Introduction to Flexible PCB
Flexible printed circuit boards, or flexible PCBs, have revolutionized the electronics industry by providing a versatile and compact solution for interconnecting electronic components. Unlike traditional rigid PCBs, flexible PCBs are made from thin, flexible materials that can bend, twist, and fold without breaking or losing their electrical properties. This unique characteristic has made flexible PCBs an essential component in a wide range of applications, from consumer electronics to medical devices and aerospace systems.
What is a Flexible PCB?
A flexible PCB is a type of printed circuit board that is made from a thin, flexible substrate material, such as polyimide or polyester. The substrate is coated with a conductive layer, typically copper, which is etched to create the desired circuit pattern. The circuit pattern is then covered with a protective layer, such as coverlay or solder mask, to insulate and protect the circuitry.
Advantages of Flexible PCBs
Flexible PCBs offer several advantages over traditional rigid PCBs, including:
-
Flexibility: The most obvious advantage of flexible PCBs is their flexibility. They can bend, twist, and fold without breaking or losing their electrical properties, making them ideal for applications where space is limited or where the PCB needs to conform to a specific shape.
-
Lightweight: Flexible PCBs are typically much lighter than rigid PCBs, making them ideal for applications where weight is a critical factor, such as in aerospace or wearable devices.
-
Durability: Despite their flexibility, flexible PCBs are actually more durable than rigid PCBs in many ways. They are resistant to vibration and shock, and they can withstand extreme temperatures and harsh environments.
-
Cost-effective: Flexible PCBs can be more cost-effective than rigid PCBs in certain applications, particularly where the PCB needs to be custom-shaped or where the device requires multiple interconnects.
Types of Flexible PCBs
There are several types of flexible PCBs, each with its own unique characteristics and applications.
Single-sided Flexible PCBs
Single-sided flexible PCBs have a conductive layer on only one side of the substrate. They are the simplest and most cost-effective type of flexible PCB, making them ideal for applications where cost is a primary concern.
Double-sided Flexible PCBs
Double-sided flexible PCBs have conductive layers on both sides of the substrate, allowing for more complex circuit designs and higher component density. They are more expensive than single-sided flexible PCBs but offer greater functionality and flexibility.
Multi-layer Flexible PCBs
Multi-layer flexible PCBs have multiple conductive layers separated by insulating layers, allowing for even more complex circuit designs and higher component density. They are the most expensive type of flexible PCB but offer the greatest functionality and flexibility.
Rigid-Flex PCBs
Rigid-flex PCBs combine both rigid and flexible PCBs into a single board. They consist of one or more rigid PCBs connected by flexible PCBs, allowing for greater design flexibility and improved reliability. Rigid-flex PCBs are commonly used in applications where the PCB needs to be folded or bent around components or where the device requires a high degree of reliability.
Applications of Flexible PCBs
Flexible PCBs are used in a wide range of applications, from consumer electronics to medical devices and aerospace systems. Some of the most common applications include:
Wearable Devices
Flexible PCBs are an essential component in wearable devices, such as smartwatches, fitness trackers, and medical monitoring devices. Their flexibility and lightweight design allow them to conform to the shape of the human body, making them comfortable and unobtrusive to wear.
Medical Devices
Flexible PCBs are widely used in medical devices, such as pacemakers, hearing aids, and implantable sensors. Their flexibility and durability make them ideal for applications where the device needs to be implanted inside the human body or where it needs to withstand harsh environments.
Automotive Electronics
Flexible PCBs are increasingly being used in automotive electronics, such as in-vehicle infotainment systems, advanced driver assistance systems (ADAS), and electric vehicle battery management systems. Their flexibility and durability make them ideal for applications where the PCB needs to withstand extreme temperatures, vibration, and shock.
Aerospace Systems
Flexible PCBs are commonly used in aerospace systems, such as satellites, aircraft, and spacecraft. Their lightweight design and ability to withstand extreme temperatures and harsh environments make them ideal for these applications.
Consumer Electronics
Flexible PCBs are used in a wide range of consumer electronics, such as smartphones, tablets, and digital cameras. Their flexibility and compact design allow for smaller, more portable devices with improved functionality and reliability.
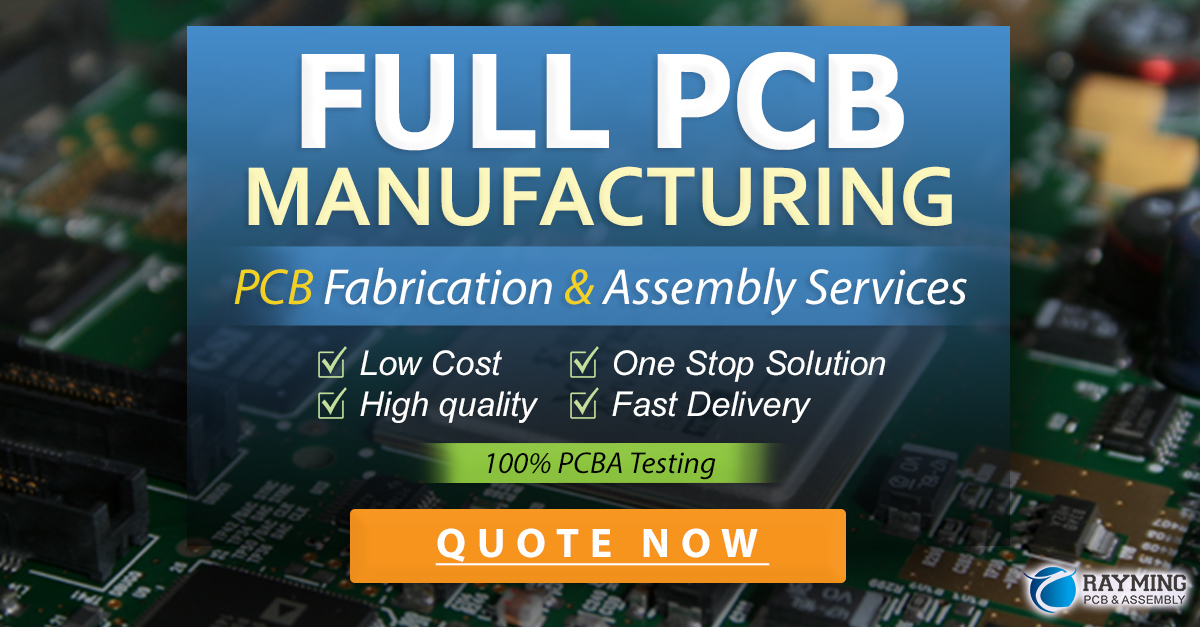
Designing Flexible PCBs
Designing flexible PCBs requires a different approach than designing rigid PCBs. Some of the key considerations when designing flexible PCBs include:
Material Selection
Choosing the right substrate material is critical when designing flexible PCBs. The material must be flexible enough to meet the application requirements while also being durable enough to withstand the expected environmental conditions. Common substrate materials include polyimide, polyester, and PET.
Circuit Design
Designing the circuit for a flexible PCB requires careful consideration of the expected bending and folding of the board. The circuit must be designed to minimize stress on the components and connections while also ensuring adequate electrical performance.
Component Selection
Choosing the right components for a flexible PCB is also critical. The components must be able to withstand the expected bending and folding of the board without breaking or losing their electrical properties. Surface-mount components are typically preferred over through-hole components for flexible PCBs.
Manufacturing Process
Manufacturing flexible PCBs requires specialized equipment and processes. The manufacturing process must be carefully controlled to ensure the quality and reliability of the finished product. Common manufacturing processes for flexible PCBs include photolithography, etching, and lamination.
Challenges and Limitations of Flexible PCBs
While flexible PCBs offer many advantages over traditional rigid PCBs, they also come with some challenges and limitations that designers and manufacturers must consider.
Limited Component Density
Flexible PCBs typically have lower component density than rigid PCBs due to the need for larger spacing between components to accommodate bending and folding. This can limit the functionality and complexity of the circuit design.
Higher Cost
Flexible PCBs are typically more expensive than rigid PCBs due to the specialized materials and manufacturing processes required. This can make them cost-prohibitive for some applications.
Limited Power Handling
Flexible PCBs typically have lower power handling capabilities than rigid PCBs due to the thinner conductors and insulating layers used. This can limit their use in high-power applications.
Reduced Mechanical Strength
While flexible PCBs are durable in many ways, they do have reduced mechanical strength compared to rigid PCBs. This can make them more susceptible to damage from repeated bending and folding.
Future Trends in Flexible PCBs
The demand for flexible PCBs is expected to continue to grow in the coming years, driven by the increasing demand for smaller, more portable electronic devices and the growing use of IoT and wearable technologies. Some of the key trends in flexible PCBs include:
Increased Use of Stretchable Materials
Researchers are developing new stretchable materials that can be used in flexible PCBs, allowing for even greater flexibility and conformability. These materials could enable new applications in wearable devices and medical implants.
3D Printing of Flexible PCBs
3D printing technology is being used to produce flexible PCBs with complex geometries and shapes that would be difficult or impossible to achieve with traditional manufacturing methods. This could enable new applications in aerospace, medical devices, and other industries.
Integration with Other Technologies
Flexible PCBs are being integrated with other technologies, such as sensors, antennas, and batteries, to create more advanced and functional electronic devices. This trend is expected to continue as the demand for smarter, more connected devices grows.
Frequently Asked Questions (FAQ)
- Q: What is the difference between a flexible PCB and a rigid PCB?
A: A flexible PCB is made from a thin, flexible substrate material that can bend and fold without breaking, while a rigid PCB is made from a rigid, non-flexible material. Flexible PCBs offer greater design flexibility and improved durability in certain applications, while rigid PCBs offer higher component density and power handling capabilities.
- Q: What are the most common applications for flexible PCBs?
A: Flexible PCBs are commonly used in wearable devices, medical devices, automotive electronics, aerospace systems, and consumer electronics. They are ideal for applications where the PCB needs to conform to a specific shape or where space is limited.
- Q: What are the advantages of using flexible PCBs?
A: The main advantages of using flexible PCBs include their flexibility, lightweight design, durability, and cost-effectiveness in certain applications. They can also offer improved reliability and functionality compared to rigid PCBs in some cases.
- Q: What are the challenges and limitations of using flexible PCBs?
A: Some of the challenges and limitations of using flexible PCBs include limited component density, higher cost, limited power handling capabilities, and reduced mechanical strength compared to rigid PCBs. Designers and manufacturers must carefully consider these factors when deciding whether to use flexible PCBs in a particular application.
- Q: What are some of the future trends in flexible PCBs?
A: Some of the key trends in flexible PCBs include the increased use of stretchable materials, 3D printing of flexible PCBs, and integration with other technologies such as sensors, antennas, and batteries. These trends are expected to drive new applications and innovations in the field of flexible PCBs in the coming years.
Conclusion
Flexible PCBs have become an essential component in a wide range of electronic devices, from consumer electronics to medical devices and aerospace systems. Their unique characteristics, including flexibility, lightweight design, and durability, have made them a popular choice for applications where traditional rigid PCBs may not be suitable.
As the demand for smaller, more portable electronic devices continues to grow, the use of flexible PCBs is expected to increase in the coming years. Designers and manufacturers will need to carefully consider the advantages and limitations of flexible PCBs when deciding whether to use them in a particular application.
Looking to the future, new materials and manufacturing processes are being developed that could enable even greater functionality and design flexibility in flexible PCBs. The integration of flexible PCBs with other technologies, such as sensors and antennas, is also expected to drive new innovations and applications in the field.
Overall, flexible PCBs represent an exciting and rapidly evolving technology that is poised to play an increasingly important role in the future of electronics. As designers and manufacturers continue to push the boundaries of what is possible with flexible PCBs, we can expect to see new and innovative applications emerge in the years to come.
Leave a Reply