What is an IMS PCB?
An Insulated Metal Substrate (IMS) PCB, also known as a metal core PCB, is a special type of printed circuit board that offers superior thermal performance compared to standard FR-4 PCBs. The key feature of an IMS PCB is its metal substrate, typically made of aluminum, which acts as a heat sink to efficiently dissipate heat away from the electronic components.
IMS PCBs consist of three main layers:
- A top layer of copper foil for the circuit pattern
- A thin layer of dielectric insulating material
- A metal substrate, usually aluminum, as the base
The dielectric layer is thermally conductive but electrically insulating, allowing heat to pass through to the metal substrate while preventing short circuits.
Why Use an IMS PCB?
The primary reason to use an IMS PCB is its excellent thermal management properties. In applications where high power density or heat-generating components are used, such as power electronics, LEDs, and automotive systems, efficient heat dissipation is crucial for maintaining performance and reliability.
Compared to standard PCBs, IMS PCBs offer several advantages:
- Higher thermal conductivity, allowing for better heat dissipation
- Improved reliability and longer lifespan of electronic components
- Reduced need for additional heat sinks or cooling mechanisms
- Smaller form factor and lighter weight
- Lower thermal resistance between components and the PCB
Applications of IMS PCBs
IMS PCBs are used in a wide range of industries and applications where thermal management is critical. Some common applications include:
- Power electronics
- Switch mode power supplies (SMPS)
- Motor drives
- Inverters
- Automotive electronics
- Engine control units (ECUs)
- LED lighting
- Electric vehicle battery management systems
- LED lighting
- High-power LED fixtures
- Street lighting
- Automotive headlights
- Telecommunications
- Power amplifiers
- Base station equipment
- Aerospace and defense
- Radar systems
- Satellite communications
- Avionics
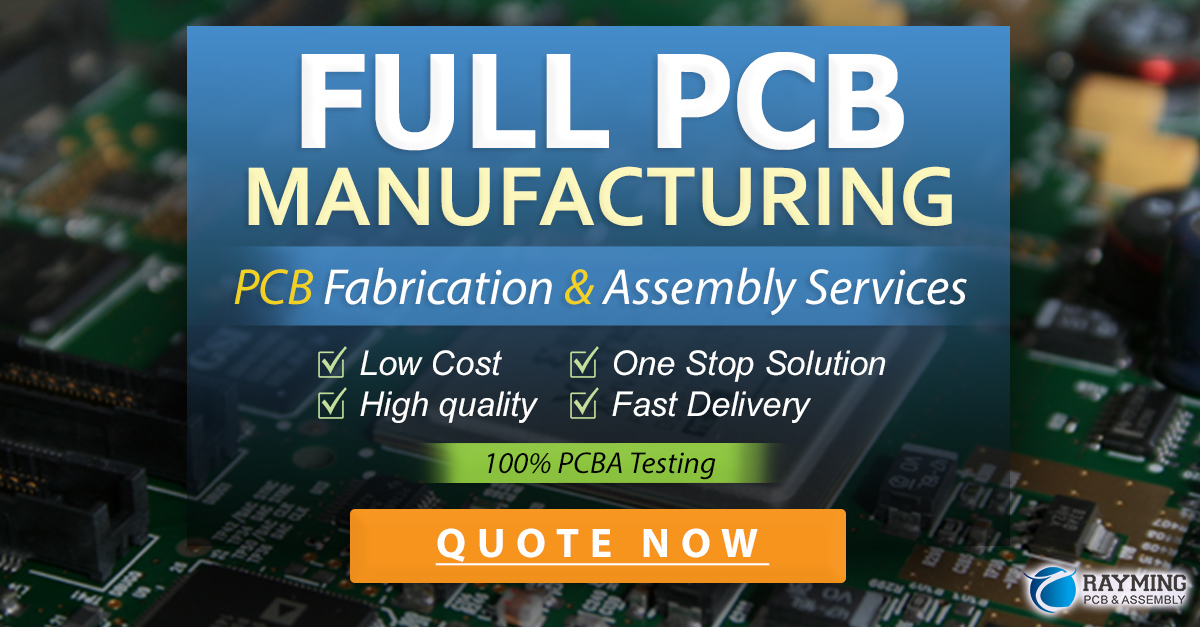
IMS PCB Materials
The choice of materials for an IMS PCB is crucial for its performance and reliability. The three main components of an IMS PCB – the copper foil, dielectric layer, and metal substrate – must be carefully selected based on the application requirements.
Copper Foil
The copper foil used in IMS PCBs is typically available in thicknesses ranging from 0.5 oz to 10 oz per square foot. The thickness of the copper foil affects the current-carrying capacity and the thermal conductivity of the PCB. Thicker copper foil allows for higher current carrying capacity and better heat spreading, but it also increases the overall thickness and weight of the PCB.
Dielectric Layer
The dielectric layer in an IMS PCB is a thin, thermally conductive but electrically insulating material that separates the copper foil from the metal substrate. The most common dielectric materials used in IMS PCBs are:
- Epoxy-based dielectrics
- Offer good thermal conductivity and electrical insulation
- Suitable for most general-purpose applications
- Ceramic-filled dielectrics
- Provide higher thermal conductivity than epoxy-based dielectrics
- Ideal for high-power applications
- Polyimide-based dielectrics
- Offer excellent thermal stability and chemical resistance
- Suitable for high-temperature applications
The table below compares the thermal conductivity of common IMS PCB dielectric materials:
Dielectric Material | Thermal Conductivity (W/mK) |
---|---|
Epoxy-based | 1-5 |
Ceramic-filled | 2-10 |
Polyimide-based | 0.5-1 |
Metal Substrate
The metal substrate in an IMS PCB acts as a heat sink, efficiently spreading and dissipating heat away from the electronic components. The most common metal substrate material is aluminum, chosen for its excellent thermal conductivity, lightweight, and low cost. Other metal substrates, such as copper or copper-molybdenum alloy, may be used in specialized applications requiring even higher thermal performance.
Aluminum substrates are available in various thicknesses, typically ranging from 0.5mm to 3mm. The choice of substrate thickness depends on the specific application requirements, such as the amount of heat generated, the size and weight constraints, and the mechanical strength needed.
Thermal Management with IMS PCBs
The primary function of an IMS PCB is to effectively manage heat generated by electronic components. The metal substrate acts as a heat spreader, quickly conducting heat away from the components and evenly distributing it across the PCB. This helps to maintain a lower and more uniform temperature across the board, reducing thermal stress on the components and improving overall system reliability.
To quantify the thermal performance of an IMS PCB, several key parameters are used:
-
Thermal conductivity (k): The ability of a material to conduct heat, measured in watts per meter-kelvin (W/mK). Higher thermal conductivity means better heat conduction.
-
Thermal resistance (Rth): The measure of a material’s resistance to heat flow, expressed in degrees Celsius per watt (°C/W). Lower thermal resistance indicates better heat dissipation.
-
Junction-to-ambient thermal resistance (Rja): The total thermal resistance from the junction of a component to the ambient environment, considering the heat flow through the PCB, any additional heat sinks, and the surrounding air.
The table below compares the thermal conductivity of common PCB materials:
Material | Thermal Conductivity (W/mK) |
---|---|
FR-4 (standard PCB) | 0.25-0.3 |
Aluminum (IMS PCB) | 150-200 |
Copper (IMS PCB) | 380-400 |
Ceramic-filled dielectric | 2-10 |
To calculate the junction-to-ambient thermal resistance (Rja) for a component on an IMS PCB, the following formula can be used:
Rja = Rjc + Rcs + Rsa
Where:
– Rjc is the junction-to-case thermal resistance of the component
– Rcs is the case-to-sink thermal resistance, which includes the thermal resistance of the dielectric layer and the metal substrate
– Rsa is the sink-to-ambient thermal resistance, which accounts for any additional heat sinks and the ambient environment
By minimizing the thermal resistance at each stage, IMS PCBs can effectively dissipate heat and maintain lower component temperatures, leading to improved system performance and reliability.
Designing with IMS PCBs
When designing an IMS PCB, several factors must be considered to ensure optimal thermal performance and reliability:
-
Component placement: High heat-generating components should be placed on the metal substrate for maximum heat dissipation. Adequate spacing between components helps to avoid hot spots and ensures even heat distribution.
-
Copper thickness: Thicker copper foil improves current carrying capacity and heat spreading, but it also increases the PCB’s overall thickness and weight. The copper thickness should be selected based on the specific application requirements.
-
Dielectric layer: The choice of dielectric material and its thickness affects the thermal conductivity and electrical insulation of the IMS PCB. Thinner dielectric layers offer lower thermal resistance but may compromise electrical insulation.
-
Via placement: Thermal vias can be used to further improve heat transfer from the components to the metal substrate. These vias should be placed close to the heat-generating components and evenly distributed across the PCB.
-
Solder mask: A solder mask can be applied to the copper foil to protect the circuitry and prevent short circuits. However, the solder mask also acts as a thermal insulator, so it should be used sparingly and only where necessary.
-
Additional heat sinks: In some cases, additional heat sinks may be required to dissipate heat effectively. These heat sinks can be attached to the metal substrate using thermal adhesive or mechanical fasteners.
By carefully considering these design factors, engineers can create IMS PCBs that offer optimal thermal performance and reliability for their specific applications.
Manufacturing IMS PCBs
The manufacturing process for IMS PCBs is similar to that of standard PCBs, with a few key differences:
-
Substrate preparation: The metal substrate is cleaned and roughened to improve adhesion of the dielectric layer.
-
Dielectric layer application: The dielectric layer is applied to the metal substrate using techniques such as screen printing, roller coating, or lamination.
-
Copper foil lamination: The copper foil is laminated onto the dielectric layer using heat and pressure.
-
Circuit patterning: The copper foil is patterned using standard PCB manufacturing processes, such as photolithography and etching.
-
Solder mask application: If required, a solder mask is applied to the copper foil to protect the circuitry and prevent short circuits.
-
Surface finish: A surface finish, such as HASL (Hot Air Solder Leveling) or ENIG (Electroless Nickel Immersion Gold), is applied to the exposed copper to improve solderability and protect against oxidation.
-
Singulation: The IMS PCB panel is cut into individual boards using routing or punching techniques.
Quality control is critical throughout the manufacturing process to ensure that the IMS PCBs meet the required specifications for thermal performance, electrical insulation, and mechanical strength.
FAQ
1. What are the advantages of using an IMS PCB over a standard FR-4 PCB?
IMS PCBs offer superior thermal conductivity compared to standard FR-4 PCBs, allowing for better heat dissipation and improved reliability of electronic components. They also enable smaller form factors and lighter weight designs, as the metal substrate can replace additional heat sinks or cooling mechanisms.
2. Can IMS PCBs be used in high-voltage applications?
Yes, IMS PCBs can be used in high-voltage applications, provided that the appropriate dielectric material and thickness are selected to ensure adequate electrical insulation between the copper foil and the metal substrate.
3. What is the typical thermal conductivity of an aluminum IMS PCB substrate?
Aluminum IMS PCB substrates typically have a thermal conductivity ranging from 150 to 200 W/mK, which is significantly higher than the thermal conductivity of standard FR-4 PCB materials (0.25-0.3 W/mK).
4. How does the thickness of the dielectric layer affect the thermal performance of an IMS PCB?
A thinner dielectric layer offers lower thermal resistance, allowing for better heat transfer from the electronic components to the metal substrate. However, a thinner dielectric layer may compromise the electrical insulation properties of the IMS PCB, so a balance must be struck based on the specific application requirements.
5. Can IMS PCBs be soldered using standard SMT (Surface Mount Technology) processes?
Yes, IMS PCBs can be soldered using standard SMT processes, such as reflow soldering or wave soldering. The metal substrate provides an excellent heat sink during the soldering process, helping to prevent thermal damage to the components and ensuring reliable solder joints.
Conclusion
IMS PCBs offer a highly effective solution for thermal management in electronic systems, particularly in applications where high power density or heat-generating components are used. By combining a metal substrate with a thermally conductive dielectric layer and copper foil, IMS PCBs can efficiently dissipate heat away from electronic components, improving system performance and reliability.
When designing with IMS PCBs, careful consideration must be given to factors such as component placement, copper thickness, dielectric material, and via placement to ensure optimal thermal performance. By understanding the unique properties and manufacturing processes of IMS PCBs, engineers can create designs that maximize the benefits of this innovative technology.
As electronic systems continue to push the boundaries of power density and miniaturization, the demand for advanced thermal management solutions like IMS PCBs will only continue to grow. With their superior thermal conductivity, lightweight, and versatility, IMS PCBs are poised to play an increasingly crucial role in enabling the next generation of high-performance electronics across a wide range of industries and applications.
Leave a Reply