Introduction
Flexible printed circuits (FPCs), also known as flex circuits, are integral components of many modern electronic devices. From consumer electronics to medical devices, flex circuits enable compact and creative product designs through their thin, lightweight, and bendable properties. As products continue getting smaller and more complex, the demand for flex circuits is rapidly growing.
Choosing the right flexible circuit manufacturer is critical to ensuring your flex circuit prototypes and production runs meet requirements for performance, quality, and cost. This guide will explore key considerations when selecting a flex circuit supplier, top manufacturers, and what to expect when working with a flex circuit fabrication partner.
Key Factors in Choosing a Flexible Circuit Manufacturer
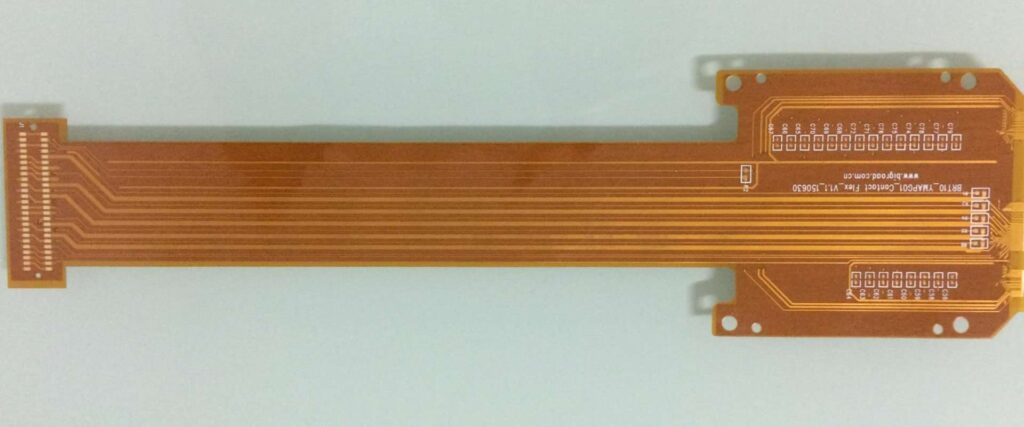
Flexible Circuit Materials and Constructions
Flex circuits can be fabricated from different materials using various conductive and insulating layers. Common materials include polyimide, polyester, polyethylene naphthalate (PEN), and liquid crystal polymer (LCP). The material properties impact the circuit’s flex life, temperature rating, chemical resistance, and other performance specs.
Manufacturers should offer a range of flex circuit constructions to suit your mechanical and electrical needs. This includes single, double, and multilayer designs with or without stiffeners or covers. Discuss your flex requirements with potential suppliers.
Design Capabilities and Constraints
Your flex circuit partner should have expertise in designing complex flex circuits, including managing tight tolerance and high-density interconnects. Look for capabilities around:
- Fine line traces and spaces to 5 microns or below
- Flex-to-rigid capabilities to allow integration with PCBs
- Tight bend radius control
- High layer counts up to 12+ layers
- Via construction down to 25 microns or lower
Understand their design rules and constraints to ensure your design is manufacturable. For example, are there limits on the thinnest materials or tightest tolerances they can reliably produce?
Assembly and Additional Services
Many flex circuit suppliers offer in-house assembly of components onto the fabricated circuits. This includes soldering, adhesive bonding, thermal compression bonding, and reflow. Evaluate capabilities for accurate, high-mix assembly.
Additional services to consider are conformal coating, electrical testing, X-ray inspection, and other quality checks. This helps streamline manufacturing by keeping more steps under one roof.
Certifications and Quality Processes
Reputable flex circuit manufacturers will have the certifications and process controls to produce consistent, high-quality products:
- ISO 9001 certification for quality management
- IPC certifications for rigid and flex PCB design and assembly
- Rigorous quality checks during fabrication and assembly
- Capability to meet regulatory standards like ITAR for defense projects
Prototyping and Low Volume Support
When researching manufacturers, look for capabilities around low volume and prototype runs. This includes:
- Low minimum order quantities
- Quick turnaround times for prototype builds
- High mix production with frequent design changes
- Dedicated engineering support throughout prototyping
Cost and Pricing Models
Pricing models generally fall into:
- Square inch pricing based on flex circuit size
- Panel pricing where multiple circuits are produced on a panel
- Layer pricing considering unique material and process costs per layer
Manufacturers should provide detailed quotations clearly outlining costs. Expect pricing to vary considerably between different flex circuit manufacturers based on capabilities and conditions.
Top Flexible Circuit Manufacturers
Here are some of the top flex circuit manufacturers operating globally:
Flexible Circuit Technologies
With over 50 years in the industry, Flexible Circuit Technologies provides the full spectrum of flex and rigid-flex manufacturing. They produce ultra-complex designs with tolerances down to 3 microns and 12+ layers. Their flex-to-rigid capabilities allow seamless integration with PCBs.
All Flex
All Flex focuses exclusively on flex and rigid-flex circuits with expertise down to 1 mil lines and spaces. They provide comprehensive in-house assembly and testing services. Their customer base covers defense, aerospace, medical, industrial, and other markets.
Flexible Interconnect
Flexible Interconnect offers prototyping and production of single, double, and multilayer flex circuits. They utilize the latest laser processing and photolithography equipment to produce tight tolerances below 10 microns. Assembly options include SMT, thermal compression bonding, and more.
DFW Inc.
DFW Inc. provides prototyping through medium volume production of flex circuits. They are particularly adept at quick-turn prototypes with 1-2 day deliveries. Additional capabilities around design, assembly, and box build enable one-stop manufacturing support.
Compass Circuits
Compass Circuits produces rigid, flex, and rigid-flex designs, including for aerospace, defense, and industrial applications. They specialize in high layer count, high density interconnects and multi-panel designs. Robust in-house testing ensures reliability and performance.
This covers some of the most recognized flexible circuit manufacturers. But there are many others offering varying capabilities. The best fit depends on your specific project requirements and expectations.
Working with a Flex Circuit Fabrication Partner
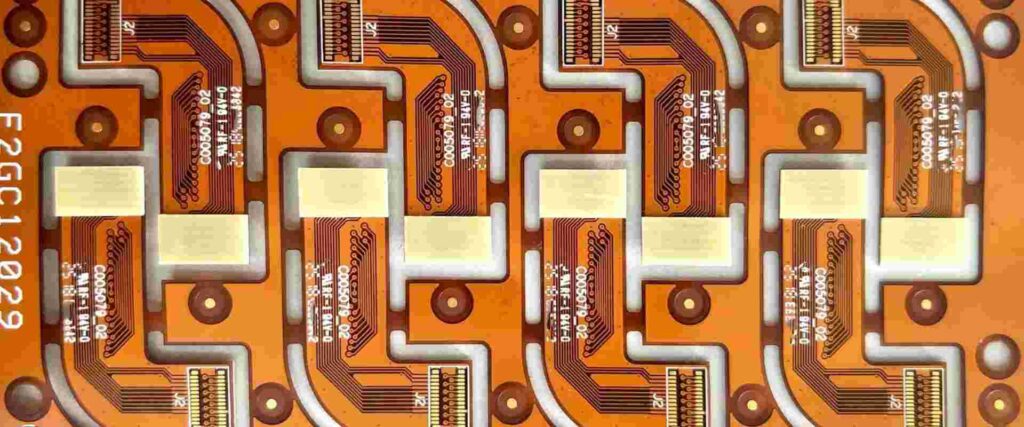
Here is an overview of what to expect when partnering with a flex circuit manufacturer:
Design Review
Submit your flex circuit designs for an initial review by the manufacturer’s engineers. They will check that your design is viable for fabrication and highlight any recommended adjustments based on their design rules and capabilities. This process validates the design upfront and prevents issues later on.
Prototyping
Low volume prototyping is a critical stage for testing different flex circuit variations. Expect repeated builds with quick turnaround (1-5 days) as you refine the optimal design. Prototyping support is essential for confirming performance prior to broader production.
Fabrication
Fabrication involves laminating together the conductive, insulating, and cover layer materials using high pressure and temperature. Complex circuits require multiple precision processes like photolithography, etching, plating, and laser cutting. The best manufacturers continuously inspect fabrication quality at all process stages.
Assembly
If assembling components like connectors or chips onto the circuits, the manufacturer will carry out the required soldering, bonding, or other attachment methods. Further inspection and testing verifies assembly quality.
Testing and Inspection
Inspection techniques include visual checking, microsectioning, and electrical testing. This confirms continuity, isolation between conductors, component alignment, and other parameters. X-ray is commonly used for inspection of hidden solder joints and interfaces.
Delivery
The completed flex circuit prototypes or production runs are then delivered per the schedule. Reputable manufacturers will ensure on-time delivery for each stage from prototyping through full production ramp up.
Key Takeaways When Selecting a Flex Circuit Partner
- Look for expertise with your required constructions, tolerances, and assemblies
- Consider capabilities for low volume prototyping and engineering support
- Evaluate certifications, quality processes, and testing capabilities
- Check lead times, costs, and minimum order quantities
- Partner early for design reviews and ensure manufacturability
- Find a supplier that prioritizes communication and collaboration
Flex Circuit Manufacturer Comparison
Here is a comparison of some key specifications across popular flex circuit manufacturers:
Manufacturer | Min. Line/Space | Min. Hole Size | Min. Bend Radius | Max. Layers |
---|---|---|---|---|
Flexible Circuit Technologies | 3 μm | 25 μm | 0.10 mm | 12+ |
All Flex | 1 mil | 1 mil | 0.076 mm | 6 |
Flexible Interconnect | 10 μm | 25 μm | 0.40 mm | 6 |
Compass Circuits | 5 μm | 25 μm | 0.13 mm | 12+ |
DFW Inc. | 2 mils | 1 mil | 0.25 mm | 6 |
This gives a snapshot of process capabilities, but have in-depth discussions with each manufacturer about your particular requirements.
Frequently Asked Questions
What are some applications of flex circuits?
Flex circuits are widely used in products like mobile phones, tablets, notebooks, cameras, wearables, medical devices, automotive electronics, aerospace avionics, and many other applications where their thin, bendable, and customizable nature provides advantages.
How long does it take to manufacture flex circuits?
Lead times range from 24 hours for simple prototypes to 8+ weeks for complex, high volume production runs. Discuss projected timeframes with manufacturers early in your design process.
How should flex circuits be handled and stored?
Avoid touching conductive surfaces, exposure to dirt/debris, sharp folding, contact with chemicals, or other handling that could contaminate or damage the circuits. Follow manufacturer guidelines on storage conditions.
Can flex circuits be reworked or repaired if damaged?
Some repairability is possible but limited depending on where damage occurs. Avoiding damage through proper handling is ideal. Consult your manufacturer about repair options if needed.
What are important considerations around cost?
Pricing depends on design complexity, order quantities, lead times, and manufacturer capabilities. Get detailed quotes accounting for all materials, processing, testing, and logistics costs.
Conclusion
As products continue trending toward smaller, lighter, and more dynamic designs, the performance benefits of flex circuits will be in increasing demand across industries. However, significant expertise is required to fabricate these complex circuits reliably. Finding the right flex circuit manufacturer is critical to meeting your product needs in terms of capability, quality, and value. Use this guide to understand key evaluation criteria and establish an effective partnership. With the rapid pace of technology development, a collaborative manufacturer will be indispensable in keeping your products competitive through innovative flex circuit solutions.
Leave a Reply