What is a PCB antipad?
A PCB (Printed Circuit Board) antipad, also known as a thermal relief or thermal isolation pad, is a design feature used in PCB manufacturing to improve the reliability and manufacturing process of the board. It is a small, non-conductive area around a hole or via that connects a component pin to a copper plane or trace on the PCB.
The primary purpose of an antipad is to reduce the thermal stress on the component pin during the soldering process. When a component is soldered to a large copper plane, the heat from the soldering iron can quickly dissipate through the copper, making it difficult to achieve a proper solder joint. By creating an antipad around the hole, the thermal connection between the pin and the copper plane is reduced, allowing the pin to reach the necessary temperature for a reliable solder joint.
Why Use PCB Antipads?
There are several reasons why PCB designers choose to incorporate antipads in their designs:
-
Improved Soldering Quality: Antipads help ensure that component pins reach the proper temperature during the soldering process, resulting in better solder joint formation and improved reliability of the PCB.
-
Reduced Thermal Stress: By limiting the heat transfer between the component pin and the copper plane, antipads help reduce thermal stress on the component, which can cause damage or premature failure.
-
Enhanced Manufacturing Process: Antipads make it easier for the soldering iron to heat the component pin to the required temperature, reducing the time and effort needed to create a proper solder joint. This can lead to faster production times and lower manufacturing costs.
-
Increased Current Capacity: In some cases, antipads can be used to increase the current-carrying capacity of a via by reducing the amount of copper connected to it. This can be particularly useful in high-current applications.
Designing PCB Antipads
When designing PCB antipads, there are several factors to consider to ensure optimal performance and reliability:
Antipad Size
The size of the antipad is a critical factor in its effectiveness. If the antipad is too small, it may not provide sufficient thermal isolation, while if it is too large, it can compromise the structural integrity of the PCB. The ideal antipad size depends on several factors, including the size of the component pin, the thickness of the PCB, and the desired level of thermal isolation.
A general rule of thumb is to make the antipad diameter approximately 20-50% larger than the diameter of the hole or via. For example, if the hole diameter is 0.5mm, the antipad diameter should be between 0.6mm and 0.75mm.
Hole Diameter (mm) | Recommended Antipad Diameter (mm) |
---|---|
0.3 | 0.36 – 0.45 |
0.5 | 0.6 – 0.75 |
0.8 | 0.96 – 1.2 |
1.0 | 1.2 – 1.5 |
Antipad Shape
The most common antipad shape is circular, as it provides uniform thermal isolation around the hole or via. However, in some cases, other shapes such as squares or rectangles may be used to accommodate specific design requirements or to increase the antipad’s effectiveness in certain directions.
Antipad Placement
Antipads should be placed around all holes and vias that connect component pins to copper planes or traces. In some cases, it may be necessary to place antipads around mounting holes or other non-component holes to maintain consistent thermal isolation across the PCB.
Thermal Spokes
In addition to antipads, thermal spokes (also known as thermal ties) can be used to further improve the thermal isolation of a component pin. Thermal spokes are thin copper traces that connect the antipad to the surrounding copper plane, providing a controlled path for heat dissipation. The number and width of thermal spokes can be adjusted to achieve the desired balance between thermal isolation and structural integrity.
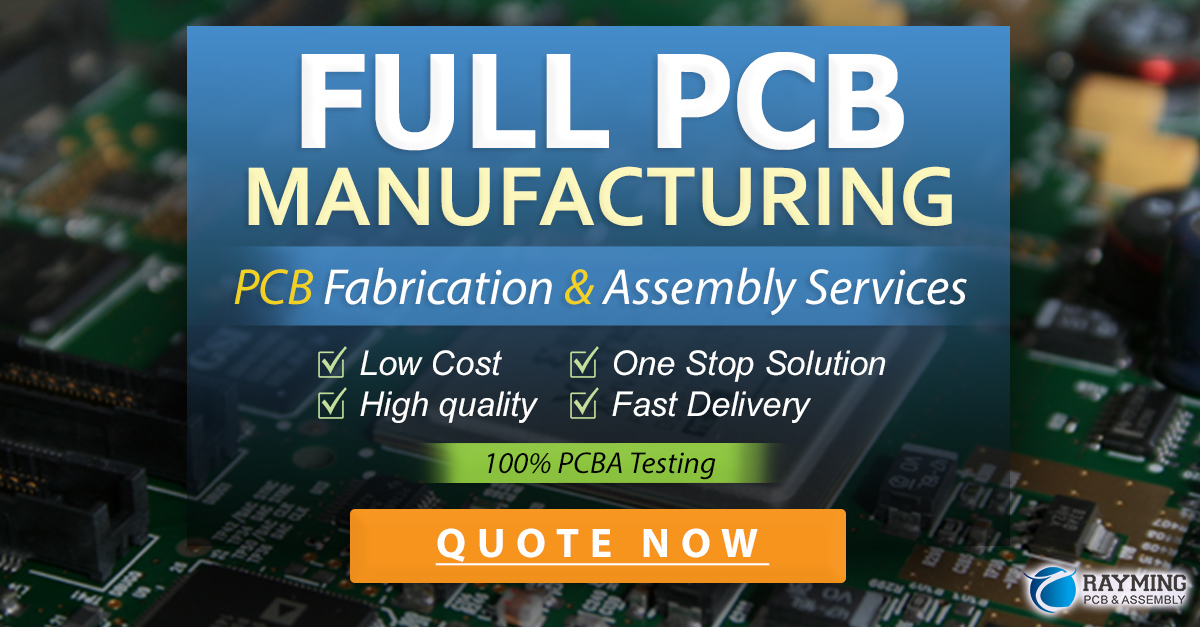
PCB Antipad Design Best Practices
To ensure optimal performance and reliability of your PCB design, consider the following best practices when incorporating antipads:
-
Use appropriate antipad sizes: Follow the recommended antipad size guidelines based on the hole or via diameter to ensure adequate thermal isolation without compromising the structural integrity of the PCB.
-
Maintain consistent antipad placement: Place antipads around all relevant holes and vias to ensure consistent thermal isolation across the PCB.
-
Consider thermal spoke usage: Use thermal spokes in conjunction with antipads to provide additional thermal isolation and control heat dissipation.
-
Evaluate the impact on signal integrity: In high-speed designs, antipads can affect signal integrity by altering the impedance of the signal path. Carefully evaluate the impact of antipads on signal integrity and make appropriate adjustments to the design if necessary.
-
Collaborate with your PCB manufacturer: Work closely with your PCB manufacturer to ensure that your antipad design is compatible with their manufacturing processes and design rules.
Frequently Asked Questions (FAQ)
-
What is the difference between an antipad and a thermal relief?
An antipad and a thermal relief are essentially the same things – a non-conductive area around a hole or via that provides thermal isolation. The terms are often used interchangeably. -
Do I need to use antipads in every PCB design?
While antipads are beneficial in many PCB designs, they may not be necessary for every application. In general, antipads are most useful in designs with large copper planes or high-current traces where thermal isolation is critical for reliable soldering and component performance. -
Can antipads be used for non-component holes, such as mounting holes?
Yes, antipads can be used around non-component holes to maintain consistent thermal isolation across the PCB. However, the decision to use antipads in these cases should be based on the specific requirements of the design. -
How do I determine the appropriate antipad size for my design?
The ideal antipad size depends on factors such as the hole or via diameter, PCB thickness, and desired thermal isolation level. As a general guideline, make the antipad diameter 20-50% larger than the hole diameter. Consult with your PCB manufacturer for specific recommendations based on your design requirements. -
Can antipads affect the signal integrity of my PCB design?
In high-speed designs, antipads can potentially impact signal integrity by altering the impedance of the signal path. It is essential to carefully evaluate the effect of antipads on signal integrity and make necessary adjustments to the design to ensure optimal performance.
Conclusion
PCB antipads are a valuable design feature that can improve the reliability and manufacturing process of your PCB by providing thermal isolation for component pins during soldering. By reducing thermal stress and enhancing solder joint formation, antipads contribute to the overall quality and longevity of your PCB.
When incorporating antipads into your PCB design, consider factors such as antipad size, shape, placement, and the use of thermal spokes. Follow best practices and collaborate closely with your PCB manufacturer to ensure that your antipad design is optimized for your specific application and manufacturing process.
While antipads may not be necessary for every PCB design, they are a powerful tool in the designer’s arsenal for creating reliable, high-performance electronic products.
Leave a Reply