What is PCB Assembly Testing?
PCB assembly testing, also known as PCBA testing or printed circuit board assembly testing, is the process of validating that a manufactured PCB functions as intended according to its design specifications. The goal is to identify any defects or issues with the assembLED PCB before it is integrated into the final product or shipped to the customer.
PCBA testing is a critical step in the electronics manufacturing process to ensure quality, reliability, and functionality of the end product. It helps catch problems early on when they are easier and less costly to fix, rather than discovering defects after final assembly or even worse, in the hands of end users.
There are various types of tests that fall under PCB assembly testing:
- In-Circuit Testing (ICT)
- Flying Probe Testing
- Burn-In Testing
- X-Ray Inspection
- Automated Optical Inspection (AOI)
- Functional Circuit Testing (FCT)
This article will focus specifically on functional testing, also called FCT, for PCB assemblies and the associated costs. But first, let’s define what functional testing entails.
What is Functional Circuit Testing (FCT)?
Functional circuit testing, or FCT, is a type of PCB assembly test that checks the functionality and performance of the complete, assembled PCB. It verifies that the PCBA operates as intended per its design and meets all functional requirements.
Unlike in-circuit testing which tests individual components, FCT tests the PCB as a whole, fully-functional system. Test signals are sent through the inputs of the PCB, and the outputs are measured and compared to expected values to validate proper operation.
FCT typically comes at the end of the manufacturing process after the PCB has gone through other types of testing and inspection. It is the final gate before the PCBA is approved and released to integration or distribution.
The FCT Process
The functional circuit testing process involves several steps:
-
Test Planning – Defining test coverage, creating test plans, and designing test fixtures and software
-
Test Development – Implementing the test plans by building the physical test setup (bed-of-nails fixtures, flying probe programs, etc.) and developing the test software/scripts
-
Test Execution – Running the FCT tests on the manufactured PCBAs and recording test results
-
Failure Analysis – Investigating, debugging and determining the root cause of any failures
-
Rework and Retest – Reworking or repairing any identified defects and rE-Testing the boards
The specific FCT process and test methods used will vary depending on the complexity of the PCBA, production volumes, available equipment, and other factors. The goal is to design the most efficient and effective testing process that will provide maximum test coverage to catch potential issues.
Benefits of Functional Testing for PCBA
So why perform functional circuit testing on PCB assemblies? There are several key benefits and reasons to include FCT in the manufacturing test process:
1. Verify Functionality
The most obvious and important benefit of FCT is that it confirms the PCB assembly functions properly as a complete system. It ensures the PCBA does what it is supposed to do according to its requirements and specifications.
2. Catch Defects Early
FCT helps identify post-assembly defects and workmanship issues before the PCBA makes it further down the line. Finding problems early allows them to be corrected when it is easier and less expensive compared to finding them later on.
3. Avoid Costly Failures
Issues that slip through to the end product can lead to high costs, such as product returns, recalls, warranty claims, and damage to brand reputation. FCT provides an additional gate to prevent these expensive failures from reaching customers.
4. Improve Quality & Reliability
Thorough functional testing improves the overall quality and reliability of the final PCBA. By verifying functionality and catching defects, FCT helps ensure that only high-quality, working boards make it through to the end user.
5. Reduce Manufacturing Costs
While FCT does add some upfront costs, it can actually reduce total manufacturing costs in the long run by identifying issues early and avoiding expensive late-stage failures and rework. Early detection and correction of problems is always more cost-effective.
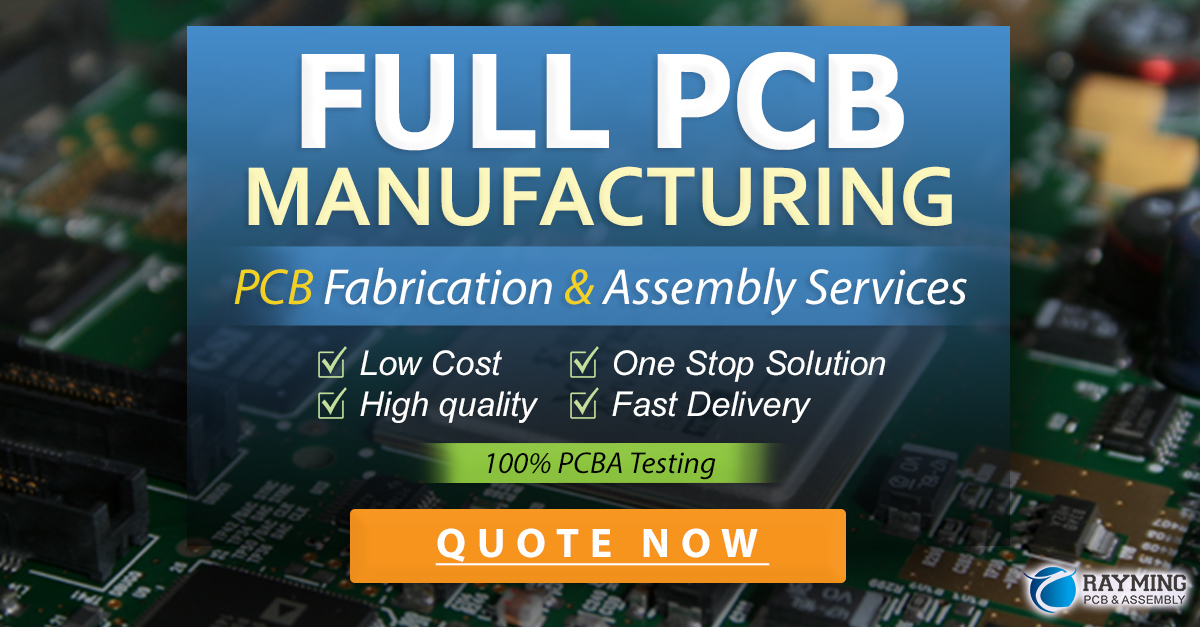
Types of PCB Functional Testing
There are several different FCT methods and technologies used to functionally test PCBAs depending on the project needs. Some common types include:
1. Boundary Scan Testing (JTAG)
JTAG testing utilizes boundary scan architecture built into JTAG-compliant components on the PCBA. It allows access to test individual device pins without physical probing.
2. Functional Test Fixtures
Custom test fixtures, such as bed-of-nails fixtures, are used to make electrical contact with test points on the PCB in order to apply input signals and measure outputs. Fixtures are commonly used for in-circuit as well as functional testing.
3. Flying Probe Testing
Flying probe testers use movable probes to contact test points on the PCB top and bottom sides. They offer flexibility without needing custom fixtures but sacrifice speed compared to bed-of-nails.
4. Hot Mock-up Testing
Hot mock-up testing uses a test setup that mimics the final environment the PCBA will operate in. It may include connecting to other system components, subsystems, or peripherals to test functionality.
5. Burn-In Testing
Burn-in testing applies extreme conditions, such as elevated temperature and voltage, to stress the PCBA and identify any potential long-term reliability issues or failures.
The right mix of functional test methods will depend on the specific PCBA requirements, production volumes, available budget and equipment, and other considerations. The goal is to achieve the target test coverage in the most cost-effective way.
Functional Test Coverage
One of the key considerations when planning and developing an FCT process is functional test coverage. Test coverage refers to how thoroughly the FCT tests exercise the functionality of the PCBA and cover potential failure modes.
Ideally, FCT should provide 100% coverage of the PCBA functionality according to its specifications and requirements. However, in practice it is not always feasible to achieve complete coverage due to time, cost and equipment constraints.
The goal is to prioritize the most critical and high-risk functions and maximize coverage of those areas. Test engineers have to balance test coverage with other factors and make tradeoffs to develop an optimal test strategy.
Some key aspects to consider for FCT test coverage include:
- Interfaces – Testing all external interfaces such as buttons, switches, displays, connectors, etc.
- Communications – Verifying wired and wireless communication protocols and busses (USB, Ethernet, Wi-Fi, Bluetooth, SPI, I2C, etc.)
- Power Management – Validating power management ICs, voltage regulators, and power distribution
- Analog and Mixed-Signal – Testing ADCs, DACs, analog sensors, filters, etc.
- Embedded Firmware – Exercising and verifying embedded software/firmware functionality
- Fault Insertion – Simulating potential faults and error conditions to test detection and handling
There are also different levels of fidelity to consider for functional testing, from basic smoke tests that just check for major failures to comprehensive tests that exercise every function and possible use case. The right level of test fidelity depends on factors such as the criticality of the application, reliability requirements, and risk tolerance.
Functional Testing Costs and ROI
Of course, one of the major considerations for functional testing is the cost versus the return on investment (ROI). FCT requires time, equipment and resources that add to the PCBA Manufacturing cost, so it is important to optimize the test process to get the most value.
FCT Cost Drivers
There are several elements that contribute to the total cost of functional testing:
-
Test Development – The engineering time and effort to plan, develop and debug the FCT process, tests, fixtures and software. This is typically a one-time cost but can be significant for complex boards and test requirements.
-
Test Equipment – The capital cost for any required test equipment, such as flying probe testers, oscilloscopes, logic analyzers, environmental chambers, etc. Equipment costs can range from a few thousand to hundreds of thousands of dollars depending on the needs.
-
Test Fixtures – Any custom test fixtures, such as bed-of-nails or jigs, that need to be designed and fabricated. Fixtures can cost hundreds to thousands of dollars each but are often a one-time expense.
-
Test Execution – The recurring labor cost to load, run and unload the PCBAs on the tester. This cost scales with production volume but is typically fairly low, especially with automated testing.
-
Troubleshooting and Rework – The time and effort for technicians to diagnose failures, isolate faults, and rework/repair boards that fail FCT. These costs can add up but are still usually cheaper than failures further downstream.
The key is to strike the right balance between test coverage and cost to get the most bang for the buck. Investing in FCT can have a very positive ROI by catching defects early and avoiding more costly late-stage or post-sales quality.
Reducing Functional Testing Costs
There are several strategies to help minimize functional testing costs while still achieving quality goals:
-
Design for Testability (DFT) – Optimize the PCBA design for testing by including test points, JTAG/boundary scan, self-diagnostics, etc. DFT techniques make testing easier, faster and more comprehensive.
-
Test Automation – Automate as much of the FCT process as possible with software to reduce manual labor and increase efficiency. Many flying probe and ICT testers support automated handling and program execution.
-
Standardized Test Platforms – Use standardized, off-the-shelf test equipment and software where possible to avoid custom development costs. Many FCT applications can be done with general-purpose instruments and tools.
-
Limit Custom Fixtures – Minimize the use of custom test fixtures and use alternative methods such as flying probe where possible. Fixtures add significant cost and lead time and are less flexible to changes.
-
Combine Test Methods – Use a combination of test methods (ICT, flying probe, AOI, AXI, etc.) to optimize test coverage and efficiency. No one method catches every defect so strategic overlap of methods provides better results.
-
Outsource to Experts – Consider outsourcing functional testing to a service provider with the right skills, equipment, and expertise. Outsourcing can reduce capital costs and provide access to the latest test technologies and methods.
PCBA Functional Test FAQ
What is the difference between ICT and functional testing?
In-circuit testing (ICT) checks individual components and pins on the PCBA, while functional testing checks the complete board as a system. ICT finds assembly and component-level faults, while FCT verifies the PCBA functions per its overall specifications and requirements.
Is functional testing required for all PCBAs?
Functional testing is not always required but is strongly recommended for most PCBAs, especially those for critical, high-reliability or high-volume applications. FCT provides an additional level of testing to ensure quality and catch any defects that may have been missed by other test methods.
How much does functional testing cost?
The cost of functional testing can vary widely depending on the complexity of the PCBA, test requirements, production volumes, and other factors. Setup costs for developing tests and fixtures can range from a few thousand to tens of thousands of dollars, while recurring costs are typically a few dollars per unit. The key is that FCT costs are lower than the cost of failures and recalls.
Can functional testing be automated?
Many aspects of functional testing can be automated to improve efficiency and reduce costs. Automated test equipment (ATE) such as flying probes and robotic handlers can perform testing with minimal human intervention. Test software can also automate the execution and analysis of FCT tests.
How long does functional testing take?
Functional test times can range from a few seconds to several minutes or more per PCBA depending on the complexity and test requirements. On average, most FCT takes around 1-5 minutes per board. Parallel testing is often used to increase throughput and reduce overall test time.
Conclusion
Functional circuit testing is a critical part of the PCB assembly process to ensure quality, reliability, and functionality. FCT verifies that the manufactured PCBA performs as intended and meets all requirements before it ships to the customer or end user.
While FCT does add some costs and time to PCBA production, it provides significant value and ROI by identifying and correcting post-assembly defects when they are cheaper and easier to fix. The key is to optimize the functional test strategy to achieve the best balance of test coverage and cost.
With the right mix of FCT methods, equipment, and expertise, manufacturers can minimize costs while still assuring the highest level of quality for their products. The cost of investing in proper PCBA functional testing is small compared to the cost of field failures and dissatisfied customers.
Leave a Reply