What are FR1, FR2, FR3, and FR4?
FR stands for “Flame Retardant,” and the numbers following it (1, 2, 3, and 4) indicate the specific grade or type of material. These materials are classified based on their composition, performance characteristics, and adherence to industry standards.
FR1
FR1 is a paper-based phenolic resin laminate. It is the most basic and economical among the FR materials. FR1 is known for its low cost and ease of fabrication, making it suitable for simple, low-density electronic applications.
Key characteristics of FR1:
– Low cost
– Easy to fabricate
– Suitable for low-density electronic applications
– Limited thermal and electrical properties
FR2
FR2 is a step up from FR1 and is made from a combination of paper and epoxy resin. It offers improved mechanical and electrical properties compared to FR1. FR2 is commonly used in consumer electronics and low-end industrial applications.
Key characteristics of FR2:
– Improved mechanical and electrical properties compared to FR1
– Suitable for consumer electronics and low-end industrial applications
– Better moisture resistance than FR1
– Moderate cost
FR3
FR3 is a composite material made from cotton paper reinforced with epoxy resin. It provides enhanced mechanical strength and electrical insulation properties compared to FR1 and FR2. FR3 finds applications in various industries, including automotive and telecommunications.
Key characteristics of FR3:
– Enhanced mechanical strength and electrical insulation
– Suitable for automotive and telecommunications applications
– Better thermal resistance than FR1 and FR2
– Higher cost compared to FR1 and FR2
FR4
FR4 is the most widely used and versatile among the FR materials. It is a composite material composed of woven fiberglass reinforced with epoxy resin. FR4 offers excellent mechanical, thermal, and electrical properties, making it suitable for a wide range of applications, including high-speed digital circuits, aerospace, and military electronics.
Key characteristics of FR4:
– Excellent mechanical, thermal, and electrical properties
– Widely used in high-speed digital circuits, aerospace, and military electronics
– High glass transition temperature (Tg)
– Dimensional stability and resistance to warping
– Higher cost compared to other FR materials
Comparison Table
Property | FR1 | FR2 | FR3 | FR4 |
---|---|---|---|---|
Base Material | Paper | Paper | Cotton Paper | Woven Fiberglass |
Resin | Phenolic | Epoxy | Epoxy | Epoxy |
Thermal Resistance | Low | Moderate | Good | Excellent |
Electrical Insulation | Low | Moderate | Good | Excellent |
Mechanical Strength | Low | Moderate | Good | Excellent |
Moisture Resistance | Low | Moderate | Good | Excellent |
Glass Transition Temperature | Low | Moderate | High | High |
Typical Applications | Simple | Consumer | Automotive, | High-speed digital, |
electronics | electronics | Telecom | Aerospace, Military | |
Cost | Low | Moderate | High | High |
Choosing the Right FR Material
When selecting the appropriate FR material for your PCB, consider the following factors:
-
Application Requirements: Evaluate the specific requirements of your application, such as the operating environment, temperature range, and electrical performance needs.
-
Cost Considerations: Determine your budget and consider the cost implications of each FR material. Higher-grade materials like FR4 may have a higher cost but offer superior performance.
-
Manufacturing Compatibility: Ensure that the chosen FR material is compatible with your manufacturing processes and equipment.
-
Compliance with Industry Standards: Verify that the selected FR material meets the relevant industry standards and certifications required for your application.
-
Availability and Lead Time: Check the availability of the FR material and consider the lead time for procurement to avoid potential delays in your project timeline.
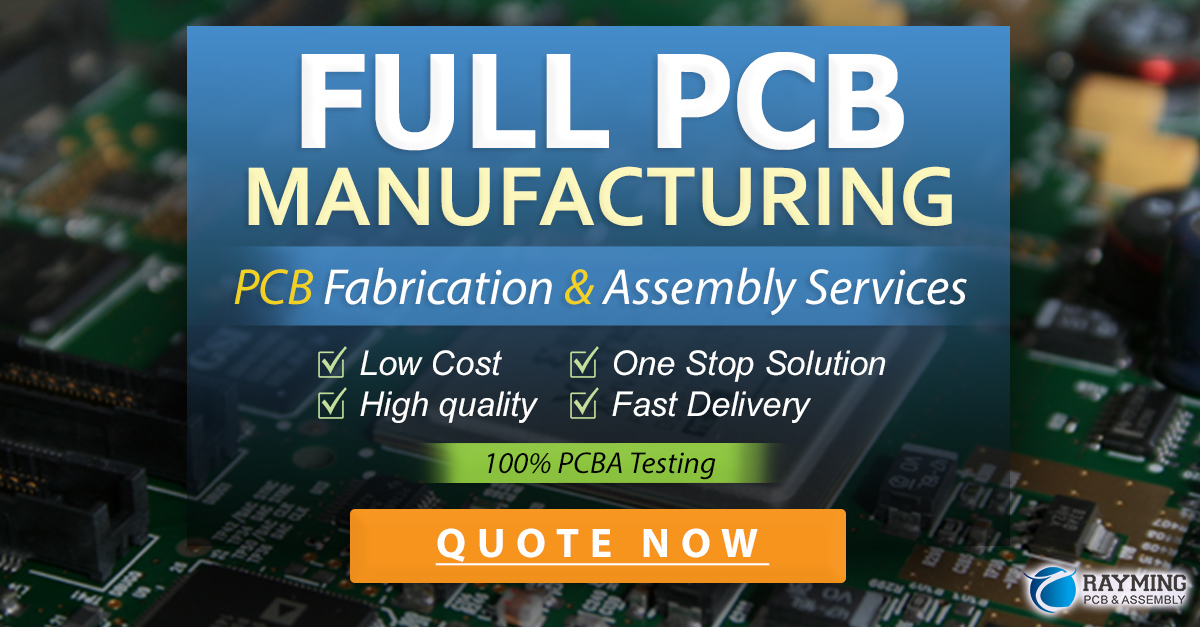
Frequently Asked Questions (FAQ)
-
Q: Can FR1 be used for high-speed digital circuits?
A: No, FR1 is not suitable for high-speed digital circuits due to its limited thermal and electrical properties. FR4 is the recommended choice for such applications. -
Q: Is FR2 suitable for automotive applications?
A: While FR2 offers improved properties compared to FR1, it may not be the best choice for automotive applications. FR3 or FR4 are more suitable due to their enhanced mechanical strength and thermal resistance. -
Q: What is the main difference between FR3 and FR4?
A: The main difference between FR3 and FR4 lies in their base materials. FR3 uses cotton paper reinforced with epoxy resin, while FR4 uses woven fiberglass reinforced with epoxy resin. FR4 offers superior mechanical, thermal, and electrical properties compared to FR3. -
Q: Can FR4 be used for aerospace and military applications?
A: Yes, FR4 is widely used in aerospace and military applications due to its excellent properties, including high glass transition temperature, dimensional stability, and resistance to warping. -
Q: How do I choose the right FR material for my PCB?
A: When choosing the right FR material, consider factors such as application requirements, cost, manufacturing compatibility, compliance with industry standards, and availability. Evaluate your specific needs and consult with PCB manufacturers or material suppliers for guidance.
Conclusion
Understanding the differences between FR1, FR2, FR3, and FR4 materials is essential for selecting the most suitable option for your PCB application. Each material has its own set of properties, advantages, and limitations. By considering factors such as application requirements, cost, manufacturing compatibility, and industry standards, you can make an informed decision and choose the FR material that best fits your needs.
Remember, the choice of FR material can significantly impact the performance, reliability, and longevity of your PCB. Take the time to evaluate your options carefully and consult with experts in the field to ensure the success of your project.
With this comprehensive guide, you now have a solid foundation of knowledge about FR1, FR2, FR3, and FR4 materials. Use this information to make informed decisions and create high-quality PCBs that meet your specific requirements.
Leave a Reply