copper thickness for a particular flex PCB design:
Current Carrying Capacity
The primary factor is the required current carrying capacity. Thicker copper can handle higher current levels without overheating. High power circuits may need 2 oz copper for adequate current capacity. Simpler low power flex circuits can utilize thinner 1⁄4 oz copper.
Mechanical Properties
Thinner copper is more flexible, while thicker copper is stiffer. This can impact the ability to fold or bend the flex PCB. Critical flexing areas may require thinner 1⁄2 oz copper. Stiffener areas may utilize thicker 1 oz copper.
Cost
Thicker copper is more expensive. Using a thinner 1⁄2 oz copper where possible can help reduce costs. Critical high current areas may require thicker copper, while lower current areas can be thinner.
Manufacturing Considerations
The capabilities of the flex PCB manufacturer are considered. Not all factories can produce very thin 1⁄4 oz copper reliably. Design within their process capabilities.
Reliability Requirements
Thicker copper provides better resistance to corrosion and fatigue over long term use. Mission critical flex circuits may utilize 1 oz copper for enhanced reliability.
Layer Count
Multilayer flex PCBs require thinner copper to control the total thickness. 1⁄2 oz copper is common for multilayer flex.
Copper Weight Conversion
Here is a quick reference for converting between copper thickness in microns, ounces, and mils:
Copper Thickness Conversion
Microns | Ounces | Mils |
---|---|---|
9 μm | 1⁄4 oz | 0.36 mil |
18 μm | 1⁄2 oz | 0.72 mil |
35 μm | 1 oz | 1.4 mil |
70 μm | 2 oz | 2.8 mil |
Copper Thickness Specification
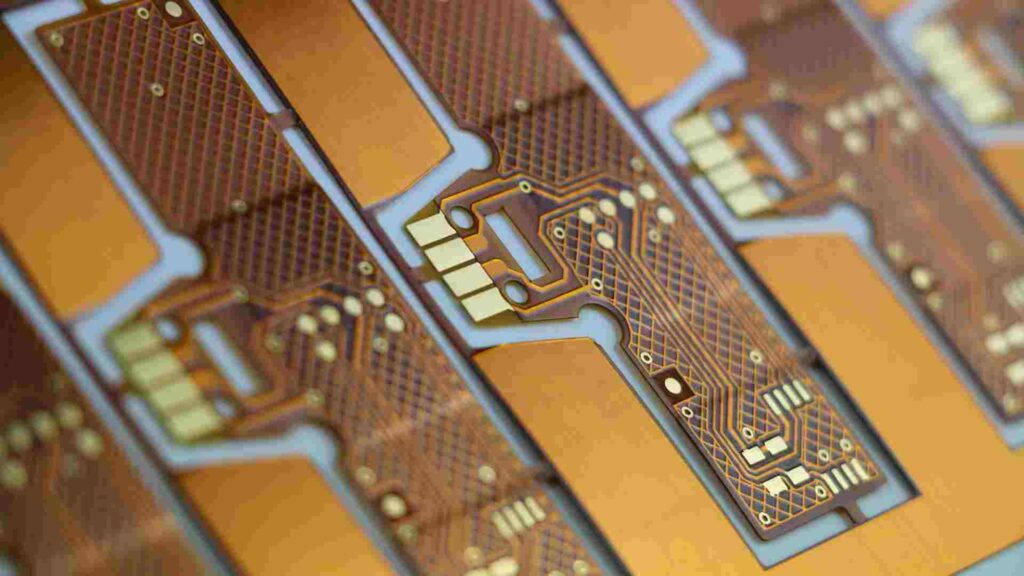
When designing your flex PCB, pay close attention to specifying the required copper thickness for each layer. Clearly communicate the desired thickness for cover layers, inner layers, and traces in the design files.
Verify any minimum copper thickness requirements with your flex PCB manufacturer’s capabilities before finalizing the design.
Carefully review board house quality reports and cross-sections to ensure the fabricated boards meet the specified copper thicknesses. Paying attention to copper weight during the design, communication, and quality assurance stages helps avoid potential issues.
Design Considerations for Copper Thickness
Here are some key points to consider when selecting copper thickness in your flex PCB design:
- Use thinner copper in dynamic flexing areas to prevent cracking
- Utilize thicker copper for high current carrying conductors
- Balance cost vs reliability needs for each circuit area
- Keep within board house manufacturing capabilities
- Account for any minimum trace/space needs
- Consider conductivity, flexibility, and reliability
- Review design guides from material suppliers
- Verify final thickness during inspection
Effects of Too Thin or Too Thick Copper
Using copper that is too thin or too thick for a particular flex PCB application can cause problems:
Effects of Too Thin Copper
- Insufficient current capacity results in overheating
- More susceptibility to corrosion over time
- Traces may crack more easily from dynamic bending
Effects of Too Thick Copper
- May lack flexibility required for dynamic areas
- Increased stiffness prevents routing in tight areas
- Can increase costs unnecessarily
- Excessive thickness stresses plated through holes
Careful selection of the optimal copper thickness helps avoid these types of issues.
Frequently Asked Questions
Here are some common questions about copper thickness in flexible PCBs:
What is the most common copper thickness used in flex PCBs?
The most common copper thickness used for typical flex PCB applications is 1⁄2 oz (18 μm). This provides a good balance of flexibility, conductivity, and cost.
How thick can the copper get in a flex PCB?
Flexible circuits can be fabricated with a range of copper thicknesses from 1⁄4 oz (9 μm) up to 2 oz (70 μm) or potentially thicker for specialized high current applications.
Is 1 oz copper too thick for a flex PCB?
1 oz (35 μm) copper is not necessarily too thick for many flex PCB designs. It provides good conductivity and robustness. As long as the flex circuit does not require tight dynamic bending, 1 oz copper may be suitable.
Can you use 1⁄2 oz copper for high current?
While thicker copper is typically required for high current, 1⁄2 oz may be sufficient if the traces are wide enough. Carefully consider the current density to determine if 1⁄2 oz can handle the expected load.
What are the tradeoffs between thinner and thicker copper?
Thinner copper allows for greater flexibility and reduced costs but may sacrifice some conductivity and reliability. Thicker copper provides higher current capacity and robustness but reduces bendability and increases costs.
Conclusion
Determining the appropriate copper thickness for your flex PCB design involves balancing flexibility, conductivity, manufacturability, and cost requirements. 1⁄2 oz and 1 oz copper are most commonly used, with 2 oz for high current designs. Carefully consider current capacity, mechanical, reliability, and cost factors. Clearly communicate desired copper thicknesses and verify the fabricated board meets specifications. With the right copper thickness, your flex circuit can deliver reliable performance in demanding dynamic applications.
Leave a Reply