Introduction to FFC and FPC
Flexible Flat Cables (FFC) and Flexible Printed Circuits (FPC) are two types of flexible interconnects widely used in various electronic devices. These interconnects offer several advantages over traditional rigid printed circuit boards (PCBs), such as reduced weight, increased flexibility, and improved space efficiency. While both FFC and FPC serve similar purposes, there are some key differences between them that make each suitable for specific applications.
In this article, we will explore the differences between FFC and FPC, their construction, applications, advantages, and disadvantages. We will also discuss the factors to consider when choosing between FFC and FPC for your electronic projects.
What is FFC?
Flexible Flat Cables (FFC), also known as ribbon cables, are a type of flexible interconnect consisting of a flat, ribbon-like cable with multiple conductors running parallel to each other. These conductors are typically made of copper and are insulated with a thin layer of plastic, such as polyester or polyimide.
Construction of FFC
FFCs are constructed by laminating a flat conductor cable between two insulating layers. The conductor cable is usually made of annealed copper, which is soft and flexible. The insulating layers are typically made of polyester or polyimide, which provide excellent electrical insulation and mechanical protection.
The conductors in an FFC are arranged in a single plane, with a fixed pitch between each conductor. The pitch refers to the distance between the centers of two adjacent conductors. Common pitches for FFCs include 0.5mm, 1.0mm, and 1.25mm.
Advantages of FFC
-
Flexibility: FFCs are highly flexible, allowing them to bend and fold easily without damaging the conductors. This flexibility enables designers to create more compact and space-efficient electronic devices.
-
Low profile: FFCs have a thin, flat profile, which makes them ideal for use in slim and portable electronic devices, such as smartphones, tablets, and laptops.
-
Easy to terminate: FFCs can be easily terminated using connectors specifically designed for them. These connectors often feature a ZIF (Zero Insertion Force) mechanism, which allows for easy insertion and removal of the cable without damaging the conductors.
-
Cost-effective: FFCs are generally more cost-effective than FPCs, especially for simpler designs with fewer layers and less complex routing.
Disadvantages of FFC
-
Limited current carrying capacity: Due to the thin, flat nature of FFCs, they have a limited current carrying capacity compared to traditional round cables or FPCs with thicker conductors.
-
Susceptibility to noise: FFCs are more susceptible to electromagnetic interference (EMI) and crosstalk compared to FPCs, as the conductors are not shielded.
-
Limited flexibility in design: FFCs have a fixed pitch between conductors, which limits the design flexibility compared to FPCs.
What is FPC?
Flexible Printed Circuits (FPC) are a type of flexible interconnect that consists of a thin, flexible substrate with printed conductors and components. FPCs are essentially a flexible version of rigid PCBs, offering the same functionality but with added flexibility.
Construction of FPC
FPCs are constructed by printing conductive traces on a flexible substrate, typically made of polyimide or polyester. The conductive traces are usually made of copper and are etched onto the substrate using a photolithographic process.
FPCs can have multiple layers, with conductive traces on each layer interconnected through plated through-holes (PTHs) or microvias. The layers are laminated together using adhesive materials, such as acrylic or epoxy.
Advantages of FPC
-
High density: FPCs can accommodate high-density circuitry, with fine pitch traces and small components. This allows for more complex designs and better space utilization compared to FFCs.
-
Improved signal integrity: FPCs offer better signal integrity compared to FFCs, as the conductive traces can be shielded and the substrate material provides better dielectric properties.
-
Design flexibility: FPCs allow for greater design flexibility, as the conductive traces can be routed in any direction and can have varying widths and spacing.
-
Integration of components: FPCs can have components, such as resistors, capacitors, and ICs, directly mounted onto the substrate, reducing the need for additional interconnects.
Disadvantages of FPC
-
Higher cost: FPCs are generally more expensive than FFCs, especially for complex designs with multiple layers and high-density circuitry.
-
Limited flexibility: Although FPCs are flexible, they are not as flexible as FFCs due to the presence of components and multiple layers.
-
Challenging assembly: The assembly process for FPCs can be more challenging compared to FFCs, as the components need to be precisely placed and soldered onto the substrate.
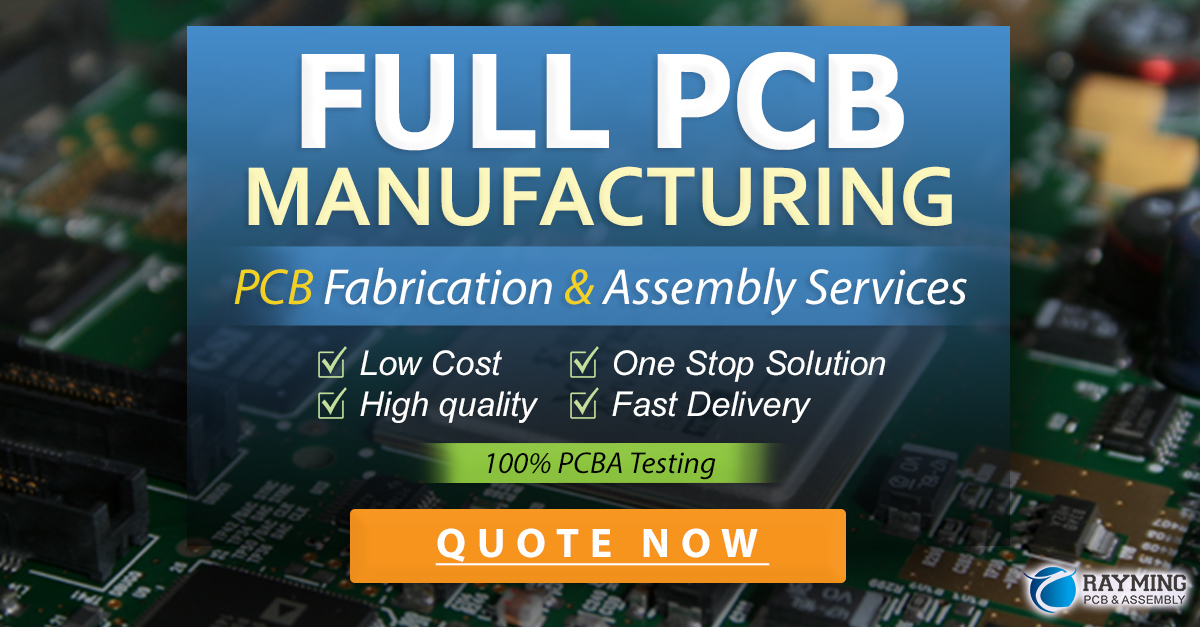
FFC vs FPC: Key Differences
Now that we have a better understanding of FFC and FPC, let’s summarize the key differences between them:
Characteristic | FFC | FPC |
---|---|---|
Construction | Flat conductor cable laminated between insulating layers | Conductive traces printed on a flexible substrate |
Flexibility | High flexibility, can bend and fold easily | Flexible, but not as flexible as FFC due to components and multiple layers |
Density | Lower density, fixed pitch between conductors | High density, can accommodate fine pitch traces and small components |
Signal Integrity | More susceptible to EMI and crosstalk | Better signal integrity, conductive traces can be shielded |
Design Flexibility | Limited design flexibility, fixed pitch between conductors | Greater design flexibility, conductive traces can be routed in any direction |
Cost | Generally more cost-effective, especially for simpler designs | More expensive, especially for complex designs with multiple layers |
Assembly | Easy to terminate using ZIF connectors | More challenging assembly process, components need to be precisely placed and soldered |
Applications of FFC and FPC
Both FFC and FPC find applications in various electronic devices, where flexibility, space efficiency, and lightweight are crucial. Some common applications include:
- Consumer electronics: Smartphones, tablets, laptops, digital cameras, and wearables.
- Automotive electronics: Infotainment systems, instrument clusters, and sensors.
- Medical devices: Portable medical equipment, implantable devices, and diagnostic tools.
- Industrial automation: Robotics, motion control systems, and machine vision.
- Aerospace and defense: Avionics, satellite systems, and military communication devices.
Factors to Consider When Choosing Between FFC and FPC
When deciding between FFC and FPC for your electronic project, consider the following factors:
-
Design complexity: If your design is simple, with fewer layers and less complex routing, FFC may be a more cost-effective option. However, if your design requires high-density circuitry and integration of components, FPC may be the better choice.
-
Flexibility requirements: If your application demands high flexibility, such as in wearable devices or moving parts, FFC may be the preferred option due to its superior flexibility.
-
Signal integrity: If your design is sensitive to EMI or requires better signal integrity, FPC may be the better choice, as it offers better shielding and dielectric properties.
-
Cost constraints: FFC is generally more cost-effective than FPC, especially for simpler designs. However, if your project requires the advanced features and benefits of FPC, the added cost may be justified.
-
Assembly process: Consider the assembly process for your project. FFCs are easier to terminate using ZIF connectors, while FPCs require precise placement and soldering of components.
FAQ
-
Q: Can FFC and FPC be used interchangeably?
A: While FFC and FPC serve similar purposes, they are not always interchangeable. The choice between FFC and FPC depends on the specific requirements of your project, such as design complexity, flexibility, signal integrity, and cost constraints. -
Q: What is the typical lifespan of FFC and FPC?
A: The lifespan of FFC and FPC depends on various factors, such as the materials used, the operating environment, and the stress subjected to the interconnects. In general, FFC and FPC can last for several years under normal operating conditions, but their lifespan may be reduced in harsh environments or under excessive stress. -
Q: Can FFC and FPC be customized for specific applications?
A: Yes, both FFC and FPC can be customized to meet the specific requirements of an application. Customization options include the number of conductors, pitch, length, and termination options for FFC, and the substrate material, conductor thickness, and layer count for FPC. -
Q: Are there any environmental concerns associated with FFC and FPC?
A: FFC and FPC materials, such as polyimide and polyester, are generally considered environmentally friendly and can be recycled. However, the recycling process may be complicated due to the presence of copper and other materials. It is essential to follow proper disposal and recycling guidelines to minimize environmental impact. -
Q: What are the common failure modes of FFC and FPC?
A: Common failure modes of FFC and FPC include: - Conductor breakage due to excessive bending or stress
- Insulation damage due to abrasion or chemical exposure
- Connector failure due to improper insertion or withdrawal
- Solder joint failure in FPCs due to thermal stress or vibration
To minimize the risk of failure, it is essential to follow proper handling, installation, and maintenance guidelines for FFC and FPC.
Conclusion
FFC and FPC are two types of flexible interconnects that offer several advantages over traditional rigid PCBs, such as reduced weight, increased flexibility, and improved space efficiency. While both FFC and FPC serve similar purposes, they have distinct differences in construction, flexibility, density, signal integrity, design flexibility, cost, and assembly process.
When choosing between FFC and FPC for your electronic project, consider factors such as design complexity, flexibility requirements, signal integrity, cost constraints, and assembly process. By understanding the key differences between FFC and FPC and carefully evaluating your project requirements, you can select the most suitable interconnect solution for your application.
As technology advances, both FFC and FPC will continue to play crucial roles in enabling the development of more compact, lightweight, and flexible electronic devices across various industries.
Leave a Reply