Flexible printed circuits (FPCs) are an essential component in modern electronics. As devices continue getting smaller and more compact, FPCs allow for circuitry to bend and flex with the device. With their growing popularity, there is increasing demand for high-quality flexible printed circuit manufacturers. In this guide, we will explore the world of FPC manufacturing and provide tips on how to select the right FPC partner.
What Are Flexible Printed Circuits?
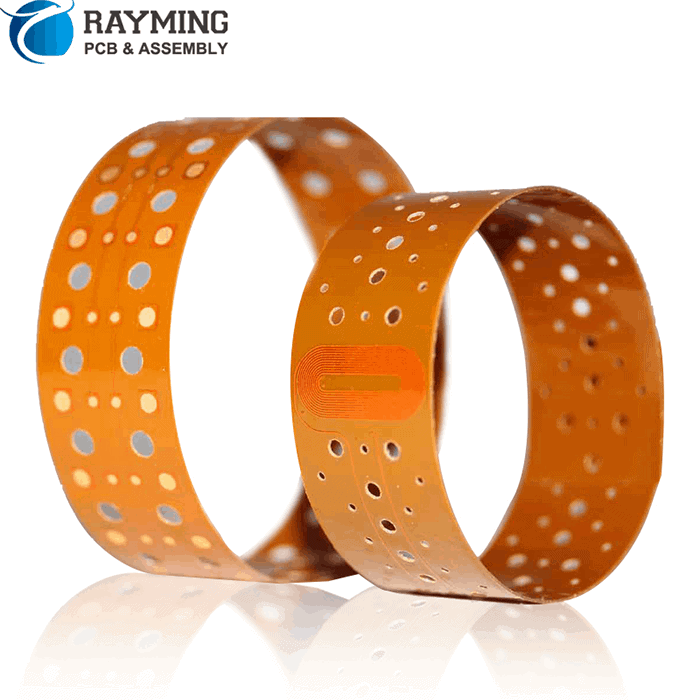
A flexible printed circuit (FPC) is a thin, lightweight circuit made of flexible base material with conductive traces etched or printed on top. The base material, typically a polyimide film, allows the FPC to bend and flex without damage to the circuitry. FPCs enable efficient use of space in compact electronics like smartphones and wearables.
Compared to rigid printed circuit boards (PCBs), FPCs provide the following advantages:
- Lightweight and thin profile – ideal for small electronics
- Can bend and flex without breaking circuits
- Dynamic flexing ability expands possible applications
- Easier to work with during assembly with dynamic flexing
- Can be rolled up for efficient storage
With these benefits, FPCs are increasingly used in applications like:
- Consumer electronics – smartphones, wearables, tablets
- Automotive electronics
- Medical devices
- Industrial electronics
- Aerospace avionics
Flexible Printed Circuit Design and Manufacturing
The design and fabrication of FPCs require specialized expertise and process capabilities. Here is an overview of FPC manufacturing steps:
1. Design
FPC layouts are designed with CAD software like Altium Designer. The circuit layout and flex requirements are modeled. The design is optimized for manufacturability and flex durability.
2. Raw Material Preparation
The flexible base material, typically a polyimide film, is cut into sheets of required sizes. A cover lay film may be laminated to protect traces.
3. Imaging
Using photolithography processes, the circuit layout artwork is transferred to the base material. A photoresist layer is coated, exposed to UV, and developed.
4. Etching
The unprotected copper foil is chemically etched away, leaving only the desired circuit traces on the base polyimide.
5. Component Assembly
Electronic components are precisely placed and soldered onto the etched traces to form the finished circuit.
6. Testing
Each FPC goes through rigorous electrical and mechanical testing to ensure reliable functionality.
7. Singulation
Individual FPCs are cut and shaped from the panel based on designs. Specialized tools cut flex circuits without damage.
The combination of specialized design expertise, engineering capabilities, and process know-how makes FPC manufacturing highly complex.
Benefits of Hiring a Flexible PCB Manufacturer
As an OEM in need of FPCs, partnering with a professional flexible PCB manufacturer provides many benefits:
Specialized expertise – FPC fabrication requires niche skills in design, material sciences, electrochemistry, high-precision manufacturing, etc. A good FPC partner offers this breadth of knowledge.
Quality assurance – With both rigorous quality control and advanced manufacturing technology, FPC vendors provide reliable and high-performing flex circuits.
Cost efficiency – Volume manufacturing capabilities and supply chain management can reduce FPC costs.
Proactive support – Experienced FPC partners provide design and engineering support for optimized manufacturability.
Fast turnaround – Quick-turn FPC prototypes help test concepts early. Shorter manufacturing times allow meeting tight deadlines.
Production scalability – The ability to efficiently scale from prototypes to high-volume production as needed.
One-stop solution – FPC companies offer end-to-end services from design support to delivery.
Therefore, partnering with the right flexible PCB company provides immense value. But it is crucial to select a reliable and capable manufacturer.
How to Select a Flexible PCB Manufacturing Partner

With many FPC vendors to choose from, here are key factors to consider during selection:
Factor | What to Look For |
---|---|
Technology | Cutting-edge capabilities for imaging, etching, testing, etc. Automated processes for precision and repeatability. |
Expertise | Significant experience in FPC design and manufacturing. Strong engineering knowledge. |
Quality | Consistent production quality. Rigorous testing and inspection. ISO certifications. |
Reliability | Proven on-time delivery record. Stable production capacity. Established supply chain. |
Customization | Ability to customize FPC designs as needed. Flexibility in order volumes. |
Cost | Competitive pricing. Value-added services to contain costs. |
Responsiveness | Quick-turnaround prototypes. Helpful customer service. Short production times. |
Sustainability | Eco-friendly manufacturing processes. Compliance to regulations like RoHS. |
Thoroughly evaluating potential FPC partners on these aspects helps find the right match for your needs and expectations. Check their website content, request product samples, ask for customer references, etc. to make an informed decision.
Top Flexible PCB Manufacturers
Many companies provide FPC manufacturing and assembly globally. Here are some of the top vendors:
1. Flexium Interconnect
Founded in 2000, Flexium is headquartered in Taiwan with factories in Thailand and China. They offer sophisticated technologies for high layer count and ultra-fine line FPCs.
2. Career Technologies
Career Technologies, established in 1999, provides advanced FPC and rigid-flex solutions. They serve industries like healthcare, automotive, and aerospace.
3. Flexible Circuit Technologies
Based in Minnesota, Flexible Circuit Technologies offers prototyping and production of complex, high-performance FPCs. They focus on medical, industrial, and aviation applications.
4. All Flex
All Flex, founded in 1977, provides comprehensive flex and rigid-flex PCB solutions. They have patented laser manufacturing processes and engineering expertise.
5. Lenthor Engineering
Florida-based Lenthor Engineering has over 48 years of experience in flex PCB design, engineering, and OEM electronics assembly.
6. Minco
Minnesota-based Minco designs and manufactures specialized flex circuits for medical, aerospace, and industrial applications.
7. MFLEX
Headquartered in California with global operations, MFLEX is a leading manufacturer of flex circuits and flexible packaging solutions.
This list covers some of the top FPC companies, but there are many other good manufacturers around. Focus on choosing one that best fits your specific requirements.
Key Takeaways on Flexible PCB Manufacturing
- Flexible printed circuits enable efficient electronics packaging with their bendability.
- FPC manufacturing entails complex design, photolithography, etching, assembly, and testing processes.
- Partnering with an experienced FPC manufacturer provides many benefits in expertise, quality, costs, and delivery.
- Carefully evaluate potential suppliers based on their capabilities, expertise, processes, and track record.
- Many established companies offer reliable global FPC fabrication and assembly services.
Frequently Asked Questions
Q: What are some common applications of FPCs?
Common applications of flex PCBs include consumer electronics like smartphones and laptops, automotive dashboard displays, digital cameras, medical devices, industrial electronics, aerospace avionics, etc. Their compact and dynamic nature suits many space-constrained uses.
Q: How is an FPC different from a rigid PCB?
Unlike rigid boards which are solid, FPCs use a flexible base material that allows bending without breaking internal circuit traces. This flexing ability allows efficient configurations in tight spaces and moving applications. FPCs are thinner and lighter as well.
Q: Are FPCs more expensive than rigid PCBs?
Yes, FPC fabrication typically has higher costs compared to rigid PCBs. The specialized materials, complex processes, lower production volumes, and precision requirements contribute to the cost premium. However, FPCs enable space savings in product design.
Q: Can FPC manufacturers handle low-volume orders?
Many FPC companies cater to customers requiring low-volume or prototype orders before higher production. Their capabilities to efficiently switch between small and large production runs gives flexibility. However, per-unit costs are higher for low volumes.
Q: How long does it take to manufacture FPCs?
Production time depends on order size, design complexity, and manufacturer capabilities. Small prototyping volumes may take 2-5 days. For larger production orders of thousands of units, standard lead times range from 2-4 weeks.
Leave a Reply