Introduction to PCB Assembly
Printed Circuit Board (PCB) assembly is a crucial process in the manufacturing of electronic devices. It involves the placement and soldering of electronic components onto a PCB to create a functional circuit. The process requires precision, accuracy, and adherence to strict quality standards to ensure the reliability and performance of the final product.
In this article, we will explore the different types of PCB assembly services available and provide tips to help you make your PCB assembly project a success.
Types of PCB Assembly Services
1. Surface Mount Assembly (SMT)
Surface Mount Technology (SMT) is the most common type of PCB assembly. It involves placing surface mount components directly onto the surface of the PCB and soldering them in place using automated machines. SMT is known for its high precision, speed, and the ability to accommodate smaller components, resulting in more compact and efficient PCB designs.
Advantages of SMT:
- Higher component density
- Faster assembly process
- Improved reliability
- Better high-frequency performance
2. Through-Hole Assembly (THA)
Through-Hole Assembly involves inserting component leads through holes drilled in the PCB and soldering them on the opposite side. This method is typically used for larger components or those that require more mechanical stability. Though THA is slower and less efficient than SMT, it remains essential for certain applications.
Advantages of THA:
- Better mechanical stability
- Easier manual assembly and repair
- Suitable for high-power components
3. Mixed Technology Assembly (MTA)
Mixed Technology Assembly combines both SMT and THA techniques on a single PCB. This approach is used when a design requires the benefits of both technologies, such as when using through-hole connectors alongside surface mount components. MTA allows for more complex and versatile PCB designs.
4. Electro-Mechanical Assembly (EMA)
Electro-Mechanical Assembly involves integrating mechanical components, such as connectors, switches, and heat sinks, with the PCB. This process requires specialized skills and tools to ensure proper fitting and functionality of the mechanical parts in relation to the electronic components.
PCB Assembly Process
The PCB assembly process typically consists of the following steps:
-
Solder Paste Application: Solder paste is applied to the PCB pads using a stencil or screen printing process.
-
Component Placement: SMT components are placed onto the solder paste using pick-and-place machines, while through-hole components are inserted manually or with specialized machinery.
-
Reflow Soldering: The PCB is heated in a reflow oven, melting the solder paste and creating a permanent connection between the components and the PCB.
-
Inspection and Testing: The assembLED PCB undergoes visual inspection and electrical testing to ensure proper functionality and adherence to quality standards.
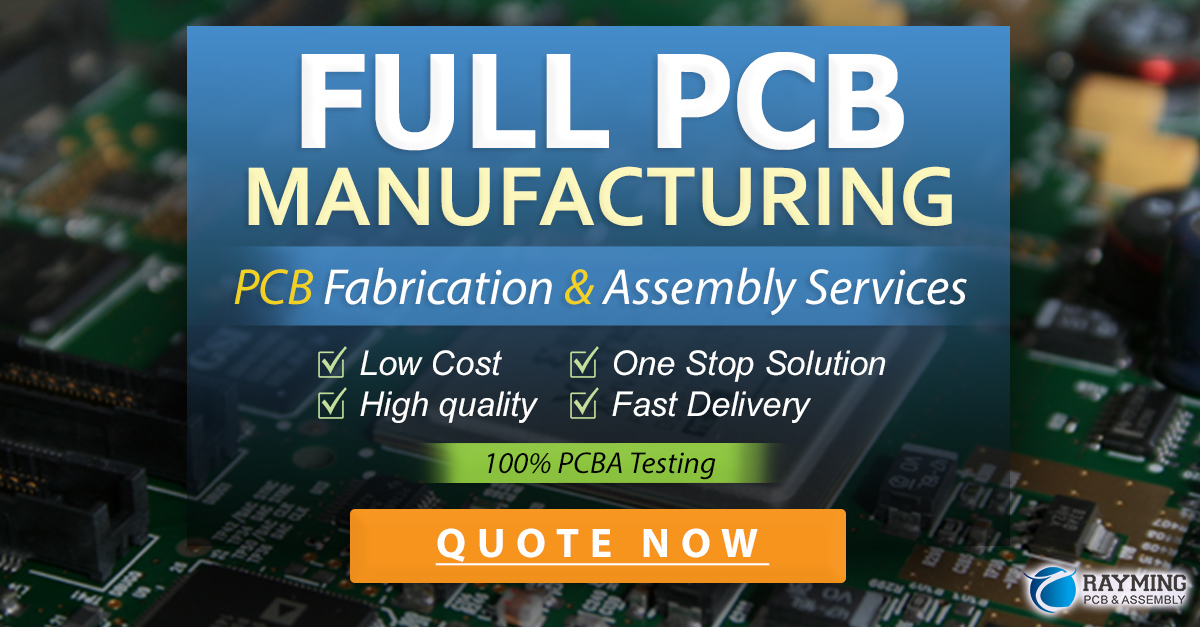
Tips for a Successful PCB Assembly
To ensure the success of your PCB assembly project, consider the following tips:
-
Choose the Right PCB Assembly Service: Select a PCB assembly service that has experience with your specific requirements and can meet your quality, timeline, and budget expectations.
-
Design for Manufacturability (DFM): Ensure your PCB design follows DFM guidelines to minimize assembly issues and improve yields. This includes considering component placement, routing, and clearances.
-
Use High-Quality Components: Source components from reputable suppliers to ensure reliability and performance. Counterfeit or subpar components can lead to assembly failures and product malfunctions.
-
Provide Clear and Complete Documentation: Supply your PCB assembly partner with comprehensive documentation, including bill of materials (BOM), assembly drawings, and any special instructions to avoid confusion and delays.
-
Plan for Testing and Quality Control: Incorporate testing and quality control measures into your project plan to catch and address any issues early in the assembly process.
Frequently Asked Questions (FAQ)
1. What is the difference between SMT and THA?
SMT (Surface Mount Technology) involves placing components directly onto the surface of the PCB, while THA (Through-Hole Assembly) requires inserting component leads through holes in the PCB and soldering them on the opposite side. SMT is faster, more precise, and allows for higher component density, while THA offers better mechanical stability and is suitable for larger components.
2. How do I choose the right PCB assembly service for my project?
When choosing a PCB assembly service, consider factors such as their experience with your specific requirements, quality standards, production capabilities, turnaround time, and cost. Look for a partner that can provide the level of support and expertise your project demands.
3. What is Design for Manufacturability (DFM), and why is it important?
Design for Manufacturability (DFM) is the practice of designing PCBs in a way that optimizes the manufacturing process. By following DFM guidelines, you can minimize assembly issues, improve yields, and reduce costs. DFM considerations include component placement, routing, clearances, and testability.
4. How can I ensure the quality of my PCB assembly?
To ensure the quality of your PCB assembly, use high-quality components from reputable suppliers, provide clear and complete documentation to your assembly partner, and incorporate testing and quality control measures into your project plan. Working with an experienced PCB assembly service that adheres to strict quality standards can also help guarantee the best results.
5. What are the benefits of using mixed technology assembly (MTA)?
Mixed technology assembly (MTA) combines SMT and THA techniques on a single PCB, allowing for more complex and versatile designs. MTA enables the use of through-hole components for mechanical stability or high-power applications alongside the benefits of SMT, such as higher component density and faster assembly. This approach provides the best of both worlds for projects that require a mix of component types and assembly methods.
Conclusion
PCB assembly is a critical process in the production of electronic devices, and choosing the right assembly service and techniques can make a significant difference in the success of your project. By understanding the different types of PCB assembly services available and following best practices for design and manufacturing, you can ensure that your PCB assembly meets your performance, reliability, and cost requirements.
Remember to select an experienced PCB assembly partner, design for manufacturability, use high-quality components, provide comprehensive documentation, and plan for testing and quality control. By keeping these factors in mind, you can navigate the PCB assembly process with confidence and achieve the best possible results for your project.
Leave a Reply