Introduction
Printed circuit boards (PCBs) are essential components in nearly all modern electronic devices. Flexible PCBs, also known as flex PCBs, offer advantages over rigid PCBs in applications where flexibility is required. As flex PCBs become more widely used, understanding the factors that determine their cost is important for designers and manufacturers. This article will examine the key determinants of flex PCB pricing and provide guidance on minimizing costs.
Flex PCB Materials
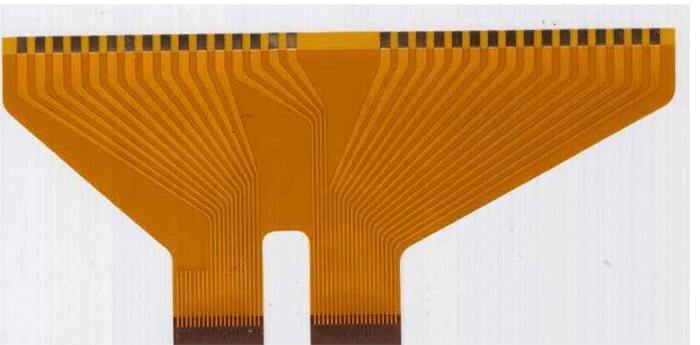
The materials used in manufacturing flex PCBs significantly impact the overall cost. The most common materials are:
Polyimide Films
Polyimide, such as Kapton, is the most popular flexible PCB substrate. It provides excellent thermal stability and chemical resistance while maintaining flexibility. Polyimide costs more than the rigid FR-4 substrates used in rigid PCBs.
Adhesive Layers
Adhesives bond the copper traces to the polyimide substrate. Acrylic and epoxy are two common adhesive options, with acrylic generally being more affordable.
Copper Foil
Copper foils come in different thicknesses, measured in ounces per square foot. Thicker copper is more costly but allows for higher current capacity. 1-oz and 1⁄2-oz copper foils are commonly used.
Coverlay/Soldermask
The coverlay or soldermask protects traces from environmental damage and prevents solder bridging. Liquid photoimageable soldermasks are commonly used on flex PCBs.
Stiffeners
Stiffeners made from materials like aluminum or FR-4 can be selectively added to flex PCBs to provide rigidity where needed. These add cost.
Flex PCB Layer Count
The number of conductive layers in a flex PCB impacts cost:
- Single-layer: One layer of traces, most affordable option
- Double-layer: Two conductive layers, moderate increase in cost
- Multilayer: Three or more layers, each additional layer increases cost
Complex designs may require more layers, while simpler circuits can be implemented with one or two layers.
Flex PCB Size
Larger flex PCBs require more raw materials driving up cost. Panel utilization also decreases with larger boards. Key size factors include:
- Overall dimensions: Bigger boards cost more
- Complexity: More complex board outlines increase fabrication complexity
- Quantity: Manufacturing many small boards costs more than fewer large boards
Production Quantity
As with most manufactured goods, PCB production costs decrease significantly with volume. Setup costs and materials waste are amortized over the production quantity.
Quantity | Typical Cost |
---|---|
1-10 boards | High per unit cost |
10-50 boards | Moderate per unit cost |
50-100 boards | Low per unit cost |
>100 boards | Minimum cost achieved |
Higher quantities allow manufacturers to maximize equipment utilization and streamline workflows.
Design for Manufacturing
Design choices that simplify flex PCB fabrication reduce costs. Some guidelines:
- Minimize the number of layers
- Use consistent trace widths and clearances
- Avoid small drilled holes and vias
- Place components on one side only if possible
- Utilize panel space efficiently
Consulting with manufacturers during design can identify areas for cost reduction.
Testing and Certifications
Testing and inspection requirements tack on additional costs. Common options include:
- Functional testing of assembled boards
- IPC testing standards
- UL safety certification
Only specify testing that is absolutely required for the application. Coordinate with your PCB partner to identify the optimal testing protocol.
Summary
To recap, the primary flex PCB cost drivers are:
- Materials selection
- Number of layers
- Board size and complexity
- Production volume
- Design considerations
- Testing requirements
Carefully evaluating each of these factors allows designers to control costs while still meeting design requirements.
Flex PCB Cost Reduction Tips
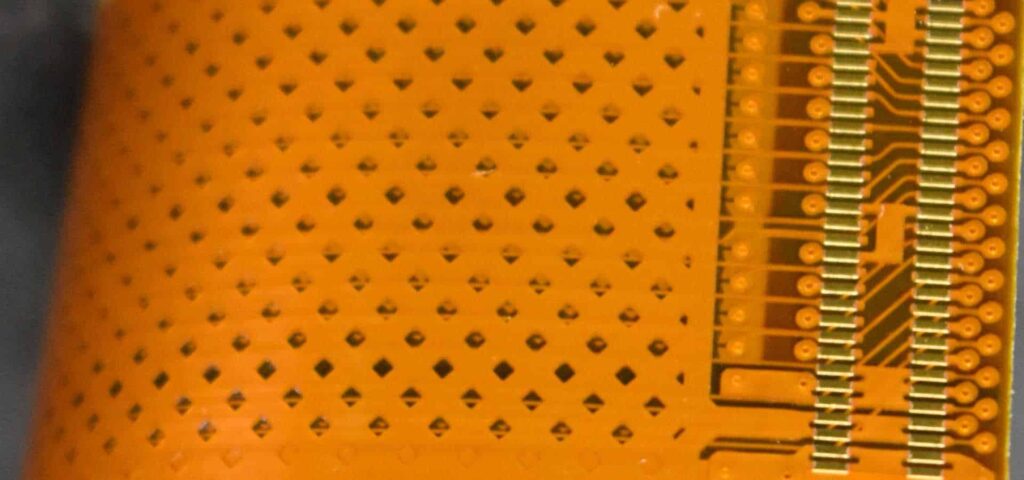
Here are some practical tips to reduce flex PCB costs while maintaining quality:
1. Use Single Layer Designs Where Possible
Single layer designs require the least materials and simplify fabrication. Multilayer boards should only be used when routing density necessitates it.
2. Select Lower-Cost Materials
Work with your PCB manufacturer to select the most cost-effective materials based on performance requirements. Thinner copper weights, acrylic adhesive, and halogen-free FR-4 stiffeners can reduce cost in many applications.
3. Design Efficient Panel Layouts
Panel design has a major impact on cost. Effective panel utilization using automated panelization software optimizes fabrication.
4. Standardize Design Rules
Consistent trace widths, hole sizes, spacing, and other rules simplify manufacturing. Avoid unique rules for each layer.
5. Consolidate Orders
Combining multiple PCB designs onto shared production panels reduces costs through economies of scale. Batch orders to achieve volume discounts.
6.Reduce Testing Requirements
Eliminate any non-essential testing or certification requirements. Only test critical parameters to ensure quality.
7. Work with Experienced Flex PCB Suppliers
Suppliers familiar with flex PCB design and fabrication can provide guidance to avoid pitfalls. Find a supplier willing to collaborate.
8. Take Advantage of Design Software
Use PCB design tools with built-in DFM analysis and panelization to lower cost. PCBViewer and Altium offer good options.
9. Ask for DFM Feedback
Have your supplier review designs and provide DFM suggestions before finalizing them. Take advantage of their expertise.
Flex PCB Cost Estimation
Determining the exact cost for a flex PCB requires obtaining pricing from a supplier. However, some rough flex PCB pricing guidelines are:
Flex PCB Type | Typical Cost Range |
---|---|
2-layer, simple design, small quantity | $200 – $500 |
4-layer, medium complexity, medium quantity | $1,000 – $5,000 |
Multilayer, high complexity, production volume | $5,000 – $10,000 |
Cost drivers like materials, layer count, size, and quantity influence pricing significantly. Getting multiple quotes from suppliers helps determine fair market pricing.
Online flex PCB calculators like PCBShopper provide very rough estimates, but quotes from manufacturers will be more accurate.
Flex PCB Cost Optimization Case Study
Acme Electronics designed a flex PCB for a wearable fitness tracker device. Their initial design resulted in the following pricing estimate:
Parameter | Initial Design |
---|---|
Layers | 6 layers |
Flex Stackup | Polyimide / copper / FR4 |
Quantity | 500 boards |
Panel Size | 250mm x 250mm |
Pricing Estimate | $8,000 |
The Acme team identified several areas to reduce costs:
Simplified Layer Stack: Dropped from 6 layers to 4 layers by optimizing routing.
Panel Layout: Increased panel size to 300mm x 600mm for better material utilization.
Material Selection: Changed adhesive to lower-cost acrylic type.
Build Consolidation: Combined the fitness tracker build with another product to reach 1,000 board quantity.
These changes reduced the pricing estimate to $5,500, a 31% cost reduction!
Careful cost analysis and optimization during the design stage allowed Acme to lower their flex PCB expenses substantially.
Flex PCB Cost FAQ’s
Here are some frequently asked questions about determining and reducing flex PCB costs:
Q: Does flex PCB cost increase linearly with size?
A: No, the relationship is not linear. Increased size has some fixed costs like setup charges in addition to the variable material costs, so the cost curve trends upwards exponentially with size.
Q: Can 2-layer flex PCBs be cost effective?
A: Yes, 2-layer designs with good layout can definitely be cost-optimized for many applications. The key is avoiding unnecessary layers.
Q: How much does impedance control features increase cost?
A: Impedanced traces require tighter tolerances so expect a 25-50% cost increase for controlled impedance.
Q: What design features have the biggest impact on cost?
A: Layer count, board size, and production volume are typically the three biggest cost drivers.
Q: Is it better to order few large panels or many small panels?
A: Generally, fewer large panels are preferred for optimal material utilization and fabrication efficiency. But small batches have fixed setup costs that offset this.
Conclusion
Determining flex PCB pricing involves assessing numerous design factors and fabrication process parameters. With an understanding of the key cost drivers, designers can make informed design and component choices to minimize overall expense. Partnering with an experienced flex PCB manufacturer is crucial for cost-optimized designs. Wise flex PCB cost management unlocks substantial savings in electronic products.
Leave a Reply