Introduction to Automotive PCBs
Automotive Printed Circuit Boards (PCBs) are an essential component in modern vehicles, enabling the integration of sophisticated electronic systems that enhance safety, performance, and user experience. As the automotive industry continues to evolve, with a growing emphasis on electric vehicles (EVs), autonomous driving, and connected car technologies, the demand for high-quality, reliable, and innovative automotive PCBs is on the rise.
In this article, we will explore the latest trends, challenges, and opportunities in the automotive PCB market, focusing on the newest developments as of 2024. We will also discuss the key factors driving the growth of this industry and the technical requirements for designing and manufacturing automotive PCBs.
Market Overview and Growth Drivers
The global automotive PCB market is expected to experience significant growth in the coming years, driven by several key factors:
- Increasing demand for electric vehicles (EVs) and hybrid electric vehicles (HEVs)
- Growing adoption of advanced driver assistance systems (ADAS) and autonomous driving technologies
- Rising demand for connected car features and infotainment systems
- Stringent government regulations on vehicle safety and emissions
According to recent market research reports, the automotive PCB market is projected to reach USD 14.5 billion by 2026, growing at a CAGR of 6.8% during the forecast period (2021-2026).
Year | Market Size (USD Billion) | Growth Rate (CAGR) |
---|---|---|
2021 | 9.8 | – |
2022 | 10.5 | 7.1% |
2023 | 11.2 | 6.7% |
2024 | 12.0 | 7.1% |
2025 | 12.8 | 6.7% |
2026 | 14.5 | 6.8% |
Key Applications of Automotive PCBs
Automotive PCBs find applications in various systems and components within a vehicle, including:
- Powertrain control modules (PCMs)
- Engine control units (ECUs)
- Electronic power steering (EPS) systems
- Advanced driver assistance systems (ADAS)
- Infotainment and telematics systems
- Body control modules (BCMs)
- Battery management systems (BMS) for EVs and HEVs
As vehicles become more electrified and autonomous, the complexity and functionality of these systems continue to increase, requiring more advanced and reliable automotive PCBs.
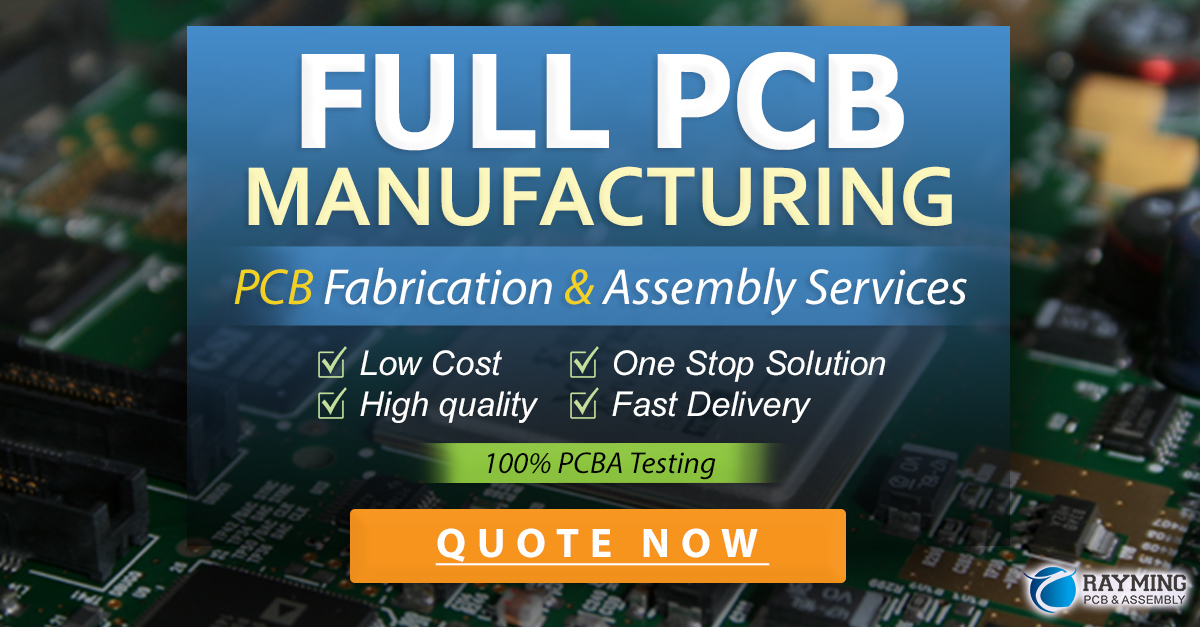
Technical Requirements and Challenges
Designing and manufacturing automotive PCBs presents unique challenges due to the harsh operating environment and stringent reliability requirements. Some of the key technical requirements for automotive PCBs include:
- High temperature resistance (up to 150°C)
- Vibration and shock resistance
- Moisture and chemical resistance
- Electromagnetic compatibility (EMC) and electromagnetic interference (EMI) shielding
- Miniaturization and high-density interconnect (HDI) design
- Compliance with industry standards (e.g., AEC-Q100, ISO 26262)
To meet these requirements, automotive PCB manufacturers must employ advanced materials, such as high-Tg laminates, and specialized manufacturing processes, such as Controlled Impedance routing and conformal coating.
Latest Trends and Innovations
As of 2024, several new trends and innovations are shaping the automotive PCB industry:
1. Flexible and Rigid-Flex PCBs
The growing demand for miniaturization and weight reduction has led to increased adoption of flexible and rigid-flex PCBs in automotive applications. These PCBs offer improved packaging efficiency, reduced weight, and enhanced reliability compared to traditional rigid PCBs.
2. Advanced Materials and Coatings
Automotive PCB manufacturers are exploring new materials and coatings to enhance the performance and durability of their products. Some examples include:
- Ceramic-filled laminates for improved thermal management
- Halogen-free and low-loss materials for higher signal integrity
- Nanoparticle-based conformal coatings for better environmental protection
3. Embedded Components and 3D PCBs
Embedding components within the PCB Substrate and utilizing 3D PCB Design techniques can further reduce the size and weight of automotive electronic systems. These approaches also enable better thermal management and improved signal integrity.
4. Smart and Multi-functional PCBs
The integration of sensors, antennas, and other functional components directly into the PCB is becoming more common in automotive applications. These smart and multi-functional PCBs enable advanced features such as wireless connectivity, condition monitoring, and predictive maintenance.
Automotive PCB Supply Chain and Key Players
The automotive PCB supply chain involves a complex network of raw material suppliers, PCB manufacturers, electronic component manufacturers, and automotive OEMs and Tier 1 suppliers. Some of the key players in the automotive PCB market include:
- Nippon Mektron
- Meiko Electronics
- Unimicron
- Tripod Technology
- Samsung Electro-Mechanics
- CMK Corporation
- TTM Technologies
- Daeduck Electronics
- Chin Poon Industrial
- KCE Electronics
As the demand for automotive PCBs continues to grow, collaboration and partnerships among these players are becoming increasingly important to ensure a robust and resilient supply chain.
Conclusion and Future Outlook
The automotive PCB market is poised for significant growth in the coming years, driven by the increasing adoption of electric vehicles, autonomous driving technologies, and connected car features. To meet the evolving needs of the automotive industry, PCB manufacturers must continue to innovate and develop advanced materials, design techniques, and manufacturing processes.
As we look ahead to 2024 and beyond, the successful players in the automotive PCB market will be those who can effectively navigate the technical challenges, adapt to changing market dynamics, and deliver high-quality, reliable, and cost-effective solutions to their customers.
Frequently Asked Questions (FAQ)
1. What are the key differences between automotive PCBs and standard PCBs?
Automotive PCBs are designed to withstand the harsh operating environment of a vehicle, which includes exposure to high temperatures, vibrations, moisture, and chemicals. They also need to meet stringent reliability and safety requirements, such as AEC-Q100 and ISO 26262. In contrast, standard PCBs are designed for less demanding applications and may not have the same level of durability and reliability.
2. What are the most common materials used in automotive PCBs?
The most common materials used in automotive PCBs include FR-4, high-Tg laminates, polyimide, and ceramic-filled laminates. These materials are chosen for their ability to withstand high temperatures, mechanical stress, and moisture while maintaining excellent electrical properties.
3. How do flexible and rigid-flex PCBs benefit automotive applications?
Flexible and rigid-flex PCBs offer several advantages for automotive applications, including reduced weight, improved packaging efficiency, and enhanced reliability. They can conform to complex shapes and fit into tight spaces, enabling more compact and lightweight electronic systems. Additionally, the flexibility of these PCBs helps to absorb vibrations and shocks, improving the overall durability of the system.
4. What are the key challenges in designing and manufacturing automotive PCBs?
Some of the key challenges in designing and manufacturing automotive PCBs include:
- Meeting the high-temperature and environmental resistance requirements
- Achieving miniaturization and high-density interconnect (HDI) designs while maintaining signal integrity
- Ensuring electromagnetic compatibility (EMC) and shielding against electromagnetic interference (EMI)
- Complying with industry standards and safety regulations
- Managing the complex supply chain and ensuring the availability of raw materials and components
5. How are automotive PCB manufacturers adapting to the growth of electric vehicles and autonomous driving technologies?
Automotive PCB manufacturers are adapting to the growth of electric vehicles and autonomous driving technologies by investing in research and development, expanding their product portfolios, and collaborating with key players in the industry. They are focusing on developing advanced materials, design techniques, and manufacturing processes that can meet the specific requirements of these emerging applications, such as high-voltage isolation, thermal management, and high-speed data transmission.
Leave a Reply