What are Medical PCBs?
Medical PCBs are specialized printed circuit boards designed and manufactured specifically for use in medical devices and equipment. These PCBs must meet stringent quality and regulatory standards to ensure the safety and reliability of the medical devices they are integrated into. Medical PCBs are used in a wide range of applications, including:
- Diagnostic imaging equipment (X-ray, MRI, CT scanners)
- Patient monitoring systems
- Implantable devices (pacemakers, defibrillators)
- Surgical instruments
- Laboratory equipment
- Wearable medical devices
The Role of Medical PCB Manufacturers
Medical PCB manufacturers are responsible for the design, fabrication, assembly, and testing of printed circuit boards for medical devices. Their primary goal is to produce high-quality, reliable PCBs that meet the unique requirements of the medical industry. Some of the key responsibilities of medical PCB manufacturers include:
1. Compliance with Regulatory Standards
Medical PCB manufacturers must comply with various regulatory standards and guidelines to ensure the safety and effectiveness of medical devices. These standards include:
- ISO 13485: Quality management system for medical devices
- IPC-6012: Qualification and performance specification for rigid printed boards
- IPC-A-600: Acceptability of printed boards
- FDA 21 CFR Part 820: Quality system regulation for medical devices
Compliance with these standards requires medical PCB manufacturers to implement strict quality control processes, maintain detailed documentation, and undergo regular audits.
2. Material Selection
Medical PCBs require the use of high-quality, biocompatible materials that can withstand the rigors of medical applications. Medical PCB manufacturers must carefully select materials that are:
- Non-toxic and non-reactive with human tissue
- Resistant to sterilization processes (e.g., autoclaving, gamma radiation)
- Capable of operating in harsh environments (e.g., high humidity, extreme temperatures)
- Durable and reliable over extended periods
Some common materials used in medical PCBs include polyimide, polytetrafluoroethylene (PTFE), and ceramic substrates.
3. Specialized Manufacturing Processes
Medical PCB manufacturers employ specialized manufacturing processes to ensure the highest level of quality and reliability. These processes may include:
- Clean room manufacturing to minimize contamination
- Automated optical inspection (AOI) to detect defects
- X-ray inspection to verify internal structures
- Functional testing to ensure proper operation
- Conformal coating to protect against moisture and contaminants
By utilizing these advanced manufacturing techniques, medical PCB manufacturers can produce PCBs that meet the stringent requirements of the medical industry.
4. Supply Chain Management
Medical PCB manufacturers must maintain a robust and reliable supply chain to ensure the timely delivery of high-quality components and materials. This involves:
- Qualifying and monitoring suppliers
- Maintaining adequate inventory levels
- Ensuring traceability of components
- Implementing counterfeit prevention measures
Effective supply chain management is essential for meeting production schedules and avoiding delays in the development and manufacturing of medical devices.
Challenges Faced by Medical PCB Manufacturers
Medical PCB manufacturers face several unique challenges due to the stringent requirements and regulations of the medical industry. Some of these challenges include:
1. Miniaturization and High Density
As medical devices become smaller and more complex, medical PCBs must be designed with higher component density and smaller feature sizes. This requires advanced manufacturing capabilities and expertise in miniaturization techniques, such as microvia technology and high-density interconnect (HDI) PCBs.
2. Reliability and Durability
Medical PCBs must be designed and manufactured to withstand the rigors of medical applications, including exposure to harsh environments, frequent sterilization, and long-term use. Ensuring the reliability and durability of medical PCBs requires extensive testing, the use of high-quality materials, and robust manufacturing processes.
3. Regulatory Compliance
Compliance with regulatory standards and guidelines is a critical challenge for medical PCB manufacturers. Keeping up with evolving regulations, maintaining detailed documentation, and undergoing regular audits can be time-consuming and resource-intensive. Medical PCB manufacturers must have a thorough understanding of the regulatory landscape and implement effective quality management systems to ensure ongoing compliance.
4. Cost Pressures
The medical industry is increasingly focused on cost containment, putting pressure on medical PCB manufacturers to reduce costs while maintaining high quality and reliability. This requires manufacturers to optimize their processes, leverage automation, and implement lean manufacturing principles to improve efficiency and minimize waste.
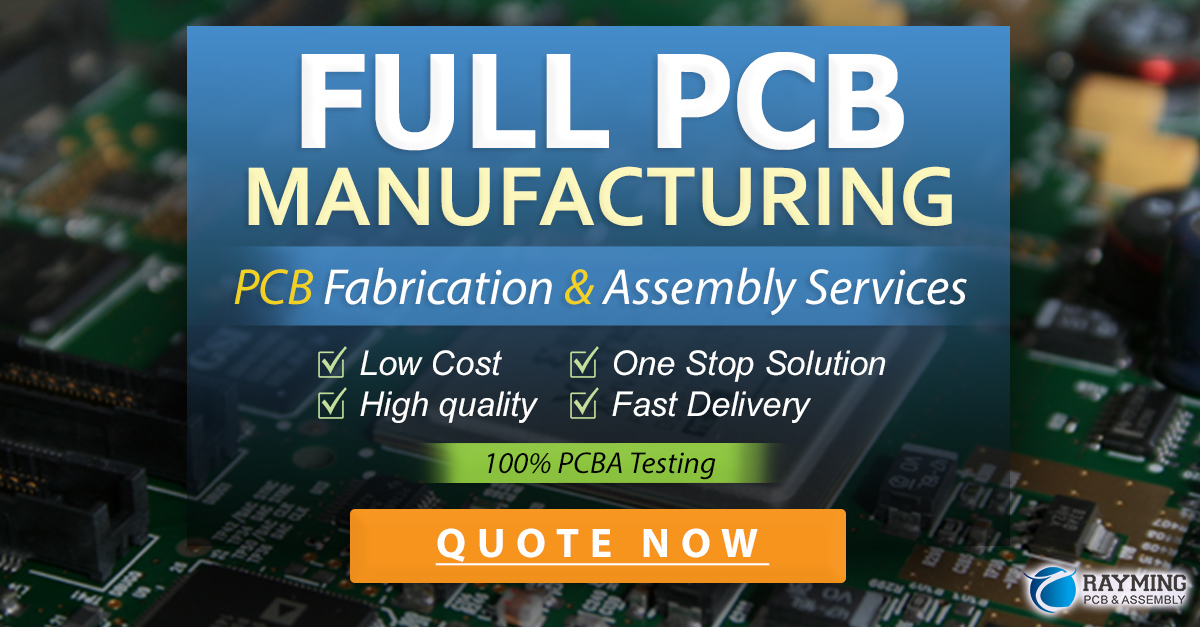
Selecting the Best Medical PCB Manufacturer
Choosing the right medical PCB manufacturer is crucial for the success of your medical device project. When evaluating potential manufacturers, consider the following factors:
1. Experience and Expertise
Look for a manufacturer with extensive experience in producing PCBs for medical applications. They should have a deep understanding of the unique requirements and challenges of the medical industry and a proven track record of delivering high-quality, reliable PCBs.
2. Quality Management System
Ensure that the manufacturer has a robust quality management system in place, preferably certified to ISO 13485. This demonstrates their commitment to quality and their ability to consistently produce PCBs that meet the stringent requirements of the medical industry.
3. Manufacturing Capabilities
Evaluate the manufacturer’s manufacturing capabilities to ensure they can meet your specific requirements. This includes their ability to handle complex designs, high-density layouts, and specialized materials. Also, consider their capacity to scale production to meet your volume needs.
4. Regulatory Compliance
Verify that the manufacturer is compliant with relevant regulatory standards and guidelines, such as IPC and FDA regulations. Ask for evidence of their compliance, such as audit reports and certifications.
5. Supply Chain Management
Assess the manufacturer’s supply chain management practices to ensure they can maintain a reliable and traceable supply of components and materials. This is critical for ensuring the quality and consistency of your medical PCBs.
6. Customer Support and Communication
Choose a manufacturer that offers excellent customer support and maintains open and transparent communication throughout the project. They should be responsive to your needs, provide timely updates, and be proactive in addressing any issues or concerns.
FAQ
1. What is the difference between medical PCBs and standard PCBs?
Medical PCBs are designed and manufactured to meet the stringent quality and regulatory requirements of the medical industry. They must be made from biocompatible materials, withstand harsh environments, and ensure reliable performance over extended periods. Standard PCBs, on the other hand, may not be subject to the same level of rigorous standards and may not be suitable for use in medical devices.
2. How long does it typically take to manufacture a medical PCB?
The lead time for manufacturing a medical PCB can vary depending on the complexity of the design, the materials used, and the manufacturing processes required. On average, the lead time can range from 4 to 12 weeks, but this can be longer for more complex projects or shorter for simpler designs.
3. Are medical PCBs more expensive than standard PCBs?
Yes, medical PCBs are generally more expensive than standard PCBs due to the higher quality materials, specialized manufacturing processes, and the need to comply with stringent regulatory requirements. The cost of a medical PCB can be several times higher than a comparable standard PCB.
4. What certifications should I look for when selecting a medical PCB manufacturer?
When selecting a medical PCB manufacturer, look for certifications such as ISO 13485 (quality management system for medical devices), ISO 9001 (quality management system), and IPC 6012 (qualification and performance specification for rigid printed boards). These certifications demonstrate the manufacturer’s commitment to quality and their ability to meet the requirements of the medical industry.
5. Can medical PCBs be reworked or repaired?
Reworking or repairing a medical PCB can be challenging due to the high-reliability requirements and the need to maintain the integrity of the board. In many cases, it may be necessary to replace the entire PCB rather than attempt a repair. If a repair is necessary, it should only be performed by a qualified and experienced technician using approved methods and materials.
Conclusion
Medical PCB manufacturers play a vital role in the development and production of high-quality, reliable printed circuit boards for medical devices and equipment. By adhering to strict quality standards, utilizing specialized manufacturing processes, and maintaining a robust supply chain, these manufacturers ensure that medical PCBs meet the unique requirements of the medical industry.
When selecting a medical PCB manufacturer, it is essential to consider factors such as experience, quality management, manufacturing capabilities, regulatory compliance, and customer support. By partnering with the right manufacturer, you can ensure the success of your medical device project and deliver safe, effective, and reliable products to the market.
As the medical industry continues to evolve and demand more advanced and miniaturized devices, medical PCB manufacturers will need to stay at the forefront of technology and adapt to new challenges. By investing in innovation, quality, and expertise, these manufacturers will be well-positioned to support the growth and development of the medical device industry for years to come.
Here is a table comparing key aspects of medical PCBs and standard PCBs:
Aspect | Medical PCBs | Standard PCBs |
---|---|---|
Materials | Biocompatible, high-quality materials | Wide range of materials available |
Manufacturing Process | Specialized processes, clean room manufacturing | Standard manufacturing processes |
Quality Standards | Stringent, compliance with ISO 13485, FDA regulations | Less stringent, compliance with IPC standards |
Reliability | High, designed for long-term use in harsh environments | Varies based on application and design |
Cost | Higher due to specialized materials and processes | Lower, varies based on complexity and volume |
Lead Time | Longer, typically 4-12 weeks or more | Shorter, typically 1-4 weeks |
This table highlights the key differences between medical PCBs and standard PCBs, emphasizing the higher quality standards, specialized materials and processes, and increased costs associated with medical PCBs.
Leave a Reply