Finalize and Test Your Breadboard Prototype
Before starting the process of creating a PCB version of your project, make sure your breadboard prototype is fully complete, tested, and working as intended. Iron out any remaining bugs and validate that it meets all of your design requirements and specifications.
Key Points for Finalizing Your Prototype
- Double-check all wiring and connections
- Perform thorough testing of all features and functions
- Optimize component selection if needed (e.g. for cost, size, availability)
- Consider power requirements and battery life
- Incorporate any final design tweaks or improvements
Create a Schematic Diagram
The first step in moving to a PCB is converting your physical breadboard layout into a schematic diagram. A schematic is a symbolic representation that shows how all the components in your circuit are connected electrically.
Schematic Creation Process
- Select an electronics CAD software package (e.g. Eagle, KiCad, Altium)
- Place component symbols and assign values/ratings
- Make connections between components with wires or nets
- Add power and ground symbols
- Annotate components with reference designators
- Perform an electrical rules check (ERC) to detect errors
Design the PCB Layout
With a completed schematic, you’re ready to create the physical PCB layout. The PCB layout determines the size and shape of the board and where all the components and traces will be placed.
PCB Layout Process
- Set up design rules (e.g. trace widths, clearances, hole sizes)
- Place component footprints based on schematic
- Define board shape and dimensions
- Route traces to make connections between components
- Add copper pours for power/ground planes if needed
- Place mounting holes and any additional holes
- Run a design rules check (DRC) to verify manufacturability
Some general tips for PCB layout:
– Minimize trace lengths and avoid sharp angles
– Provide proper grounding and power distribution
– Consider signal integrity and EMI for sensitive circuits
– Leave room for connectors, switches, indicators etc.
– Keep components on a 0.1″ grid for easier soldering
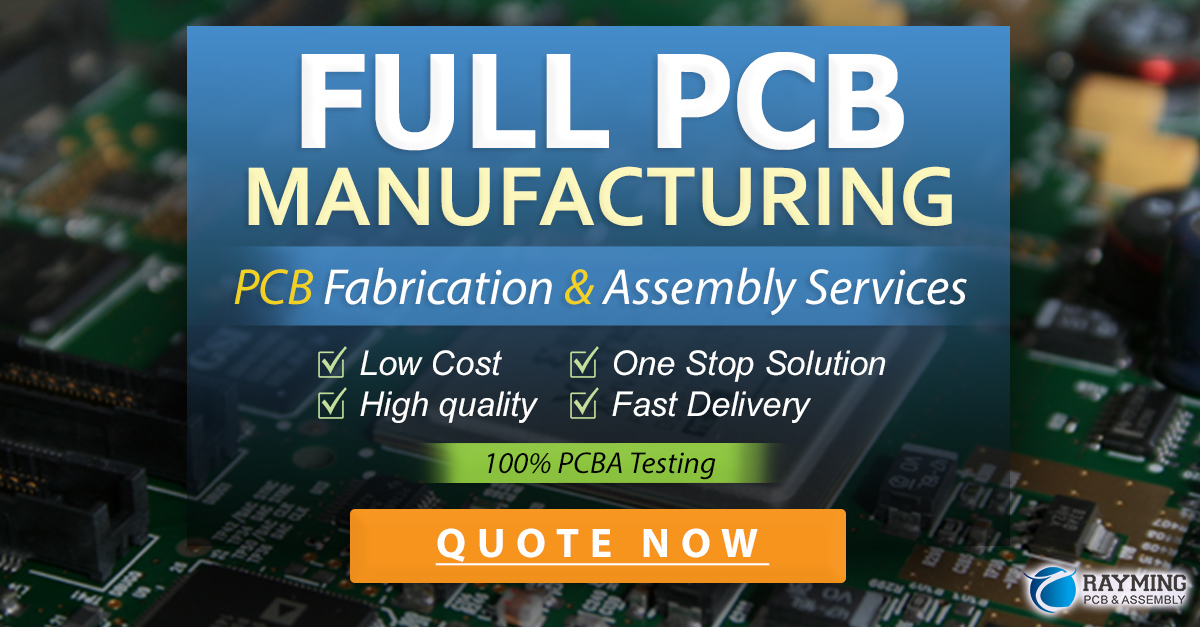
Generate Gerber and Drill Files
Once your PCB layout is finalized, you need to generate the manufacturing files that a PCB fabrication shop will use to actually produce the physical boards. The industry standard formats are Gerber files for the copper layers/masks and NC drill files for holes.
Manufacturing File Generation Steps
- Double-check layouts and run a final DRC in your CAD tool
- Select layers/settings for Gerber file generation
- Select drill file type (e.g. Excellon) and hole sizes
- Generate Gerber and drill files
- Carefully inspect Gerber/drill previews for errors
- Zip up files, name clearly, and send to PCB fab
Typical Gerber files for a 2-layer PCB:
| Filename | Layer |
|———-|——-|
| .GTL | Top copper |
| .GBL | Bottom copper |
| .GTS | Top soldermask |
| .GBS | Bottom soldermask |
| .GTO | Top silkscreen |
| .GBO | Bottom silkscreen |
| .TXT | NC drills |
Find a PCB Manufacturer
With manufacturing files ready, you need to find a PCB shop to actually fabricate your boards. There are many options ranging from quick-turn prototyping houses to large-scale offshore manufacturers.
What to Look for in a PCB Manufacturer
- Capabilities that match your design (# layers, materials, tolerances, etc)
- Reliable quality and good reviews/references
- Reasonable cost and turnaround time
- Good communication and support
- Certifications (e.g. ISO 9001, UL, IPC)
Some well-known PCB Prototype services:
– OSH Park
– Seeed Studio
– PCBWay
– JLCPCB
– PCB123
For higher volumes, research offshore manufacturers (e.g. China) or local shops. Always get multiple quotes and ask for references before committing to a supplier.
Assemble Your First Articles
After receiving your fabricated bare PCBs from the manufacturer, it’s time to assemble your first complete boards. This involves soldering all the components in place.
PCB Assembly Options
- Hand soldering
- Lowest cost, practical for small quantities
- Requires proper tools and technique
- Can be tedious and time-consuming
- Reflow soldering
- Applies solder paste and uses oven to melt
- Works well for surface mount parts
- Requires solder paste, stencil, reflow oven
- Professional assembly
- Outsource to an assembly shop
- Often uses pick-and-place machines and reflow
- Good for large quantities or complex boards
- More expensive than DIY
For prototypes, hand soldering is often sufficient. Use a temperature-controlled iron, fine solder, and practice good technique. Work carefully to avoid bridging pins or damaging components.
Test and Debug Assembled Boards
With your first PCBs fully assembled, it’s critical to thoroughly test them to ensure everything is working properly. Debug any issues that arise.
PCB Testing and Debugging Process
- Visual inspection
- Check for good solder joints, component placement
- Look for shorts, cold joints, missing/damaged parts
- Power up carefully
- Use current-limited supply if possible
- Check for shorts or excessive power draw
- Test basic functionality
- Verify expected voltages at key points
- Check major ICs for proper power-on conditions
- Test full functionality
- Validate all features and functions per your design
- Compare to known-good breadboard prototype
- Debug problems
- Isolate issues to a particular section or component
- Check solder connections, replace suspicious parts
- Use multimeter and oscilloscope to pinpoint faults
Debugging tips:
– Check connectors and cabling carefully
– Use ESD-safe tools and workstation
– Check datasheets and schematics
– Desolder and test suspicious parts separately
– Consider design mods to fix unforeseen issues
Refine Design and Order Subsequent Revisions
Based on what you learn from testing your first assembled boards, you’ll likely need to make some design tweaks and order subsequent PCB revisions before you arrive at a perfect, production-ready product.
Design Refinement Process
- Implement fixes for any bugs/flaws found in testing
- Make improvements based on real-world usage/feedback
- Optimize layout for manufacturing or assembly
- Consider design for test (DFT) features if needed
- Update schematic and regenerate fresh PCB layout
- Re-run DRCs and generate new manufacturing files
- Order next revision of boards and repeat cycle
This iterative process of refining, rebuilding, and retesting ultimately leads you to a solid, reliable product ready to be manufactured in volume.
Ramp up to Production
After you’ve dialed in your proven, tested PCB design, you’re finally ready to scale up to volume production. This involves working closely with your manufacturer and assembler.
Preparation for Production
- Finalize all documentation (drawings, BOMs, test procedures, etc)
- Conduct a design for manufacturability (DFM) review with suppliers
- Define quality assurance and acceptance test plans
- Create assembly instructions, jigs, and fixtures
- Set up supply chain and production scheduling
- Consider regulatory certifications (FCC, CE, UL, etc)
- Plan for packaging and fulfillment
Working closely with experienced manufacturing partners is key to a smooth transition into production. Communicate clearly, plan ahead, and stay directly involved to ensure a successful ramp-up.
Frequently Asked Questions (FAQ)
What if my PCB doesn’t work after assembly?
First, thoroughly inspect the assembled board for visible defects, starting with solder connections. Check voltages to make sure power is good. Work methodically to isolate the problem to a particular subsystem then dig further with an oscilloscope and multimeter. Check component orientations and values carefully against the schematic. Consider that the PCB design itself may be flawed and need rework.
How much does it cost to have PCBs made?
Prototype PCBs from quick-turn shops typically cost around $1-10 per square inch, depending on quantity, number of layers, turnaround time etc. Small quantity assembly can add $30-100 per board. Volume production is much cheaper per unit but has higher setup/NRE Costs. Get quotes from multiple suppliers to compare.
What if I need to change my design after ordering PCBs?
Small changes can sometimes be made by cutting traces and adding jumper wires. For more substantial changes, you’ll have to respin the PCB layout and order new boards. Try to avoid changes by thoroughly testing your breadboard prototype. Consider contingencies and build in flexibility where possible.
How do I source components for production?
For prototypes, you can usually buy from catalog distributors (e.g. DigiKey, Mouser). For production, establish direct relationships with manufacturers or larger distributors. Avoid single-sourcing critical components. Consider long-lead time parts and plan for alternates if needed.
What regulations/certifications should I consider?
Depending on your product and where it will be sold, you may need certain certifications:
– FCC (EMI/EMC) for products with electronics
– UL or CE for safety, especially AC-powered devices
– Bluetooth/WiFi alliance certification for wireless products
– Environmental compliance (RoHS, REACH, etc)
Research what’s applicable to your product and plan testing/certification well in advance. Consult with an expert if needed.
Making the journey from breadboard to product is challenging but immensely rewarding. Following a systematic process, working with experienced partners, and paying attention to details will help ensure your success. As you gain experience with each product, you’ll hone your design and production skills. Good luck turning your concepts into reality!
Leave a Reply