Introduction to PCB Prototyping
PCB prototyping is an essential step in the development of electronic devices. It allows designers and engineers to test and validate their designs before mass production. However, building a PCB Prototype can be costly and time-consuming, especially for small businesses and hobbyists. In this article, we will explore 14 steps to build your PCB prototype at a low cost.
Step 1: Choose the Right PCB Design Software
Choosing the right PCB design software is crucial for creating a high-quality PCB prototype. There are many software options available, ranging from free open-source tools to expensive commercial software. Some popular PCB design software include:
Software | Type | Price |
---|---|---|
KiCad | Open-source | Free |
Eagle | Commercial | $169 (Standard), $820 (Premium) |
Altium Designer | Commercial | $495/month |
OrCAD | Commercial | $2,995 (Standard), $7,995 (Professional) |
When choosing PCB design software, consider your budget, the complexity of your design, and the features you need.
Step 2: Create Your PCB Design
Once you have chosen your PCB design software, it’s time to create your PCB design. Here are some tips to keep in mind:
- Keep your design simple and modular
- Use standard component sizes and footprints
- Follow the design rules and guidelines provided by your PCB manufacturer
- Use a grid to align components and traces
- Keep your traces as short and straight as possible
- Avoid sharp angles and use curved traces instead
- Use ground planes to reduce noise and improve signal integrity
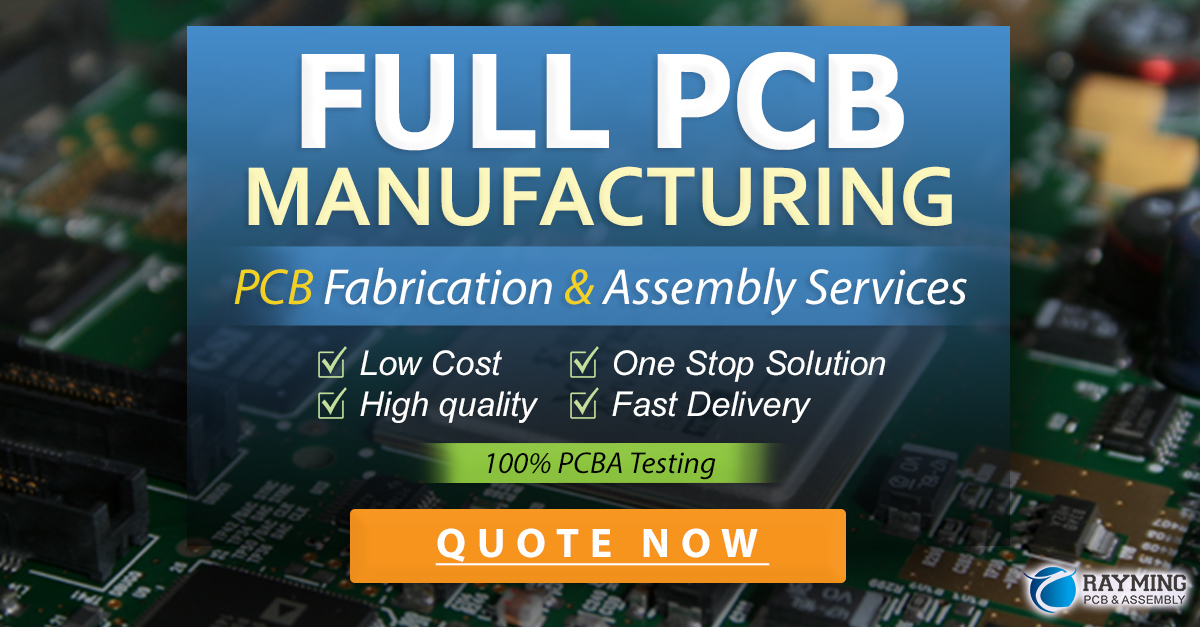
Step 3: Choose Your PCB Material
The material you choose for your PCB will depend on your application and budget. The most common PCB materials are:
Material | Description | Cost |
---|---|---|
FR-4 | Most common, made of fiberglass and epoxy resin | Low |
Polyimide | High-temperature and flexible material | High |
Aluminum | Used for heat dissipation | Medium |
Ceramic | Used for high-frequency applications | High |
FR-4 is the most cost-effective option for most applications.
Step 4: Choose Your PCB Thickness
The thickness of your PCB will depend on your application and the number of layers you need. The most common PCB thicknesses are:
Thickness | Layers | Application |
---|---|---|
0.8mm | 1-2 | Low-cost, simple designs |
1.6mm | 2-4 | Most common, good for most applications |
2.4mm | 4-6 | High-power, high-layer count designs |
Thinner PCBs are cheaper but may be more fragile and prone to warping.
Step 5: Choose Your Copper Weight
The copper weight of your PCB refers to the thickness of the copper layer. The most common copper weights are:
Weight | Thickness | Application |
---|---|---|
1 oz | 35 µm | Most common, good for most applications |
2 oz | 70 µm | High-current, high-power designs |
3 oz | 105 µm | Very high-current, high-power designs |
Higher copper weights are more expensive but can handle higher currents and power.
Step 6: Choose Your Solder Mask Color
The solder mask is a protective layer that covers the copper traces on your PCB. The most common solder mask colors are:
Color | Description |
---|---|
Green | Most common, good contrast with white silkscreen |
Red | High visibility, good for prototypes |
Blue | Aesthetically pleasing, good for consumer products |
Black | Hides imperfections, good for high-end products |
White | High contrast, good for LED lighting |
The choice of solder mask color is mostly aesthetic, but can also affect the visibility of your components and traces.
Step 7: Choose Your Silkscreen Color
The silkscreen is the text and graphics printed on top of your PCB. The most common silkscreen colors are:
Color | Description |
---|---|
White | Most common, good contrast with green solder mask |
Black | Good contrast with white solder mask |
Yellow | High visibility, good for warning labels |
The choice of silkscreen color should provide good contrast with your solder mask color.
Step 8: Choose Your Surface Finish
The surface finish is the coating applied to the exposed copper pads on your PCB. The most common surface finishes are:
Finish | Description | Cost |
---|---|---|
HASL | Hot Air Solder Leveling, most common | Low |
ENIG | Electroless Nickel Immersion Gold, good for fine-pitch components | High |
OSP | Organic Solderability Preservative, cheap but short shelf life | Low |
Immersion Silver | Good for high-frequency applications | Medium |
Immersion Tin | Good for lead-free soldering | Medium |
The choice of surface finish will depend on your application, budget, and the types of components you are using.
Step 9: Generate Your Gerber Files
Once your PCB design is complete, you need to generate Gerber files to send to your PCB manufacturer. Gerber files are the industry standard format for PCB manufacturing and include all the information needed to fabricate your PCB, including:
- Copper layers
- Solder mask layers
- Silkscreen layers
- Drill files
Most PCB design software can generate Gerber files automatically. Make sure to double-check your Gerber files before sending them to your manufacturer.
Step 10: Choose Your PCB Manufacturer
Choosing the right PCB manufacturer is crucial for getting a high-quality PCB prototype at a low cost. Some factors to consider when choosing a PCB manufacturer include:
- Price
- Turnaround time
- Quality
- Customer service
- Capabilities (e.g. minimum trace width, hole size, etc.)
Some popular low-cost PCB manufacturers include:
Manufacturer | Capabilities | Lead Time | Price (10x10cm, 2 layer) |
---|---|---|---|
JLCPCB | 6/6mil trace/space, 0.3mm hole | 24 hours | $2 for 5 pcs |
PCBWay | 4/4mil trace/space, 0.2mm hole | 24 hours | $5 for 10 pcs |
ALLPCB | 3.5/3.5mil trace/space, 0.2mm hole | 48 hours | $9 for 10 pcs |
Step 11: Place Your PCB Order
Once you have chosen your PCB manufacturer, it’s time to place your PCB order. Most manufacturers have an online ordering system where you can upload your Gerber files and specify your PCB specifications (e.g. material, thickness, color, etc.). Make sure to double-check your order before submitting it.
Step 12: Assemble Your PCB
Once you receive your PCB from the manufacturer, it’s time to assemble your components. If you are assembling your PCB by hand, here are some tips:
- Use a soldering iron with a fine tip and adjustable temperature control
- Use flux to help the solder flow and prevent oxidation
- Start with the smallest components first (e.g. resistors, capacitors)
- Use tweezers to hold components in place while soldering
- Inspect each solder joint under a magnifying glass to ensure a good connection
If you have a complex design or a large number of PCBs to assemble, you may want to consider using a pick-and-place machine or outsourcing your assembly to a professional service.
Step 13: Test Your PCB
Once your PCB is assembled, it’s time to test it to ensure it functions as intended. Here are some testing methods you can use:
- Visual inspection: Check for any visible defects or missing components
- Continuity test: Use a multimeter to check for short circuits or open connections
- Functional test: Apply power to your PCB and test its functionality using a test fixture or oscilloscope
- Boundary scan test: Use JTAG or other boundary scan techniques to test for manufacturing defects
- In-circuit test: Use a bed-of-nails test fixture to test individual components and circuits
Testing your PCB thoroughly can help you catch any issues before finalizing your design.
Step 14: Iterate and Refine Your Design
Building a PCB prototype is an iterative process. Based on the results of your testing, you may need to make changes to your design and build a new prototype. Some common reasons for iteration include:
- Fixing design errors or oversights
- Optimizing performance or power consumption
- Reducing cost or complexity
- Adding new features or functionality
Don’t be afraid to iterate on your design until you achieve the desired results.
Frequently Asked Questions
1. What is the cheapest way to make a PCB prototype?
The cheapest way to make a PCB prototype is to use a low-cost PCB manufacturer like JLCPCB or PCBWay. These manufacturers offer prices as low as $2 for a 10x10cm 2-layer PCB.
2. Can I make a PCB prototype at home?
Yes, it is possible to make a PCB prototype at home using a variety of methods, including:
- Toner transfer method: Print your PCB design onto glossy paper using a laser printer, then iron it onto a copper-clad board and etch away the excess copper.
- Photoresist method: Apply a photosensitive film to a copper-clad board, expose it to UV light through a transparency of your PCB design, then develop and etch the board.
- CNC milling: Use a CNC machine to mill away the excess copper from a copper-clad board, leaving only your PCB traces.
However, these methods can be time-consuming and may not produce professional-quality results.
3. How long does it take to get a PCB prototype?
The turnaround time for a PCB prototype depends on the manufacturer and the complexity of your design. Some manufacturers offer 24-hour turnaround times for simple designs, while more complex designs may take several days or weeks.
4. What is the minimum order quantity for a PCB prototype?
The minimum order quantity for a PCB prototype varies by manufacturer, but is typically around 5-10 pieces. Some manufacturers may offer lower minimum quantities for an additional fee.
5. How much does it cost to assemble a PCB prototype?
The cost to assemble a PCB prototype depends on the complexity of your design and the number of components. Hand assembly can be done for free if you have the necessary tools and skills, but can be time-consuming for complex designs. Professional assembly services typically charge by the component, with prices ranging from a few cents to several dollars per component.
Conclusion
Building a PCB prototype is an essential step in the development of electronic devices, but it doesn’t have to be expensive or time-consuming. By following these 14 steps and using low-cost PCB manufacturers, you can build a high-quality PCB prototype at a fraction of the cost of traditional methods. Remember to iterate on your design until you achieve the desired results, and don’t be afraid to seek professional help if needed.
Leave a Reply