Introduction to PCB Electrical Testing
Printed Circuit Boards (PCBs) are the backbone of modern electronics, found in everything from smartphones and laptops to medical devices and aerospace systems. To ensure that these critical components function reliably and meet stringent quality standards, PCB manufacturers employ a range of testing methods, with electrical testing being one of the most crucial. In this article, we will delve into the world of PCB electrical testing, exploring its importance, the various techniques used, and the benefits it brings to the manufacturing process.
The Importance of Electrical Testing in PCB Manufacturing
Electrical testing is an essential step in the PCB manufacturing process, as it helps to identify and eliminate defects that could lead to device malfunction or failure. By thoroughly testing each PCB for electrical continuity, short circuits, open circuits, and other issues, manufacturers can ensure that only high-quality, fully functional boards make it to the final product. This not only improves the reliability and performance of the end-user devices but also helps to minimize costly recalls and warranty claims.
Key Benefits of PCB Electrical Testing
- Early detection of defects
- Improved product quality and reliability
- Reduced manufacturing costs
- Enhanced customer satisfaction
- Compliance with industry standards and regulations
Types of PCB Electrical Tests
There are several types of electrical tests performed during the PCB manufacturing process, each designed to identify specific issues and ensure the overall quality of the board. Some of the most common PCB electrical tests include:
1. Continuity Testing
Continuity testing is used to verify that all the intended connections on a PCB are present and functioning correctly. This test checks for open circuits, ensuring that current can flow uninterrupted through the desired paths. Continuity testing is typically performed using a Multimeter or a dedicated Continuity Tester.
2. Short Circuit Testing
Short circuit testing is designed to identify any unintended connections between conductors on a PCB. These shorts can occur due to manufacturing defects, such as solder bridges or conductive debris, and can cause serious problems in the final product. Short circuit testing is often performed using a dedicated short circuit tester or an in-circuit test (ICT) system.
3. Resistance Testing
Resistance testing measures the opposition to current flow in a PCB’s conductors and components. This test helps to ensure that the board’s electrical characteristics match the design specifications and that there are no defects that could affect performance. Resistance testing is typically performed using a multimeter or an ICT system.
4. Dielectric Withstanding Voltage (DWV) Testing
DWV testing, also known as hipot testing, is used to verify the insulation between conductors on a PCB. This test applies a high voltage between different points on the board to ensure that there is no breakdown in the insulation, which could lead to shorts or other issues. DWV testing is critical for ensuring the safety and reliability of high-voltage applications.
5. Functional Testing
Functional testing is a comprehensive test that verifies the overall functionality of a PCB. This test typically involves powering up the board and testing its various functions, such as input/output, signal processing, and communication. Functional testing is often performed using specialized test fixtures and software.
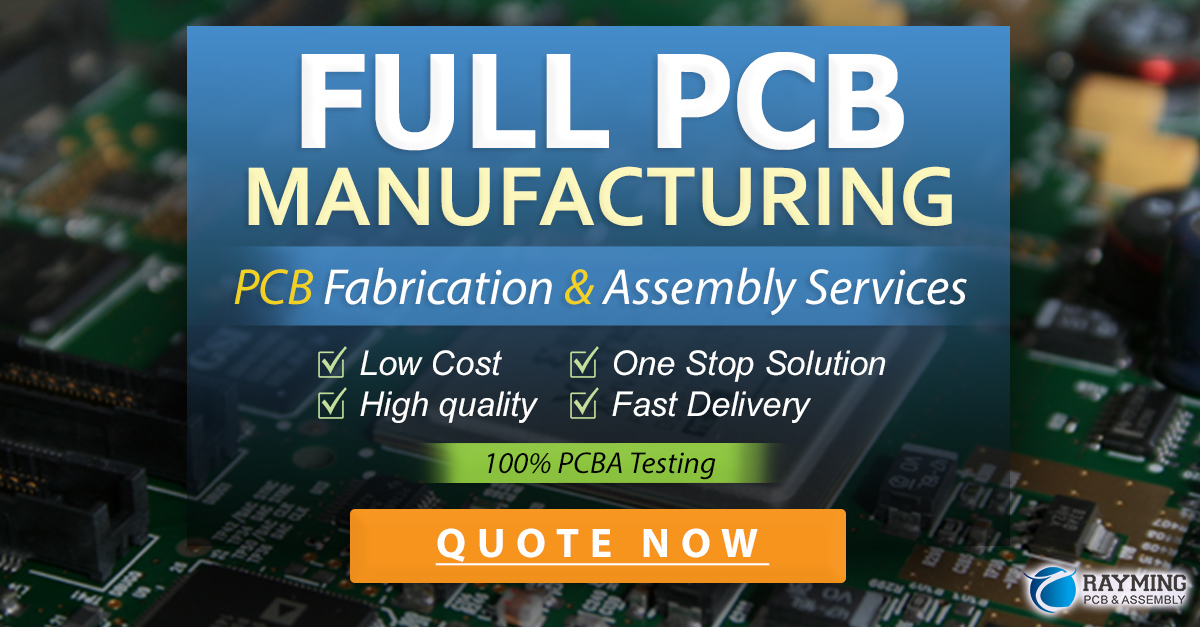
PCB Electrical Testing Methods
PCB electrical testing can be performed using various methods, each with its own advantages and limitations. The choice of testing method depends on factors such as the complexity of the board, the required test coverage, and the available resources. Some of the most common PCB electrical testing methods include:
1. Manual Testing
Manual testing involves using handheld tools, such as multimeters and oscilloscopes, to manually test individual points on a PCB. This method is suitable for low-volume production and prototype testing but can be time-consuming and prone to human error.
2. Automated Testing
Automated testing uses specialized equipment and software to perform electrical tests on PCBs. This method is faster, more accurate, and more repeatable than manual testing, making it ideal for high-volume production. Some common automated testing methods include:
a. In-Circuit Testing (ICT)
ICT uses a bed-of-nails fixture to make contact with specific points on a PCB, allowing the test system to verify the presence and functionality of individual components and circuits. ICT is highly effective at detecting manufacturing defects but requires a custom fixture for each PCB design.
b. Flying Probe Testing
Flying probe testing uses movable probes to make contact with points on a PCB, allowing for greater flexibility than ICT. This method is well-suited for low-volume production and prototype testing, as it does not require a custom fixture. However, flying probe testing is generally slower than ICT.
c. Boundary Scan Testing
Boundary scan testing, also known as JTAG testing, uses a built-in test access port (TAP) to test the interconnections and functionality of digital components on a PCB. This method is highly effective at detecting manufacturing defects and can be performed without physical access to the board. However, boundary scan testing requires compatible components and design considerations.
Implementing Electrical Testing in the PCB Manufacturing Process
To effectively implement electrical testing in the PCB manufacturing process, it is essential to consider the following factors:
- Test coverage: Ensure that the chosen testing methods provide adequate coverage of the PCB’s electrical characteristics and functionality.
- Test planning: Develop a comprehensive test plan that outlines the specific tests to be performed, the test sequence, and the acceptance criteria.
- Equipment and software: Invest in high-quality test equipment and software that is compatible with the PCB designs and manufacturing process.
- Operator training: Provide thorough training to test operators to ensure that they can perform the tests consistently and interpret the results accurately.
- Continuous improvement: Regularly review and update the electrical testing process to incorporate new technologies, address any issues, and optimize efficiency.
Electrical Testing Standards and Regulations
PCB electrical testing is subject to various industry standards and regulations, which ensure the safety, reliability, and compatibility of electronic products. Some of the key standards and regulations related to PCB electrical testing include:
- IPC-9252A: Base Material Electrical Test Methods for PCBs
- IPC-TM-650: Test Methods Manual for PCBs
- IEC 61189-3: Test Methods for Electrical Materials, Printed Boards, and Other Interconnection Structures
- UL 796: Standard for Printed Wiring Boards
Compliance with these standards and regulations is essential for ensuring the quality and marketability of PCB-based products.
FAQ
1. What is the difference between continuity testing and short circuit testing?
Continuity testing checks for open circuits, ensuring that current can flow through the intended paths on a PCB. Short circuit testing, on the other hand, identifies any unintended connections between conductors that could cause problems in the final product.
2. Can all PCBs be tested using the same methods?
No, the choice of testing method depends on factors such as the complexity of the board, the required test coverage, and the available resources. Different PCB designs may require different testing approaches to ensure comprehensive coverage and accurate results.
3. How often should electrical testing be performed during the PCB manufacturing process?
The frequency of electrical testing depends on the specific manufacturing process and quality control requirements. Typically, electrical testing is performed at multiple stages, such as after initial board fabrication, after component assembly, and before final packaging. Some manufacturers may also perform sample testing on a per-batch basis.
4. What are the consequences of not performing adequate electrical testing on PCBs?
Inadequate electrical testing can lead to a range of problems, including:
- Increased defect rates and product failures
- Higher manufacturing costs due to rework and scrap
- Delayed product launches and reduced time-to-market
- Damage to brand reputation and customer relationships
- Potential safety hazards and legal liabilities
5. How can manufacturers ensure the effectiveness of their PCB electrical testing process?
To ensure the effectiveness of PCB electrical testing, manufacturers should:
- Develop a comprehensive test plan that covers all relevant electrical characteristics and functionalities
- Invest in high-quality test equipment and software that is compatible with their PCB designs and manufacturing process
- Provide thorough training to test operators to ensure consistent and accurate test execution
- Regularly review and update the testing process to incorporate new technologies and address any issues
- Monitor test results and use the data to drive continuous improvement initiatives
Conclusion
Electrical testing is a critical component of the PCB manufacturing process, ensuring that only high-quality, fully functional boards make it to the final product. By employing a range of testing methods and adhering to industry standards and regulations, manufacturers can minimize defects, improve reliability, and enhance customer satisfaction. As electronic devices continue to become more complex and demanding, the importance of effective PCB electrical testing will only continue to grow, making it a key focus area for manufacturers seeking to stay competitive in today’s fast-paced, quality-driven market.
Test Type | Purpose | Method |
---|---|---|
Continuity Testing | Verify intended connections | Multimeter or continuity tester |
Short Circuit Testing | Identify unintended connections | Short circuit tester or ICT |
Resistance Testing | Measure opposition to current flow | Multimeter or ICT |
DWV Testing | Verify insulation between conductors | High-voltage tester |
Functional Testing | Verify overall board functionality | Specialized test fixtures and software |
Table 1: Common PCB Electrical Tests and Their Characteristics
Testing Method | Advantages | Limitations |
---|---|---|
Manual Testing | Suitable for low-volume and prototype testing | Time-consuming and prone to human error |
In-Circuit Testing (ICT) | Highly effective at detecting manufacturing defects | Requires a custom fixture for each PCB design |
Flying Probe Testing | Greater flexibility than ICT, no custom fixture needed | Slower than ICT |
Boundary Scan Testing | Can test without physical access to the board | Requires compatible components and design considerations |
Table 2: Comparison of PCB Electrical Testing Methods
Leave a Reply