Introduction to Barometric Pressure Sensors
Barometric pressure sensors, also known as absolute pressure sensors, are essential tools for measuring atmospheric pressure in various applications. These sensors play a crucial role in weather monitoring, aviation, automotive systems, and many other fields where accurate pressure measurements are required. In this comprehensive article, we will dive deep into the world of barometric pressure sensors, exploring their working principles, types, applications, and key considerations when selecting the right sensor for your needs.
How Barometric Pressure Sensors Work
Barometric pressure sensors measure the absolute pressure of the surrounding environment, which includes both atmospheric pressure and any additional pressure applied to the sensor. The basic working principle of these sensors involves the use of a pressure-sensitive element, such as a diaphragm or a piezoelectric crystal, that deforms or generates an electrical signal when subjected to pressure changes.
Pressure-Sensitive Elements
The most common pressure-sensitive elements used in barometric pressure sensors are:
-
Diaphragm: A thin, flexible membrane that deflects when exposed to pressure changes. The deflection is then converted into an electrical signal using various transduction methods.
-
Piezoelectric crystal: A material that generates an electrical charge when subjected to mechanical stress, such as pressure changes.
Transduction Methods
Once the pressure-sensitive element responds to pressure changes, the sensor employs one of the following transduction methods to convert the mechanical deformation into an electrical signal:
-
Piezoresistive: The pressure-sensitive element is bonded to a piezoresistive material, which changes its electrical resistance when subjected to mechanical stress. This change in resistance is then measured and correlated to the applied pressure.
-
Capacitive: The pressure-sensitive element acts as one plate of a capacitor, while a fixed plate is placed nearby. As the element deforms due to pressure changes, the capacitance between the plates varies, allowing the sensor to measure the pressure.
-
Optical: The pressure-sensitive element is coupled with an optical system, such as a Fabry-Perot interferometer. Pressure changes cause the element to deform, altering the optical path length and resulting in a change in the interference pattern, which is then used to calculate the pressure.
Types of Barometric Pressure Sensors
Barometric pressure sensors can be classified based on their pressure-sensitive elements, transduction methods, or packaging. Some common types include:
-
MEMS (Micro-Electro-Mechanical Systems) sensors: These sensors use miniaturized mechanical and electrical components, such as diaphragms and piezoresistive elements, to measure pressure. They are known for their small size, low power consumption, and cost-effectiveness.
-
Ceramic capacitive sensors: These sensors employ a ceramic diaphragm and capacitive transduction to measure pressure. They offer high accuracy, stability, and durability, making them suitable for demanding applications.
-
Fiber optic sensors: These sensors use optical fibers and interferometric techniques to measure pressure. They are immune to electromagnetic interference and can operate in harsh environments, such as high-temperature or corrosive conditions.
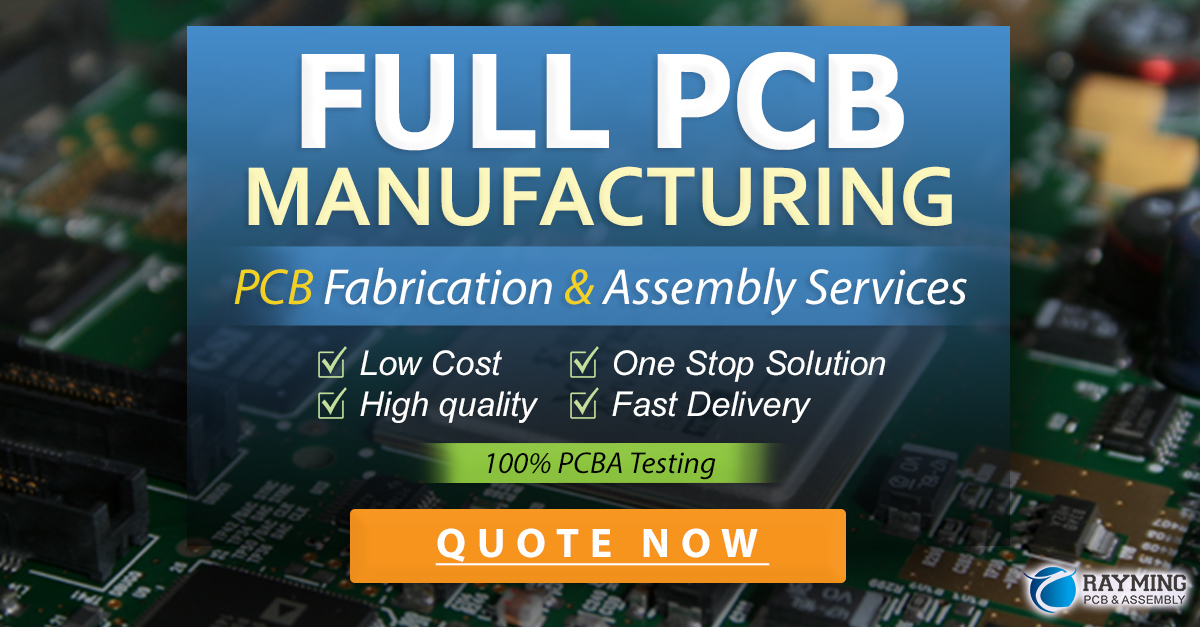
Applications of Barometric Pressure Sensors
Barometric pressure sensors find applications in a wide range of industries and fields, including:
-
Weather monitoring: Barometric pressure sensors are essential components of weather stations, helping meteorologists forecast weather patterns and monitor atmospheric conditions.
-
Aviation: Aircraft rely on barometric pressure sensors for altitude measurement, air data systems, and cabin pressure control.
-
Automotive: Barometric pressure sensors are used in engine management systems, turbocharger control, and altitude compensation for various vehicle subsystems.
-
Medical devices: Pressure sensors are employed in medical equipment, such as ventilators, anesthesia machines, and blood pressure monitors, to ensure accurate and safe operation.
-
Industrial process control: Many industrial processes, such as gas and liquid flow measurement, leak detection, and vacuum monitoring, require precise pressure measurements provided by barometric pressure sensors.
Key Considerations for Selecting Barometric Pressure Sensors
When choosing a barometric pressure sensor for your application, consider the following factors:
-
Pressure range: Ensure that the sensor’s pressure range covers the expected pressure variations in your application.
-
Accuracy and resolution: Determine the required accuracy and resolution for your application and select a sensor that meets or exceeds these requirements.
-
Environmental factors: Consider the operating temperature range, humidity, vibration, and shock levels that the sensor will be exposed to, and choose a sensor that can withstand these conditions.
-
Output type: Select a sensor with an output type (e.g., analog, digital, I2C, SPI) that is compatible with your system’s requirements.
-
Packaging and size: Consider the available space and mounting options in your application, and choose a sensor with a suitable package size and type.
-
Cost: Evaluate the sensor’s cost in relation to your budget and the overall cost of your application.
Calibration and Maintenance of Barometric Pressure Sensors
To ensure accurate and reliable pressure measurements, barometric pressure sensors require proper calibration and maintenance. Some key considerations include:
-
Initial calibration: Perform an initial calibration of the sensor upon installation to ensure accurate readings.
-
Periodic recalibration: Establish a regular calibration schedule to maintain the sensor’s accuracy over time, taking into account the application’s requirements and the sensor’s drift characteristics.
-
Temperature compensation: Many barometric pressure sensors are sensitive to temperature variations. Implement temperature compensation techniques, such as using a separate temperature sensor or a built-in temperature compensation circuit, to minimize the impact of temperature on pressure readings.
-
Moisture and contamination protection: In humid or dusty environments, protect the sensor from moisture and contaminants by using appropriate packaging, filters, or coatings.
-
Handling and storage: Follow the manufacturer’s guidelines for proper handling and storage of the sensor to prevent damage and ensure optimal performance.
Future Trends in Barometric Pressure Sensor Technology
As technology advances, barometric pressure sensors continue to evolve, offering improved performance, smaller sizes, and lower costs. Some notable trends in the field include:
-
Integration of multiple sensors: Manufacturers are developing integrated sensor packages that combine barometric pressure sensors with other sensors, such as temperature, humidity, and gas sensors, to provide comprehensive environmental monitoring solutions.
-
Wireless connectivity: The integration of wireless communication protocols, such as Bluetooth, Wi-Fi, and LoRa, into barometric pressure sensors enables remote monitoring and data logging capabilities.
-
Energy harvesting: Researchers are exploring energy harvesting techniques, such as piezoelectric or thermoelectric energy harvesting, to power barometric pressure sensors, reducing the need for batteries or external power sources.
-
Artificial intelligence and machine learning: The application of AI and machine learning algorithms to pressure sensor data can enable predictive maintenance, fault detection, and advanced data analysis, enhancing the value of pressure measurements in various industries.
Conclusion
Barometric pressure sensors are essential tools for measuring atmospheric pressure in a wide range of applications, from weather monitoring and aviation to automotive systems and industrial process control. By understanding the working principles, types, and key considerations for selecting and maintaining these sensors, engineers and researchers can leverage their capabilities to improve the performance, safety, and efficiency of their systems. As technology continues to advance, the future of barometric pressure sensors promises even greater accuracy, functionality, and integration with other sensing and communication technologies.
FAQs
-
What is the difference between absolute pressure and gauge pressure?
Absolute pressure is the pressure measured relative to a perfect vacuum, while gauge pressure is the pressure measured relative to the ambient atmospheric pressure. Barometric pressure sensors measure absolute pressure, which includes both atmospheric pressure and any additional pressure applied to the sensor. -
How often should I calibrate my barometric pressure sensor?
The frequency of calibration depends on the application’s requirements and the sensor’s drift characteristics. In general, it is recommended to calibrate the sensor upon installation and establish a regular calibration schedule based on the manufacturer’s guidelines and the specific needs of your application. -
Can barometric pressure sensors be used in harsh environments?
Yes, certain types of barometric pressure sensors, such as those with ceramic capacitive or fiber optic sensing elements, are designed to withstand harsh environments, including high temperatures, corrosive substances, and electromagnetic interference. When selecting a sensor for a harsh environment, consider the specific environmental factors and choose a sensor with appropriate packaging and protection features. -
What is the typical accuracy of a barometric pressure sensor?
The accuracy of barometric pressure sensors varies depending on the type of sensor and its specifications. High-end sensors can achieve accuracies of ±0.1 hPa or better, while lower-cost sensors may have accuracies in the range of ±1 to ±5 hPa. When selecting a sensor, consider the accuracy requirements of your application and choose a sensor that meets or exceeds these requirements. -
How do I interface a barometric pressure sensor with my system?
Barometric pressure sensors can have various output types, such as analog voltage, digital I2C, or SPI interfaces. To interface the sensor with your system, first determine the sensor’s output type and ensure that it is compatible with your system’s requirements. Then, follow the manufacturer’s guidelines for wiring and communication protocols to establish a connection between the sensor and your system’s microcontroller or data acquisition device.
Leave a Reply