A flexible joint is a mechanical coupling that allows angular misalignment or offset while transmitting torque and rotating motion. Flexible joints are used to connect rotating shafts that are not precisely aligned or have small parallel or angular misalignments. They accommodate the misalignment and enable smooth power transmission between the driving and driven shafts.
Flexible joints offer several advantages compared to rigid couplings:
Accommodate Misalignment
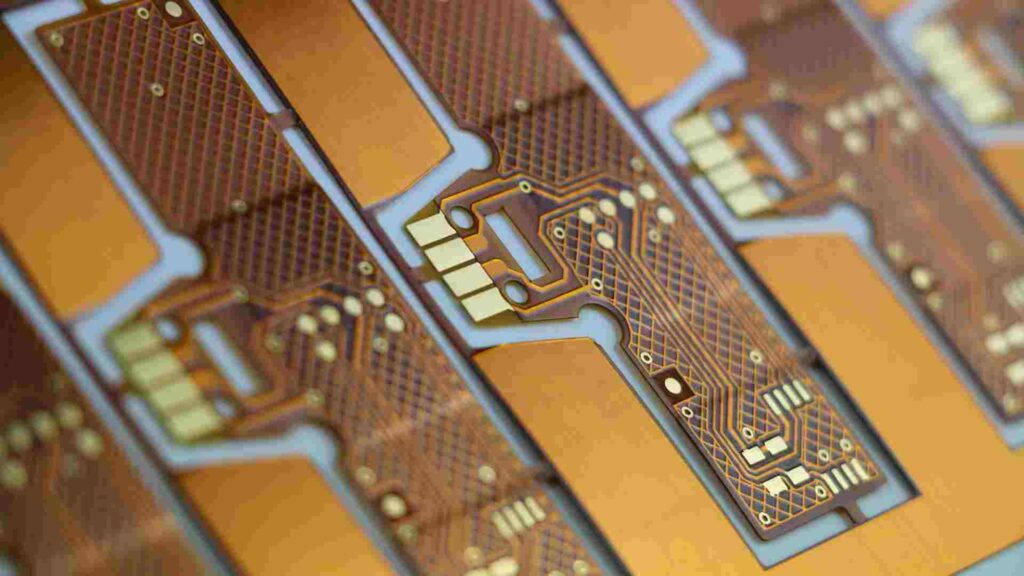
The key benefit of a flexible joint is its ability to accommodate angular, parallel, and axial misalignment between two shafts. Rigid couplings require precise alignment of the shafts, while flexible joints can operate normally even with significant misalignment. This makes installation and maintenance much simpler.
Types of misalignment that flexible joints can accommodate:
- Angular misalignment – when the shaft centerlines converge or diverge from each other. Flexible joints can allow 1° to 4° of angular misalignment.
- Parallel misalignment (offset) – when the shaft centerlines are parallel but offset. Flexible joints can accommodate 0.5 to 4 mm of parallel offset.
- Axial misalignment – when there is a difference in the spacing between the shaft ends. Flexible joints can handle around +/- 1 mm of axial misalignment.
By handling these misalignments, flexible joints prevent excessive loads on the bearings and avoid damage to connected equipment.
Absorb Vibration and Shock Loads
Flexible joints can absorb system vibrations, expansion and shock loads that would otherwise be transmitted to the equipment.
The flexible element (such as rubber, plastic, or metallic discs/springs) allows slight relative motion between the driving and driven shafts. This damps out vibrations and shocks, protecting the bearings and equipment.
Key shock and vibration damping benefits:
- Reduce vibration transmission to foundations and structures.
- Protect equipment components from fatigue failure.
- Isolate noise and vibration sensitive equipment.
- Enable smooth operation even with misaligned shafts.
This makes flexible joints well suited for applications with reciprocating loads, frequent starts/stops, and misalignment – where vibration absorption is critical.
Compensate for Thermal Expansion
Flexible joints can accommodate thermal expansion and contraction of the shafts along their axial direction.
As temperature changes during operation, shafts will expand or contract. With rigid couplings, this axial growth can lead to high loads and equipment damage. Flexible joints can compensate for axial movements up to 1 mm, enabling trouble-free operation.
Enable Quick Maintenance
Flexible joints allow easy assembly/disassembly of connected equipment for maintenance. There is no need to precisely realign shafts after re-assembly – the flexible joint tolerates misalignment.
This avoids costly re-alignment procedures and enables quick maintenance. Flexible joints are also easily replaced when worn, without affecting shaft alignment.
Types of Flexible Joints
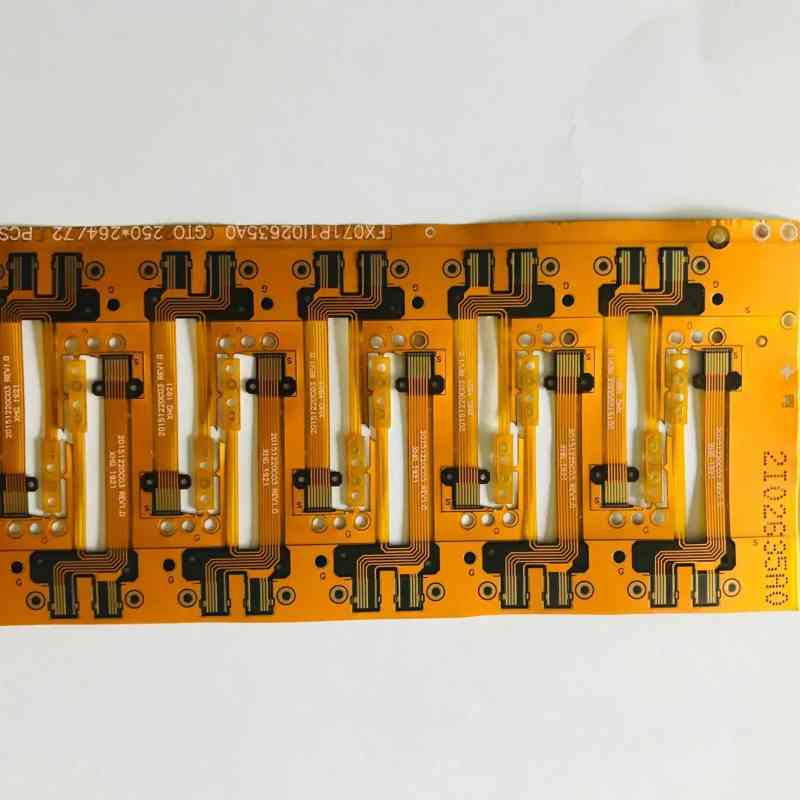
There are many different designs of flexible joints available to suit various applications and operating conditions. The most common types include:
Universal Joints
Universal joints use intersecting shafts and U-shaped yokes to achieve flexibility. They allow transmission of rotary motion at high speeds and variable angles. Universal joints accommodate angular misalignment up to 45°.
Flexible Couplings
Flexible couplings connect shafts using a flexible disc or hub made of rubber, plastic or metal. Different designs offer axial, parallel, and angular flexibility. They are easy to install but have limited vibration damping.
Flexible Shaft Couplings
These couplings join shafts using flexible metallic bellows or helical coils. They accommodate parallel, angular, and axial misalignments. Flexible shaft couplings provide vibration damping and shock absorption capabilities.
Gear Couplings
Gear couplings use two grooved hub sleeves mated by an articulated block. This provides angular and parallel flexibility while transmitting high torque. Gear couplings are robust and can operate at very high speeds.
Grid Couplings
Grid couplings consist of alternating flexible grids and sleeves spaced along the shaft. The flexible grids allow angular and parallel misalignment while damping vibrations. Grid couplings are highly flexible and durable.
Applications of Flexible Joints
Flexible joints are widely used in various industrial rotating machinery to improve reliability and uptime. Typical applications include:
- Connecting electric motors to pumps, compressors, conveyors
- Joining gearboxes to mixers, extruders, mills
- Linking drive shafts in ship propulsion systems
- Coupling steam and gas turbines to generators
- In vehicle propeller shafts and steering systems
- Linking high speed, misaligned spindles in metalworking
Any application involving the transmission of power between misaligned or vibrating shafts can benefit from using a flexible joint.
Design Considerations
Key factors to consider when selecting a flexible joint:<style type=”text/css”> .tg {border-collapse:collapse;border-spacing:0;} .tg td{border-color:black;border-style:solid;border-width:1px;font-family:Arial, sans-serif;font-size:14px; overflow:hidden;padding:10px 5px;word-break:normal;} .tg th{border-color:black;border-style:solid;border-width:1px;font-family:Arial, sans-serif;font-size:14px; font-weight:normal;overflow:hidden;padding:10px 5px;word-break:normal;} .tg .tg-c3ow{border-color:inherit;text-align:center;vertical-align:top} .tg .tg-uys7{border-color:inherit;text-align:center;vertical-align:middle} </style> <table class=”tg”> <thead> <tr> <th class=”tg-uys7″>Factor</th> <th class=”tg-uys7″>Considerations</th> </tr> </thead> <tbody> <tr> <td class=”tg-c3ow”>Torque</td> <td class=”tg-c3ow”>Select joint capacity 20-50% greater than max torque</td> </tr> <tr> <td class=”tg-c3ow”>Misalignment</td> <td class=”tg-c3ow”>Determine angular, parallel, axial misalignments. Select appropriate joint design and movement capacity</td> </tr> <tr> <td class=”tg-c3ow”>Rotation Speed</td> <td class=”tg-c3ow”>Ensure joint speed rating exceeds max RPM. Consider centrifugal force limits</td> </tr> <tr> <td class=”tg-c3ow”>Environment</td> <td class=”tg-c3ow”>Choose suitable joint materials for operating temp., corrosion resistance</td> </tr> <tr> <td class=”tg-c3ow”>Space</td> <td class=”tg-c3ow”>Consider joint dimensions, allow space for inspection/maintenance</td> </tr> </tbody> </table>
Proper selection of flexible joint type, size, materials and design is critical for reliability. Manufacturers can provide sizing guidance and custom engineered solutions.
Conclusion
Flexible joints provide distinct advantages for connecting misaligned shafts while transmitting rotational power smoothly. Key benefits include:
- Accommodating shaft misalignment
- Absorbing vibrations and shock loads
- Compensating for thermal expansion
- Enabling quick equipment maintenance
- Improving reliability in challenging operating conditions
With multiple design variations available, flexible joints can meet the demands of most industrial drivetrain applications. Correct selection and sizing is important to gain maximum benefit. Overall, flexible joints are an essential component in many rotating machinery systems.
Frequently Asked Questions
What is a flexible joint used for?
Flexible joints are used to transmit torque and rotation between two shafts that are misaligned or experience vibration/shock loads. They accommodate parallel, angular, and axial misalignments and also absorb system vibrations and expansions.
How does a flexible joint work?
Flexible joints work using flexible elements made of rubber, plastic, or metal. As the shafts rotate, these elements bend, twist, and flex to allow smooth rotation and power transmission despite misalignment. Different designs use yokes, bellows, discs, springs, splines, or gears to achieve flexibility.
What industries use flexible joints?
Flexible joints are widely used in rotating machinery in industries like oil and gas, mining, power generation, manufacturing, transportation, steel mills, paper and pulp, food processing, and more. Any application with shafts that experience misalignment or vibration can benefit from flexible joints.
What are the advantages over rigid couplings?
Unlike rigid couplings, flexible joints do not require precise shaft alignment, are easier to install/maintain, absorb vibrations, accommodate thermal expansion, and enable operation despite misalignment. This makes them ideal for applications with vibration, shock loads, or frequent disassembly.
What temperatures can flexible joints operate at?
Most standard flexible joints use rubber or plastic flexible elements and are rated for max temperatures around 80°C to 100°C. Special designs using metallic bellows or hinges can handle much higher temps up to 540°C for high temperature applications.
Leave a Reply