What is PCB Conformal Coating?
PCB conformal coating is a thin polymeric film which conforms to the contours of a printed circuit board to protect the board and its components from harsh environments. The coating ‘conforms’ to the board, covering and protecting the different shapes and components.
Types of Conformal Coatings
There are five main types of PCB conformal coatings:
Coating Type | Characteristics |
---|---|
Acrylic | Easy to apply and remove, low cost, good moisture and fungal resistance |
Silicone | Excellent flexibility and high temperature resistance, more difficult to apply and repair |
Urethane | Excellent abrasion and chemical resistance, harder to apply, repair and remove |
Epoxy | Excellent resistance to chemicals and abrasion, very hard and durable, difficult to apply and remove |
Parylene | Excellent barrier properties, uniformly coats all surfaces, applied via vapor deposition, very thin coatings achievable |
Why Use Conformal Coating on PCBs?
Conformal coating provides several key benefits and protections for PCBs:
Environmental Protection
Conformal coatings protect PCBs from moisture, humidity, dust, dirt, fungus, thermal cycling, and airborne contaminants. This protection is critical for PCBs operating in harsh environments.
Insulation and Isolation
The coating provides electrical insulation and isolation between components, preventing short circuits and arcing. This is especially important for high voltage applications.
Mechanical Support
The coating provides some mechanical support and protection against vibration and physical damage. It helps to hold components in place.
When is Conformal Coating Needed?
Not all PCBs need conformal coating. It depends on the operating environment and reliability requirements. Here are some situations where conformal coating should be considered:
Harsh Environments
If the PCB will be exposed to moisture, humidity, dust, chemicals, or wide temperature swings, conformal coating is often necessary. Examples include:
- Outdoor equipment
- Automotive electronics
- Marine and aerospace applications
- Industrial controls
High Reliability Requirements
For applications where reliability is critical, such as medical devices, aerospace systems, and critical infrastructure, conformal coating adds an extra layer of protection against failure.
Condensation Concerns
If the PCB may experience condensation due to temperature changes or high humidity, conformal coating can prevent short circuits and corrosion caused by the condensation.
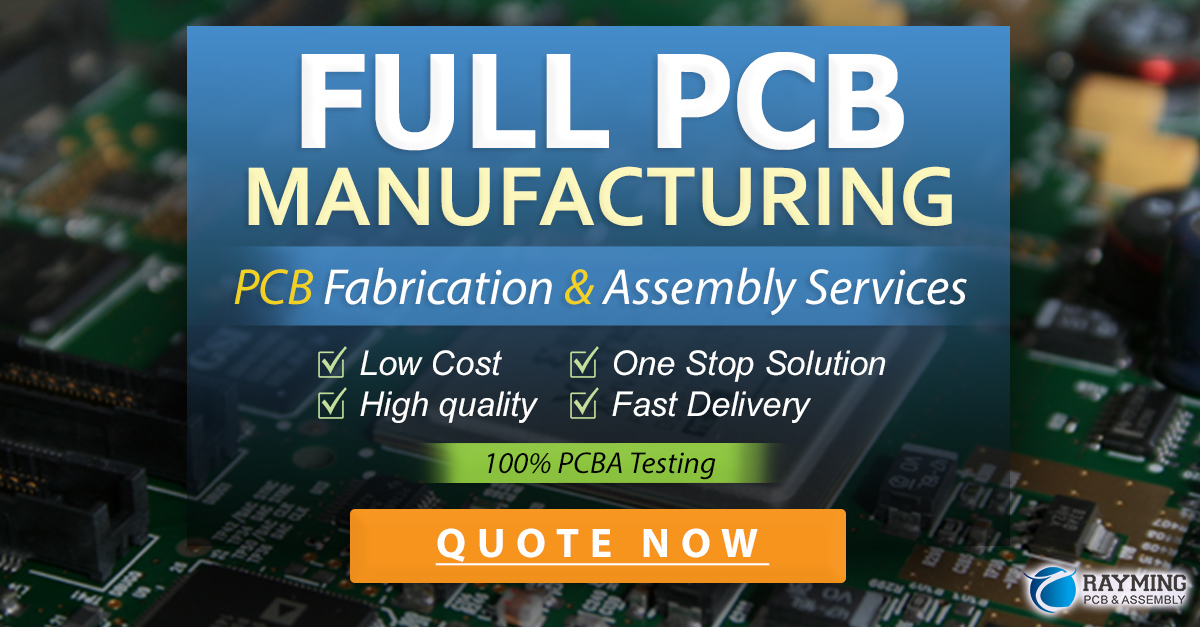
Conformal Coating Standards and Specifications
There are several standards and specifications that cover PCB conformal coating:
Standard | Description |
---|---|
IPC-CC-830 | The most widely used standard, covers the requirements for qualification and performance of conformal coatings |
MIL-I-46058C | Military specification for conformal coatings |
IEC 61086 | International standard for conformal coatings |
UL 746E | Underwriters Laboratories standard for conformal coatings |
How is Conformal Coating Applied?
There are several methods for applying conformal coating to PCBs:
Brushing
Brushing is a manual method suitable for low volume production or repair. It is low cost but can result in uneven coating thickness.
Spraying
Spraying is the most common application method. It can be done manually or automated. Proper masking is important to prevent coating of unwanted areas.
Dipping
Dipping involves immersing the PCB in a tank of coating material. It coats both sides of the board but can result in a thicker coating than other methods.
Selective Coating
Selective coating uses automated systems to apply coating only to specific areas of the PCB. This is useful when certain components must not be coated.
Considerations for Conformal Coating
When deciding whether to use conformal coating and which type to use, there are several factors to consider:
Material Compatibility
The coating must be compatible with the PCB materials, components, and any expected contaminants. Some coatings may react with certain plastics or metals.
Repairability
Some coatings, like silicone and urethane, are difficult to remove for repairs. This should be considered for applications where repairs may be necessary.
Thickness
The coating thickness affects its protective properties as well as its impact on the size and weight of the PCB. Thicker coatings provide more protection but can be problematic for tight spaces.
Curing
Some coatings require heat curing which can damage heat-sensitive components. UV or moisture curing may be preferable in these cases.
Cost
Conformal coating adds cost to the PCB Assembly process. The cost varies with the type of coating and application method. This cost must be weighed against the benefits in reliability and protection.
Frequently Asked Questions
1. Can conformal coating be removed?
Yes, conformal coating can be removed for rework or repair. The ease of removal depends on the type of coating. Acrylic coatings are relatively easy to remove, while silicone and urethane coatings are more difficult.
2. How thick should the conformal coating be?
The thickness of the conformal coating depends on the type of coating and the application requirements. Typical thicknesses range from 25-250 microns (0.001-0.010 inches). Thicker coatings provide more protection but can be problematic in tight spaces.
3. Can conformal coating be applied over components?
Yes, conformal coating can be applied over components. However, some components, such as connectors, switches, and adjustable resistors, may need to be masked to prevent the coating from interfering with their function.
4. Does conformal coating affect the electrical properties of the PCB?
Conformal coating can have a slight effect on the electrical properties of the PCB, such as increasing the dielectric constant and dissipation factor. However, these effects are usually minimal and can be accounted for in the PCB Design.
5. How long does conformal coating last?
The lifespan of a conformal coating depends on the type of coating and the environmental conditions. Under normal conditions, a conformal coating can last the lifetime of the product. However, in harsh environments, the coating may degrade over time and need to be reapplied.
Conclusion
Conformal coating is a valuable tool for protecting PCBs from environmental hazards and improving reliability. However, it is not necessary for all applications. The decision to use conformal coating should be based on a careful consideration of the operating environment, reliability requirements, and the costs and benefits of the coating process.
When conformal coating is needed, the choice of coating material and application method depends on the specific requirements of the PCB and the manufacturing process. By understanding the properties and tradeoffs of different coatings and application methods, manufacturers can optimize the protection and reliability of their PCB assemblies.
Leave a Reply