What is an LED PCB?
An LED PCB, or Light Emitting Diode Printed Circuit Board, is a specialized type of PCB designed to power and control LED lights. These boards are used in a wide range of applications, from simple indicator lights to complex LED displays and lighting systems. LED PCBs are known for their energy efficiency, long lifespan, and versatility in design.
Components of an LED PCB
An LED PCB typically consists of the following components:
- Substrate: The base material of the PCB, usually made of FR-4 or aluminum.
- Copper traces: Conductive paths that carry electrical signals and power to the LEDs.
- LEDs: The light-emitting diodes themselves, available in various colors, sizes, and power ratings.
- Resistors: Used to limit the current flowing through the LEDs, preventing damage and ensuring consistent brightness.
- Capacitors: Help to stabilize the power supply and reduce noise.
- Connectors: Allow the LED PCB to be connected to a power source or other components.
Advantages of LED PCBs
LED PCBs offer several advantages over traditional lighting solutions:
- Energy efficiency: LEDs consume significantly less power than incandescent or fluorescent lights, resulting in lower energy costs and a reduced environmental impact.
- Long lifespan: LED PCBs can last for tens of thousands of hours, reducing maintenance and replacement costs.
- Versatility: LED PCBs can be designed in a wide range of shapes, sizes, and colors to suit various applications and design requirements.
- Durability: LEDs are solid-state devices, making them more resistant to shock, vibration, and extreme temperatures compared to traditional lighting solutions.
- Instant on/off: LEDs can be turned on and off instantly, without the need for a warm-up period or cool-down time.
Applications of LED PCBs
LED PCBs are used in a wide range of industries and applications, including:
- Automotive: Used for headlights, taillights, interior lighting, and dashboard indicators.
- Consumer electronics: Found in smartphones, tablets, laptops, and televisions for backlighting and indicator lights.
- Signage and displays: Used in digital billboards, scoreboards, and information displays.
- Lighting: Used in home, office, and industrial lighting applications, as well as in street lights and other outdoor lighting solutions.
- Medical devices: Used in medical equipment for illumination, such as in surgical lights and endoscopes.
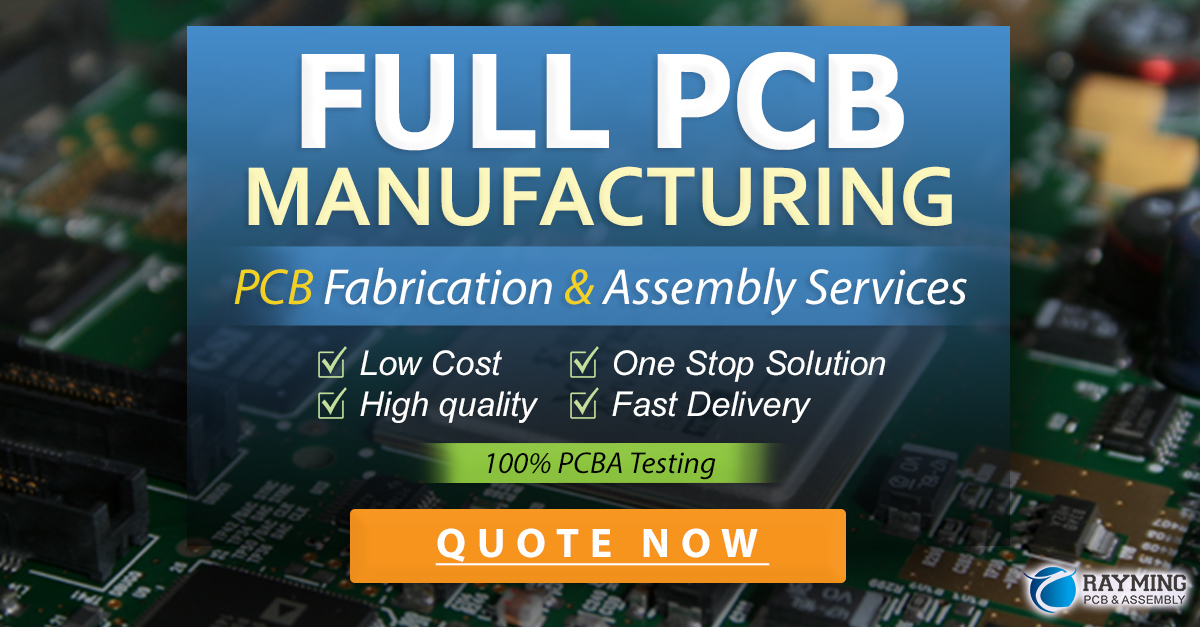
Designing an LED PCB
When designing an LED PCB, several factors must be considered to ensure optimal performance and reliability:
1. Choosing the Right LEDs
Selecting the appropriate LEDs for your application is crucial. Consider the following factors:
- Color: Choose the desired color of the LEDs based on your application requirements.
- Brightness: Determine the required luminous intensity, measured in millicandelas (mcd) or lumens (lm).
- Forward voltage and current: Ensure that the LEDs’ forward voltage and current ratings are compatible with your power supply and circuit design.
- Viewing angle: Consider the viewing angle of the LEDs, which determines how widely the light is distributed.
2. PCB Layout
Proper PCB layout is essential for ensuring optimal LED performance and minimizing electromagnetic interference (EMI). Consider the following guidelines:
- Trace width: Ensure that the copper traces are wide enough to handle the required current without excessive voltage drop or overheating.
- Trace length: Minimize the length of traces to reduce resistance and ensure even current distribution among the LEDs.
- Ground plane: Use a solid ground plane to provide a low-impedance return path for the current and to help dissipate heat.
- Thermal management: Consider the thermal requirements of the LEDs and incorporate appropriate heat dissipation techniques, such as thermal vias or metal core PCBs (MCPCBs).
3. Current Limiting and Control
LEDs require a constant current to operate properly and maintain consistent brightness. There are several methods for controlling the current in an LED PCB:
- Resistors: Use current-limiting resistors in series with each LED to set the current.
- Constant current drivers: Use dedicated LED driver ICs that provide a constant current output, regardless of variations in the supply voltage or LED forward voltage.
- PWM control: Use pulse-width modulation (PWM) to control the brightness of the LEDs by rapidly turning them on and off at a high frequency.
4. Power Supply Considerations
When designing the power supply for an LED PCB, consider the following factors:
- Voltage: Ensure that the power supply voltage is compatible with the forward voltage of the LEDs and any control circuitry.
- Current: Ensure that the power supply can provide sufficient current to power all the LEDs and any additional components.
- Efficiency: Choose a power supply with high efficiency to minimize power losses and heat generation.
- Ripple: Use appropriate filtering capacitors to minimize voltage ripple and ensure stable LED operation.
Manufacturing LED PCBs
Once the LED PCB design is finalized, the board can be manufactured using standard PCB fabrication processes:
- Substrate preparation: The PCB substrate, typically FR-4 or aluminum, is cut to the required size and shape.
- Copper patterning: The copper layer is patterned using a photolithography process to create the desired traces and pads.
- Solder mask application: A solder mask is applied to the PCB to protect the copper traces and prevent short circuits.
- Silkscreen printing: Text and symbols are printed on the PCB using silkscreen printing for easy identification and assembly.
- Component placement: The LEDs, resistors, capacitors, and other components are placed on the PCB using automated pick-and-place machines or manual assembly.
- Soldering: The components are soldered to the PCB using reflow soldering or wave soldering techniques.
- Inspection and testing: The assembled LED PCB is inspected for quality and tested to ensure proper functionality.
Troubleshooting LED PCBs
If an LED PCB is not functioning as expected, there are several common issues to investigate:
- LED polarity: Ensure that the LEDs are installed with the correct polarity (anode and cathode).
- Solder joints: Check for cold solder joints, bridging, or insufficient solder on the component leads.
- Component values: Verify that the correct resistor and capacitor values are used, as specified in the design.
- Power supply: Check that the power supply is providing the correct voltage and current, and that there are no shorts or open circuits in the power connections.
- Trace continuity: Use a multimeter to check for continuity along the copper traces and ensure there are no breaks or shorts.
Future of LED PCBs
As LED technology continues to advance, LED PCBs are expected to become even more efficient, versatile, and cost-effective. Some emerging trends in LED PCB design and manufacturing include:
- Flexible LED PCBs: The development of flexible substrates and components allows for the creation of bendable and conformable LED PCBs, opening up new possibilities for wearable electronics and unique lighting applications.
- Smart LED PCBs: The integration of sensors, microcontrollers, and wireless connectivity enables the development of smart LED PCBs that can be remotely controlled and programmed to respond to various stimuli or conditions.
- Organic LEDs (OLEDs): The use of organic materials in LED PCBs offers the potential for even thinner, lighter, and more efficient lighting solutions, with the added benefit of being eco-friendly and recyclable.
- High-density LED arrays: Advances in miniaturization and packaging technologies allow for the creation of high-density LED arrays on PCBs, enabling more compact and powerful lighting solutions.
FAQ
-
Q: What is the difference between an LED PCB and a regular PCB?
A: An LED PCB is specifically designed to power and control LED lights, while a regular PCB can be used for a wide range of electronic applications. LED PCBs often include specialized components and design considerations to ensure optimal LED performance and reliability. -
Q: Can I use a regular PCB for my LED project?
A: While it is possible to use a regular PCB for an LED project, it is not recommended. LED PCBs are designed with specific considerations in mind, such as current limiting, thermal management, and trace layout, which are crucial for ensuring the proper operation and longevity of the LEDs. -
Q: What is the lifespan of an LED PCB?
A: The lifespan of an LED PCB depends on several factors, including the quality of the components, the design of the PCB, and the operating conditions. However, LED PCBs generally have a much longer lifespan compared to traditional lighting solutions, often lasting tens of thousands of hours. -
Q: How do I choose the right LED for my PCB design?
A: When selecting an LED for your PCB design, consider factors such as color, brightness, forward voltage, forward current, and viewing angle. Ensure that the chosen LED is compatible with your power supply and circuit design, and that it meets the requirements of your specific application. -
Q: Can I control the brightness of LEDs on a PCB?
A: Yes, there are several methods for controlling the brightness of LEDs on a PCB. One common method is pulse-width modulation (PWM), which involves rapidly turning the LEDs on and off at a high frequency to vary the perceived brightness. Alternatively, you can use a constant current LED driver with dimming capabilities to adjust the brightness.
Conclusion
LED PCBs are an essential component in modern lighting applications, offering energy efficiency, long lifespan, versatility, and durability. Designing an LED PCB involves careful consideration of factors such as LED selection, PCB layout, current limiting, and power supply requirements. By understanding the principles and best practices of LED PCB design and manufacturing, engineers and designers can create innovative and reliable lighting solutions for a wide range of industries and applications. As LED technology continues to advance, the future of LED PCBs looks bright, with emerging trends such as flexible substrates, smart functionality, organic materials, and high-density arrays paving the way for even more exciting possibilities in the world of illumination.
Leave a Reply