What is PCB Solderability?
PCB solderability refers to the ability of a printed circuit board (PCB) to be soldered easily and effectively. It is a critical factor in ensuring the reliability and functionality of electronic devices. Solderability is influenced by various factors such as the surface finish of the PCB, the quality of the solder, and the soldering process itself.
Factors Affecting PCB Solderability
Several factors can impact the solderability of a PCB. These include:
-
Surface Finish: The surface finish of the PCB plays a crucial role in its solderability. Common surface finishes include Hot Air Solder Leveling (HASL), Electroless Nickel Immersion Gold (ENIG), and Organic Solderability Preservative (OSP). Each surface finish has its own advantages and disadvantages in terms of solderability.
-
Solder Quality: The quality of the solder used in the soldering process is another important factor. Poor quality solder can lead to issues such as brittle joints, insufficient wetting, and reduced reliability.
-
Soldering Process: The soldering process itself can also affect the solderability of a PCB. Factors such as the temperature profile, the type of soldering iron used, and the skill of the operator can all impact the quality of the solder joint.
Testing PCB Solderability
To ensure the solderability of a PCB, various tests can be performed. These tests can be divided into two main categories: destructive and non-destructive tests.
Destructive Tests
Destructive tests involve physically altering or damaging the PCB to assess its solderability. Some common destructive tests include:
-
Solder Float Test: In this test, a sample of the PCB is immersed in molten solder for a specified time and temperature. The PCB is then removed and examined for any defects or issues with the solder joint.
-
Wetting Balance Test: This test measures the wetting force of the solder on the PCB. A sample of the PCB is suspended in molten solder, and the force required to remove it is measured. This provides an indication of the solderability of the PCB.
Non-Destructive Tests
Non-destructive tests do not involve any physical alteration or damage to the PCB. Some common non-destructive tests include:
-
Visual Inspection: A visual inspection of the PCB can reveal any obvious defects or issues with the solder joints. This can be done with the naked eye or using magnification tools such as a microscope.
-
X-Ray Inspection: X-ray inspection can be used to examine the internal structure of the solder joint. This can reveal any voids, cracks, or other defects that may not be visible from the surface.
-
Electrical Testing: Electrical testing can be used to verify the functionality of the PCB and ensure that all connections are properly soldered. This can include continuity testing, resistance measurement, and functional testing.
Improving PCB Solderability
There are several steps that can be taken to improve the solderability of a PCB. These include:
-
Proper Storage: PCBs should be stored in a clean, dry environment to prevent oxidation and contamination of the surface finish.
-
Cleaning: Prior to soldering, the PCB should be cleaned to remove any dirt, grease, or other contaminants that may affect the solderability.
-
Proper Solder Selection: The solder used should be of high quality and appropriate for the specific application. Lead-free solder is becoming increasingly common due to environmental concerns.
-
Controlled Soldering Process: The soldering process should be carefully controlled to ensure consistent results. This includes maintaining the proper temperature profile and using appropriate soldering techniques.
Types of PCB Solderability Tests
There are several types of PCB solderability tests that can be performed to assess the quality and reliability of the solder joints. These tests can be categorized into two main groups: qualitative tests and quantitative tests.
Qualitative Tests
Qualitative tests are subjective tests that rely on visual inspection and the judgment of the operator. Some common qualitative tests include:
-
Visual Inspection: As mentioned earlier, visual inspection is a simple but effective way to assess the solderability of a PCB. The operator looks for any obvious defects or issues with the solder joints, such as insufficient wetting, bridging, or voids.
-
Dye Penetrant Test: In this test, a dye is applied to the PCB and allowed to penetrate any cracks or voids in the solder joint. The excess dye is then removed, and the PCB is inspected under ultraviolet light. Any remaining dye indicates the presence of defects in the solder joint.
Quantitative Tests
Quantitative tests provide objective, measurable data on the solderability of a PCB. Some common quantitative tests include:
-
Wetting Balance Test: As described earlier, the wetting balance test measures the wetting force of the solder on the PCB. This provides a quantitative measure of the solderability of the PCB.
-
Solder Spread Test: In this test, a controlled amount of solder is applied to the PCB, and the spread of the solder is measured. A larger spread indicates better solderability.
-
Solder Ball Test: This test involves placing a small ball of solder on the PCB and measuring the time it takes for the ball to collapse and wet the surface. A faster collapse time indicates better solderability.
Comparison of Quantitative Tests
Test | Measurement | Advantages | Disadvantages |
---|---|---|---|
Wetting Balance | Wetting force | Provides quantitative data | Requires specialized equipment |
Solder Spread | Solder spread area | Simple to perform | Affected by solder volume and surface |
Solder Ball | Collapse time | Fast and easy to perform | Limited to small areas |
Interpreting PCB Solderability Test Results
Once the solderability tests have been performed, the results must be interpreted to determine the quality and reliability of the solder joints. Here are some key factors to consider when interpreting the results:
-
Acceptance Criteria: Each solderability test should have clearly defined acceptance criteria that specify the minimum requirements for a passing result. These criteria may vary depending on the specific application and the standards being followed.
-
Comparison to Standards: The results of the solderability tests should be compared to the relevant industry standards, such as IPC-A-610 or J-STD-001. These standards provide guidelines for acceptable solder joint quality and can help ensure consistency and reliability.
-
Statistical Analysis: When multiple samples are tested, statistical analysis can be used to determine the overall solderability of the PCB. This can include calculating the average, standard deviation, and process capability index (Cpk) of the results.
-
Root Cause Analysis: If any failures or defects are identified during the solderability tests, a root cause analysis should be performed to determine the underlying cause of the issue. This may involve examining the PCB design, the manufacturing process, or the soldering materials and equipment.
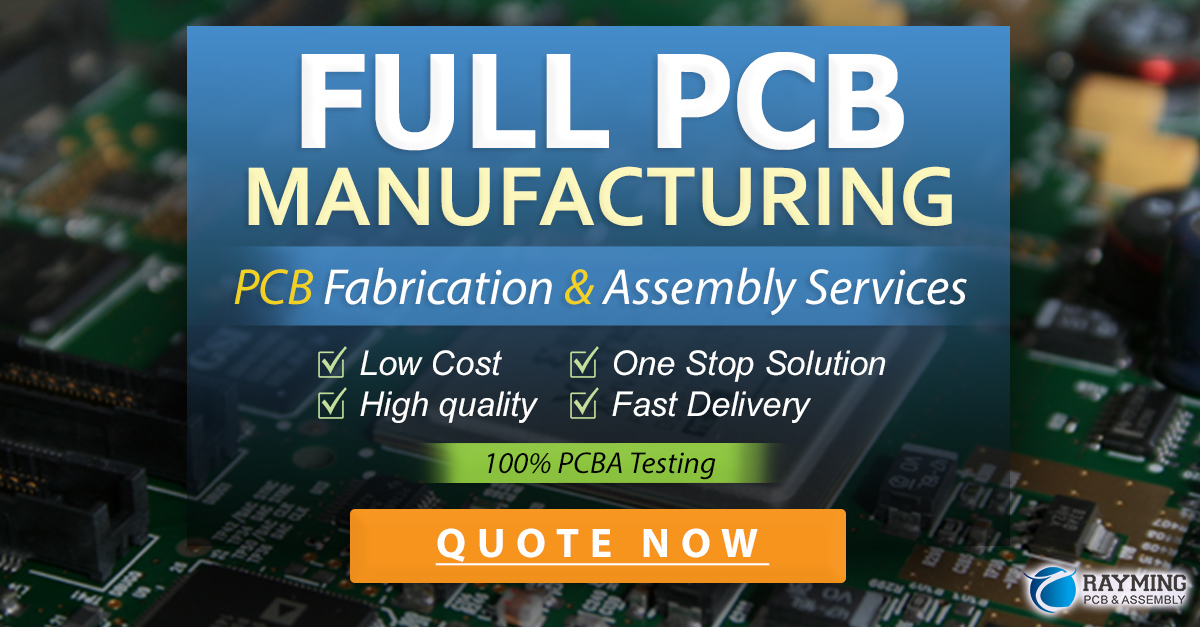
Frequently Asked Questions (FAQ)
-
What is the difference between solderability and solder joint reliability?
Solderability refers to the ability of a PCB to be soldered easily and effectively, while solder joint reliability refers to the long-term durability and functionality of the solder joint under various environmental and operational conditions. -
How often should PCB solderability tests be performed?
The frequency of solderability tests depends on various factors such as the complexity of the PCB, the manufacturing process, and the end-use application. In general, solderability tests should be performed during the initial qualification of a new PCB design or manufacturing process, and then periodically throughout production to ensure consistency and reliability. -
Can solderability tests be performed on assembled PCBs?
While some solderability tests, such as visual inspection and electrical testing, can be performed on assembled PCBs, most destructive and quantitative tests require bare PCB samples. It is generally recommended to perform solderability tests on bare PCBs prior to assembly to identify any issues early in the manufacturing process. -
What are the most common causes of poor solderability?
Poor solderability can be caused by various factors, including contamination of the PCB surface, inadequate surface finish, improper storage or handling, and incorrect soldering materials or processes. Identifying and addressing these root causes is critical for improving solderability and ensuring reliable solder joints. -
How can I improve the solderability of my PCBs?
There are several steps you can take to improve the solderability of your PCBs, including: - Selecting an appropriate surface finish for your application
- Ensuring proper storage and handling of PCBs to prevent contamination
- Using high-quality soldering materials and equipment
- Implementing a robust quality control process that includes regular solderability testing
- Providing adequate training and guidance to personnel involved in the soldering process
Conclusion
PCB solderability is a critical factor in ensuring the reliability and functionality of electronic devices. By understanding the factors that affect solderability, the types of tests that can be performed, and how to interpret the results, manufacturers can take steps to improve the quality and consistency of their solder joints. Regular solderability testing, along with proper storage, handling, and soldering processes, can help ensure that PCBs meet the required standards and perform as intended over their lifetime.
Leave a Reply