Introduction to PCB Classification
Printed Circuit Boards (PCBs) are essential components in modern electronics, providing a platform for mounting and interconnecting electronic components. To ensure proper manufacturing and assembly, PCBs are classified based on various criteria, such as the number of layers, component density, and hole size. Two key aspects of PCB classification are pattern class and drill class, which define the complexity and precision of the board’s design and manufacturing process.
In this article, we will explore the concepts of pattern class and drill class in PCB classification, their importance, and how they impact the manufacturing process and end-product quality.
What is Pattern Class?
Pattern class, also known as conductor class or trace class, refers to the minimum width and spacing of the conductive traces on a PCB. It is a crucial factor in determining the manufacturing complexity and the level of precision required to produce the board.
The pattern class is defined by the IPC (Institute for Printed Circuits) standard IPC-6012, which specifies three main classes:
Class | Description |
---|---|
Class 1 | General electronic products |
Class 2 | Dedicated service electronic products |
Class 3 | High-reliability electronic products |
Each class has its own set of requirements for minimum trace width and spacing, as well as other design parameters such as Annular Ring size and via diameter.
Class 1 Pattern
Class 1 pattern is the least stringent of the three classes and is suitable for general electronic products where the consequences of failure are not critical. Examples include consumer electronics, toys, and low-cost appliances.
The minimum trace width and spacing for Class 1 pattern are:
Feature | Minimum Size |
---|---|
Trace width | 0.2 mm (8 mil) |
Trace spacing | 0.2 mm (8 mil) |
Class 2 Pattern
Class 2 pattern is designed for dedicated service electronic products, where extended life and continuous performance are required. Applications include telecommunications equipment, industrial controls, and automotive electronics.
The minimum trace width and spacing for Class 2 pattern are:
Feature | Minimum Size |
---|---|
Trace width | 0.15 mm (6 mil) |
Trace spacing | 0.15 mm (6 mil) |
Class 3 Pattern
Class 3 pattern is reserved for high-reliability electronic products, where failure could result in significant economic loss or risk to human life. Examples include aerospace systems, medical devices, and military equipment.
The minimum trace width and spacing for Class 3 pattern are:
Feature | Minimum Size |
---|---|
Trace width | 0.1 mm (4 mil) |
Trace spacing | 0.1 mm (4 mil) |
What is Drill Class?
Drill class refers to the categorization of hole sizes and tolerances on a PCB. It is an essential aspect of PCB classification, as it determines the precision and accuracy required for drilling holes for through-hole components, vias, and mounting holes.
The drill class is defined by the IPC standard IPC-6012, which specifies three main classes:
Class | Description |
---|---|
Class 1 | General electronic products |
Class 2 | Dedicated service electronic products |
Class 3 | High-reliability electronic products |
Each class has its own set of requirements for hole size tolerances, which become more stringent as the class number increases.
Class 1 Drill
Class 1 drill is suitable for general electronic products where the consequences of failure are not critical. The hole size tolerances for Class 1 drill are:
Hole Size | Tolerance |
---|---|
≤ 0.8 mm (31 mil) | ± 0.1 mm (4 mil) |
> 0.8 mm (31 mil) | ± 0.15 mm (6 mil) |
Class 2 Drill
Class 2 drill is designed for dedicated service electronic products, where extended life and continuous performance are required. The hole size tolerances for Class 2 drill are:
Hole Size | Tolerance |
---|---|
≤ 0.5 mm (20 mil) | ± 0.08 mm (3 mil) |
> 0.5 mm (20 mil) | ± 0.1 mm (4 mil) |
Class 3 Drill
Class 3 drill is reserved for high-reliability electronic products, where failure could result in significant economic loss or risk to human life. The hole size tolerances for Class 3 drill are:
Hole Size | Tolerance |
---|---|
≤ 0.3 mm (12 mil) | ± 0.05 mm (2 mil) |
> 0.3 mm (12 mil) | ± 0.08 mm (3 mil) |
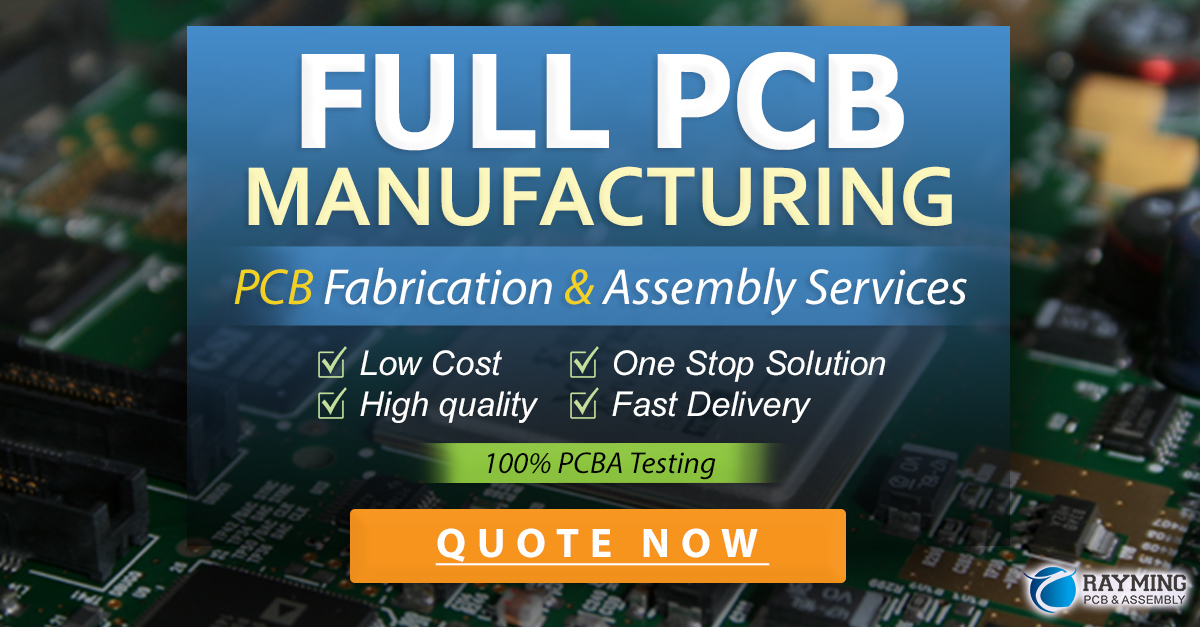
The Importance of Pattern Class and Drill Class in PCB Manufacturing
Pattern class and drill class play a crucial role in the PCB manufacturing process, as they directly impact the design, fabrication, and assembly of the board.
Design Considerations
When designing a PCB, engineers must consider the pattern class and drill class requirements based on the intended application and the level of reliability needed. Choosing the appropriate class ensures that the board’s design is compatible with the manufacturing capabilities and meets the necessary performance criteria.
For example, a Class 3 pattern with fine traces and tight spacing may be required for a high-density, high-reliability PCB used in aerospace applications. In contrast, a Class 1 pattern may be sufficient for a low-cost consumer electronic device.
Fabrication Process
The pattern class and drill class also influence the PCB fabrication process. Higher class numbers require more advanced manufacturing techniques, tighter process controls, and specialized equipment to achieve the necessary precision and accuracy.
For instance, producing a Class 3 pattern may require the use of high-resolution photoplots, advanced etching techniques, and strict quality control measures to ensure that the fine traces and spaces are correctly formed. Similarly, drilling holes for a Class 3 board may require the use of high-precision drilling machines and frequent tool changes to maintain the tight tolerances.
Assembly and Reliability
The choice of pattern class and drill class also impacts the assembly process and the overall reliability of the PCB. Higher class numbers generally result in more precise and accurate component placement, as well as better electrical performance and reliability.
For example, a Class 3 drill with tight hole size tolerances ensures that through-hole components fit securely and make reliable electrical connections. This is particularly important for high-reliability applications where failure could have severe consequences.
Factors Influencing the Choice of Pattern Class and Drill Class
When selecting the appropriate pattern class and drill class for a PCB, several factors must be considered:
-
Application requirements: The intended use of the PCB and the level of reliability required are the primary factors in determining the pattern and drill class. High-reliability applications, such as aerospace and medical devices, typically require Class 3, while general consumer electronics may only need Class 1.
-
Component density: The density of components on the PCB influences the choice of pattern class. Higher-density boards with fine-pitch components may require a higher pattern class to accommodate the smaller trace widths and spacings.
-
Manufacturing capabilities: The available manufacturing technologies and equipment at the PCB fabrication facility must be considered when choosing the pattern and drill class. Some facilities may not have the capability to produce high-class boards with very fine features and tight tolerances.
-
Cost considerations: Higher pattern and drill classes generally result in higher manufacturing costs due to the need for advanced equipment, materials, and process controls. The cost of the PCB must be balanced against the reliability and performance requirements of the application.
FAQ
-
What is the difference between pattern class and drill class in PCB classification?
Pattern class refers to the minimum width and spacing of the conductive traces on a PCB, while drill class refers to the categorization of hole sizes and tolerances on a PCB. -
What are the three main classes for pattern and drill in PCB classification?
The three main classes for both pattern and drill in PCB classification are Class 1 (general electronic products), Class 2 (dedicated service electronic products), and Class 3 (high-reliability electronic products). -
How does the choice of pattern class and drill class affect the PCB manufacturing process?
The choice of pattern class and drill class directly impacts the design, fabrication, and assembly of the PCB. Higher class numbers require more advanced manufacturing techniques, tighter process controls, and specialized equipment to achieve the necessary precision and accuracy. -
What factors should be considered when selecting the appropriate pattern class and drill class for a PCB?
Factors to consider when selecting the appropriate pattern class and drill class include the application requirements, component density, manufacturing capabilities, and cost considerations. -
Can a PCB have different pattern and drill classes for different layers or sections?
Yes, a PCB can have different pattern and drill classes for different layers or sections, depending on the specific design requirements and the complexity of the board. This is known as a hybrid PCB, where different classes are used to optimize performance, reliability, and cost.
Conclusion
PCB classification based on pattern class and drill class is essential for ensuring the proper design, manufacturing, and assembly of printed circuit boards. Understanding the differences between the classes and their impact on the manufacturing process and end-product quality is crucial for engineers, designers, and manufacturers.
By selecting the appropriate pattern and drill class for a given application, considering factors such as reliability requirements, component density, manufacturing capabilities, and cost, PCB designers and manufacturers can optimize the performance and reliability of the final product while minimizing costs and production challenges.
As electronic devices continue to advance and become more complex, the importance of accurate PCB classification and adherence to industry standards will only continue to grow. By staying informed about the latest developments in PCB classification and manufacturing technologies, professionals in the electronics industry can ensure the production of high-quality, reliable PCBs that meet the ever-increasing demands of modern applications.
Leave a Reply