What is IMS PCB?
IMS PCB, or Insulated Metal Substrate Printed Circuit Board, is a type of circuit board that combines a metal substrate with a dielectric layer and a copper circuit layer. The metal substrate, usually aluminum or copper, provides excellent thermal conductivity, while the dielectric layer electrically insulates the copper circuit from the metal substrate. This unique construction enables IMS PCBs to efficiently dissipate heat generated by electronic components, making them ideal for applications that require high power density and thermal management.
Advantages of IMS PCB
- Enhanced thermal management
- Improved electrical performance
- Increased reliability
- Reduced size and weight
- Cost-effective solution
Structure of IMS PCB
An IMS PCB consists of three main layers:
- Metal substrate (base layer)
- Dielectric layer (insulation layer)
- Copper foil (circuit layer)
Metal Substrate
The metal substrate serves as the base layer and provides mechanical support for the IMS PCB. The most common materials used for the metal substrate are aluminum and copper due to their excellent thermal conductivity properties.
Material | Thermal Conductivity (W/mK) |
---|---|
Aluminum | 205 |
Copper | 400 |
Dielectric Layer
The dielectric layer is an insulating material that electrically isolates the copper circuit layer from the metal substrate. This layer is typically made of a thermally conductive but electrically insulating material, such as:
- Epoxy resin
- Polyimide
- Ceramic-filled polymer
The dielectric layer’s thickness and thermal conductivity play a crucial role in determining the IMS PCB’s overall thermal performance.
Copper Foil
The copper foil layer is where the electronic circuit is etched. The thickness of the copper foil can vary depending on the application’s requirements, with common thicknesses ranging from 17.5 µm to 400 µm (0.5 oz to 12 oz).
Manufacturing Process of IMS PCB
The manufacturing process of IMS PCBs involves several steps:
- Substrate preparation
- Dielectric layer application
- Copper foil lamination
- Circuit pattern etching
- Surface finish application
- Singulation and packaging
Substrate Preparation
The metal substrate is cleaned and treated to ensure proper adhesion of the dielectric layer. This step may involve degreasing, brushing, or chemical etching to roughen the surface and improve bonding strength.
Dielectric Layer Application
The dielectric layer is applied to the prepared metal substrate using various methods, such as:
- Screen printing
- Roller coating
- Curtain coating
- Lamination
The choice of application method depends on the dielectric material, the desired thickness, and the production volume.
Copper Foil Lamination
The copper foil is laminated onto the dielectric layer using heat and pressure. The lamination process ensures a strong bond between the copper foil and the dielectric layer, minimizing the risk of delamination during subsequent processing steps.
Circuit Pattern Etching
The desired circuit pattern is transferred onto the copper foil using photolithography and etching techniques. This process involves:
- Applying a photoresist layer
- Exposing the photoresist to UV light through a photomask
- Developing the photoresist to reveal the circuit pattern
- Etching away the unwanted copper using chemical etchants
- Stripping the remaining photoresist
Surface Finish Application
A surface finish is applied to the exposed copper traces to protect them from oxidation and enhance solderability. Common surface finishes include:
- Hot Air Solder Leveling (HASL)
- Electroless Nickel Immersion Gold (ENIG)
- Immersion Tin
- Organic Solderability Preservative (OSP)
Singulation and Packaging
The IMS PCB panel is cut into individual boards using methods such as routing, scoring, or punching. The finished boards are then packaged and shipped to the customer.
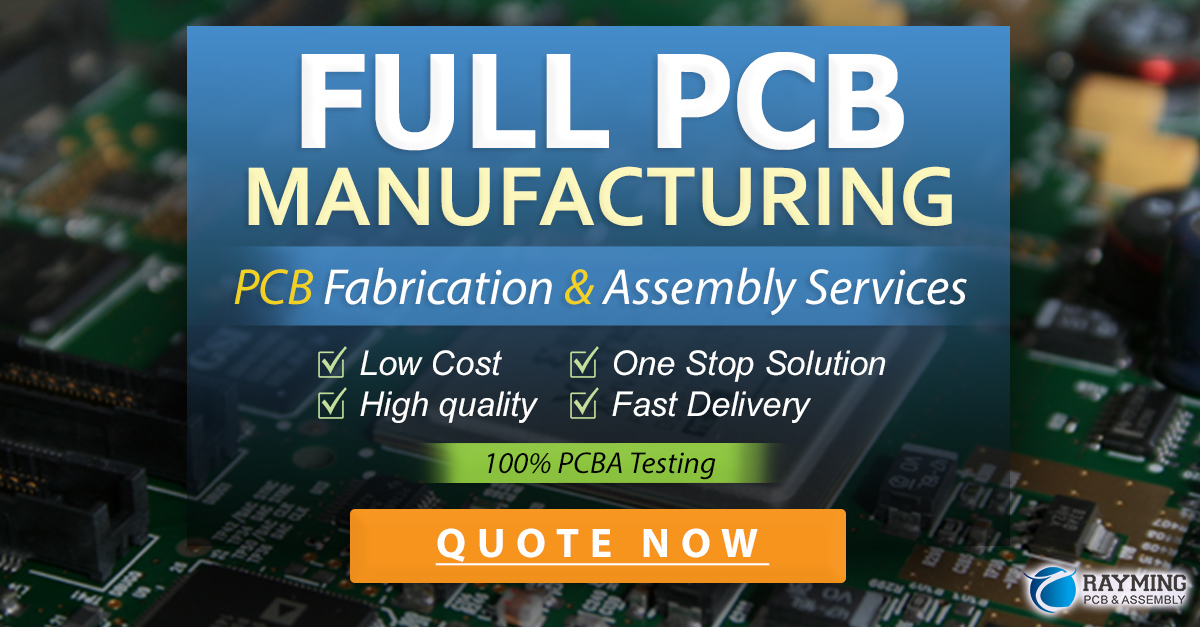
Applications of IMS PCB
IMS PCBs are widely used in applications that require efficient heat dissipation and high power density, such as:
- LED lighting
- Automotive electronics
- Power converters
- Motor drives
- Telecommunications equipment
LED Lighting
IMS PCBs are particularly well-suited for LED lighting applications due to their ability to dissipate heat efficiently. LEDs generate a significant amount of heat, which can negatively impact their performance and lifetime. By using IMS PCBs, LED manufacturers can:
- Improve LED efficiency
- Extend LED lifetime
- Reduce the size of LED fixtures
- Simplify thermal management designs
Automotive Electronics
The automotive industry has increasingly adopted IMS PCBs for various electronic components, such as:
- Engine control units (ECUs)
- Power steering modules
- Headlight control modules
- Battery management systems
IMS PCBs help automotive electronics withstand harsh operating conditions, including high temperatures, vibrations, and mechanical shocks.
Power Converters
Power converters, such as DC-DC converters and AC-DC power supplies, can benefit from the use of IMS PCBs. The enhanced thermal management provided by IMS PCBs enables power converters to:
- Operate at higher power densities
- Achieve better efficiency
- Reduce the need for external heat sinks
- Minimize the overall system size and weight
Motor Drives
IMS PCBs are used in motor drive applications to manage the heat generated by power electronic components, such as IGBTs and MOSFETs. By efficiently dissipating heat, IMS PCBs help motor drives:
- Operate reliably in high-temperature environments
- Reduce the risk of component failure due to thermal stress
- Achieve more compact designs
- Lower system costs by eliminating the need for additional cooling solutions
Telecommunications Equipment
Telecommunications equipment, such as base stations and routers, can also benefit from the use of IMS PCBs. The high power density and thermal management requirements of these applications make IMS PCBs an ideal choice for:
- Power amplifier modules
- Optical transceiver modules
- Backplane PCBs
- High-speed data processing units
Design Considerations for IMS PCB
When designing an IMS PCB, several factors must be considered to ensure optimal performance and reliability:
- Thermal management
- Dielectric material selection
- Copper thickness and trace width
- Via design and placement
- Solder mask and surface finish selection
Thermal Management
Effective thermal management is crucial for IMS PCBs. Designers should consider the following aspects:
- Thermal conductivity of the metal substrate and dielectric layer
- Thickness of the dielectric layer
- Placement of high-power components
- Use of thermal vias to enhance heat transfer
- Incorporation of additional cooling solutions, such as heat sinks or fans, if necessary
Dielectric Material Selection
The choice of dielectric material depends on the application’s requirements, including:
- Operating temperature range
- Dielectric strength
- Thermal conductivity
- Mechanical properties
- Cost
Some common dielectric materials used in IMS PCBs are:
Material | Thermal Conductivity (W/mK) | Dielectric Strength (kV/mm) |
---|---|---|
Epoxy resin | 0.2 – 0.5 | 20 – 50 |
Polyimide | 0.1 – 0.3 | 100 – 200 |
Ceramic-filled polymer | 1.0 – 10.0 | 10 – 30 |
Copper Thickness and Trace Width
The copper thickness and trace width should be optimized based on the current carrying capacity and thermal requirements of the circuit. Thicker copper and wider traces can help improve heat dissipation and reduce electrical resistance. However, this must be balanced with the need for circuit miniaturization and cost considerations.
Via Design and Placement
Vias play a crucial role in IMS PCBs, as they provide electrical interconnections and facilitate heat transfer between layers. Designers should consider the following aspects:
- Via size and placement
- Thermal via density and distribution
- Via Filling materials, such as copper or solder
- Use of microvias for high-density designs
Solder Mask and Surface Finish Selection
The choice of solder mask and surface finish can impact the IMS PCB’s manufacturability, solderability, and reliability. Factors to consider include:
- Compatibility with the dielectric material
- Thermal resistance
- Adhesion strength
- Durability in harsh environments
- Ease of application and processing
Frequently Asked Questions (FAQ)
-
Q: What is the main difference between IMS PCB and traditional FR-4 PCB?
A: The main difference is that IMS PCB uses a metal substrate, usually aluminum or copper, as the base layer, while traditional FR-4 PCB uses a glass-reinforced epoxy laminate. This allows IMS PCB to have better thermal conductivity and heat dissipation capabilities compared to FR-4 PCB. -
Q: Can IMS PCB be used for high-frequency applications?
A: Yes, IMS PCB can be used for high-frequency applications. However, the choice of dielectric material and the design of the copper traces must be carefully considered to minimize signal loss and maintain signal integrity. -
Q: How does the thickness of the dielectric layer affect the thermal performance of IMS PCB?
A: A thinner dielectric layer generally improves the thermal performance of IMS PCB, as it reduces the thermal resistance between the copper layer and the metal substrate. However, a thinner dielectric layer may also increase the risk of dielectric breakdown and reduce the electrical insulation between the layers. -
Q: Can IMS PCB be used in flexible circuit applications?
A: While IMS PCB is primarily used for rigid circuit applications, it is possible to use flexible dielectric materials, such as polyimide, to create flexible IMS PCB. However, the metal substrate may limit the overall flexibility of the circuit compared to traditional flexible PCB Materials. -
Q: Are there any environmental concerns associated with the manufacturing and disposal of IMS PCB?
A: Like any electronic product, the manufacturing and disposal of IMS PCB can have environmental impacts. However, many manufacturers are adopting eco-friendly practices, such as using Lead-Free Solders and recyclable materials, to minimize these impacts. Proper disposal and recycling of IMS PCB at the end of its life cycle can also help reduce environmental concerns.
Conclusion
IMS PCB is a specialized type of printed circuit board that offers superior thermal management and high power density capabilities compared to traditional PCB materials. By combining a metal substrate with a dielectric layer and a copper circuit layer, IMS PCB can efficiently dissipate heat generated by electronic components, enabling the development of more compact, reliable, and cost-effective electronic systems.
As the demand for high-performance electronics continues to grow across various industries, including LED lighting, automotive, power conversion, motor drives, and telecommunications, the adoption of IMS PCB is expected to increase. However, designing and manufacturing IMS PCB requires careful consideration of thermal, electrical, and mechanical factors to ensure optimal performance and reliability.
By understanding the structure, manufacturing process, applications, and design considerations of IMS PCB, engineers and manufacturers can leverage this technology to create innovative and efficient electronic solutions that meet the ever-increasing demands of modern industries.
Leave a Reply