Understanding PCB Thickness
PCB thickness is typically measured in either millimeters (mm) or thousandths of an inch (mils). One mil equals 0.001 inch or 0.0254 mm. The thickness of a PCB is determined by the combined thickness of the copper layers, substrate material, and any additional layers such as solder mask or silkscreen.
Common PCB Thickness Standards
There are several standard thicknesses for PCBs, which have been established by industry organizations such as the Institute for Interconnecting and Packaging Electronic Circuits (IPC). The most common PCB thicknesses are:
Thickness (mm) | Thickness (mils) | Layers | Application |
---|---|---|---|
0.4 | 15.75 | 1-2 | Very thin, flexible PCBs |
0.6 | 23.62 | 1-2 | Thin, flexible PCBs |
0.8 | 31.50 | 1-2 | Rigid-flex PCBs |
1.0 | 39.37 | 1-2 | Rigid PCBs |
1.2 | 47.24 | 2-4 | Rigid PCBs |
1.6 | 62.99 | 4-8 | Rigid PCBs, most common |
2.0 | 78.74 | 8-12 | Thick, Multilayer PCBs |
2.4 | 94.49 | 12-16 | Very thick, multilayer PCBs |
3.2 | 125.98 | 16+ | Extremely thick, multilayer PCBs |
Factors Influencing PCB Thickness Choice
Several factors must be considered when selecting the appropriate PCB thickness for a given application. These include:
1. Number of Layers
The number of layers in a PCB directly impacts its thickness. As the layer count increases, so does the overall thickness of the board. For example, a 2-layer PCB might be 1.0 mm thick, while an 8-layer board could be 1.6 mm or thicker.
2. Mechanical Strength
Thicker PCBs offer greater mechanical strength and rigidity, making them more suitable for applications that require durability or resistance to vibration and impact. Thinner PCBs, on the other hand, are more flexible and better suited for applications that require bending or folding.
3. Electrical Performance
PCB thickness can also affect electrical performance. Thinner boards may be more susceptible to signal integrity issues, such as crosstalk and electromagnetic interference (EMI), due to the closer proximity of traces. Thicker boards offer better insulation between layers and can help mitigate these issues.
4. Manufacturing Constraints
The chosen PCB thickness must be compatible with the manufacturing capabilities of the PCB fabricator. Some manufacturers may have limitations on the minimum or maximum thickness they can produce, as well as the available layer counts and material options.
PCB Thickness and Manufacturing Considerations
When designing a PCB, it is crucial to consider the manufacturing implications of the chosen thickness. These considerations include:
Drilling and Plating
Thicker PCBs require longer drill bits and more time to drill through-holes. This can increase manufacturing costs and lead times. Additionally, thicker boards may require special attention during the plating process to ensure even copper distribution in the holes.
Lamination and Pressing
The lamination and pressing processes used to bond the layers of a PCB together can be affected by the board’s thickness. Thicker boards may require higher pressures and longer pressing times to ensure proper adhesion between layers.
Etching and Soldering
PCB thickness can also impact the etching and soldering processes. Thinner boards may be more susceptible to over-etching, leading to narrower traces and potential signal integrity issues. Thicker boards may require additional time for etching and soldering to ensure proper connections.
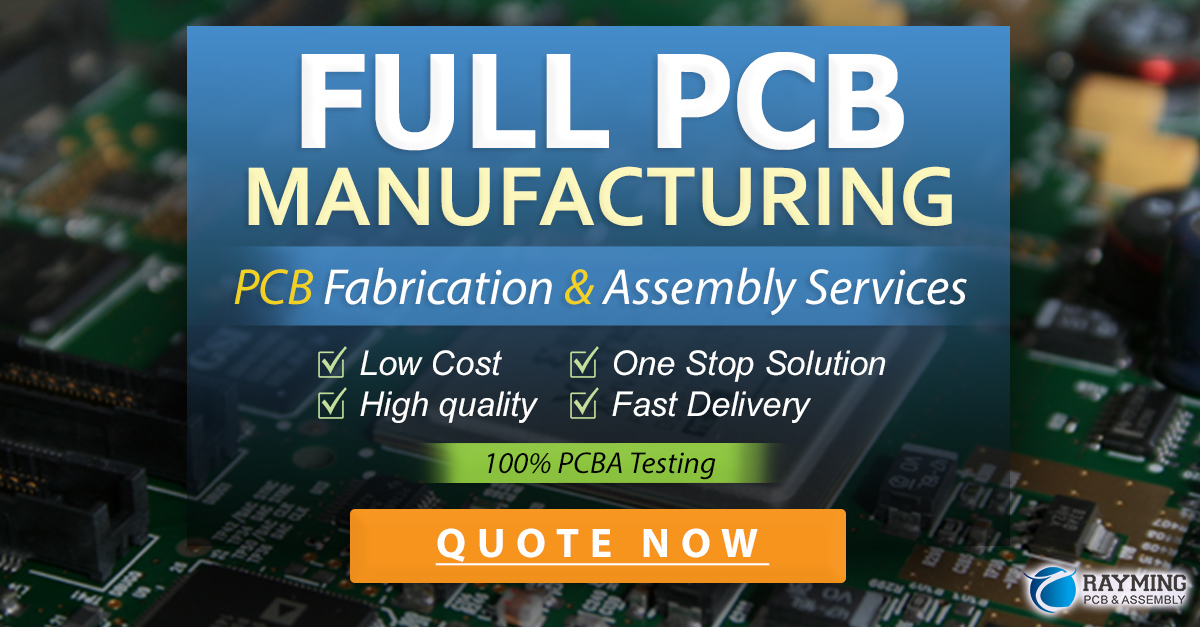
Choosing the Right PCB Thickness
Selecting the appropriate PCB thickness for a given application involves balancing various factors, including:
- Electrical requirements
- Mechanical requirements
- Manufacturing capabilities
- Cost considerations
By carefully evaluating these factors and consulting with experienced PCB design and manufacturing professionals, engineers can choose the optimal PCB thickness for their projects.
PCB Thickness Standards and Certifications
Several industry organizations have established standards and certifications related to PCB thickness and manufacturing quality. These include:
IPC Standards
The IPC (formerly known as the Institute for Interconnecting and Packaging Electronic Circuits) is a global trade association that develops standards for the electronic interconnection industry. Some key IPC standards related to PCB thickness include:
- IPC-2221: Generic Standard on Printed Board Design
- IPC-6012: Qualification and Performance Specification for Rigid Printed Boards
- IPC-6013: Qualification and Performance Specification for Flexible Printed Boards
UL Certifications
Underwriters Laboratories (UL) is a global safety certification company that provides testing and certification services for electronic products. PCBs that meet UL standards for thickness, material selection, and manufacturing quality can earn UL certification, which is often required for products sold in certain markets.
Advanced PCB Thickness Techniques
As electronic devices continue to shrink in size and increase in complexity, PCB designers and manufacturers are exploring advanced techniques to optimize board thickness and performance. Some of these techniques include:
High Density Interconnect (HDI) PCBs
HDI PCBs feature finer trace widths and smaller via sizes, allowing for higher component density and reduced board size. These boards often use thinner substrates and specialized manufacturing processes to achieve their compact dimensions.
Embedded Components
Embedding components, such as resistors and capacitors, within the layers of a PCB can help reduce board size and thickness. This technique requires careful design and specialized manufacturing processes, but can result in significant space savings and improved electrical performance.
3D PCBs
3D PCBs, also known as molded interconnect devices (MIDs), are designed to conform to three-dimensional shapes. These boards can be formed using injection molding or 3D printing techniques, and can help reduce the overall size and thickness of electronic assemblies.
FAQ
1. What is the most common PCB thickness?
The most common PCB thickness is 1.6 mm (62.99 mils), which is often used for 4 to 8-layer boards in a wide range of applications.
2. Can I use a thinner PCB to save cost?
While thinner PCBs may be less expensive in terms of material costs, they may not always be the most cost-effective solution. Thinner boards may require more specialized manufacturing processes, longer production times, and may be more susceptible to damage or signal integrity issues. It is essential to consider the total cost of ownership when selecting a PCB thickness.
3. How does PCB thickness affect signal integrity?
PCB thickness can affect signal integrity in several ways. Thinner boards may be more susceptible to crosstalk and EMI due to the closer proximity of traces. Thicker boards offer better insulation between layers and can help mitigate these issues. However, thicker boards may also introduce challenges related to impedance control and signal timing.
4. Can I mix different thicknesses on the same PCB?
Yes, it is possible to design a PCB with varying thicknesses in different areas of the board. This is often done in rigid-flex PCB designs, where certain sections of the board are made thinner to allow for bending or folding. However, designing and manufacturing PCBs with mixed thicknesses can be more complex and costly compared to using a uniform thickness throughout.
5. How do I choose the right PCB thickness for my project?
Choosing the right PCB thickness involves careful consideration of your project’s electrical, mechanical, and manufacturing requirements. Factors to consider include the number of layers needed, the desired mechanical strength and flexibility, signal integrity concerns, and the capabilities of your chosen PCB manufacturer. It is recommended to consult with experienced PCB design and manufacturing professionals to help select the optimal thickness for your specific application.
Conclusion
PCB thickness is a critical parameter that can significantly impact the performance, reliability, and cost of electronic devices. By understanding the various PCB thickness standards, factors influencing thickness choice, and manufacturing considerations, engineers can make informed decisions when designing and producing PCBs for their projects.
As the electronics industry continues to evolve, advanced techniques such as HDI PCBs, embedded components, and 3D PCBs are pushing the boundaries of what is possible with PCB thickness optimization. By staying up-to-date with these developments and working closely with experienced PCB professionals, designers can create innovative, high-performance electronic products that meet the ever-increasing demands of the market.
Leave a Reply