Introduction to Heatsinks
A heatsink is a passive heat exchanger that transfers heat generated by an electronic or a mechanical device to a fluid medium, often air or a liquid coolant, where it is dissipated away from the device, thereby allowing regulation of the device’s temperature. In computers, heatsinks are used to cool central processing units or graphics processors. Heatsinks are used with high-power semiconductor devices such as power transistors and optoelectronics such as lasers and light emitting diodes (LEDs), where the heat dissipation ability of the component itself is insufficient to moderate its temperature.
The Importance of Heatsinks in Electronics
Heatsinks are essential components in modern electronic devices. They prevent the overheating of critical components, which can lead to decreased performance, malfunctions, or even permanent damage. By efficiently dissipating heat, heatsinks help maintain optimal operating temperatures, ensuring the reliability and longevity of electronic systems.
The Need for DIY Heatsinks
While heatsinks are readily available for purchase, there are situations where a custom solution is required. This may be due to unique device specifications, space constraints, or the need for cost-effective alternatives. In such cases, building a DIY heatsink can be a valuable skill.
Understanding Heat Transfer Principles
To effectively design and build a DIY heatsink, it is crucial to understand the basic principles of heat transfer. Heat transfer occurs through three primary mechanisms: conduction, convection, and radiation.
Conduction
Conduction is the transfer of heat through direct contact between materials. In a heatsink, conduction occurs between the heat-generating component and the heatsink material, typically metal, which then conducts the heat away from the source.
Convection
Convection is the transfer of heat through the movement of fluids or gases. In the context of heatsinks, convection refers to the transfer of heat from the heatsink surface to the surrounding air. The effectiveness of convection depends on factors such as surface area, air flow rate, and temperature difference between the heatsink and the ambient air.
Radiation
Radiation is the transfer of heat through electromagnetic waves. While radiation plays a role in heat transfer, its contribution is generally less significant compared to conduction and convection in heatsink design.
Factors Affecting Heatsink Performance
Several factors influence the performance and efficiency of a heatsink. Understanding these factors is essential when designing and building a DIY heatsink.
Material Selection
The choice of material significantly impacts the heatsink’s performance. Common materials used for heatsinks include:
Material | Thermal Conductivity (W/mK) |
---|---|
Aluminum | 205 |
Copper | 401 |
Silver | 429 |
Diamond | 2,300 |
Aluminum is a popular choice due to its good thermal conductivity, lightweight, and cost-effectiveness. Copper offers superior thermal conductivity but is heavier and more expensive. Silver and diamond, while having excellent thermal properties, are rarely used due to their high cost.
Surface Area
The surface area of a heatsink plays a crucial role in its heat dissipation capacity. A larger surface area allows for more heat transfer through convection. This is why heatsinks often feature fins or other protrusions, which increase the overall surface area without significantly increasing the heatsink’s size.
Thermal Interface Material (TIM)
Thermal interface materials, such as thermal grease or thermal pads, are used to fill the microscopic gaps between the heat source and the heatsink. These materials improve heat transfer by ensuring proper contact and minimizing air gaps. The selection of an appropriate TIM can greatly enhance the heatsink’s performance.
Airflow and Orientation
The effectiveness of a heatsink also depends on the airflow around it. Adequate airflow helps in removing heat from the heatsink through convection. The orientation of the heatsink relative to the airflow direction can impact its performance. Generally, a heatsink should be oriented to allow for maximum airflow over its surface area.
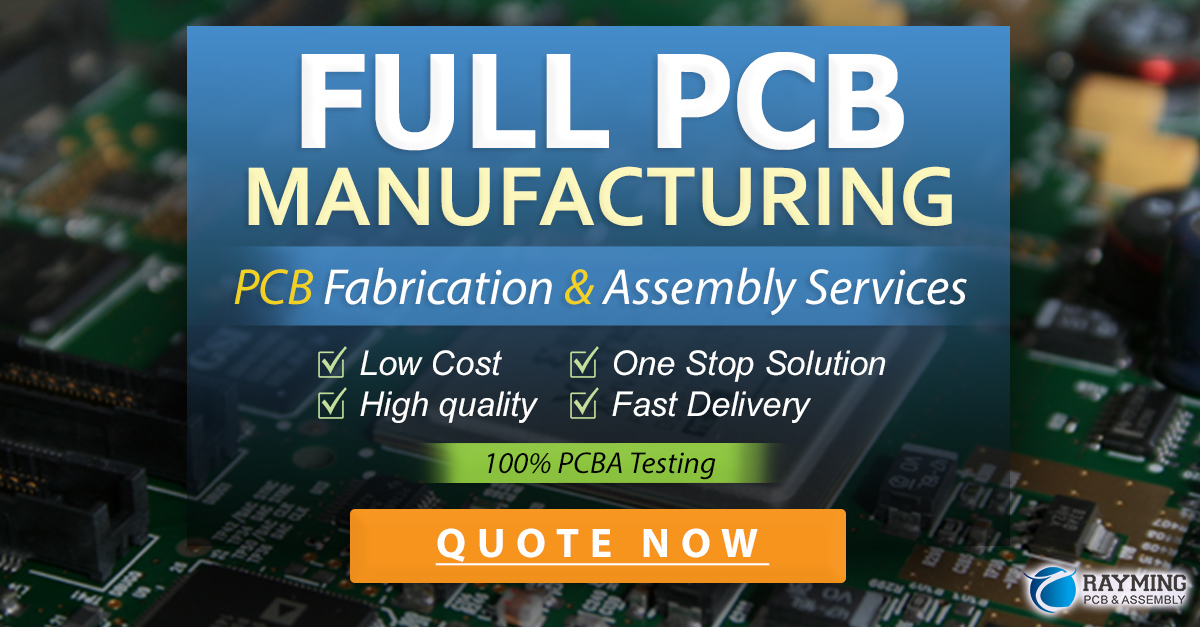
Designing a DIY Heatsink
When designing a DIY heatsink, consider the following steps:
Step 1: Determine the Heat Dissipation Requirements
Estimate the amount of heat generated by the device that needs cooling. This information is usually provided by the manufacturer in the form of thermal design power (TDP) or maximum power dissipation. Knowing the heat dissipation requirements will help you size your heatsink appropriately.
Step 2: Choose the Heatsink Material
Select a material with high thermal conductivity, such as aluminum or copper. Consider factors like weight, cost, and ease of machining when making your choice.
Step 3: Design the Heatsink Geometry
Determine the size and shape of your heatsink based on the available space and the heat dissipation requirements. Incorporate fins or other features to increase the surface area for better heat dissipation.
Step 4: Consider Manufacturability
When designing your heatsink, keep in mind the manufacturing process you will use. Whether you plan to machine the heatsink yourself or have it fabricated by a third party, ensure that your design is feasible and can be manufactured with the available tools and techniques.
Step 5: Optimize for Airflow
Design your heatsink to allow for optimal airflow. Consider the orientation of the fins and the overall shape of the heatsink to maximize airflow and improve convective heat transfer.
Building a DIY Heatsink
Once you have designed your heatsink, follow these steps to build it:
Step 1: Gather Materials and Tools
Collect the necessary materials, such as aluminum or copper stock, and tools like saws, drills, and files. If you plan to machine the heatsink, ensure you have access to the required equipment.
Step 2: Cut the Heatsink Base
Cut the heatsink base to the desired size using a saw or other cutting tool. Ensure that the base is flat and smooth.
Step 3: Create the Fins
Cut or machine the fins according to your design. If using a saw, make sure to keep the cuts straight and evenly spaced. If using a milling machine, follow your design specifications carefully.
Step 4: Attach the Fins to the Base
Secure the fins to the heatsink base using a suitable method, such as soldering, brazing, or epoxy. Ensure that the fins are firmly attached and make good contact with the base.
Step 5: Finish the Heatsink
Clean and polish the heatsink to remove any burrs or rough edges. If desired, you can apply a protective coating or anodize the heatsink to improve its appearance and durability.
Testing and Installation
After building your DIY heatsink, it is essential to test its performance and install it properly.
Testing the Heatsink
To test your heatsink, follow these steps:
- Attach a temperature sensor to the device that needs cooling.
- Apply a thermal load to the device, such as running a stress test or a benchmark.
- Monitor the temperature of the device with and without the heatsink installed.
- Compare the temperature readings to ensure that the heatsink is effectively dissipating heat.
Installing the Heatsink
When installing your DIY heatsink, keep the following points in mind:
- Clean the mating surfaces of the device and the heatsink to ensure proper contact.
- Apply a suitable thermal interface material, such as thermal grease or a thermal pad, to fill any gaps between the device and the heatsink.
- Securely fasten the heatsink to the device using the appropriate mounting mechanism, such as screws or clips.
- Ensure that the heatsink is oriented correctly to allow for optimal airflow.
Frequently Asked Questions (FAQ)
1. Can I use any metal for making a DIY heatsink?
While metals with high thermal conductivity, such as aluminum and copper, are ideal for heatsinks, other metals like steel or brass can also be used. However, their lower thermal conductivity may result in reduced heat dissipation performance.
2. How do I determine the size of the heatsink I need?
The size of the heatsink depends on factors like the amount of heat generated by the device, the available space, and the desired operating temperature. You can use online heatsink calculators or consult with thermal engineering experts to determine the appropriate heatsink size for your application.
3. Can I use a 3D printer to make a heatsink?
Yes, you can use a 3D printer to create a heatsink. However, the material used should have good thermal conductivity. Some 3D printing filaments, such as those containing metal particles, can be suitable for heatsink applications.
4. Is it necessary to use a thermal interface material?
Yes, using a thermal interface material is crucial for optimal heat transfer between the device and the heatsink. Without a TIM, air gaps can form, reducing the effectiveness of the heatsink.
5. Can I use a DIY heatsink in high-powered electronic devices?
While DIY heatsinks can be effective for low to moderate heat dissipation requirements, high-powered electronic devices may require more advanced cooling solutions. In such cases, it is advisable to use commercially available heatsinks or consult with thermal management experts to ensure proper cooling and safety.
Conclusion
Building a DIY heatsink can be a rewarding and cost-effective solution for cooling electronic devices. By understanding heat transfer principles, selecting the right materials, and following proper design and manufacturing techniques, you can create a heatsink tailored to your specific needs. However, it is essential to test your heatsink thoroughly and ensure that it provides adequate cooling for your application. With the knowledge and skills gained from this guide, you can explore the world of DIY heatsinks and unlock new possibilities in electronic cooling.
Leave a Reply