Introduction to PCB Fabrication and RAYPCB
Printed Circuit Board (PCB) fabrication is the process of manufacturing circuit boards that mechanically support and electrically connect electronic components using conductive pathways, tracks or signal traces etched from copper sheets laminated onto a non-conductive substrate. PCBs are essential components in virtually all modern electronic devices.
RAYPCB is a leading PCB manufacturer specializing in quick-turn, prototype to medium volume production of high-quality, custom-manufactured PCBs. With state-of-the-art facilities and experienced engineers, RAYPCB offers industry-leading 72 hours lead time for expedited medium and small volume PCB orders.
Advantages of RAYPCB’s Expedited PCB Fabrication Service
- Rapid 72 hours lead time for medium and small volume orders
- High-quality PCBs manufactured to IPC Class 2 or 3 standards
- Experienced engineers providing Design for Manufacturing (DFM) support
- State-of-the-art facilities with automated production lines
- Competitive pricing for prototype to medium volumes
- Wide range of PCB types and specifications supported
PCB Fabrication Process Overview
The PCB fabrication process typically involves the following key steps:
-
PCB Design and Layout: Creating the schematic design and layout files for the PCB using EDA (Electronic Design Automation) software.
-
DFM Check and File Preparation: Performing a Design for Manufacturing (DFM) check on the design files and preparing the Gerber and drill files for production.
-
PCB Material Selection and Cutting: Selecting the appropriate PCB substrate material (e.g., FR-4, Rogers, etc.) and cutting it to the required panel size.
-
Drilling: Drilling holes in the PCB panel for through-hole components and vias using CNC drilling machines.
-
Copper Patterning: Applying a photoresist layer, exposing it with the PCB pattern, developing the photoresist, and etching away the unwanted copper to create the circuit pattern.
-
Lamination (for multi-layer PCBs): Aligning and laminating multiple layers of patterned cores and prepregs under high temperature and pressure to form the complete multi-layer PCB Stackup.
-
Solder Mask Application: Applying a solder mask layer over the copper traces to protect them from oxidation and prevent solder bridges.
-
Silkscreen Printing: Printing text, logos, and component identifiers on the PCB surface using silkscreen printing.
-
Surface Finish: Applying a surface finish (e.g., HASL, ENIG, OSP) to the exposed copper pads to protect them from oxidation and improve solderability.
-
Electrical Testing: Performing electrical tests (e.g., continuity, isolation, HiPot) to ensure the PCB functions correctly.
-
Final Inspection and Packaging: Visually inspecting the PCBs for defects, packaging them, and preparing them for shipment.
PCB Fabrication Process Flow Chart
Step | Process | Description |
---|---|---|
1 | PCB Design and Layout | Create schematic and layout files |
2 | DFM Check and File Preparation | Perform DFM check and prepare production files |
3 | Material Selection and Cutting | Select PCB material and cut to size |
4 | Drilling | Drill holes for components and vias |
5 | Copper Patterning | Create copper circuit pattern |
6 | Lamination (multi-layer) | Laminate multiple patterned layers |
7 | Solder Mask Application | Apply solder mask over copper traces |
8 | Silkscreen Printing | Print text and identifiers on PCB |
9 | Surface Finish | Apply surface finish to exposed pads |
10 | Electrical Testing | Test PCB functionality |
11 | Final Inspection and Packaging | Inspect, package, and ship PCBs |
RAYPCB’s Expedited PCB Fabrication Capabilities
RAYPCB offers expedited PCB fabrication services with a lead time of just 72 hours for medium and small volume orders. This rapid turnaround time is made possible by RAYPCB’s advanced facilities, automated production lines, and experienced staff.
PCB Specifications Supported by RAYPCB
RAYPCB supports a wide range of PCB types and specifications, including:
- PCB Type: Single-sided, Double-sided, Multi-layer (up to 16 layers)
- Material: FR-4, High Tg FR-4, Rogers (RO4003C, RO4350B), Aluminium, Flexible
- Thickness: 0.4mm to 3.2mm
- Copper Weight: 0.5oz to 4oz
- Min. Trace/Space: 3mil/3mil
- Min. Hole Size: 0.2mm (mechanical), 0.1mm (laser)
- Solder Mask: Green, Red, Yellow, Blue, White, Black
- Silkscreen: White, Black, Yellow
- Surface Finish: HASL, Lead-free HASL, ENIG, OSP, Immersion Silver, Immersion Tin
PCB Specification Table
Specification | Options |
---|---|
PCB Type | Single-sided, Double-sided, Multi-layer (up to 16) |
Material | FR-4, High Tg FR-4, Rogers (RO4003C, RO4350B), Aluminium, Flexible |
Thickness | 0.4mm to 3.2mm |
Copper Weight | 0.5oz to 4oz |
Min. Trace/Space | 3mil/3mil |
Min. Hole Size | 0.2mm (mechanical), 0.1mm (laser) |
Solder Mask | Green, Red, Yellow, Blue, White, Black |
Silkscreen | White, Black, Yellow |
Surface Finish | HASL, Lead-free HASL, ENIG, OSP, Immersion Silver, Immersion Tin |
Advantages of RAYPCB’s Advanced Facilities and Automation
RAYPCB’s state-of-the-art facilities and automated production lines offer several advantages for expedited PCB fabrication:
- Faster Production Times: Automation allows for quicker processing of PCBs, reducing lead times.
- Improved Consistency and Quality: Automated systems ensure consistent and high-quality results, minimizing human error.
- Increased Efficiency: Automation streamlines the production process, improving overall efficiency and reducing waste.
- Cost Savings: Faster production times and increased efficiency lead to cost savings, which can be passed on to customers.
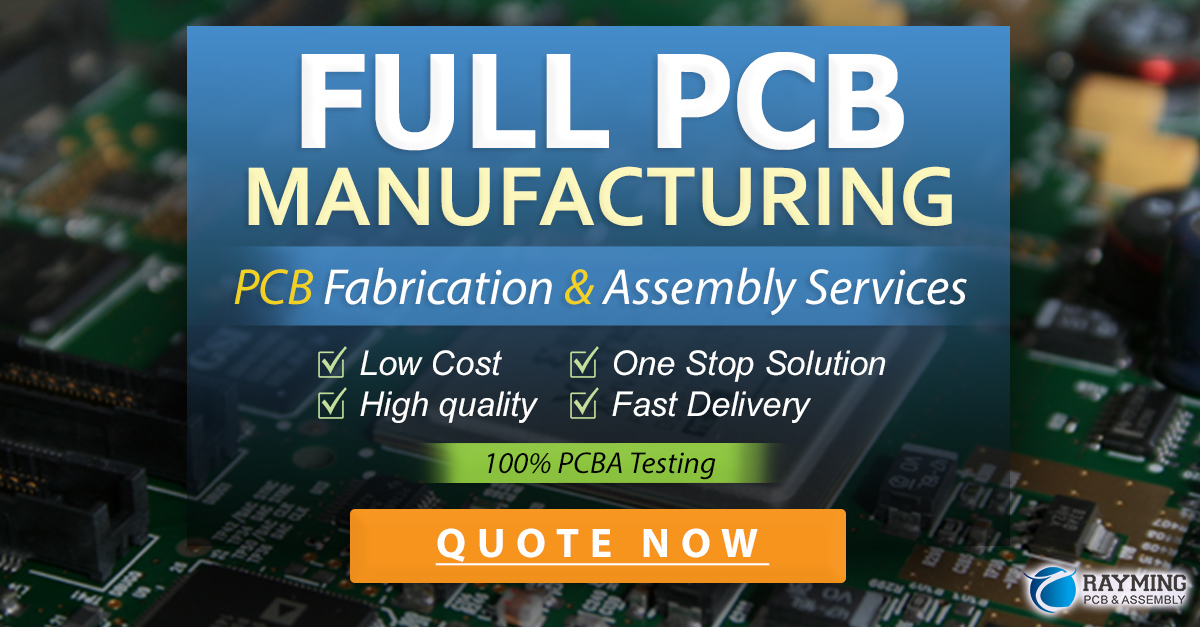
Design for Manufacturing (DFM) Support
RAYPCB’s experienced engineers provide Design for Manufacturing (DFM) support to ensure that PCB designs are optimized for manufacturability, reliability, and cost-effectiveness. DFM involves analyzing the PCB design files and providing feedback and recommendations to improve the design for production.
Benefits of DFM
Implementing DFM practices offers several benefits:
- Reduced Manufacturing Costs: Identifying and addressing potential manufacturing issues early in the design process can help reduce production costs.
- Improved Reliability: DFM helps ensure that PCBs are designed to be reliable and robust, minimizing the risk of failures and defects.
- Faster Time-to-Market: By optimizing designs for manufacturability, DFM can help expedite the production process and reduce lead times.
- Enhanced Collaboration: DFM promotes collaboration between PCB designers and manufacturers, fostering a better understanding of each other’s requirements and constraints.
Common DFM Guidelines
Some common DFM guidelines for PCB design include:
- Ensuring proper trace width and spacing for the desired manufacturing capabilities
- Avoiding acute angles in traces to prevent acid traps during etching
- Providing sufficient clearance around holes and vias for reliable drilling and plating
- Using standard drill sizes and minimizing the number of different drill sizes
- Ensuring solder mask openings are not too small or too close to each other
- Providing adequate space for silkscreen text and symbols
Ordering Process and Lead Times
Ordering PCBs from RAYPCB is a straightforward process, and the company offers industry-leading lead times for expedited medium and small volume orders.
How to Order PCBs from RAYPCB
- Submit your PCB design files: Upload your Gerber and drill files to RAYPCB’s online quotation system or send them via email.
- Receive a quote: RAYPCB will review your files and provide a quote for your PCB order within 24 hours.
- Confirm your order: Review the quote and confirm your order by accepting the quote and providing payment.
- Track your order: RAYPCB will provide regular updates on the status of your order, and you can track its progress online.
Lead Times for Expedited Medium and Small Volume Orders
RAYPCB offers a 72 hours lead time for expedited medium and small volume PCB orders. This lead time applies to orders that meet the following criteria:
- PCB Quantity: Up to 50 pieces for medium volume, up to 10 pieces for small volume
- PCB Layers: Up to 8 layers
- PCB Size: Up to 500mm x 500mm
For orders that exceed these criteria, RAYPCB will provide a custom lead time based on the specific requirements of the order.
Expedited Lead Time Table
Order Type | PCB Quantity | PCB Layers | PCB Size | Lead Time |
---|---|---|---|---|
Medium Volume | Up to 50 pcs | Up to 8 | Up to 500x500mm | 72 hours |
Small Volume | Up to 10 pcs | Up to 8 | Up to 500x500mm | 72 hours |
Conclusion
RAYPCB’s expedited medium and small volume PCB fabrication service, with its 72 hours lead time, is an excellent choice for customers who require high-quality PCBs quickly. The company’s advanced facilities, automated production lines, and experienced staff ensure that PCBs are manufactured to the highest standards while meeting tight deadlines.
By offering Design for Manufacturing (DFM) support and a wide range of PCB specifications, RAYPCB can accommodate the diverse needs of its customers. The straightforward ordering process and regular order updates make working with RAYPCB a seamless experience.
Frequently Asked Questions (FAQ)
-
Q: What is the minimum order quantity for expedited PCB fabrication at RAYPCB?
A: There is no minimum order quantity for expedited PCB fabrication at RAYPCB. However, the 72 hours lead time applies to medium volume orders of up to 50 pieces and small volume orders of up to 10 pieces. -
Q: What file formats does RAYPCB accept for PCB design submission?
A: RAYPCB accepts industry-standard Gerber and drill files (RS-274X) for PCB design submission. These files should include all the necessary layers, such as copper, solder mask, silkscreen, and drill data. -
Q: Does RAYPCB offer assembly services in addition to PCB fabrication?
A: Yes, RAYPCB offers PCB Assembly services, including surface mount (SMT) and through-hole (THT) assembly. However, the 72 hours lead time applies only to PCB fabrication and not assembly. -
Q: What quality standards does RAYPCB adhere to?
A: RAYPCB manufactures PCBs in accordance with IPC Class 2 and 3 standards, ensuring high-quality and reliable products. The company also holds ISO 9001:2015 and UL certifications. -
Q: How does RAYPCB Ensure the confidentiality of customer designs?
A: RAYPCB takes the confidentiality of customer designs very seriously. The company has strict non-disclosure policies in place and ensures that all customer data is securely stored and accessed only by authorized personnel on a need-to-know basis.
Leave a Reply