Understanding the Basics of Voltage Regulation
Before we dive into the specifics of the AVR PCB circuit, let’s first understand the fundamental concepts of voltage regulation. In an ideal power generation system, the output voltage should remain constant regardless of the load demands. However, in reality, various factors such as load fluctuations, generator characteristics, and environmental conditions can cause voltage variations. This is where the AVR comes into play, continuously monitoring and adjusting the excitation current supplied to the generator’s field winding to maintain a stable voltage output.
Types of Voltage Regulators
Voltage regulators can be broadly classified into two categories: linear regulators and switching regulators. Linear regulators operate by dissipating excess voltage as heat, making them less efficient but simpler in design. On the other hand, switching regulators employ high-frequency switching techniques to regulate voltage, offering higher efficiency but with increased complexity. In the context of generating set up, switching regulators are commonly used due to their superior efficiency and ability to handle higher power levels.
Key Components of an AVR PCB
The AVR PCB comprises several essential components that work together to achieve precise voltage regulation. These components include:
-
Voltage Sensing Circuit: This circuit continuously monitors the generator’s output voltage and provides feedback to the AVR control system.
-
Current Sensing Circuit: The current sensing circuit measures the load current drawn from the generator, enabling the AVR to adjust the excitation current accordingly.
-
Excitation Control Circuit: Based on the voltage and current feedback, the excitation control circuit regulates the current supplied to the generator’s field winding, thereby controlling the output voltage.
-
Power Supply Circuit: The power supply circuit provides the necessary voltage and current levels to power the various components on the AVR PCB.
-
Protection Circuits: The AVR PCB incorporates protection circuits to safeguard the generator and the connected load from overvoltage, undervoltage, and overcurrent conditions.
Designing the AVR PCB Circuit
Designing an efficient and reliable AVR PCB circuit requires careful consideration of several factors. Let’s explore the key aspects of AVR PCB design.
Schematic Design
The first step in designing the AVR PCB is creating a detailed schematic diagram that represents the electrical connections and components of the circuit. The schematic should include all the necessary components, such as voltage and current sensing circuits, excitation control circuit, power supply, and protection circuits. It is crucial to ensure that the schematic is accurate, well-organized, and follows industry standards and best practices.
Component Selection
Selecting the right components for the AVR PCB is critical for optimal performance and reliability. The components should be chosen based on their electrical specifications, power ratings, and environmental requirements. Some key considerations include:
- Voltage and current ratings: The components must be capable of handling the expected voltage and current levels in the circuit.
- Temperature ratings: The components should be selected to withstand the operating temperature range of the generating set up.
- Accuracy and precision: The sensing and control components must provide accurate and precise measurements and control signals.
- Reliability: The components should have a proven track record of reliability and durability in similar applications.
PCB Layout and Routing
Once the schematic design is finalized and the components are selected, the next step is to create the PCB layout and routing. The PCB layout determines the physical placement of components on the board, while routing establishes the electrical connections between them. The layout and routing process should adhere to the following guidelines:
- Signal integrity: The PCB layout should minimize signal interference and crosstalk by properly separating high-frequency signals from sensitive analog circuits.
- Power integrity: The power supply traces should be adequately sized to handle the required current and minimize voltage drops.
- Thermal management: The components that generate significant heat should be strategically placed to ensure proper heat dissipation and avoid thermal hotspots.
- Manufacturability: The PCB layout should be designed with manufacturability in mind, considering factors such as component placement, trace spacing, and soldermask clearances.
Simulation and Testing
Before finalizing the AVR PCB design, it is essential to perform simulations and tests to validate the circuit’s functionality and performance. Simulation tools can help identify potential issues, such as voltage spikes, current overloads, and stability problems. Additionally, Prototype Boards can be fabricated and tested under various operating conditions to ensure that the AVR PCB meets the required specifications and standards.
Manufacturing and Assembly
Once the AVR PCB design is finalized and tested, the next step is to proceed with manufacturing and assembly. This process involves the following stages:
PCB Fabrication
The PCB design files are sent to a PCB fabrication facility, where the physical board is manufactured. The fabrication process includes the following steps:
- Printing the PCB layout on a copper-clad laminate
- Etching away the unwanted copper to form the conductive traces
- Drilling holes for through-hole components and vias
- Applying soldermask and silkscreen layers for protection and component identification
Component Procurement
The components required for the AVR PCB Assembly are procured from reliable suppliers. It is important to ensure that the components meet the specified requirements and are available in sufficient quantities to support the production schedule.
PCB Assembly
The PCB assembly process involves soldering the components onto the fabricated PCB. This can be done manually for low-volume production or using automated assembly lines for high-volume manufacturing. The assembly process typically includes the following steps:
- Solder paste application: A precise amount of solder paste is applied to the component pads on the PCB.
- Component placement: The components are placed on the PCB using pick-and-place machines or manually, depending on the production volume and complexity.
- Reflow soldering: The PCB with the placed components is passed through a reflow oven, where the solder paste melts and forms a permanent electrical and mechanical connection between the components and the PCB.
- Inspection and testing: The assembLED PCBs undergo visual inspection and electrical testing to ensure proper functionality and quality.
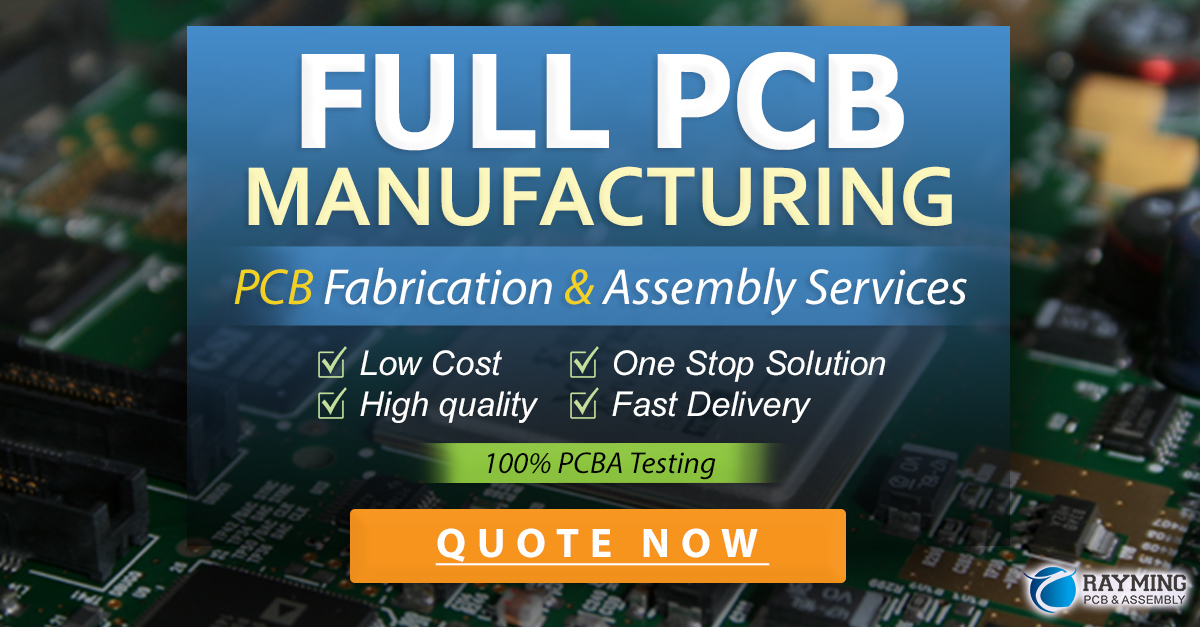
Integration and Commissioning
After the AVR PCB is manufactured and assembled, it is integrated into the generating set up. The integration process involves the following steps:
Wiring and Connections
The AVR PCB is connected to the generator’s output terminals, field winding, and other relevant components using appropriate wiring and connectors. It is crucial to ensure that the connections are secure, properly insulated, and follow the recommended wiring practices.
Calibration and Configuration
The AVR PCB may require calibration and configuration to match the specific characteristics of the generator and the desired voltage regulation parameters. This typically involves adjusting potentiometers, setting DIP switches, or programming the AVR using dedicated software tools. The calibration process ensures that the AVR accurately senses the voltage and current levels and provides the correct excitation control signals.
Commissioning and Testing
Once the AVR PCB is integrated and calibrated, the generating set up undergoes commissioning and testing. This involves running the generator under various load conditions and verifying that the AVR maintains stable voltage regulation. The testing process may include:
- No-load testing: Running the generator without any connected load to verify the AVR’s ability to maintain the rated voltage.
- Load testing: Applying various load levels to the generator and monitoring the voltage regulation performance.
- Transient response testing: Subjecting the generator to sudden load changes and observing the AVR’s response in terms of voltage recovery time and stability.
- Environmental testing: Testing the generating set up under different environmental conditions, such as temperature extremes, humidity, and vibration, to ensure reliable operation.
Maintenance and Troubleshooting
Regular maintenance and prompt troubleshooting are essential for ensuring the long-term reliability and performance of the AVR PCB and the generating set up as a whole. Some key aspects of maintenance and troubleshooting include:
Periodic Inspections
Regular visual inspections of the AVR PCB and associated components can help identify any signs of wear, damage, or loosening of connections. Inspections should be performed according to the manufacturer’s recommended schedule and may include:
- Checking for any physical damage, such as cracks, burns, or corrosion on the PCB or components.
- Verifying the tightness and integrity of electrical connections and wiring.
- Inspecting the cooling system, such as heatsinks and fans, for proper functioning and cleanliness.
Preventive Maintenance
Preventive maintenance tasks help maintain the optimal performance and reliability of the AVR PCB. These tasks may include:
- Cleaning the PCB and components to remove dust, dirt, and debris that can affect heat dissipation and electrical insulation.
- Replacing aging or worn-out components, such as electrolytic capacitors, before they fail and cause system downtime.
- Updating the AVR firmware or software to incorporate the latest features, bug fixes, and performance enhancements.
Troubleshooting Techniques
When voltage regulation issues arise, effective troubleshooting techniques can help identify and resolve the problem quickly. Some common troubleshooting steps include:
- Checking the voltage and current readings at various points in the circuit to isolate the faulty component or section.
- Verifying the continuity and resistance of electrical connections and windings using a Multimeter.
- Comparing the observed symptoms with the manufacturer’s troubleshooting guide or fault code descriptions.
- Using oscilloscopes or other diagnostic tools to analyze the waveforms and identify any anomalies or distortions.
Spare Parts Management
Maintaining an adequate inventory of spare parts is crucial for minimizing downtime and ensuring quick repairs in case of component failures. The spare parts inventory should include critical components such as voltage regulators, sensing devices, protection circuits, and power supply modules. It is important to procure spare parts from reliable sources and store them properly to preserve their quality and functionality.
Frequently Asked Questions (FAQ)
-
What is the purpose of an automatic voltage regulator (AVR) in a generating set up?
An AVR maintains a stable voltage output from the generator by continuously monitoring the voltage and adjusting the excitation current supplied to the generator’s field winding. -
What are the key components of an AVR PCB?
The key components of an AVR PCB include voltage sensing circuits, current sensing circuits, excitation control circuits, power supply circuits, and protection circuits. -
What factors should be considered when selecting components for an AVR PCB?
When selecting components for an AVR PCB, factors such as voltage and current ratings, temperature ratings, accuracy, precision, and reliability should be considered. -
What are the main steps involved in manufacturing and assembling an AVR PCB?
The main steps involved in manufacturing and assembling an AVR PCB include PCB fabrication, component procurement, solder paste application, component placement, reflow soldering, and inspection and testing. -
How can troubleshooting be performed effectively when voltage regulation issues arise in a generating set up?
Effective troubleshooting techniques include checking voltage and current readings, verifying continuity and resistance of connections, comparing symptoms with troubleshooting guides, and using diagnostic tools like oscilloscopes to analyze waveforms.
Conclusion
The automatic Voltage Regulator PCB circuit plays a vital role in maintaining stable and reliable voltage output in generating set up. By understanding the fundamentals of voltage regulation, the key components of an AVR PCB, and the design considerations, engineers can develop efficient and robust AVR systems. Proper manufacturing, assembly, integration, and commissioning processes ensure the optimal performance of the AVR PCB. Regular maintenance, troubleshooting, and spare parts management are essential for the long-term reliability and availability of the generating set up.
As power generation technologies continue to evolve, advancements in AVR PCB design and components will enable even more precise and efficient voltage regulation. With the increasing demand for stable and high-quality power supply, the role of the AVR PCB in generating set up will remain critical in ensuring the reliable operation of electrical systems across various industries and applications.
Leave a Reply