What is Design for Manufacturability (DFM)?
Design for Manufacturability (DFM) is the practice of designing products in a way that makes them easier, faster, and more cost-effective to manufacture. DFM involves considering various aspects of the manufacturing process during the design phase, such as material selection, part geometry, tolerances, and assembly methods. By incorporating DFM principles early in the product development cycle, companies can avoid costly design changes, reduce production time, and improve overall product quality.
Why Outsource DFM?
Outsourcing DFM services to a specialized provider like RAYMING offers several advantages over handling it in-house:
-
Access to Expert Knowledge: RAYMING has a team of experienced engineers and designers who specialize in DFM. They have in-depth knowledge of various manufacturing processes, materials, and industry best practices, allowing them to provide expert guidance and recommendations.
-
Cost Savings: Maintaining an in-house DFM team can be expensive, requiring significant investments in hiring, training, and equipment. By outsourcing to RAYMING, you can access their expertise and resources on an as-needed basis, reducing overhead costs and allowing you to allocate resources more efficiently.
-
Faster Time-to-Market: RAYMING’s streamlined DFM processes and advanced tools can help identify and resolve potential manufacturability issues early in the design phase. This can significantly reduce the number of design iterations and accelerate your product’s time-to-market.
-
Focus on Core Competencies: Outsourcing DFM allows your team to focus on their core competencies, such as product innovation, marketing, and sales, while leaving the manufacturability aspects to the experts at RAYMING.
RAYMING’s DFM Services
RAYMING offers a comprehensive suite of DFM services tailored to meet the unique needs of each client. Some of their key services include:
1. Design Review and Analysis
RAYMING’s engineers review your product design files and provide detailed feedback on potential manufacturability issues. They analyze factors such as part geometry, material selection, tolerances, and assembly methods, and offer recommendations for design optimization.
2. Material Selection and Optimization
Choosing the right materials is crucial for ensuring product performance, durability, and cost-effectiveness. RAYMING’s experts can help you select the most suitable materials based on your product requirements, manufacturing processes, and budget constraints.
3. Tolerance Analysis and Optimization
Proper tolerance management is essential for ensuring product quality and reducing manufacturing costs. RAYMING’s engineers use advanced tools and techniques to analyze your design’s tolerance stack-up and identify areas for optimization, minimizing the risk of assembly issues and reducing scrap rates.
4. Manufacturing Process Selection
RAYMING’s team can help you select the most appropriate manufacturing processes for your product based on factors such as production volume, material properties, and cost considerations. They have expertise in various processes, including injection molding, CNC machining, sheet metal fabrication, and 3D printing.
5. Assembly and Packaging Optimization
RAYMING’s DFM services also cover assembly and packaging aspects of your product. They can provide guidance on designing for easy assembly, reducing the number of parts, and optimizing packaging to minimize costs and improve product protection during shipping and handling.
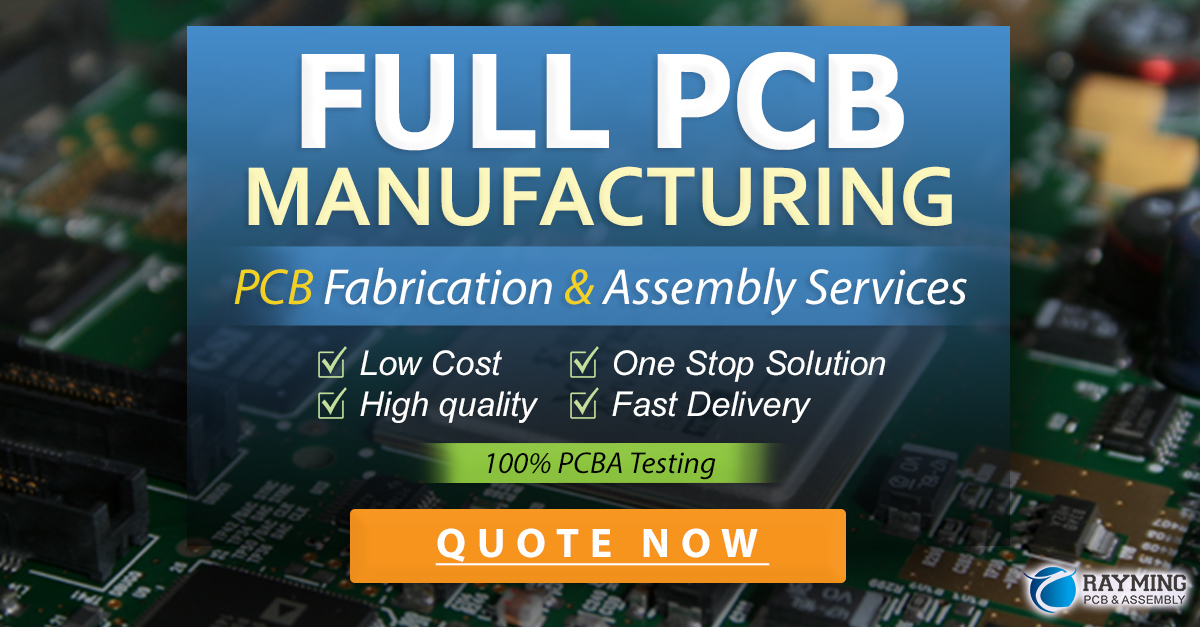
RAYMING’s DFM Process
RAYMING follows a structured and collaborative approach to DFM, working closely with clients throughout the product development cycle. Their typical DFM process includes the following steps:
-
Design File Submission: Clients submit their product design files to RAYMING, typically in CAD formats such as STEP, IGES, or native CAD files.
-
Initial Design Review: RAYMING’s engineers perform an initial review of the design files to identify potential manufacturability issues and areas for improvement.
-
DFM Analysis and Recommendations: Based on the initial review, RAYMING conducts a detailed DFM analysis using advanced tools and simulations. They provide a comprehensive report with specific recommendations for design optimization.
-
Collaborative Design Iteration: RAYMING works closely with the client’s design team to implement the recommended changes and iterate on the design until it meets all manufacturability requirements.
-
Final Design Verification: Once the design is finalized, RAYMING performs a final verification to ensure that all DFM principles have been incorporated and the product is ready for manufacturing.
Case Studies
To illustrate the benefits of outsourcing DFM to RAYMING, let’s take a look at two case studies:
Case Study 1: Medical Device Manufacturer
A leading medical device manufacturer partnered with RAYMING to optimize the design of a new surgical instrument. The company faced challenges in achieving the required precision and reliability while keeping manufacturing costs down.
RAYMING’s DFM experts reviewed the initial design and identified several areas for improvement, including:
- Simplifying the part geometry to reduce machining complexity
- Optimizing tolerances to minimize the risk of assembly issues
- Selecting alternative materials to reduce costs without compromising performance
By implementing RAYMING’s recommendations, the medical device manufacturer achieved:
Benefit | Improvement |
---|---|
Manufacturing Cost Reduction | 25% |
Production Lead Time Reduction | 30% |
Scrap Rate Reduction | 50% |
Overall Product Quality Improvement | Significant |
Case Study 2: Automotive Supplier
An automotive supplier engaged RAYMING to help optimize the design of a new electronic control unit (ECU) housing. The supplier needed to ensure the housing could withstand harsh operating conditions while meeting strict cost and weight targets.
RAYMING’s DFM team conducted a thorough analysis of the initial design and provided recommendations, including:
- Optimizing the wall thickness to reduce material usage and weight
- Incorporating design features to enhance structural rigidity
- Selecting a high-performance plastic material with excellent thermal and mechanical properties
By partnering with RAYMING, the automotive supplier achieved the following results:
Benefit | Improvement |
---|---|
Weight Reduction | 15% |
Material Cost Savings | 20% |
Tooling Cost Savings | 30% |
Product Performance Improvement | Significant |
These case studies demonstrate the tangible benefits of outsourcing DFM to RAYMING, including cost savings, improved product quality, and faster time-to-market.
FAQ
-
Q: How do I get started with outsourcing DFM to RAYMING?
A: To get started, simply reach out to RAYMING’s sales team and provide them with your product design files. They will review your files and provide a detailed proposal outlining the scope of work, timeline, and pricing. -
Q: What CAD formats does RAYMING accept?
A: RAYMING accepts a wide range of CAD formats, including STEP, IGES, and native CAD files from popular software such as SolidWorks, CATIA, and NX. -
Q: How long does the DFM process typically take?
A: The duration of the DFM process depends on the complexity of your product and the extent of the required design changes. However, RAYMING’s streamlined processes and advanced tools generally allow for faster turnaround times compared to handling DFM in-house. -
Q: Will outsourcing DFM to RAYMING compromise the confidentiality of my product design?
A: No, RAYMING takes client confidentiality very seriously. They have strict non-disclosure agreements (NDAs) in place and follow industry-standard security protocols to protect your intellectual property. -
Q: Can RAYMING help with DFM for products manufactured outside of China?
A: Yes, RAYMING’s DFM services are not limited to products manufactured in China. They have experience working with clients and manufacturers globally and can provide DFM support for products manufactured in various regions.
Conclusion
Outsourcing DFM services to a specialized provider like RAYMING can offer significant benefits for companies looking to optimize their product development processes and reduce costs. With their expert knowledge, advanced tools, and streamlined processes, RAYMING can help you identify and resolve potential manufacturability issues early in the design phase, leading to faster time-to-market, improved product quality, and substantial cost savings.
By partnering with RAYMING for your DFM needs, you can focus on your core competencies while leveraging their expertise to ensure your products are designed for optimal manufacturability. Don’t let manufacturability challenges hold back your product development efforts – consider outsourcing DFM to RAYMING and take your products to the next level.
Leave a Reply