Introduction
Flex circuits, also known as flexible printed circuits (FPCs), are essential components in modern electronics. As devices continue to get smaller and more portable, the need for flex circuits is greater than ever. But what is the true cost of these versatile interconnects? In this article, we will analyze the various factors that contribute to overall flex circuit pricing. With a transparent understanding of flex circuit costs, you can make informed sourcing decisions.
What is a Flex Circuit?
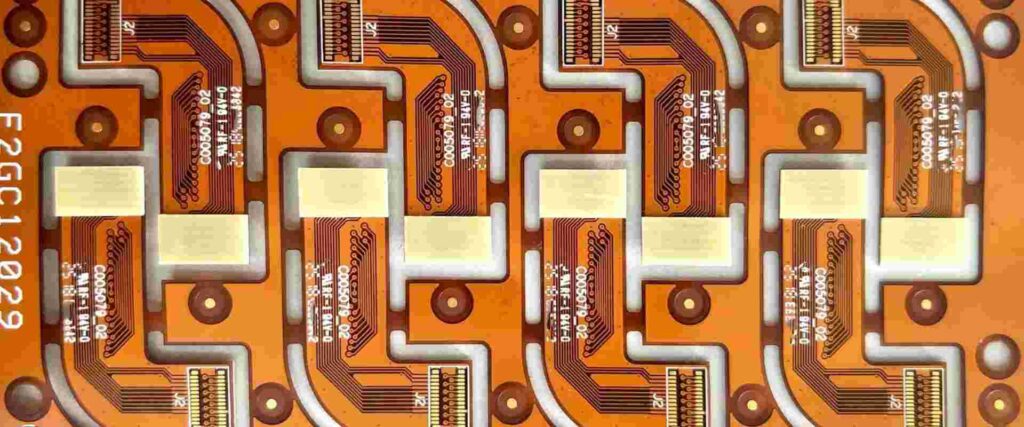
Before diving into costs, let’s review what exactly a flex circuit is and why they are useful.
A flex circuit is a thin, flexible circuit board made of flexible insulating substrate materials like polyimide or polyester. Flex circuits have conductive traces etched or printed onto the substrate, allowing current to flow between components. The circuits can bend, twist, and flex dynamically during use.
Key benefits of flex circuits:
- Extremely thin and lightweight – Takes up less space compared to rigid boards
- Flexible – Can bend and conform around objects
- Durable – Withstands vibration, shock, and repeated motion
- Reliable connections – Excellent for dynamic applications
- Efficient manufacturing – Low scrap rates compared to rigid boards
With these advantages, it’s no wonder flex circuits are found in everything from mobile devices and wearables to automotive parts and medical devices. Now let’s explore what goes into their cost.
Cost Drivers of Flex Circuits
Many factors influence the overall cost of flex circuits. Here are some of the most significant:
1. Design Complexity
The complexity of the flex circuit design is a primary driver of cost. Simpler circuits with fewer layers, components, and bends are cheaper to produce than highly complex designs.
Key design factors impacting cost include:
- Number of conductive layers – More layers increases costs
- Component density – More components means higher costs
- Bend radius – Tight bends add fabrication challenges
- Flex-to-rigid sections – Transitions drive up cost
- Shielding requirements – EMI shielding increases materials cost
Optimizing the design to be as straightforward as possible reduces cost.
2. Materials
The materials used in the flex circuit also significantly impact overall cost. More exotic, high-performance materials drive costs up.
Substrate – Polyimide is most common and cost-effective. Other options like polyester or transparent substrates are pricier.
Conductors – Copper is standard for traces. Silver or gold conductors add cost premiums.
Coverlay – Flexible insulator over conductors. Polyimide is frequently used. Liquid photoimageable coverlays are higher cost.
Adhesives – Used to bond layers. Acrylic or epoxy adhesives range in cost.
Stiffeners – Rigid sections often added. FR4, polyimides, aluminum can be used.
Selecting cheaper substrate and conductor materials reduces overall cost.
3. Quality
The quality of the flex circuit directly impacts pricing as well. More stringent quality standards require additional manufacturing steps and increase cost.
Key quality factors:
- Number of quality checks – More inspection equals higher cost
- Testing methods – Automated optical inspection (AOI) adds cost
- Tolerance requirements – Tighter tolerances require precision manufacturing
- Certifications – Industry standards like ISO raise cost
- Traceability – Full production lot traceability increases cost
Relaxing quality requirements where possible brings down costs.
4. Volume
As with most manufactured goods, volume substantially impacts per-unit pricing for flex circuits. Thanks to economies of scale, higher volumes provide opportunities for cost savings.
Volume price breaks typically occur at:
- 1-10 units – High per-unit cost for prototypes
- 10-50 units – Reduced per-unit pricing
- 50-100 units – Additional discounts
- 100+ units – Highest discount for production volumes
Volume pricing incentivizes larger orders to reduce per-unit costs.
5. Location
Where the flex circuit is manufactured also influences cost. There can be major price differences between regions.
Some guideline pricing by region:
- United States – $70-150+ per square foot
- Europe – $50-120+ per square foot
- China – $20-50 per square foot
- Other Asian countries – $30-60 per square foot
Labor, materials, and other overhead costs vary greatly by country. Sourcing overseas provides opportunities for significant cost savings.
Flex Circuit Cost Reduction Tips

Now that we’ve reviewed the key factors impacting flex circuit pricing, here are some tips for cost reduction:
- Simplify the design – Remove unnecessary layers or bends if possible. Consolidate components.
- Leverage cheaper materials – Use standard polyimide substrates rather than costly alternatives. Reduce conductor layers.
- Relax tolerances – Expand tolerances where functionality allows. This reduces rework and scrap.
- Minimize testing – Only test what is required for functionality and certification.
- Order larger volumes – Take advantage of volume discounts for 100+ units.
- Consider overseas production – Asian countries offer substantially lower manufacturing costs.
- Compare multiple suppliers – Get quotes from different companies to find the best price.
- Build a relationship – Develop a partnership with the supplier to receive preferred pricing.
While opting for the lowest cost option in each category may seem attractive, it’s important to balance cost reduction with meeting functional requirements and quality standards. Work closely with your flex circuit supplier to find the optimal cost solution.
Flex Circuit Cost Estimator
To get an initial idea of potential flex circuit costs for a project, you can use the following cost estimator:
Flex Circuit Cost Estimator
Parameter | Cost Impact |
---|---|
Circuit area | $10-20 per sq. in. |
Layers: 1 layer | Baseline cost |
Layers: 2 layers | + 15% |
Layers: 4+ layers | + 25% or more |
High-speed design | + 15% |
Impedance control | + 15% |
Flex-to-rigid sections | + 10% |
Adhesive lamination | + 10% |
Tight tolerances (+/- 0.10mm or less) | + 10-15% |
Automated optical inspection | + 10% |
Solder mask | + 5% |
SIlksceen legend | + 3% |
Gold conductors | + 15% or more |
This table provides estimated increases in cost above a simple single-layer base circuit without any special requirements. The costs are highly dependent on order volumes, supplier capabilities, and other factors. Use these percentages as a general guideline for the impacts of complexity, materials, quality processes and other parameters. Combining multiple features and requirements would have an additive effect on cost.
To receive an accurate flex circuit quote for your specific design, always consult directly with potential manufacturers. Provide them with complete specifications, quality expectations, and volume information. With this data, they can give you reliable flex circuit pricing.
Comparing Flex Circuit Suppliers
Once you have a flex circuit design completed, you’ll need to source a supplier for manufacturing. Here are some helpful tips for comparing and selecting flex circuit production partners:
- Get multiple quotes – Have at least 3-4 suppliers provide quotations for an apples-to-apples comparison.
- Review capabilities – Ensure suppliers have expertise in your design requirements like multilayer or high density flex.
- Ask about quality systems – What inspections, tests, certifications, and controls do they implement?
- Discuss volumes – Review if they offer benefits for higher volumes or charge more for low volumes.
- Evaluate lead times – How quickly can they deliver prototypes vs production runs?
- Review locations – Consider travel time, shipping costs, and communications.
- Compare service levels – Gauge responsiveness of sales and engineering support.
- Ask for references – Reach out to current customers to assess capabilities and performance.
- Review pricing – Compare total costs including materials, labor, testing, and overhead.
By evaluating suppliers in these areas, you can find the best partner that delivers the quality, responsiveness, and cost-effectiveness you need in a flex circuit producer.
Flex Circuit Cost FAQ
Here are answers to some frequently asked questions about the costs of flexible printed circuits:
Q: Does flex circuit size affect cost?
A: Yes, larger surface area drives cost up. Expect pricing around $10-20 per square inch depending on complexity. Smaller circuits have lower material and handling costs.
Q: Are multilayer flex circuits more expensive?
A: Yes, each additional layer adds cost for lamination, via drilling, and materials. 4+ layers could increase cost by 25% or more versus 2 layers.
Q: How much does flex-to-rigid board cost increase?
A: The transitions to rigid sections add fabrication steps like surface preparations. This often increases cost around 10% compared to pure flex.
Q: Is automated optical inspection (AOI) required?
A: No, but AOI improves quality control. The enhanced testing adds around 10% to the overall cost.
Q: Does location affect flex circuit cost?
A: Yes, overseas manufacturing has much lower labor costs. Asia averages 30-60% lower cost than the United States.
Q: Can I get discounts for ordering in high volumes?
A: Definitely. Price breaks typically occur at 100+ units. Costs reduce with economies of scale through larger orders.
Q: How can I reduce costs for simple flex designs?
A: Simplifying by reducing layers, tolerances, and test requirements produces the most cost-effective flex circuits.
Conclusion
This overview of the numerous considerations around flex circuit costs demonstrates the complexity in pricing these essential components. From design to quality to location and volumes, many interconnected factors influence cost. Understanding the impacts of these cost drivers enables informed decision making when sourcing flex circuits.
With the tips provided in this article, you can balance meeting technical requirements with controlling costs. Seek out flex circuit suppliers that provide transparent pricing based on your complete design specs and volume needs. The ideal partner will deliver a cost-optimized solution tailored to your specific project’s budget and performance goals.
Leave a Reply