Importance of Track to Track Spacing
Proper track to track spacing is essential for several reasons:
-
Signal Integrity: Adequate spacing between tracks helps minimize electromagnetic interference (EMI) and crosstalk between adjacent signals. This is particularly important for high-speed digital circuits and sensitive analog signals.
-
Manufacturing Feasibility: The minimum track to track spacing is limited by the capabilities of the manufacturing process. Tighter spacing requires more advanced and expensive manufacturing techniques.
-
Reliability: Insufficient track to track spacing can lead to short circuits or unintended connections between tracks, compromising the reliability and functionality of the device.
-
Design Rule Compliance: PCB and IC designs must adhere to a set of design rules that specify minimum track to track spacing based on the manufacturing process and the desired level of reliability.
Factors Affecting Track to Track Spacing
Several factors influence the minimum track to track spacing in a design:
Manufacturing Process
The manufacturing process used for PCB fabrication or IC Packaging determines the minimum achievable track to track spacing. Some common manufacturing processes and their typical minimum track to track spacing are:
Manufacturing Process | Minimum Track to Track Spacing |
---|---|
Standard PCB | 0.15 mm (6 mil) |
High-Density Interconnect (HDI) PCB | 0.075 mm (3 mil) |
IC Packaging (Wire Bonding) | 0.025 mm (1 mil) |
IC Packaging (Flip Chip) | 0.020 mm (0.8 mil) |
Signal Characteristics
The characteristics of the signals carried by the tracks also influence the required track to track spacing. High-speed signals, high-frequency signals, and signals with fast rise and fall times are more susceptible to crosstalk and EMI, requiring greater spacing between tracks.
Dielectric Material
The dielectric material used between the tracks affects the minimum track to track spacing. Materials with higher dielectric constants allow for tighter spacing, while materials with lower dielectric constants require greater spacing to maintain signal integrity.
Voltage Difference
The voltage difference between adjacent tracks also determines the minimum track to track spacing. Higher voltage differences require greater spacing to prevent arcing or breakdown of the dielectric material.
Calculating Track to Track Spacing
Track to track spacing can be calculated using various methods depending on the design requirements and the level of accuracy needed. Some common methods include:
Rule of Thumb
A quick way to estimate the minimum track to track spacing is to use a rule of thumb based on the manufacturing process. For example, a common rule of thumb for standard PCB design is to use a minimum track to track spacing of 0.15 mm (6 mil).
Empirical Formulas
Empirical formulas based on experimental data and experience can provide more accurate estimates of the required track to track spacing. One such formula is:
TT = k × (T + H)
Where:
– TT is the track to track spacing
– k is a constant that depends on the manufacturing process and the desired level of reliability (typically 0.5 to 2)
– T is the track width
– H is the track height or thickness
Simulation and Modeling
For critical designs or high-speed applications, computer-aided simulation and modeling tools can be used to accurately determine the required track to track spacing. These tools consider factors such as signal characteristics, dielectric properties, and manufacturing constraints to optimize the spacing for signal integrity and reliability.
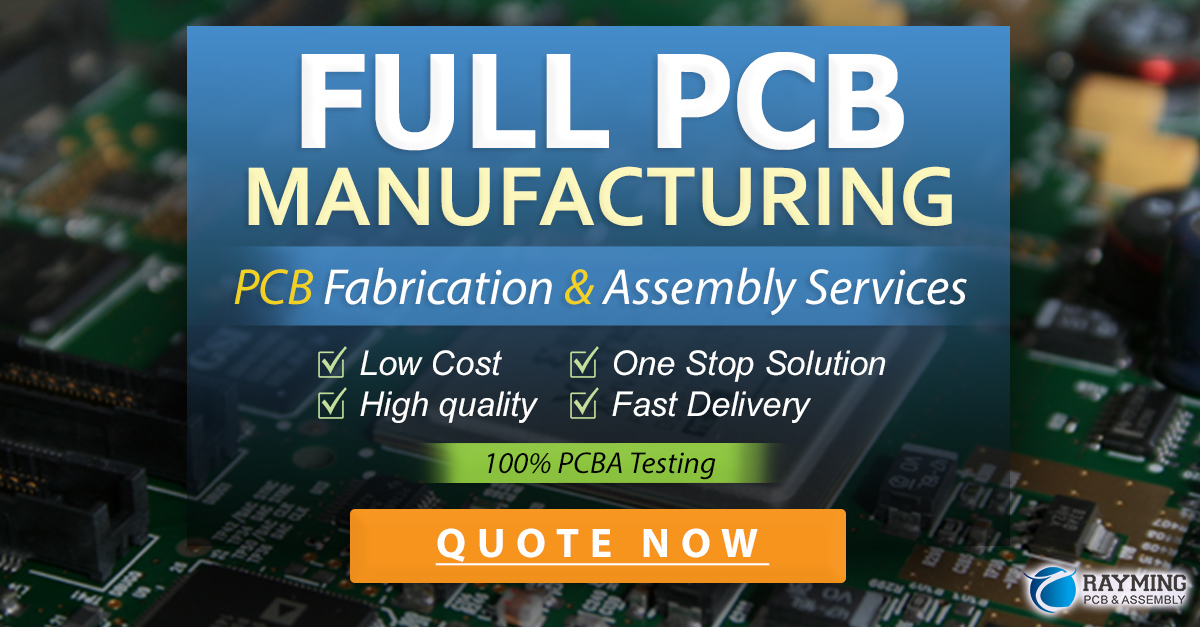
Industry Standards
Several industry standards provide guidelines and recommendations for track to track spacing in PCB and IC design. Some notable standards include:
IPC-2221
IPC-2221 is a generic standard for PCB design that provides guidelines for track to track spacing based on the voltage difference between adjacent tracks and the manufacturing process.
IPC-2226
IPC-2226 is a standard specifically for HDI PCB design that provides guidelines for track to track spacing based on the HDI technology used (microvias, buried vias, etc.) and the signal characteristics.
JEDEC Standards
The Joint Electron Device Engineering Council (JEDEC) publishes standards for IC packaging that include guidelines for track to track spacing based on the package type and the manufacturing process.
Best Practices for Track to Track Spacing
To ensure optimal signal integrity, reliability, and manufacturability, designers should follow these best practices for track to track spacing:
-
Adhere to Design Rules: Always follow the design rules specified by the PCB fabricator or IC packaging vendor, which include minimum track to track spacing requirements.
-
Consider Signal Characteristics: Provide additional spacing for high-speed, high-frequency, or sensitive signals to minimize crosstalk and EMI.
-
Use Appropriate Dielectric Materials: Select dielectric materials with suitable properties for the desired track to track spacing and signal characteristics.
-
Minimize Voltage Differences: Avoid placing tracks with large voltage differences adjacent to each other, or provide sufficient spacing to prevent arcing or dielectric breakdown.
-
Perform Simulations: Use computer-aided simulation tools to optimize track to track spacing for critical or high-speed designs.
-
Collaborate with Manufacturers: Work closely with PCB fabricators and IC packaging vendors to ensure that the designed track to track spacing is compatible with their manufacturing processes and capabilities.
Frequently Asked Questions (FAQ)
1. What is the minimum track to track spacing for a standard PCB?
The minimum track to track spacing for a standard PCB is typically 0.15 mm (6 mil), but this can vary depending on the specific manufacturing process and design requirements.
2. How does track to track spacing affect signal integrity?
Insufficient track to track spacing can lead to crosstalk and electromagnetic interference (EMI) between adjacent signals, compromising signal integrity. Adequate spacing helps minimize these effects, especially for high-speed or sensitive signals.
3. What factors determine the minimum track to track spacing in a design?
The minimum track to track spacing in a design is determined by factors such as the manufacturing process, signal characteristics, dielectric material, and voltage difference between adjacent tracks.
4. How can I calculate the required track to track spacing for my design?
Track to track spacing can be calculated using rule of thumb estimates, empirical formulas, or computer-aided simulation and modeling tools, depending on the design requirements and the level of accuracy needed.
5. What industry standards provide guidelines for track to track spacing?
Industry standards such as IPC-2221 for general PCB design, IPC-2226 for HDI PCB design, and JEDEC standards for IC packaging provide guidelines and recommendations for track to track spacing based on various factors such as manufacturing processes and signal characteristics.
Leave a Reply