What is a Waterproof PCB?
A waterproof printed circuit board (PCB) is a specially designed and manufactured PCB that is resistant to moisture, water, and other liquids. Unlike traditional PCBs, which can be damaged or malfunction when exposed to water, waterproof PCBs are built to withstand wet environments and continue functioning properly.
Waterproof PCBs are essential in many applications where electronic devices are exposed to water or high humidity, such as:
- Outdoor electronics (e.g., security cameras, sensors)
- Marine electronics (e.g., boat navigation systems, fish finders)
- Medical devices (e.g., wearable health monitors)
- Industrial equipment (e.g., sensors, control systems)
- Consumer electronics (e.g., smartwatches, fitness trackers)
How are Waterproof PCBs Made?
The process of making a waterproof PCB involves several key steps and techniques:
1. PCB Design
The first step in creating a waterproof PCB is to design the circuit board with water resistance in mind. This includes:
- Choosing the right PCB material (e.g., FR-4, polyimide)
- Designing the PCB layout to minimize exposed metal surfaces
- Adding protective coatings and sealants to the PCB design
2. PCB Fabrication
Once the PCB design is finalized, the board is fabricated using specialized equipment and processes, such as:
- Multilayer PCB manufacturing
- Controlled Impedance PCB fabrication
- High-density interconnect (HDI) PCB fabrication
3. Conformal Coating
After the PCB is fabricated, a conformal coating is applied to the board to provide an additional layer of protection against water and moisture. Common conformal coating materials include:
- Acrylic
- Silicone
- Polyurethane
- Parylene
Conformal Coating Material | Advantages | Disadvantages |
---|---|---|
Acrylic | Easy to apply, low cost | Limited chemical resistance |
Silicone | Excellent flexibility, wide temperature range | Difficult to repair |
Polyurethane | Good chemical and abrasion resistance | Requires longer cure time |
Parylene | Uniform coverage, excellent barrier properties | Expensive, requires specialized equipment |
4. Encapsulation
In some cases, additional protection may be required beyond conformal coating. Encapsulation involves completely sealing the PCB and its components in a protective material, such as:
- Epoxy
- Silicone gel
- Urethane
Encapsulation provides the highest level of waterproofing but can make repairs and modifications more difficult.
Waterproof PCB Standards and Ratings
Several standards and rating systems exist to classify the level of water resistance provided by a waterproof PCB:
IP Rating (Ingress Protection)
The IP rating system is an international standard that classifies the level of protection provided by an electronic device’s enclosure against solid objects and liquids. The rating consists of two digits:
- The first digit (0-6) indicates protection against solid objects
- The second digit (0-9) indicates protection against liquids
For example, an IP67 rating means the device is completely protected against dust (6) and can withstand immersion in water up to 1 meter deep for 30 minutes (7).
IP Rating | Solid Object Protection | Liquid Protection |
---|---|---|
IP54 | Protected against dust (limited ingress) | Protected against splashing water from all directions |
IP65 | Completely protected against dust | Protected against low-pressure water jets from all directions |
IP67 | Completely protected against dust | Protected against immersion in water up to 1m deep for 30 minutes |
IP68 | Completely protected against dust | Protected against continuous immersion in water (depth and duration specified by manufacturer) |
IEC 60529
IEC 60529 is an international standard that defines the IP rating system and provides guidelines for testing and certifying electronic devices for water resistance.
MIL-STD-810
MIL-STD-810 is a U.S. military standard that outlines environmental testing requirements for electronic equipment, including water resistance. The standard includes several test methods for evaluating a device’s ability to withstand exposure to water, such as:
- Rain and blowing rain
- Immersion
- Humidity
- Salt fog
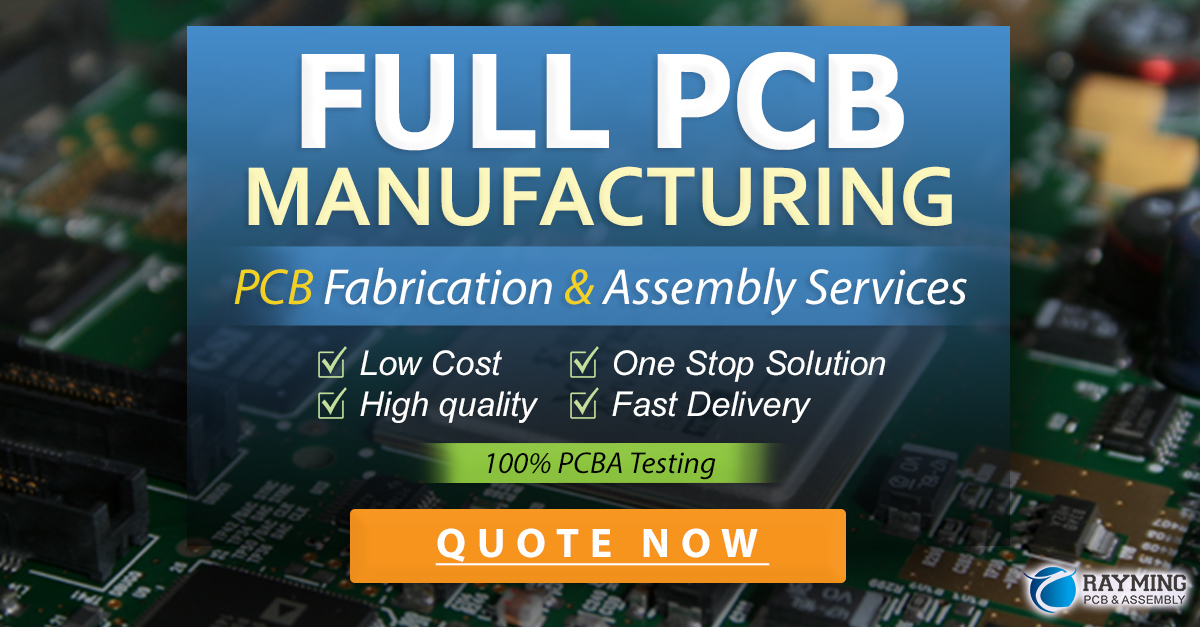
Advantages of Waterproof PCBs
Using waterproof PCBs offers several key benefits:
-
Increased reliability: Waterproof PCBs are less likely to fail or malfunction due to exposure to water or moisture, resulting in more reliable electronic devices.
-
Longer lifespan: By protecting the PCB and its components from water damage, waterproof PCBs can help extend the lifespan of electronic devices.
-
Wider application range: Waterproof PCBs enable electronic devices to be used in a wider range of environments and applications, including outdoor and marine settings.
-
Reduced maintenance: With better protection against water and moisture, waterproof PCBs require less maintenance and repair over time.
Challenges and Considerations
While waterproof PCBs offer many benefits, there are also some challenges and considerations to keep in mind:
-
Higher cost: The additional materials and processes required to make a PCB waterproof can increase the overall cost of the board compared to a standard PCB.
-
Design complexity: Designing a waterproof PCB requires careful consideration of factors such as component placement, coating application, and sealing methods, which can add complexity to the design process.
-
Repair and modification: Waterproof PCBs, especially those with encapsulation, can be more difficult to repair or modify if needed.
-
Testing and certification: Ensuring a PCB meets the desired level of water resistance requires thorough testing and, in some cases, certification to relevant standards, which can add time and cost to the development process.
FAQ
1. What is the difference between water-resistant and waterproof PCBs?
Water-resistant PCBs are designed to withstand some exposure to water and moisture but may not provide complete protection against immersion or prolonged exposure. Waterproof PCBs, on the other hand, are designed to provide complete protection against water and moisture, even in submerged conditions.
2. Can standard PCBs be made waterproof?
While it is possible to add conformal coatings or encapsulation to standard PCBs to increase their water resistance, achieving true waterproofing often requires designing the PCB specifically for that purpose from the start. This allows for the integration of waterproofing features and materials throughout the PCB design and fabrication process.
3. How long do waterproof PCBs last?
The lifespan of a waterproof PCB depends on various factors, such as the level of waterproofing, the environment in which it is used, and the quality of the materials and manufacturing processes. In general, well-designed and properly maintained waterproof PCBs can last for several years, even in harsh environments.
4. Are waterproof PCBs more expensive than standard PCBs?
Yes, waterproof PCBs are typically more expensive than standard PCBs due to the additional materials, processes, and design considerations required to achieve water resistance. The exact cost difference depends on factors such as the size and complexity of the PCB, the level of waterproofing required, and the volume of boards being produced.
5. Can waterproof PCBs be used in all electronic devices?
While waterproof PCBs can be used in a wide range of electronic devices, they may not be necessary or cost-effective for all applications. Devices that are not exposed to water or moisture, or those that have other means of protection (e.g., waterproof enclosures), may not require waterproof PCBs. It is important to carefully consider the specific requirements and operating environment of a device when deciding whether to use waterproof PCBs.
Leave a Reply