What is Organic Solderability Preservative (OSP)?
Organic Solderability Preservative (OSP) is a surface finish applied to printed circuit boards (PCBs) to maintain the solderability of exposed copper pads and prevent oxidation. OSP is a clear, organic coating that is an alternative to other surface finishes like Hot Air Solder Leveling (HASL), Electroless Nickel Immersion Gold (ENIG), and Immersion Silver.
Key Features of OSP:
- Thin, transparent organic coating
- Preserves solderability of copper pads
- Prevents oxidation and contamination
- RoHS compliant and environmentally friendly
- Cost-effective surface finish option
- Suitable for fine-pitch components and wire bonding
- Flat surface ideal for automated optical inspection (AOI)
How Does OSP Work?
OSP works by creating a protective layer over the exposed copper pads on a PCB. The organic compounds in OSP bond with the copper surface, sealing it off from the environment. This prevents oxidation and contamination that would degrade the solderability of the pads.
The OSP Application Process:
- PCB is cleaned to remove any dirt, grease, or oxides
- PCB is immersed in the OSP solution
- OSP selectively bonds to exposed copper surfaces
- Excess OSP is rinsed off the PCB
- PCB is dried, leaving a thin OSP layer on copper pads
The resulting OSP layer is typically 0.2-0.5 microns thick. This thin, uniform coating preserves solderability while still allowing for excellent electrical contact during assembly.
Advantages of Using OSP
OSP offers several advantages as a PCB Surface Finish:
-
Cost-Effective: OSP is one of the most economical surface finish options. It requires less processing than other finishes like ENIG or HASL.
-
Environmentally Friendly: OSP is RoHS compliant and does not contain any hazardous chemicals. The application process is also more environmentally friendly compared to other finishes.
-
Good Solderability: OSP provides excellent solderability for copper pads. The thin coating allows for good wetting of solder during assembly.
-
Fine-Pitch Capability: The thin, flat OSP layer is suitable for fine-pitch components and high-density PCB designs.
-
Wire Bonding: OSP is compatible with wire bonding processes used in some advanced packaging applications.
-
AOI Compatible: The transparent nature of OSP allows for easy automated optical inspection (AOI) of solder joints.
Comparison of OSP to Other Surface Finishes
Surface Finish | Thickness | Cost | Shelf Life | Fine-Pitch | Wire Bonding |
---|---|---|---|---|---|
OSP | 0.2-0.5µm | $ | 6-12 months | Yes | Yes |
HASL | 1-30µm | $ | 12+ months | Limited | No |
ENIG | 3-6µm | $$$ | 12+ months | Yes | Yes |
Immersion Ag | 0.1-0.3µm | $$ | 6-12 months | Yes | Limited |
$ = Low Cost, $$ = Medium Cost, $$$ = High Cost
As shown in the table, OSP provides a good balance of cost, performance, and compatibility with various PCB Assembly processes.
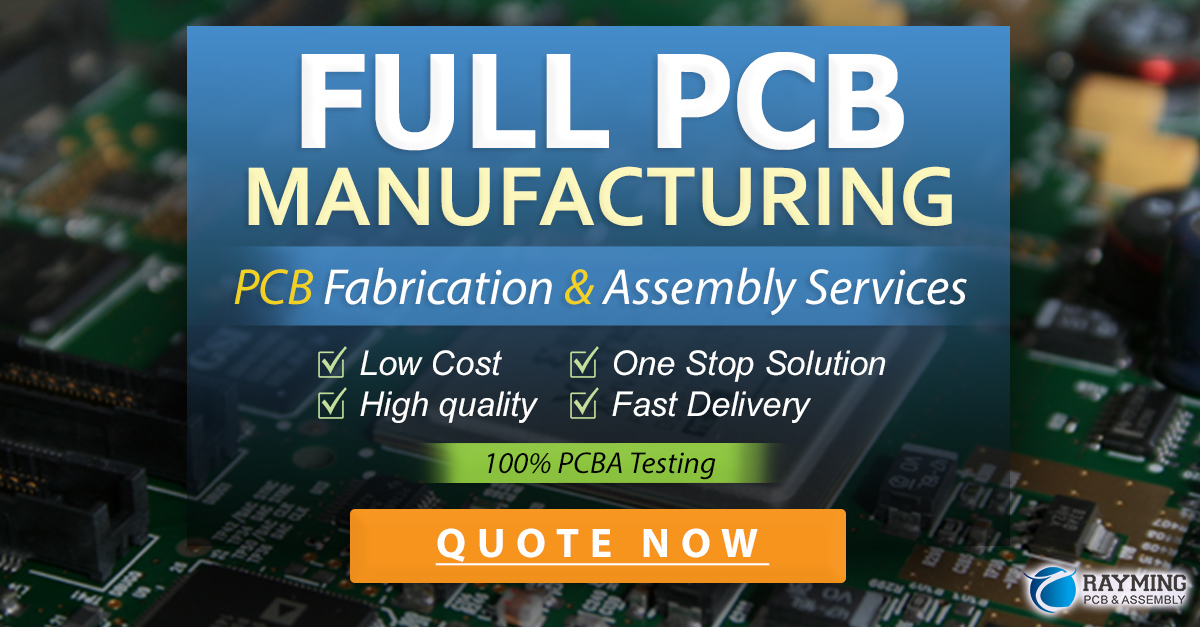
Limitations of OSP
While OSP has many advantages, there are some limitations to consider:
-
Limited Shelf Life: OSP has a shorter shelf life compared to other surface finishes. Most OSP coatings are rated for 6-12 months of storage before solderability may degrade.
-
Handling Sensitivity: OSP coated PCBs are more sensitive to handling and environmental conditions. Improper handling can lead to contamination or degradation of the OSP layer.
-
Multiple Thermal Cycles: OSP may not withstand multiple thermal cycles as well as other finishes. Repeated soldering or rework can degrade the OSP coating.
-
Cosmetic Appearance: OSP does not provide the same cosmetic enhancement as other finishes like ENIG or Immersion Silver. The copper pads will still have a matte appearance.
Tips for Working with OSP:
- Use ESD safe gloves when handling OSP coated PCBs
- Store OSP PCBs in sealed bags with desiccant
- Assemble OSP PCBs within the rated shelf life
- Minimize multiple thermal cycles or rework on OSP
- Consider other finishes for PCBs requiring long storage
By understanding these limitations and following proper handling guidelines, the benefits of OSP can be maximized while minimizing potential issues.
OSP and RAYPCB’s PCB Manufacturing
At RAYPCB, we offer OSP as a surface finish option for our PCB manufacturing services. Our state-of-the-art facilities and experienced team ensure high-quality OSP application on your PCBs.
RAYPCB’s OSP Process:
- PCBs are cleaned using a multi-stage cleaning line
- Proprietary OSP solution is applied by immersion
- Controlled rinse and dry cycles ensure optimal coating
- 100% automated optical inspection of OSP coverage
- Packaged in ESD safe, moisture-barrier bags
We have optimized our OSP process to provide consistent, reliable results. Our OSP coated PCBs have been used in a wide range of industries, including:
- Consumer electronics
- Automotive electronics
- Medical devices
- Industrial control systems
- IoT and wearable devices
PCB Design Guidelines for OSP:
When designing PCBs for OSP, consider the following guidelines:
- Minimize exposed copper areas to reduce OSP usage
- Use solder mask defined (SMD) pads for better OSP coverage
- Avoid overly tight pitch or spacing that may blur OSP edges
- Consider pad size and shape for optimal OSP application
- Follow RAYPCB’s design guidelines for manufacturability
By working closely with our customers and following these design principles, we can ensure the best possible results for OSP coated PCBs.
Frequently Asked Questions (FAQ)
1. What is the shelf life of OSP coated PCBs?
Most OSP formulations provide a shelf life of 6-12 months when stored properly. This is shorter than other finishes like ENIG or HASL, which can have a shelf life of 12+ months.
2. Can OSP be used for wire bonding applications?
Yes, OSP is compatible with wire bonding processes. The thin, flat OSP layer provides a suitable surface for wire bonding in advanced packaging applications.
3. Is OSP RoHS compliant?
Yes, OSP is RoHS compliant and does not contain any hazardous substances restricted by RoHS regulations. It is an environmentally friendly alternative to finishes that may contain lead or other harmful chemicals.
4. How does OSP compare to HASL in terms of cost?
OSP and HASL are both low-cost surface finish options. However, OSP may be slightly more expensive than HASL due to the additional processing steps and materials required.
5. Can OSP be reflowed multiple times?
OSP may degrade after multiple reflow cycles. It is best suited for PCBs that will undergo a single reflow cycle. If multiple thermal cycles are required, other surface finishes like ENIG may be more suitable.
Conclusion
Organic Solderability Preservative (OSP) is a clear, organic coating that preserves the solderability of exposed copper pads on PCBs. It offers several advantages, including cost-effectiveness, environmental friendliness, and compatibility with fine-pitch components and wire bonding.
However, OSP also has some limitations, such as a shorter shelf life and sensitivity to handling and multiple thermal cycles. By understanding these advantages and limitations, PCB designers and manufacturers can make informed decisions about when to use OSP.
At RAYPCB, we offer high-quality OSP application as part of our PCB manufacturing services. Our optimized process and experienced team ensure consistent, reliable results for our customers across various industries.
By working together and following design guidelines, we can help you maximize the benefits of OSP for your PCB projects. Contact RAYPCB today to learn more about our OSP and other surface finish options.
Leave a Reply