What is PCB Lamination?
PCB lamination is a critical process in the manufacturing of printed circuit boards (PCBs). It involves bonding together multiple layers of PCB material using heat and pressure to create a solid, unified board. The lamination process helps ensure the structural integrity, insulation, and reliability of the final PCB product.
Key Components in PCB Lamination
The main components used in PCB lamination include:
-
Core layers: These are the rigid, pre-patterned layers of the PCB, typically made from fiberglass or other dielectric materials.
-
Prepreg layers: Prepreg (pre-impregnated) layers are thin sheets of fiberglass pre-saturated with a resin that partially cures when exposed to heat. These layers bond the core layers together during lamination.
-
Copper foil: Thin sheets of copper are placed on the outer layers of the PCB stack to create conductive surfaces for electrical connections.
The Importance of PCB Lamination
PCB lamination plays a crucial role in the overall performance and reliability of the final PCB product:
- It ensures proper bonding between layers, preventing delamination and other structural issues.
- Lamination helps maintain the desired electrical properties of the PCB by providing insulation between conductive layers.
- A well-laminated PCB is better equipped to withstand environmental stresses, such as heat, humidity, and vibration.
The PCB Lamination Process
The PCB lamination process typically involves the following steps:
Step 1: Preparing the PCB Layers
Before lamination, the individual PCB layers are prepared:
- Core layers are patterned and etched according to the PCB Design.
- Prepreg layers are cut to size and aligned with the core layers.
- Copper foil is applied to the outer layers of the PCB stack.
Step 2: Stacking the Layers
The prepared layers are stacked in a specific order, alternating between core layers and prepreg layers. This stack is then placed between two sheets of steel or aluminum, called press plates or caul plates, to ensure even pressure distribution during lamination.
Step 3: Lamination Press
The PCB stack is placed in a lamination press, which applies heat and pressure to bond the layers together.
Parameter | Typical Value Range |
---|---|
Temperature | 180°C – 200°C |
Pressure | 250 psi – 400 psi |
Duration | 1 – 2 hours |
The specific lamination parameters may vary depending on the materials used and the PCB Manufacturer’s process.
Step 4: Cooling and Inspection
After lamination, the PCB is allowed to cool gradually to room temperature. This helps prevent warping or other deformations due to rapid temperature changes.
Once cooled, the laminated PCB undergoes visual inspection to check for any defects, such as blistering, delamination, or uneven copper distribution.
Factors Affecting PCB Lamination Quality
Several factors can impact the quality of PCB lamination:
Material Selection
Choosing the right materials is essential for successful lamination. Factors to consider include:
- The glass transition temperature (Tg) of the prepreg and core materials
- The coefficient of thermal expansion (CTE) of the materials
- The dielectric constant and loss tangent of the materials
Lamination Parameters
Proper control of lamination parameters is crucial for achieving a well-bonded PCB:
- Temperature: Insufficient temperature may result in poor bonding, while excessive temperature can cause material degradation or excessive resin flow.
- Pressure: Inadequate pressure may lead to voids or delamination, while excessive pressure can cause material deformation or damage.
- Duration: Insufficient lamination time may result in incomplete bonding, while excessive time can cause material degradation or unnecessary energy consumption.
Layup and Registration
Accurate alignment and registration of the PCB layers during the layup process are essential to ensure proper electrical connections and avoid short circuits or open connections.
Cleanliness and Contamination Control
Maintaining a clean environment during PCB lamination is crucial to prevent contamination that can lead to defects or reliability issues. This includes:
- Proper handling and storage of materials
- Cleaning of tools and equipment
- Controlling airborne particles and moisture levels
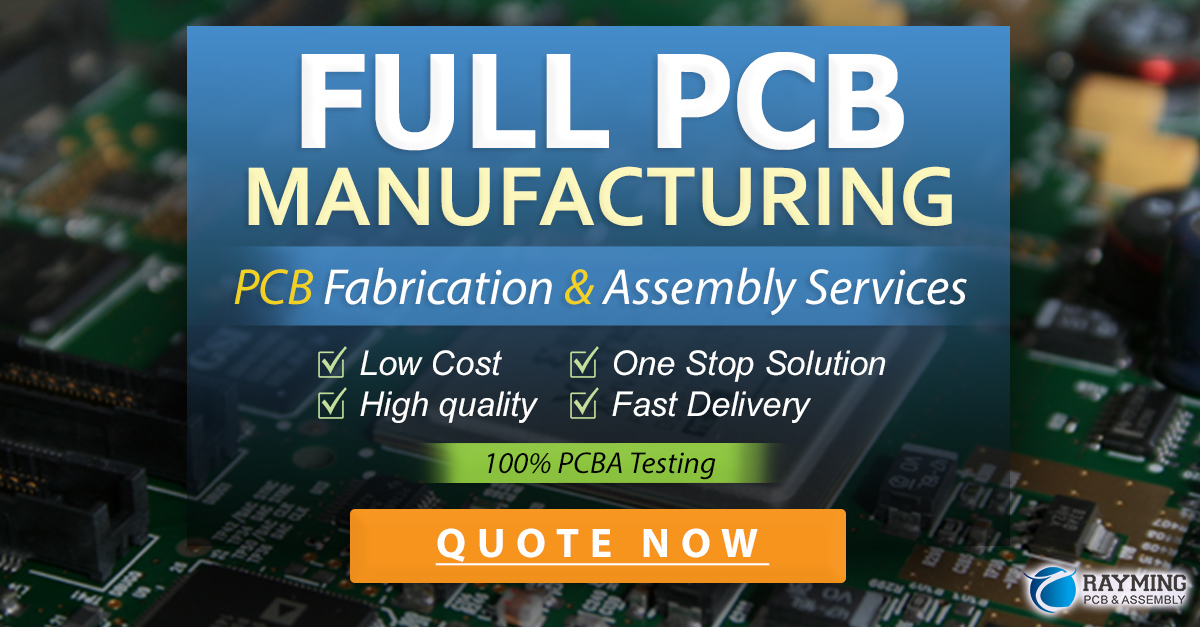
Advanced PCB Lamination Techniques
As PCB designs become more complex and demanding, advanced lamination techniques have been developed to address specific challenges:
Sequential Lamination
Sequential lamination involves laminating multiple sub-assemblies of PCB layers separately, then laminating these sub-assemblies together to form the final PCB. This technique is useful for PCBs with a large number of layers or varying layer thicknesses.
Vacuum Lamination
Vacuum lamination uses a vacuum chamber to remove air from the PCB stack before and during lamination. This helps reduce the risk of voids and improves the overall bonding quality.
Thermally Conductive Lamination
For PCBs with high heat dissipation requirements, thermally conductive materials can be incorporated into the lamination process. These materials, such as metal-clad laminates or thermally conductive prepregs, help transfer heat away from critical components.
Frequently Asked Questions (FAQ)
1. What is the difference between prepreg and core materials in PCB lamination?
Core materials are the rigid, pre-patterned layers of the PCB, while prepreg layers are thin sheets of fiberglass pre-saturated with a partially cured resin. Prepreg layers are used to bond the core layers together during lamination.
2. Can PCBs be re-laminated if there are defects or issues after the initial lamination?
In most cases, PCBs cannot be re-laminated once the initial lamination process is complete. Attempting to re-laminate a PCB can cause further damage or delamination. If defects are detected after lamination, the PCB may need to be scrapped or reworked, depending on the severity of the issue.
3. How does the choice of lamination materials affect the performance of the final PCB?
The choice of lamination materials can significantly impact the electrical, thermal, and mechanical properties of the final PCB. Factors such as the dielectric constant, glass transition temperature, and coefficient of thermal expansion of the materials should be carefully considered based on the specific requirements of the PCB application.
4. What is the role of the copper foil in PCB lamination?
Copper foil is used to create the conductive layers on the outer surfaces of the PCB. During lamination, the copper foil is bonded to the outermost prepreg layers, allowing for electrical connections to be made to the PCB’s internal layers through vias and other interconnects.
5. How can I ensure consistent and reliable PCB lamination results?
To ensure consistent and reliable PCB lamination results, consider the following:
- Choose materials with properties suitable for your specific application
- Maintain strict control over lamination parameters, such as temperature, pressure, and duration
- Ensure proper layup and registration of PCB layers
- Implement contamination control measures to maintain a clean lamination environment
- Monitor and inspect the lamination process and final PCB for any defects or anomalies
By understanding the PCB lamination process, selecting appropriate materials, and adhering to best practices, you can achieve high-quality, reliable PCBs for your electronic products. RAYPCB, a seasoned PCB manufacturer, can assist you in navigating the complexities of PCB lamination and ensuring the success of your PCB projects.
Leave a Reply