What is Alumina PCB?
Alumina PCB, also known as Aluminum Oxide (Al2O3) PCB, is a type of printed circuit board that utilizes alumina ceramic as its base material instead of the more commonly used FR-4 (Flame Retardant 4) glass-epoxy laminate. Alumina is a high-performance ceramic material that offers several advantages over traditional PCB materials, making it an ideal choice for certain applications that require enhanced thermal management, high-frequency performance, and improved mechanical stability.
Composition and Properties of Alumina
Alumina is a compound composed of aluminum and oxygen atoms, with the chemical formula Al2O3. It is a highly stable and durable ceramic material that possesses the following properties:
- High Thermal Conductivity
- Excellent electrical insulation
- Low dielectric constant and loss tangent
- High mechanical strength and hardness
- Good resistance to chemical and environmental factors
These properties make alumina an attractive material for use in PCBs, especially in applications where traditional PCB materials may not suffice.
Advantages of Alumina PCB
1. Enhanced Thermal Management
One of the primary advantages of alumina PCB is its superior thermal management capabilities. Alumina has a high thermal conductivity, which means it can efficiently dissipate heat generated by electronic components on the PCB. This is particularly important in high-power applications or when dealing with components that generate significant amounts of heat, such as power amplifiers, LEDs, or high-performance processors.
The thermal conductivity of alumina is approximately 20-30 W/mK, which is significantly higher than that of FR-4 (0.3-0.4 W/mK). This allows for better heat dissipation and helps maintain a more stable operating temperature for the electronic components, leading to improved reliability and longer product lifespans.
2. High-Frequency Performance
Alumina PCB excels in high-frequency applications due to its low dielectric constant and loss tangent. The dielectric constant of alumina is around 9.8, which is lower than that of FR-4 (typically 4.5). A lower dielectric constant means that the material has a lower capacitance, which is beneficial for high-frequency signal transmission as it reduces signal distortion and attenuation.
Moreover, alumina has a low loss tangent, which indicates its ability to minimize signal loss at high frequencies. The loss tangent of alumina is approximately 0.0001, which is significantly lower than that of FR-4 (0.02). This makes alumina PCB an excellent choice for applications involving high-frequency signals, such as RF and microwave circuits, radar systems, and wireless communication devices.
3. Mechanical Stability and Durability
Alumina PCB offers superior mechanical stability and durability compared to traditional PCB materials. Alumina has a high mechanical strength and hardness, making it resistant to bending, warping, and cracking under stress. This is particularly important in applications where the PCB is subject to harsh environmental conditions, such as extreme temperatures, vibrations, or mechanical shocks.
The coefficient of thermal expansion (CTE) of alumina is also lower than that of FR-4, which means it experiences less dimensional change with temperature variations. This stability is crucial for maintaining the integrity of the PCB and preventing issues such as solder joint failures or component misalignment.
4. Chemical and Environmental Resistance
Alumina PCB exhibits excellent resistance to chemical and environmental factors. It is highly resistant to moisture, humidity, and various chemicals, making it suitable for use in harsh industrial environments or outdoor applications. Additionally, alumina has a high melting point (2072°C) and is non-flammable, providing an added layer of safety in high-temperature or fire-prone environments.
Applications of Alumina PCB
Alumina PCB finds applications in various industries and domains where its unique properties are advantageous. Some of the common applications include:
-
High-Power Electronics: Alumina PCB is widely used in high-power electronic systems, such as power amplifiers, motor drives, and power converters, where efficient heat dissipation is critical for reliable operation.
-
RF and Microwave Circuits: The low dielectric constant and loss tangent of alumina make it an ideal material for high-frequency applications, such as RF and microwave circuits used in wireless communication systems, radar, and satellite technology.
-
LED Lighting: Alumina PCB is used in LED lighting applications to provide better thermal management and improve the efficiency and longevity of LED devices.
-
Automotive Electronics: The mechanical stability and environmental resistance of alumina PCB make it suitable for use in automotive electronics, such as engine control units, sensor modules, and power management systems.
-
Aerospace and Defense: Alumina PCB is employed in aerospace and defense applications that require high reliability, thermal stability, and resistance to harsh environmental conditions, such as avionics, missile guidance systems, and satellite communications.
-
Medical Devices: The biocompatibility and stability of alumina PCB make it a suitable choice for medical devices, such as implantable electronics, medical imaging equipment, and diagnostic tools.
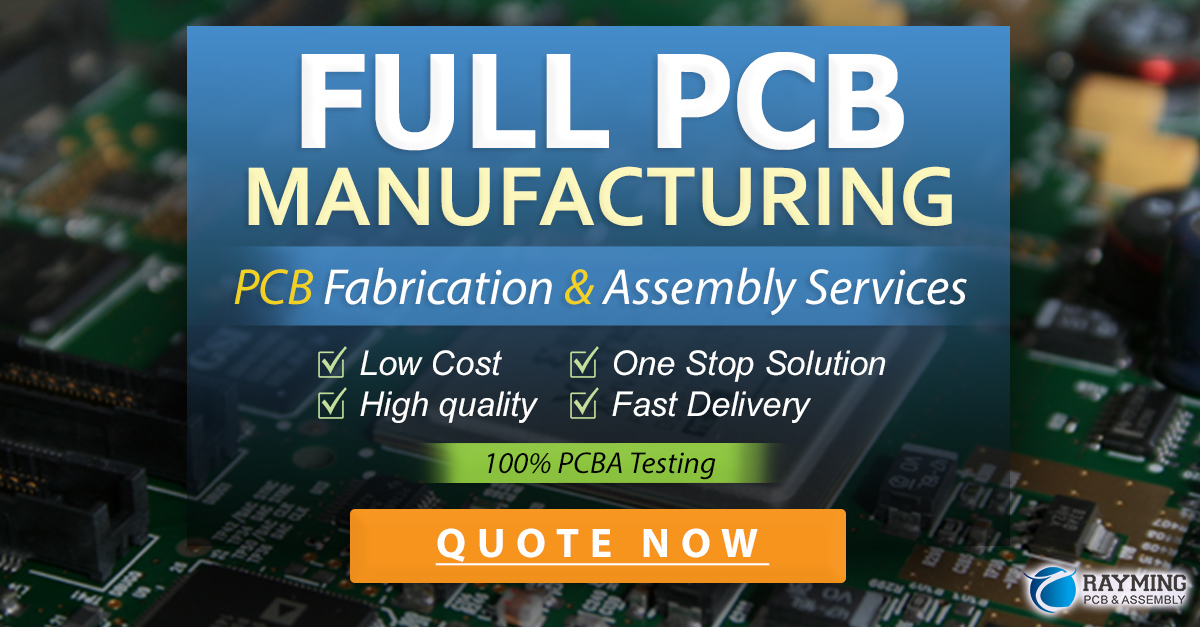
Manufacturing Process of Alumina PCB
The manufacturing process of alumina PCB differs from that of traditional PCBs due to the unique properties of the alumina substrate. The process typically involves the following steps:
-
Substrate Preparation: The alumina substrate is cut and polished to the desired size and thickness. Holes for vias and other features are drilled or laser-cut into the substrate.
-
Metallization: A thin layer of metal, usually copper or gold, is deposited onto the alumina substrate using techniques such as sputtering, electroplating, or thick-film printing. This layer acts as the conductive pattern for the PCB.
-
Patterning: The desired circuit pattern is created on the metallized alumina substrate using photolithography or screen printing techniques. The unwanted metal areas are etched away, leaving the desired conductive pattern.
-
Insulation and Protection: A dielectric layer, such as a solder mask or conformal coating, is applied to the PCB to provide insulation and protection for the conductive pattern.
-
Component Assembly: Electronic components are attached to the alumina PCB using various techniques, such as surface mount technology (SMT) or wire bonding, depending on the application requirements.
-
Testing and Inspection: The assembled alumina PCB undergoes rigorous testing and inspection to ensure its functionality, reliability, and adherence to the specified performance criteria.
Challenges and Considerations
While alumina PCB offers numerous advantages, there are also some challenges and considerations to keep in mind when working with this material:
-
Cost: Alumina PCB is generally more expensive than traditional FR-4 PCB due to the higher cost of the alumina substrate and the specialized manufacturing processes involved.
-
Design Complexity: Designing circuits on alumina PCB may require additional considerations due to the material’s unique properties. Factors such as thermal management, Impedance Matching, and signal integrity need to be carefully addressed.
-
Manufacturing Expertise: The manufacturing process of alumina PCB requires specialized equipment and expertise, which may not be readily available at all PCB fabrication facilities.
-
Component Compatibility: Not all electronic components are compatible with alumina PCB due to the differences in thermal expansion and other material properties. Careful component selection and qualification are necessary to ensure reliability.
Despite these challenges, the benefits of alumina PCB often outweigh the drawbacks in applications where high performance, reliability, and durability are paramount.
Frequently Asked Questions (FAQ)
-
Q: What is the main difference between alumina PCB and traditional FR-4 PCB?
A: The main difference lies in the base material used. Alumina PCB uses alumina ceramic as its substrate, while FR-4 PCB uses a glass-epoxy composite. Alumina offers superior thermal management, high-frequency performance, and mechanical stability compared to FR-4. -
Q: Can alumina PCB be used for low-frequency applications?
A: While alumina PCB excels in high-frequency applications, it can also be used for low-frequency applications. However, the cost and design complexity may not justify its use in such cases, and traditional PCB materials like FR-4 may be more suitable. -
Q: Is alumina PCB more expensive than FR-4 PCB?
A: Yes, alumina PCB is generally more expensive than FR-4 PCB due to the higher cost of the alumina substrate and the specialized manufacturing processes involved. -
Q: Can standard PCB manufacturing processes be used for alumina PCB?
A: The manufacturing process of alumina PCB differs from that of standard PCBs and requires specialized equipment and expertise. Some steps, such as substrate preparation and metallization, are specific to alumina PCB manufacturing. -
Q: What are some common applications of alumina PCB?
A: Alumina PCB is commonly used in high-power electronics, RF and microwave circuits, LED lighting, automotive electronics, aerospace and defense systems, and medical devices, among others. Its unique properties make it suitable for applications that require enhanced thermal management, high-frequency performance, and mechanical stability.
Conclusion
Alumina PCB is a high-performance alternative to traditional PCB materials, offering superior thermal management, high-frequency performance, mechanical stability, and environmental resistance. Its unique properties make it an ideal choice for applications in various industries, including high-power electronics, RF and microwave circuits, automotive electronics, aerospace and defense, and medical devices.
While alumina PCB comes with challenges such as higher cost and design complexity, its benefits often justify its use in applications where reliability, durability, and performance are critical. As technology advances and the demand for high-performance electronics grows, alumina PCB is expected to play an increasingly important role in enabling the development of cutting-edge products and systems.
By understanding the properties, advantages, and applications of alumina PCB, engineers and designers can make informed decisions when selecting materials for their projects and leverage the benefits of this advanced PCB technology to create innovative and reliable electronic solutions.
Leave a Reply