Flexible printed circuit boards (PCBs), also known as flex PCBs or flex circuits, are printed circuits that are flexible and bendable. They offer many advantages over traditional rigid PCBs, such as improved reliability, dynamic flexing, and installation in tight spaces. However, these benefits come at a cost – flex PCBs are generally more expensive to manufacture than rigid PCBs.
In this article, we will provide a comprehensive overview of the factors that influence the cost of flexible PCBs and break down the pricing considerations for flex PCB manufacturing.
What is a Flexible PCB?
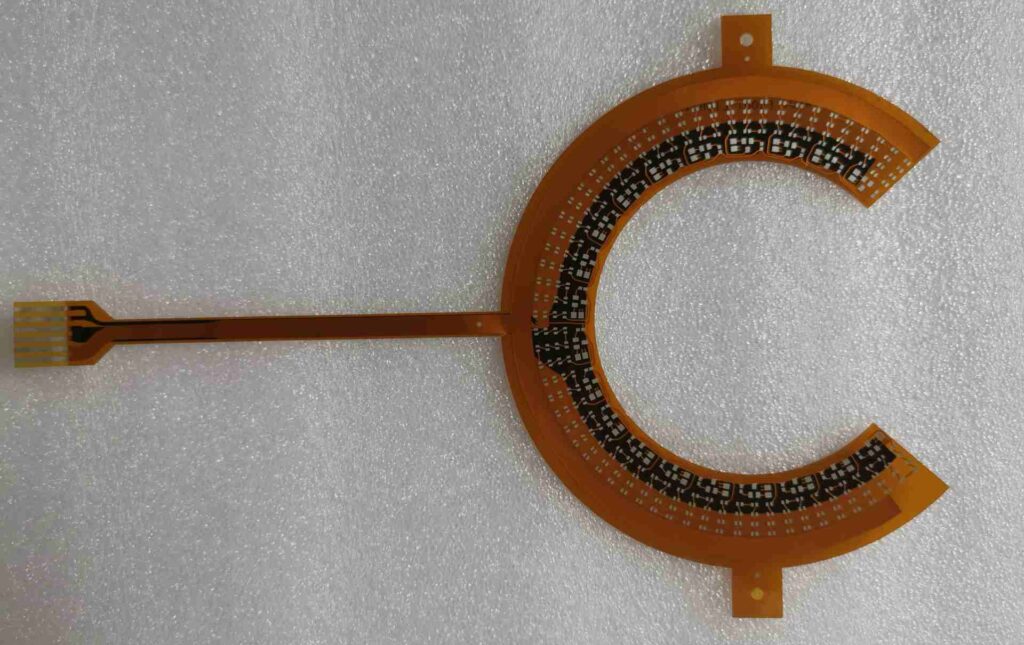
A flexible PCB is a printed circuit built on a flexible substrate such as polyimide or polyester film. The conductive pathways are etched or printed onto the substrate to connect different components. Flex PCBs can twist, bend, and flex during use without damage to the circuits.
Some key features of flexible PCBs:
- Can be bent, folded, twisted, and contorted repeatedly without failing
- Extremely thin, lightweight, and durable
- Used in dynamic flexing environments and tight spaces
- More resistant to shocks and vibrations than rigid PCBs
- Improved reliability and longer service life in motion applications
Flexible PCBs are commonly used in consumer electronics, medical devices, industrial equipment, aerospace systems, and automotive applications where size, weight, and reliability are important factors.
Factors That Influence Flex PCB Cost
The cost of manufacturing flexible PCBs depends on various factors, including:
1. Board Size
The size of the flex PCB directly impacts the material cost. Larger boards require more raw materials, increasing the base cost. The size also affects panel utilization – the number of boards that can be laid out on a panel. Better panel utilization leads to lower cost per board.
2. Layer Count
The number of conductive layers in the flex PCB stackup influences cost. More layers require additional materials, processing steps, and considerations during assembly. 2-layer flex circuits are the most cost effective. 4 to 6 layers are common. 8 layers or more are less common and more expensive.
3. Board Thickness
Thinner flex PCBs cost less because they use less material. But thickness cannot be reduced beyond a certain point without impacting durability and manufacturability. Common flex PCB thickness range from 25um (1 mil) to 250um (10 mil).
4. Materials
The base substrate (polyimide, polyester, PEN, PET, etc.) and copper foil type (RA, ED, rolled annealed) impact cost. Some exotic materials like polyether ether ketone (PEEK) are more expensive than standard polyimide.
5. Dielectric Material
The type of insulating dielectric layer used between copper layers influences cost. Common dielectrics include polyimide, acrylic, and epoxy. More advanced materials cost more.
6. Copper Weight
Copper weight is measured in ounces per square foot (oz/ft2). Heavier copper increases conductivity but also raw material cost. 1/2 oz and 1 oz copper foils are typical.
7. Finishes and Coatings
Specialsurface finishes like immersion gold, ENIG, and OSP add cost. Also, coverlay and stiffeners increase cost but may be required in some designs.
8. High-frequency Materials
Some applications require high-frequency substrates and wave-shaping copper profiles, which add cost.
9. Adhesives
The adhesive used to bond layers can impact cost, depending on type. Common adhesives include acrylic, epoxy, and polyimide.
10. Tolerances
Tight tolerances increase cost due to additional process controls. Standard flex PCB tolerance is ±0.1mm. Tighter tolerances are possible but cost more.
11. Bend Radii
Small bend radii increase manufacturing complexity and cost. Minimum bend radius is typically 3-4 times unclad dielectric thickness.
12. Stiffeners and Reinforcements
Adding stiffeners and reinforcements to maintain flex PCB shape increases cost but may be required. Common options are additional copper layers or organic/inorganic materials.
13. Board Quantity
Higher order volumes spread fixed costs over more boards, reducing per unit cost. Prototyping in low volumes is more expensive per board than production quantities.
14. Design Complexity
Complex board geometries, dense routing, small features, and tight tolerances require advanced processes, increasing cost. Simpler designs are cheaper.
15. Testing and Inspection
Extensive electrical testing, inspection, and qualification programs at various stages add cost but ensure quality. Skipping these adds risk.
16. Certifications
Special certifications like ITAR, UL, CE, RoHS add administrative and testing costs.
17. Lead Time
Rushed turnaround times add expedite fees or require tooling modifications to reduce process time.
Flex PCB Cost Per Square Inch

A common metric used to estimate flex PCB pricing is cost per square inch, which provides a ballpark baseline cost according to the following typical ranges:
- Prototyping: $5-10 per square inch
- Low Volume Production: $3-6 per square inch
- Medium Volume Production: $2-4 per square inch
- High Volume Production: $1-3 per square inch
However, this does not account for all the nuances that affect pricing. It is better used for rough upfront budgeting. The final cost depends on the specific project requirements.
Flex PCB Assembly Cost Considerations
In addition to base material and fabrication cost, the assembly of components and connectors onto the flex PCB also impacts overall cost. Here are some considerations:
- Component types and size: Smaller surface mount devices are easier and cheaper to assemble than large connectors or through-hole parts. High pin count parts add complexity.
- Component placement: Optimal component placement with minimal overlapping and routing congestion reduces assembly cost.
- SMT vs. through-hole parts: SMT assembly is generally faster and cheaper than through-hole assembly.
- Selective vs. full population: Selectively assembling components only where needed reduces cost vs. full board population.
- Sequential laminations: Complex assemblies may require sequential bonding, adding cost.
- Secondary operations: Additional steps like programming, testing, reinforcement, etc. add cost.
- Low vs. high mix: High-mix, low-volume assembly with frequent changeovers is more costly than stable high-volume production.
- Automation: Automated assembly and inspection lowers cost through speed and precision.
How to Reduce Flex PCB Costs
Here are some tips to optimize your design and minimize overall flex PCB costs:
- Minimize board size and layer count as much as possible
- Use standard materials and copper weights where possible
- Allow for larger bend radii and wider line/space
- Reduce thickness if durability permits
- Eliminate any gold finishing unless essential
- Simplify board outline and avoid tight-pitch or micro-vias
- Consolidate components to reduce parts count
- Place components for efficient automated assembly
- Build test points only where needed
- Re-use proven flex PCB designs when possible
- Work closely with your flex PCB partner to identify cost reduction opportunities
Small tweaks in the design phase can reduce cost without compromising performance or quality.
Conclusion
There are many variables that determine the cost of flexible PCBs, from the board size and layer count to the assembly process. While the cost per square inch provides a baseline estimate, the actual pricing depends on the specific requirements of the application.
By optimizing the design, consolidating components, standardizing materials, and working closely with your flex PCB supplier, costs can be minimized without sacrificing quality or manufacturability. With an understanding of the cost factors and tradeoffs involved, informed design decisions can be made to lower overall flex PCB expenses.
Frequently Asked Questions (FQA)
Q1: How is flex PCB pricing usually quoted by manufacturers?
A1: Flex PCB pricing is usually quoted based on cost per square inch, setup charges, tooling charges, and price breaks at different order volumes. Some additional charges may apply for expedited delivery, special requirements, or prototyping fees.
Q2: How can I get accurate flex PCB pricing for my design?
A2: To get an accurate quote, share your flex PCB design Gerber files, bill of materials, layer stackup, and any special requirements with the manufacturer’s engineers. Also indicate your target volumes. They will analyze the design, manufacturing needs, and provide a detailed written quotation.
Q3: What are some ways to reduce costs in multi-layer flex PCBs?
A3: Using standard materials, minimizing layer count, optimizing layer stackup, consolidating part types, re-using designs, and designing efficiently for automated assembly can help reduce multilayer flex PCB costs. Work closely with your manufacturer.
Q4: How much does it cost to prototype a new flex PCB design?
A4: Prototyping cost varies widely based on complexity, size, volumes, etc. As a rough estimate, expect to pay $5-10 per square inch for 1-2 layer flex PCB prototyping in low volumes (under 50 units). NRE charges may also apply.
Q5: What are the main benefits of using flex PCBs instead of rigid PCBs?
A5: Flex PCBs provide dynamic flexing, improved reliability, lighter weight, tighter packaging, and the ability to integrate interconnects and components in tight spaces where rigid PCBs won’t fit. This expands design possibilities.
Leave a Reply