An In-Depth Look at How Flex Circuit Costs Are Calculated
Flexible printed circuit boards (flex PCBs) offer many advantages over traditional rigid PCBs, such as flexibility, reduced weight, and the ability to fit into tight spaces. However, these benefits come at a cost – flex circuits tend to be more expensive to manufacture than standard rigid boards. In this article, we’ll take an in-depth look at the key factors that determine flex PCB pricing.
Flex Circuit Material Costs
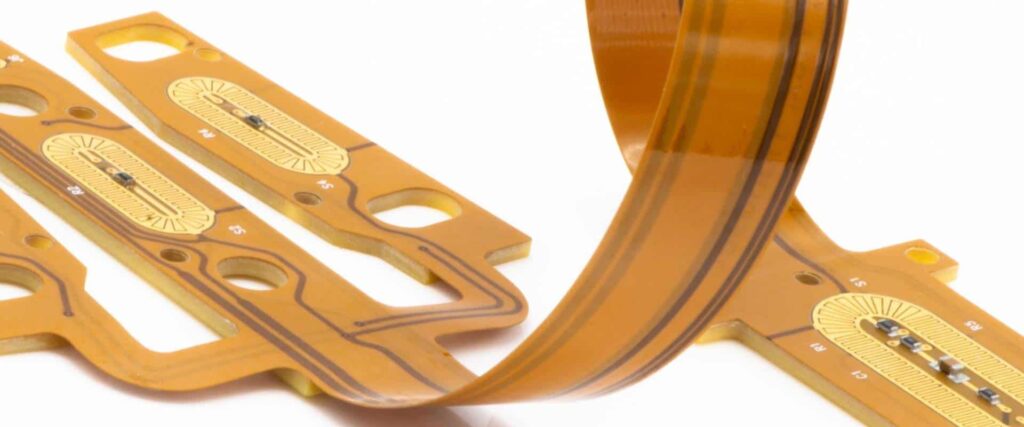
The base material is one of the biggest contributors to overall flex PCB cost. There are three main types of flexible circuit materials:
Polyimide
This is the most common and affordable flexible material. The cost per square foot is relatively low.
Polyester
More expensive than polyimide but has superior thermal resistance and chemical resistance. Ideal for high-reliability applications.
LCP (Liquid Crystal Polymer)
The most expensive flexible material. Offers extremely high temperature operation. Used for mission-critical flex circuits.
Here’s a rough comparison of the relative material costs:
Material | Relative Cost |
---|---|
Polyimide | Low |
Polyester | Medium |
LCP | High |
As you can see, the choice of base material is a major cost driver in flex PCB fabrication. Using an expensive material like LCP could triple the base costs compared to a polyimide board.
Layer Count
The number of conductive copper layers in a flex circuit also significantly impacts pricing. Each additional layer adds cost in terms of materials, processing, and testing.
Layer Count | Relative Cost |
---|---|
1-2 layers | Low |
4-6 layers | Medium |
8+ layers | High |
High layer count boards allow for more complex circuit design but come at a premium price. For simpler, low-cost boards, stick to 1 or 2 layer constructions whenever possible.
Board Size
In general, larger flex circuits will cost more than smaller ones. This is because more base material is required. Panel utilization also decreases with larger boards.
Board size should be optimized to be as small as functionally possible to minimize cost. Keeping board dimensions under 10″x10″ will help reduce pricing. Anything larger will increase quickly in cost due to material use.
Minimum Bend Radius
The minimum bend radius that a flex circuit can tolerate impacts cost. Tighter bend radii require special handling, processing, and materials that add expense.
Bend Radius | Relative Cost |
---|---|
> 10mm | Low |
5-10mm | Medium |
<5mm | High |
Design for larger bend radii whenever possible. Consult your flex PCB manufacturer for their specific capabilities.
Stiffeners and Thick Copper
Adding stiffeners and thick copper layers also increases fabrication cost. Stiffeners are typically added to provide mechanical support. Thick copper (above 2 oz) improves thermal performance.
- Stiffeners: +10-20% cost
- Thick copper: +15-30% cost
Only use these options if functionally required. Stick to thinner 1/2 or 1 oz copper if possible.
Special Finishes and Coatings
Non-standard surface finishes like immersion silver, immersion tin, and gold plating drive up cost. Conformal coatings for protection from moisture or chemicals also add expense.
Finish/Coating | Added Cost |
---|---|
Immersion silver | +10-30% |
Immersion tin | +5-20% |
Gold plating | +50-100% |
Conformal coating | +20-50% |
Avoid expensive finishes and coatings unless absolutely needed for reliability or durability.
Advanced Manufacturing Processes
Certain specialized manufacturing processes will increase fabrication costs:
- Fine line/space (<100 micron): More precision required
- Via formation: Adds steps compared to surface mount only
- Blind/buried vias: Complex laminations
- Flex-rigid boards: Combines multiple processes
Advanced processes usually add 15-30%+ to the base cost. Keep design simple wherever possible.
Low Volume Production
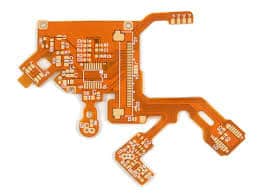
Flex PCB pricing is largely driven by economies of scale. Producing prototypes or low volumes is always more expensive per unit than high volume production runs.
Here’s a rough estimate on how volume impacts cost:
Quantity | Relative Cost Per Board |
---|---|
1-50 boards | Very High |
50-500 boards | High |
500-5,000 | Medium |
5,000+ | Low |
To save cost, produce at higher volumes or aggregate orders into larger batches.
Prototypes vs. Production
Initial prototype and engineering runs with new designs are more expensive than subsequent production runs. There are additional costs involved with developing fabrication processes, testing, and potential re-spins.
You can expect prototyping costs to be 30-50% higher than full production. Build enough margin into your budget to account for this.
Flex PCB Assembly
If you require assembly of components onto the flex circuit, this will drive costs higher as well. The assembly process requires expertise in handling thin, bendable boards.
Expect assembly pricing for flex boards to be 20-40% higher than rigid PCB assembly in low volumes. This premium can drop significantly for high-volume production.
Testing and Inspection
Thorough testing and inspection is critical for flex circuits to ensure reliable performance in use. This includes:
- Automated optical inspection (AOI)
- Netlist verification
- In-circuit testing
- Functional testing
Add 10-20% to the base cost to allow for proper quality control and defect detection.
Company Reputation and Quality
Not all flex PCB manufacturers are equal in terms of quality and service. Selecting a reputable supplier with years of experience will impact pricing but help avoid issues with faulty boards.
Be prepared to pay 10-20%+ higher costs for a reliable, high-quality supplier over a cheaper option. The extra cost is worth reduced development risk.
Tips for Reducing Flex PCB Costs
Here are some helpful tips to lower your flex circuit expenses:
- Use the simplest design possible. Minimize layers and complexity.
- Select the least expensive base material that meets functional needs.
- Standardize processes across multiple designs for efficiency.
- Partner with your supplier early in the design process for design-for-manufacturing feedback.
- Take advantage of panelization to produce multiple boards in a batch.
- Build volume into orders to benefit from bulk pricing discounts.
- Avoid unnecessary coatings, finishes, and other add-ons.
- Leverage existing approved designs when possible instead of reinventing the wheel.
- Work with your supplier to identify cost-reduction opportunities.
- Consider design tradeoffs between performance and cost.
Flexible PCB Pricing Examples
To make cost estimation more concrete, here are some real-world examples of flex PCB pricing at moderate production volumes of 500-1,000 boards:
2-Layer Polyimide Board
Simple 2-layer flex circuit 6” x 6” with:
- Polyimide base material
- FR-4 stiffener sections
- 1 oz copper traces
- Minimum 8mm bend radius
- Solder mask and legend printing
- Surface mount pads and parts only
- 500 boards quantity
Cost per board: ~$125
4-Layer Polyimide Board
More complex 4-layer flex design 8” x 8” with:
- Polyimide base material
- 3 oz copper power traces
- 6mm minimum bend radius
- 250μm line/space
- 2,000 holes with plated through vias
- Solder mask and legend
- 1,000 boards quantity
Cost per board: ~$350
6-Layer LCP High-Temp Board
Advanced 6-layer circuit 6” x 3” with:
- LCP base material
- 6 layers with mixed trace weights
- 4mm minimum bend radius
- 150μm line/space
- Immersion silver finish
- 1,000 boards quantity
Cost per board: ~$750
As you can see, cost scales dramatically based on design complexity, material selection, and build specifications. There are many avenues for controlling flex PCB costs if you pay attention to pricing factors during the design phase.
Frequently Asked Questions
Here are answers to some common questions about flex PCB pricing:
What are the main factors that increase flex PCB cost?
The biggest drivers of cost are: number of layers, board size/material use, special finishes, lower production volumes, advanced manufacturing processes, flex-rigid construction. Simpler designs, standard materials and surface finishes, and higher volumes provide the most opportunity for cost savings.
Is there a rough ballpark cost per square inch I can use for budgetary purposes?
As a very general rule for moderate production volumes, you can estimate $3-8 per square inch for simpler 2-4 layer polyimide boards, and $8-15 per square inch for more complex LCP boards with 6+ layers. But many other factors influence pricing beyond just size.
How can I get accurate pricing estimates for my specific design?
The best way is to work directly with a flex PCB manufacturer during the design process to solicit updated quotes on your actual board layout and specifications. Most suppliers will provide free design reviews and feedback to prospective customers. This will give you realistic pricing before you fully commit to a design.
What design choices can I make early on to optimize my board for lowest cost?
Focus on minimizing layers, pickup panel utilization, avoiding non-standard materials/finishes/coatings, maximizing production volumes, simplifying manufacturing processes, and involving your supplier for design for manufacturing input.
Is there a minimum order quantity for flex PCB production?
Yes, most suppliers require 50-100 board minimums for small prototype orders. For higher volume production, minimums are usually in the 500-1,000 range. If your needs are less than these amounts, you may pay an additional low volume fee.
Should I expect flex circuits to be 2-3x the cost of rigid boards?
In general flex PCBs carry about a 20-50% premium over rigid boards for equivalent complexity, and up to 2-3x for highly complex designs. The cost ratio depends heavily on the specific designs being compared. Simpler flex circuits can approach the costs of rigid boards.
Leave a Reply