What is a PCB Transmission Line?
A PCB transmission line is a copper trace or set of traces on a printed circuit board (PCB) that is designed to carry high-frequency electrical signals between components. It serves as the interconnection between transmitters, such as a microprocessor or FPGA, and receivers, like memory chips or I/O interfaces, enabling communication within the PCB.
Transmission lines play a crucial role in maintaining signal integrity and ensuring reliable data transfer in high-speed digital systems. As signal frequencies increase and rise times decrease, the behavior of the interconnects becomes more critical. At high frequencies, PCB traces no longer behave as simple electrical connections but rather as transmission lines that exhibit wave propagation properties.
Types of PCB Transmission Lines
There are several types of transmission lines commonly used in PCB design, each with its own characteristics and applications. The choice of transmission line depends on factors such as the desired impedance, signal frequency, available space, and manufacturing capabilities. The most common types include:
- Microstrip:
- Consists of a single conductor trace on the top layer of the PCB, with a ground plane on the bottom layer.
- Widely used due to its simplicity and ease of manufacturing.
-
Suitable for low to medium frequencies and short to medium trace lengths.
-
Stripline:
- Consists of a single conductor trace embedded between two ground planes.
- Provides better shielding and isolation compared to microstrip.
-
Suitable for high-frequency signals and longer trace lengths.
-
Coplanar Waveguide (CPW):
- Consists of a single conductor trace with ground planes on either side on the same layer.
- Offers good isolation and low cross-talk.
-
Suitable for high-frequency signals and applications requiring tight impedance control.
-
Differential Pairs:
- Consists of two closely spaced conductor traces with equal and opposite signals.
- Provides excellent noise immunity and reduces electromagnetic interference (EMI).
- Commonly used for high-speed differential signaling, such as USB, HDMI, and PCIe.
Characteristics of PCB Transmission Lines
To ensure proper signal propagation and maintain signal integrity, PCB transmission lines must be designed with careful consideration of several key characteristics:
Impedance
Impedance is a critical parameter in transmission line design. It represents the opposition to the flow of high-frequency signals along the transmission line. The characteristic impedance of a transmission line is determined by its geometry, dielectric material properties, and the frequency of the signal.
The most common characteristic impedances used in PCB design are 50 ohms and 100 ohms. Matching the impedance of the transmission line to the impedance of the source and load is essential to minimize reflections and ensure optimal signal transfer.
Impedance (Ω) | Application |
---|---|
50 | RF systems, coaxial cables, microstrip lines |
100 | Differential signaling, Ethernet, USB |
Propagation Delay
Propagation delay refers to the time it takes for a signal to travel from one end of the transmission line to the other. It is determined by the dielectric constant of the PCB material and the length of the transmission line.
Minimizing propagation delay is important to ensure synchronization and avoid timing issues in high-speed systems. Techniques such as using low-loss dielectric materials, minimizing trace lengths, and employing delay-matching strategies can help reduce propagation delay.
Reflection and Termination
When a signal encounters a change in impedance along the transmission line, a portion of the signal is reflected back towards the source. Reflections can cause signal distortion, ringing, and other signal integrity issues.
To mitigate reflections, proper termination techniques must be applied at the ends of the transmission line. Termination involves matching the impedance of the transmission line to the impedance of the source or load, effectively absorbing the reflected energy.
Common termination techniques include:
- Series termination: A resistor is placed in series with the signal source to match the impedance of the transmission line.
- Parallel termination: A resistor is placed in parallel with the load to match the impedance of the transmission line.
- AC termination: A combination of resistors and capacitors is used to provide frequency-dependent termination.
Cross-talk
Cross-talk occurs when signals from one transmission line couple into adjacent transmission lines through electromagnetic coupling. It can lead to signal integrity issues and cause interference between signals.
To minimize cross-talk, several techniques can be employed:
- Increasing the spacing between adjacent transmission lines.
- Using ground planes or guard traces to provide shielding.
- Employing differential signaling, which cancels out common-mode noise.
- Optimizing the routing and placement of transmission lines to avoid parallel runs.
PCB Transmission Line Design Considerations
Designing PCB transmission lines requires careful consideration of various factors to ensure optimal signal integrity and reliable communication. Some key design considerations include:
Material Selection
The choice of PCB material plays a significant role in transmission line performance. The dielectric constant (Dk) and dissipation factor (Df) of the material affect the impedance, propagation delay, and loss characteristics of the transmission line.
Common PCB materials used for high-speed applications include:
- FR-4: A widely used, cost-effective material with moderate performance.
- Rogers: High-performance materials with low loss and stable dielectric properties.
- Isola: Offers a range of materials with varying dielectric constants and low loss.
Trace Geometry
The geometry of the transmission line, including its width, thickness, and spacing, determines its characteristic impedance and propagation properties. Wider traces have lower impedance, while narrower traces have higher impedance.
The thickness of the copper trace also affects the impedance and current-carrying capacity. Thicker traces have lower resistance and can handle higher currents, but they may increase manufacturing costs.
Spacing between traces should be carefully considered to minimize cross-talk and maintain signal integrity. Adequate spacing helps reduce electromagnetic coupling and improves isolation.
Length Matching
In high-speed systems, it is often necessary to match the lengths of transmission lines to ensure synchronized arrival of signals at the receivers. Length matching helps prevent timing skew and maintains signal integrity.
Techniques for length matching include:
- Serpentine routing: Adding meandering or zigzag patterns to the traces to equalize lengths.
- Delay lines: Using intentional delay elements, such as small sections of transmission lines, to adjust timing.
- Trace routing: Carefully planning the routing of traces to minimize length differences.
Vias and Connectors
Vias and connectors introduce discontinuities in the transmission line and can affect signal integrity. Proper design and placement of vias and connectors are crucial to minimize reflections and maintain impedance matching.
Techniques for optimizing via and connector design include:
- Via stitching: Adding additional vias around signal vias to provide a low-impedance return path.
- Via shielding: Surrounding signal vias with ground vias to reduce cross-talk and improve shielding.
- Connector selection: Choosing connectors with impedance-matched designs and minimal discontinuities.
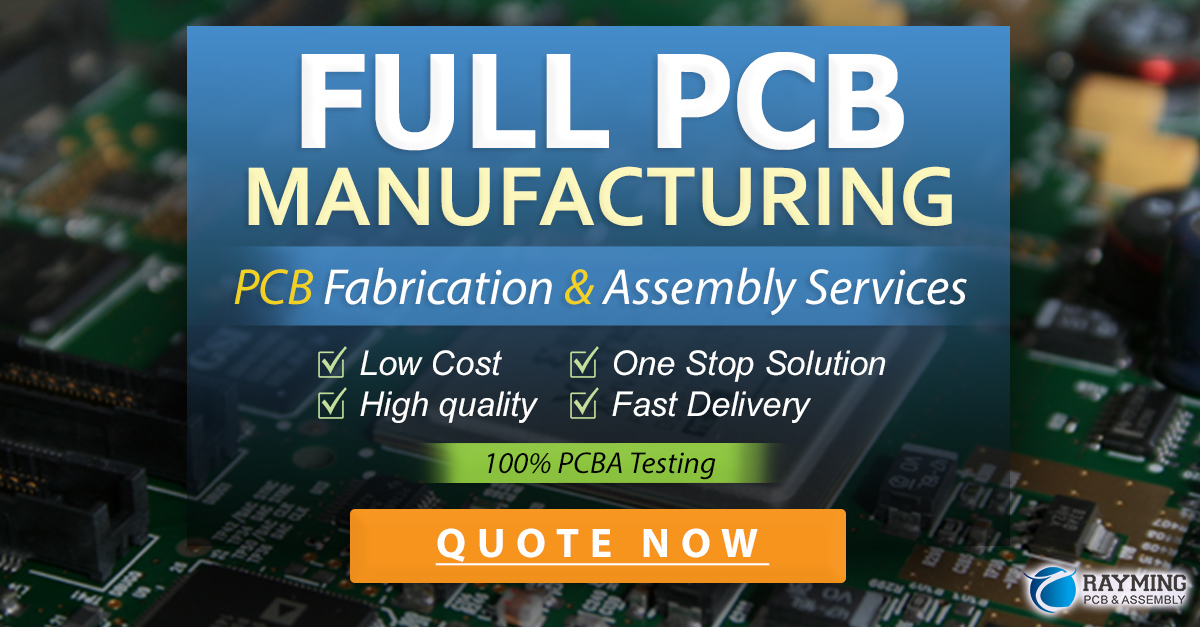
PCB Transmission Line Simulation and Analysis
To ensure the reliability and performance of PCB transmission lines, simulation and analysis tools are widely used in the design process. These tools help engineers predict and optimize the behavior of transmission lines before manufacturing the PCB.
Simulation Tools
There are several industry-standard simulation tools available for PCB transmission line analysis, including:
- ANSYS HFSS: A high-frequency electromagnetic field simulation tool for analyzing 3D structures.
- Cadence Allegro: A comprehensive PCB design and analysis tool with integrated signal integrity simulation capabilities.
- Mentor Graphics HyperLynx: A signal integrity simulation tool for analyzing high-speed PCB designs.
These tools allow engineers to model and simulate transmission lines, including their geometry, material properties, and termination schemes. They provide insights into impedance, propagation delay, reflections, and cross-talk, enabling designers to optimize the PCB layout and ensure robust signal integrity.
Analysis Techniques
Several analysis techniques are employed to evaluate the performance of PCB transmission lines:
- Time-Domain Analysis:
- Evaluates the signal waveforms and timing characteristics of the transmission line.
-
Helps identify issues such as signal distortion, overshoot, and ringing.
-
Frequency-Domain Analysis:
- Examines the frequency response of the transmission line.
-
Helps evaluate the insertion loss, return loss, and bandwidth of the transmission line.
-
Eye Diagram Analysis:
- Overlays multiple signal waveforms to create an “eye” pattern.
-
Provides insights into signal integrity, jitter, and bit error rate.
-
S-Parameter Analysis:
- Characterizes the transmission line as a two-port network.
- Helps evaluate the impedance matching, insertion loss, and return loss of the transmission line.
By employing these analysis techniques, engineers can identify potential issues, optimize the design, and ensure the transmission lines meet the required performance specifications.
Frequently Asked Questions (FAQ)
- What is the difference between a microstrip and a stripline transmission line?
- A microstrip transmission line consists of a single conductor trace on the top layer of the PCB, with a ground plane on the bottom layer. It is simpler to manufacture but has less shielding compared to a stripline.
-
A stripline transmission line consists of a single conductor trace embedded between two ground planes. It provides better shielding and isolation but is more complex to manufacture compared to a microstrip.
-
How does impedance matching affect signal integrity in PCB transmission lines?
- Impedance matching is crucial for maintaining signal integrity in PCB transmission lines. When the impedance of the transmission line matches the impedance of the source and load, reflections are minimized, and optimal signal transfer is achieved.
-
Mismatched impedances can lead to reflections, signal distortion, and degraded signal quality, affecting the overall performance and reliability of the system.
-
What is the purpose of length matching in PCB transmission line design?
- Length matching ensures that signals traveling along different transmission lines arrive at the receivers simultaneously, preventing timing skew and maintaining signal integrity.
-
Mismatched lengths can cause signals to arrive at different times, leading to synchronization issues and potential data corruption in high-speed systems.
-
How can cross-talk be mitigated in PCB transmission lines?
- Cross-talk can be mitigated by increasing the spacing between adjacent transmission lines, using ground planes or guard traces for shielding, employing differential signaling, and optimizing the routing and placement of transmission lines to avoid parallel runs.
-
Proper design techniques, such as trace separation, shielding, and differential signaling, help reduce electromagnetic coupling and improve isolation between transmission lines.
-
What are the benefits of using simulation tools for PCB transmission line analysis?
- Simulation tools allow engineers to model and analyze the behavior of transmission lines before manufacturing the PCB, saving time and cost.
- They provide insights into impedance, propagation delay, reflections, and cross-talk, enabling designers to optimize the PCB layout and ensure robust signal integrity.
- Simulation tools help identify potential issues early in the design process, allowing for iterative improvements and reducing the risk of costly design revisions.
Conclusion
PCB transmission lines play a vital role in ensuring reliable communication and signal integrity in high-speed digital systems. By understanding the characteristics, design considerations, and analysis techniques associated with transmission lines, engineers can create robust and efficient PCB designs.
Proper design of transmission lines involves careful consideration of impedance matching, propagation delay, reflection management, and cross-talk mitigation. The choice of PCB materials, trace geometry, length matching, and via and connector design all contribute to the overall performance of the transmission lines.
Simulation and analysis tools are essential for predicting and optimizing the behavior of transmission lines before manufacturing. These tools enable engineers to identify potential issues, evaluate signal integrity, and make informed design decisions.
By following best practices and leveraging advanced simulation and analysis techniques, engineers can design PCB transmission lines that deliver reliable, high-speed communication between transmitters and receivers, ensuring the overall performance and functionality of the system.
Leave a Reply