Why PCB Design Rules Matter for Data Integrity
Printed Circuit Board (PCB) design is a complex process that requires careful planning and attention to detail. One of the most critical aspects of PCB design is ensuring data integrity – making sure that the signals transmitted through the PCB are accurate, reliable, and free from interference or distortion.
Failing to follow proper PCB design rules can lead to a host of issues that can compromise data integrity, such as:
- Signal integrity problems (crosstalk, reflections, ground bounce, etc.)
- Electromagnetic Interference (EMI)
- Manufacturability and reliability issues
- Increased design and production costs
- Delays in time-to-market
To avoid these pitfalls and ensure optimal data integrity in your PCB designs, it’s essential to adhere to a set of best practices and design rules. In this article, we’ll dive into 10 key PCB design rules that will help you achieve better data and avoid common design issues.
Rule 1: Choose the Right PCB Material
The choice of PCB material can have a significant impact on signal integrity and EMI performance. The key properties to consider are:
- Dielectric constant (Dk): Affects the speed of signals through the PCB. Lower Dk means faster signal propagation.
- Dissipation factor (Df): Measures the amount of signal loss in the material. Lower Df means less signal attenuation.
- Thermal conductivity: Ability to dissipate heat. Higher conductivity is better for high-power designs.
Here’s a comparison of some common PCB materials:
Material | Dk | Df | Thermal Conductivity (W/mK) |
---|---|---|---|
FR-4 | 4.5 | 0.02 | 0.3 |
Rogers 4350B | 3.48 | 0.0037 | 0.62 |
PTFE (Teflon) | 2.1 | 0.0002 | 0.25 |
Polyimide | 3.5 | 0.002 | 0.12 |
For high-speed digital designs, materials like Rogers 4350B or Isola I-Speed are often preferred due to their lower Dk and Df values. For high-power applications, Metal Core PCBs (MCPCB) with high thermal conductivity may be necessary.
Rule 2: Use Proper Trace Widths and Spacing
The width and spacing of PCB traces can affect signal integrity, crosstalk, and EMI. Here are some guidelines to follow:
- Use wider traces for power and ground to minimize resistance and inductance.
- Use narrower traces for high-speed signals to minimize capacitance and maintain characteristic impedance.
- Maintain adequate spacing between traces to minimize crosstalk. The higher the signal frequency, the greater the spacing required.
- Follow your PCB manufacturer’s minimum trace width and spacing guidelines to ensure manufacturability.
Here’s an example table of recommended trace widths for different current levels:
Current (A) | Trace Width (mm) |
---|---|
0.1 | 0.15 |
0.5 | 0.3 |
1 | 0.6 |
2 | 1.0 |
4 | 2.0 |
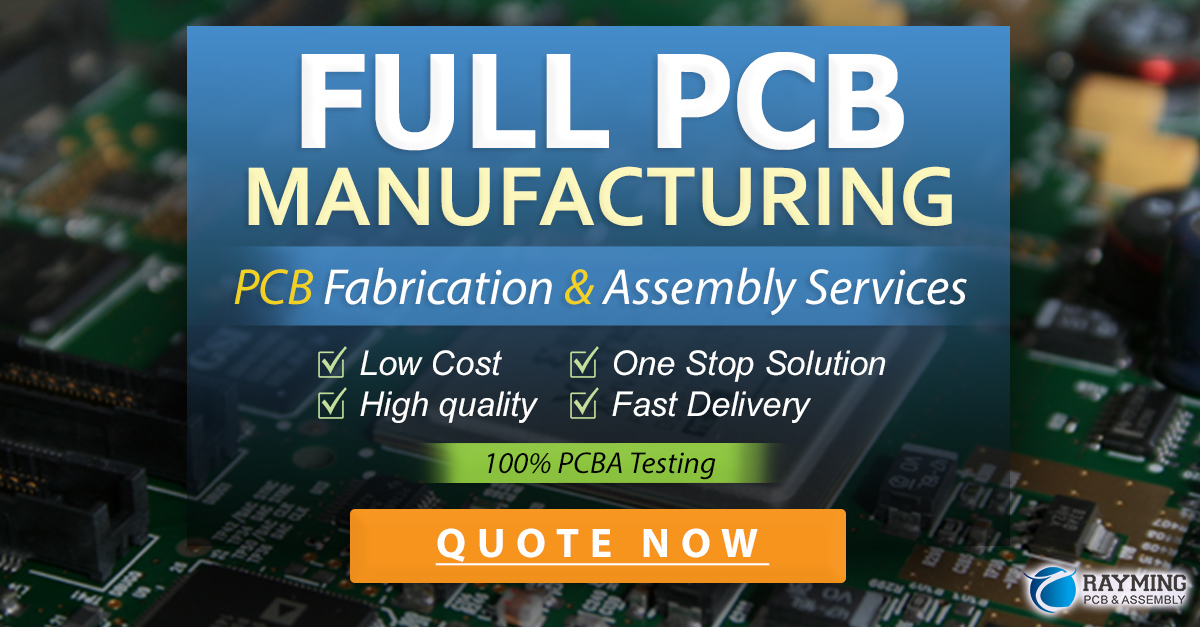
Rule 3: Maintain Proper Impedance Control
Maintaining proper characteristic impedance of PCB traces is crucial for minimizing signal reflections and ensuring signal integrity. The two main types of PCB Transmission Lines are:
- Microstrip: Trace on top or bottom layer, with a reference plane on the adjacent layer.
- Stripline: Trace embedded between two reference planes.
To control impedance, you need to consider factors such as:
- Trace width and thickness
- Dielectric thickness
- Dielectric constant of PCB material
You can use online calculators or PCB design software to determine the required trace dimensions for your desired impedance. Common impedance values are 50Ω for single-ended signals and 90-120Ω for differential pairs.
Rule 4: Use Ground and Power Planes
Proper grounding and power distribution are essential for minimizing EMI and ensuring signal integrity. Some best practices include:
- Use solid ground and power planes instead of traces whenever possible.
- Provide separate ground and power planes for analog and digital circuitry to minimize crosstalk.
- Use a star grounding topology to minimize ground loops and provide a low-impedance return path.
- Decouple power supplies with adequate capacitance to minimize noise and ripple.
Rule 5: Minimize Vias and Layer Changes
Vias and layer changes can cause signal integrity issues such as reflections, impedance mismatches, and crosstalk. To minimize these issues:
- Use blind and buried vias instead of through-hole vias when possible to minimize stub effects.
- Avoid changing layers for high-speed signals whenever possible.
- If layer changes are necessary, use via stitching to minimize impedance discontinuities.
- Keep high-speed signals on outer layers to minimize the number of vias required.
Rule 6: Route Differential Pairs Carefully
Differential signaling is commonly used for high-speed interfaces like USB, PCIe, and Ethernet. To maintain signal integrity in differential pairs:
- Route differential pairs closely together to minimize inductive coupling.
- Maintain constant spacing between the traces to maintain differential impedance.
- Avoid splitting differential pairs around obstacles or vias.
- Use length matching to ensure that both traces in a pair have equal length.
Rule 7: Follow High-Speed Routing Best Practices
When routing high-speed signals (>100 MHz), additional precautions are necessary to maintain signal integrity:
- Avoid sharp corners or bends in traces, which can cause reflections. Use 45° or curved bends instead.
- Minimize parallel runs of high-speed traces to reduce crosstalk.
- Avoid routing high-speed traces near board edges, which can cause EMI.
- Use AC coupling and termination resistors to minimize reflections and ringing.
Rule 8: Minimize Crosstalk and EMI
Crosstalk and EMI can cause signal integrity issues and violate regulatory requirements. To minimize these issues:
- Separate high-speed and low-speed signals on different layers.
- Provide adequate spacing between high-speed traces and other signals.
- Use guard traces or ground shields around sensitive signals.
- Minimize the loop area of high-current traces to reduce EMI.
- Use EMI filters and shielding when necessary.
Rule 9: Optimize Component Placement
Proper component placement can help minimize signal integrity issues and improve manufacturability:
- Place decoupling capacitors as close as possible to ICs to minimize power supply noise.
- Minimize the distance between high-speed components to reduce trace lengths and signal delays.
- Group components with similar functions together to simplify routing and minimize crosstalk.
- Orient components to minimize the number of vias and layer changes required.
- Follow component manufacturer’s placement recommendations, such as pad sizes and thermal relief.
Rule 10: Verify Your Design with Simulations and Testing
Even if you follow all the above design rules, it’s still essential to verify your PCB design before manufacturing:
- Use signal integrity simulations to verify impedance control, crosstalk, and EMI.
- Use 3D modeling to check for mechanical clearance and thermal issues.
- Perform design rule checks (DRC) to ensure that your design meets manufacturability requirements.
- Build prototypes and perform thorough testing to validate performance and reliability.
By following these PCB design rules and best practices, you can ensure optimal data integrity and avoid costly design issues and delays.
FAQ
Q1: What is the most important PCB design rule for ensuring data integrity?
A1: While all the design rules discussed are important, one of the most critical is maintaining proper impedance control (Rule 3). Impedance mismatches can cause reflections, ringing, and other signal integrity issues that can severely degrade data quality.
Q2: Can I use autorouting for high-speed PCB designs?
A2: While autorouting can be useful for simpler designs, it’s generally not recommended for high-speed designs. Manual routing allows for greater control over trace geometry, spacing, and layer changes, which are critical for maintaining signal integrity.
Q3: What should I do if I can’t avoid splitting a differential pair around an obstacle?
A3: If you must split a differential pair, try to keep the split as short as possible and maintain equal lengths for both traces. You can also use stitching vias to minimize impedance discontinuities.
Q4: How can I minimize EMI in my PCB design?
A4: There are several strategies for minimizing EMI, such as separating high-speed and low-speed signals, minimizing loop areas, using guard traces or ground shields, and applying EMI filters or shielding when necessary. Following good layout practices and keeping current return paths short are also important.
Q5: What’s the best way to verify my PCB design before manufacturing?
A5: A combination of simulation and thorough testing is the best approach. Use signal integrity simulations to verify impedance control and check for issues like crosstalk and EMI. Perform design rule checks to ensure manufacturability. Build prototypes and test them thoroughly to validate performance and reliability. Catching issues early in the design phase can save significant time and cost compared to fixing problems after manufacturing.
Leave a Reply