Introduction to MCPCB Manufacturing
Metal Core Printed Circuit Board (MCPCB) manufacturing is a specialized process that combines the advantages of traditional PCBs with the thermal management properties of metal substrates, particularly aluminum. MCPCBs are widely used in applications that require efficient heat dissipation, such as high-power LED lighting, automotive electronics, and power converters.
What is an MCPCB?
An MCPCB consists of a metal substrate, typically aluminum, with a thin layer of dielectric material and a copper circuit layer on top. The metal substrate acts as a heat sink, quickly dissipating heat generated by the components mounted on the PCB. This unique structure allows MCPCBs to handle higher power densities and operate at lower temperatures compared to traditional FR-4 PCBs.
Advantages of MCPCBs
- Excellent thermal management
- Improved reliability and longevity
- Higher power handling capability
- Reduced size and weight
- Enhanced mechanical stability
Types of MCPCBs
MCPCBs can be classified into two main categories based on their construction and flexibility:
Rigid MCPCBs
Rigid MCPCBs have a solid, inflexible structure and are the most common type of MCPCB. They offer excellent thermal performance and mechanical stability, making them suitable for a wide range of applications.
Flexible MCPCBs (Aluminum PCB Flex)
Flexible MCPCBs, also known as Aluminum PCB Flex, combine the thermal management properties of MCPCBs with the flexibility of traditional Flexible PCBs. This unique combination allows for more complex designs and improved connectivity in applications where flexibility is required, such as wearable electronics and aerospace systems.
MCPCB Manufacturing Process
The MCPCB manufacturing process involves several key steps to ensure the quality and reliability of the final product.
Step 1: Substrate Preparation
The aluminum substrate is cleaned and treated to improve adhesion with the dielectric layer. This step is crucial for ensuring the long-term reliability of the MCPCB.
Step 2: Dielectric Layer Application
A thin layer of dielectric material, typically a thermally conductive polymer, is applied to the aluminum substrate. This layer electrically isolates the metal substrate from the copper circuit layer while allowing efficient heat transfer.
Step 3: Copper Foil Lamination
A copper foil is laminated onto the dielectric layer using heat and pressure. The copper foil thickness can vary depending on the application requirements.
Step 4: Circuit Patterning
The desired circuit pattern is transferred onto the copper layer using photolithography and etching processes. This step creates the conductive traces and pads for component placement.
Step 5: Surface Finish Application
A surface finish, such as ENIG (Electroless Nickel Immersion Gold) or OSP (Organic Solderability Preservative), is applied to the exposed copper to improve solderability and protect against oxidation.
Step 6: Solder Mask Application
A solder mask is applied to the PCB surface to protect the copper traces and prevent short circuits during the soldering process. The solder mask also provides insulation and improves the PCB’s appearance.
Step 7: Cutting and Drilling
The MCPCB panel is cut into individual boards, and any required holes or slots are drilled or routed.
Step 8: Quality Control
Each MCPCB undergoes rigorous quality control tests to ensure it meets the specified electrical, thermal, and mechanical requirements.
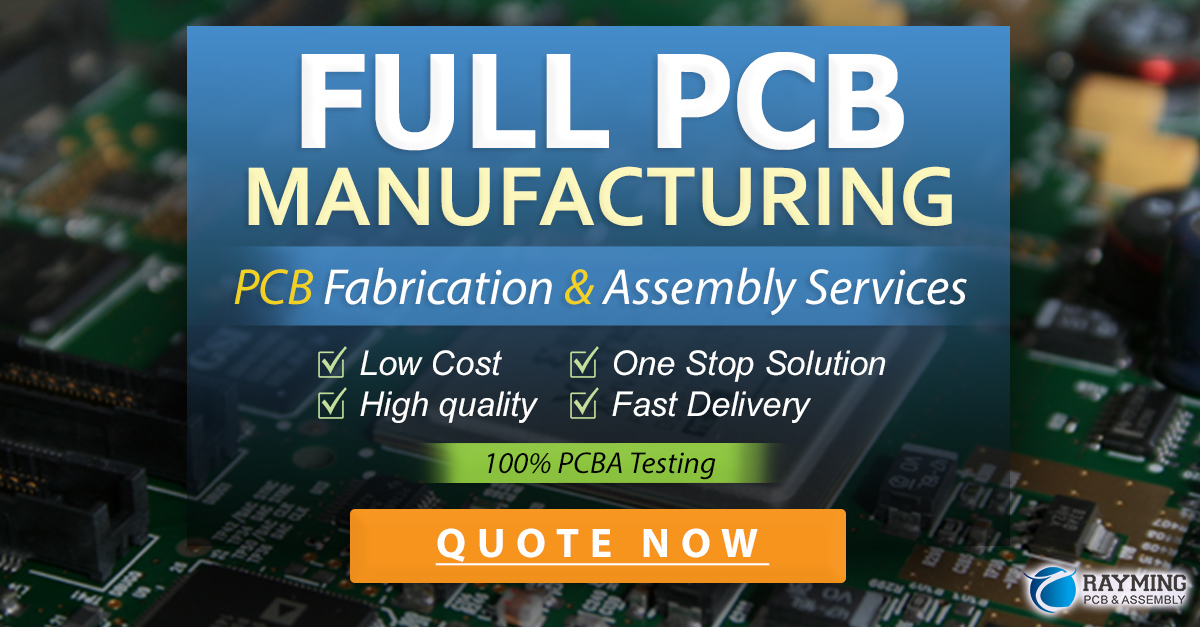
MCPCB Design Considerations
When designing an MCPCB, several factors must be considered to ensure optimal performance and reliability:
- Thermal management: Ensure proper thermal vias and heat spreading techniques are used to maximize heat dissipation.
- Dielectric material selection: Choose a dielectric material with the appropriate thermal conductivity and electrical insulation properties for the application.
- Copper thickness: Select the appropriate copper thickness based on the current carrying requirements and thermal management needs.
- Component placement: Optimize component placement to minimize thermal stress and improve overall system performance.
- Mechanical stress: Consider the mechanical stress on the MCPCB during assembly and operation, particularly for flexible designs.
Applications of MCPCBs
MCPCBs find applications in various industries due to their excellent thermal management and power handling capabilities:
- High-power LED lighting
- Automotive electronics
- Power converters and inverters
- Motor drives
- Telecommunications equipment
- Aerospace and defense systems
- Medical devices
- Industrial automation and control
Benefits of One-Stop MCPCB Manufacturing
Partnering with a one-stop MCPCB Manufacturer offers several advantages:
- Streamlined communication and project management
- Reduced lead times and faster time-to-market
- Improved quality control and consistency
- Access to a wide range of manufacturing capabilities and expertise
- Cost savings through optimized processes and materials
Choosing the Right MCPCB Manufacturer
When selecting an MCPCB manufacturer, consider the following factors:
- Experience and expertise in MCPCB manufacturing
- Range of manufacturing capabilities and services offered
- Quality control processes and certifications
- Ability to handle both rigid and flexible MCPCB designs
- Prototyping and small-batch production capabilities
- Technical support and design assistance
- Lead times and pricing
The Future of MCPCB Manufacturing
As technology advances and new applications emerge, MCPCB manufacturing continues to evolve to meet the growing demands for efficient thermal management and high-power handling. Some of the trends shaping the future of MCPCB manufacturing include:
- Advanced dielectric materials with higher thermal conductivity
- Improved thermal via designs and heat spreading techniques
- Increased adoption of flexible MCPCBs in wearable electronics and IoT devices
- Integration of embedded components and 3D structures
- Sustainable and eco-friendly manufacturing processes
Conclusion
Aluminum PCB Flex and rigid MCPCB manufacturing at a one-stop shop offers numerous benefits for businesses seeking high-quality, reliable, and thermally efficient PCBs. By understanding the manufacturing process, design considerations, and applications of MCPCBs, engineers and product designers can leverage the advantages of this technology to create innovative and high-performance electronic systems.
As the demand for efficient thermal management and high-power handling continues to grow, partnering with an experienced and capable MCPCB manufacturer is essential for success in today’s competitive market.
Frequently Asked Questions (FAQ)
1. What is the difference between an MCPCB and a traditional PCB?
MCPCBs feature a metal substrate, typically aluminum, that acts as a heat sink, while traditional PCBs use FR-4 or other non-metallic substrates. This allows MCPCBs to efficiently dissipate heat and handle higher power densities compared to traditional PCBs.
2. What are the advantages of using flexible MCPCBs?
Flexible MCPCBs combine the thermal management properties of MCPCBs with the flexibility of traditional flexible PCBs. This allows for more complex designs, improved connectivity, and use in applications where flexibility is required, such as wearable electronics and aerospace systems.
3. How do I choose the right dielectric material for my MCPCB?
The choice of dielectric material depends on the specific application requirements, such as thermal conductivity, electrical insulation, and mechanical properties. Consult with your MCPCB manufacturer to select the most appropriate dielectric material for your project.
4. Can MCPCBs be used for high-current applications?
Yes, MCPCBs are well-suited for high-current applications due to their excellent thermal management properties and the ability to use thicker copper layers. However, proper design considerations, such as thermal via placement and copper thickness, must be taken into account.
5. What are the benefits of choosing a one-stop MCPCB manufacturer?
Partnering with a one-stop MCPCB manufacturer offers streamlined communication, reduced lead times, improved quality control, access to a wide range of manufacturing capabilities, and potential cost savings through optimized processes and materials.
Property | Traditional PCB | MCPCB |
---|---|---|
Substrate Material | FR-4, CEM-3, etc. | Aluminum, Copper |
Thermal Conductivity | Low | High |
Power Handling | Moderate | High |
Heat Dissipation | Passive, Limited | Active, Efficient |
Mechanical Stability | Moderate | High |
Flexibility | Limited | Flexible Options Available |
Typical Applications | General Electronics | High-Power LEDs, Automotive, Power Electronics |
Leave a Reply