Understanding Polygon Pours in Altium Designer
Polygon pours are a crucial feature in PCB design software like Altium Designer. They allow designers to fill large copper areas on the PCB with a solid connection to a specified net, providing low-impedance power distribution, shielding, and improved thermal management. However, when working with Rigid-Flex PCBs, designers may encounter issues where the polygon pour breaks along the split lines between rigid and flexible sections. This article will explore the causes of this problem and provide solutions to ensure proper polygon pour behavior in Rigid-Flex Designs.
What are Rigid-Flex PCBs?
Rigid-flex PCBs combine the benefits of both rigid and Flexible PCBs into a single design. They consist of rigid PCB sections connected by flexible PCB sections, allowing the final product to be folded, bent, or twisted to fit into compact spaces or conform to unique shapes. This makes rigid-flex PCBs ideal for applications that require high density, reliability, and unique form factors, such as wearable devices, medical equipment, and aerospace systems.
Polygon Pour Basics
In Altium Designer, polygon pours are created using the Pour Copper feature. Designers can define the shape of the pour area, the net it is connected to, and various properties such as the pour order, thermal relief settings, and clearance rules. Once defined, the polygon pour automatically fills the designated area with copper, connecting to the specified net while adhering to the design rules and clearance settings.
Issues with Polygon Pours on Rigid-Flex Split Lines
When creating polygon pours on rigid-flex PCBs, designers may encounter a problem where the pour breaks or fails to connect along the split lines between the rigid and flexible sections. This can lead to poor power distribution, inadequate shielding, and even signal integrity issues. There are several reasons why this issue may occur:
Incorrect Layer Stack Definition
One of the primary causes of polygon pour breaks on rigid-flex split lines is an incorrect layer stack definition. In Altium Designer, the layer stack must be properly defined to include the rigid and flexible sections, as well as the split lines between them. If the split lines are not correctly defined, the software may not recognize the transition between rigid and flex, resulting in broken polygon pours.
To resolve this issue, designers should carefully review and update the layer stack definition:
- Open the Layer Stack Manager in Altium Designer
- Define the rigid and flexible sections of the PCB
- Ensure that the split lines are correctly placed and assigned to the appropriate layers
- Verify that the layer stack matches the manufacturer’s specifications for the rigid-flex PCB
Incorrect Bend Region Definition
Another factor that can contribute to polygon pour breaks is an incorrect bend region definition. Bend regions are the areas where the flexible sections of the PCB will be bent or folded. If these regions are not properly defined, the polygon pour may not account for the bending and break along the split lines.
To address this issue, designers should:
- Use the Rigid-Flex Wizard in Altium Designer to define the bend regions
- Ensure that the bend regions are placed accurately and do not overlap with components or other design elements
- Verify that the bend region properties, such as the bend radius and bend direction, are set correctly
Clearance Rule Violations
Clearance rules play a crucial role in ensuring that polygon pours maintain the required spacing from other elements on the PCB, such as traces, components, and other polygons. In rigid-flex designs, clearance rule violations along the split lines can cause the polygon pour to break or fail to connect properly.
Designers can resolve clearance rule violations by:
- Reviewing and adjusting the clearance rules in the PCB Rules and Constraints Editor
- Ensuring that the clearance rules account for the unique requirements of rigid-flex designs, such as increased spacing near bend regions
- Running a design rule check (DRC) to identify and resolve any clearance rule violations
Pour Order and Priority
The pour order and priority settings in Altium Designer determine the sequence in which polygon pours are filled and how they interact with other design elements. In some cases, incorrect pour order or priority settings can lead to polygon pour breaks on rigid-flex split lines.
To optimize the pour order and priority:
- Open the Pour Order dialog in Altium Designer
- Arrange the polygon pours in the desired order, with priority given to the most critical pours (e.g., power and ground planes)
- Ensure that the polygon pours are set to “Pour Over All Same Net Objects” to maintain connectivity across split lines
Best Practices for Polygon Pours on Rigid-Flex PCBs
To minimize the occurrence of polygon pour breaks on rigid-flex split lines and ensure optimal performance, designers should adhere to the following best practices:
Use the Rigid-Flex Wizard
Altium Designer’s Rigid-Flex Wizard is a powerful tool that guides designers through the process of creating rigid-flex layer stacks, defining bend regions, and setting up design rules. By using the wizard, designers can ensure that their rigid-flex design is properly configured and less likely to experience polygon pour breaks.
Create Separate Polygons for Rigid and Flex Sections
Instead of using a single polygon pour that spans both rigid and flexible sections, designers can create separate polygons for each section. This approach allows for more control over the pour properties and can help prevent breaks along the split lines.
To implement this method:
- Create separate polygon pours for the rigid and flexible sections of the PCB
- Ensure that the polygons are connected to the same net
- Adjust the pour properties, such as the thermal relief settings and clearance rules, for each polygon as needed
Use Teardrops and Thermal Reliefs
Teardrops and thermal reliefs can help reinforce the connections between polygon pours and other elements on the PCB, such as pads and vias. By using these features, designers can reduce the risk of polygon pour breaks and improve the overall reliability of the rigid-flex design.
To implement teardrops and thermal reliefs:
- Enable the Teardrop feature in the PCB Rules and Constraints Editor
- Adjust the teardrop parameters, such as the size and shape, to suit the design requirements
- Configure the thermal relief settings for pads and vias connected to the polygon pours
Conduct Thorough Design Reviews and DRCs
Regular design reviews and design rule checks (DRCs) are essential for identifying and resolving issues with polygon pours on rigid-flex PCBs. By conducting thorough reviews and running DRCs at various stages of the design process, designers can catch potential problems early and minimize the risk of polygon pour breaks.
To perform effective design reviews and DRCs:
- Schedule regular design reviews with the PCB design team and stakeholders
- Use the DRC feature in Altium Designer to check for clearance rule violations, polygon pour breaks, and other issues
- Review the DRC results and address any flagged issues before proceeding with the design
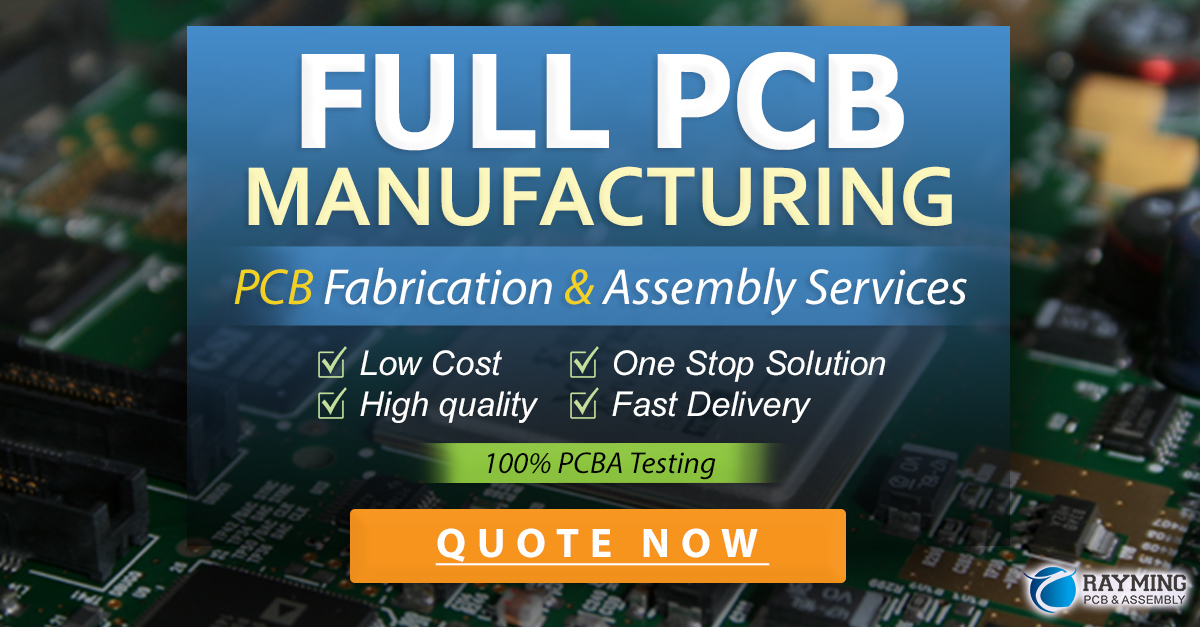
FAQ
-
What are the main causes of polygon pour breaks on rigid-flex split lines?
The main causes of polygon pour breaks on rigid-flex split lines include incorrect layer stack definition, incorrect bend region definition, clearance rule violations, and suboptimal pour order and priority settings. -
How can I prevent polygon pour breaks when designing rigid-flex PCBs in Altium Designer?
To prevent polygon pour breaks in rigid-flex designs, use the Rigid-Flex Wizard to set up the layer stack and bend regions, create separate polygons for rigid and flexible sections, use teardrops and thermal reliefs, and conduct thorough design reviews and DRCs. -
What is the purpose of the Rigid-Flex Wizard in Altium Designer?
The Rigid-Flex Wizard in Altium Designer guides designers through the process of creating rigid-flex layer stacks, defining bend regions, and setting up design rules, helping to ensure that the rigid-flex design is properly configured and less likely to experience issues like polygon pour breaks. -
How do clearance rules affect polygon pours on rigid-flex PCBs?
Clearance rules determine the minimum spacing between polygon pours and other elements on the PCB. In rigid-flex designs, clearance rule violations along the split lines can cause the polygon pour to break or fail to connect properly. Designers should review and adjust clearance rules to account for the unique requirements of rigid-flex designs. -
What are teardrops and thermal reliefs, and how do they help prevent polygon pour breaks?
Teardrops and thermal reliefs are features that reinforce the connections between polygon pours and other elements on the PCB, such as pads and vias. By using these features, designers can reduce the risk of polygon pour breaks and improve the overall reliability of the rigid-flex design.
Conclusion
Polygon pour breaks on rigid-flex split lines can be a frustrating issue for PCB designers, leading to suboptimal power distribution, inadequate shielding, and signal integrity problems. By understanding the causes of these breaks and implementing best practices in Altium Designer, such as using the Rigid-Flex Wizard, creating separate polygons for rigid and flexible sections, and conducting thorough design reviews and DRCs, designers can minimize the occurrence of polygon pour breaks and ensure the optimal performance of their rigid-flex PCBs.
Cause of Polygon Pour Breaks | Solution |
---|---|
Incorrect Layer Stack Definition | Review and update the layer stack definition, ensuring that split lines are correctly defined |
Incorrect Bend Region Definition | Use the Rigid-Flex Wizard to define bend regions accurately |
Clearance Rule Violations | Review and adjust clearance rules to account for rigid-flex requirements |
Suboptimal Pour Order and Priority | Arrange polygon pours in the desired order and set to “Pour Over All Same Net Objects” |
By addressing these issues and following best practices, PCB designers can successfully create reliable and high-performance rigid-flex designs in Altium Designer while minimizing the risk of polygon pour breaks on split lines.
Leave a Reply