Why are PCB tolerances Important?
PCB Tolerances play a crucial role in the success of your electronic device for several reasons:
- Functionality: Proper tolerances ensure that components fit correctly and the PCB functions as designed.
- Reliability: Tight tolerances help maintain consistent performance and reliability of the PCB over time.
- Manufacturability: Achievable tolerances determine the ease and cost of manufacturing the PCB.
- Cost: Tighter tolerances often increase manufacturing costs, so it’s essential to specify tolerances that meet your needs without unnecessarily driving up expenses.
Types of PCB Tolerances
There are several categories of tolerances to consider when designing a PCB:
Dimensional Tolerances
Dimensional tolerances refer to the acceptable variations in the physical dimensions of the PCB, such as:
- Board size and thickness
- Hole sizes and positions
- Line widths and spacings
- Copper feature sizes
These tolerances are typically specified in millimeters (mm) or mils (thousandths of an inch).
Board Size and Thickness Tolerances
The table below shows typical tolerances for PCB size and thickness:
Dimension | Tolerance |
---|---|
Board Size (X, Y) | ±0.25 mm |
Board Thickness (1-2 mm) | ±10% |
Board Thickness (>2 mm) | ±20% |
Hole Size and Position Tolerances
Hole tolerances depend on the hole size and type (plated or non-plated):
Hole Type | Hole Size (mm) | Tolerance (mm) |
---|---|---|
Plated | 0.2 – 0.5 | ±0.08 |
0.5 – 1.0 | ±0.10 | |
1.0 – 2.0 | ±0.15 | |
Non-Plated | 0.5 – 1.0 | ±0.10 |
1.0 – 2.0 | ±0.15 |
Position tolerance for holes is typically ±0.1 mm.
Material Tolerances
Material tolerances relate to the acceptable variations in the properties of the materials used in PCB fabrication, including:
- Substrate (e.g., FR-4) thickness and dielectric constant
- Copper foil thickness and conductivity
- Solder mask thickness and color
- Silkscreen thickness and color
For example, FR-4 substrate thickness tolerance is typically ±10%, while copper foil thickness tolerance is ±5%.
Process Tolerances
Process tolerances encompass the acceptable variations in the various manufacturing processes used to fabricate the PCB, such as:
- Etching and plating uniformity
- Solder mask registration and adhesion
- Silkscreen registration and durability
- Surface finish quality (e.g., HASL, ENIG, OSP)
These tolerances are often specified as a percentage of the nominal value or as a minimum/maximum acceptable range.
Specifying PCB Tolerances
When designing your PCB, it’s essential to clearly communicate your tolerance requirements to your manufacturer. This is typically done through notes and callouts on your fabrication drawings or by providing a separate tolerance specification document.
Some key considerations when specifying tolerances:
- Be realistic: Specify tolerances that are achievable by your chosen manufacturer and appropriate for your application. Overly tight tolerances can increase costs and lead times.
- Prioritize critical features: Focus on specifying tight tolerances for features that are most critical to your PCB’s functionality and reliability.
- Use industry standards: Refer to industry standards, such as IPC-6012, for guidance on typical tolerance values for different PCB classes and applications.
- Communicate with your manufacturer: Discuss your tolerance requirements with your PCB manufacturer early in the design process to ensure they are feasible and to identify any potential issues.
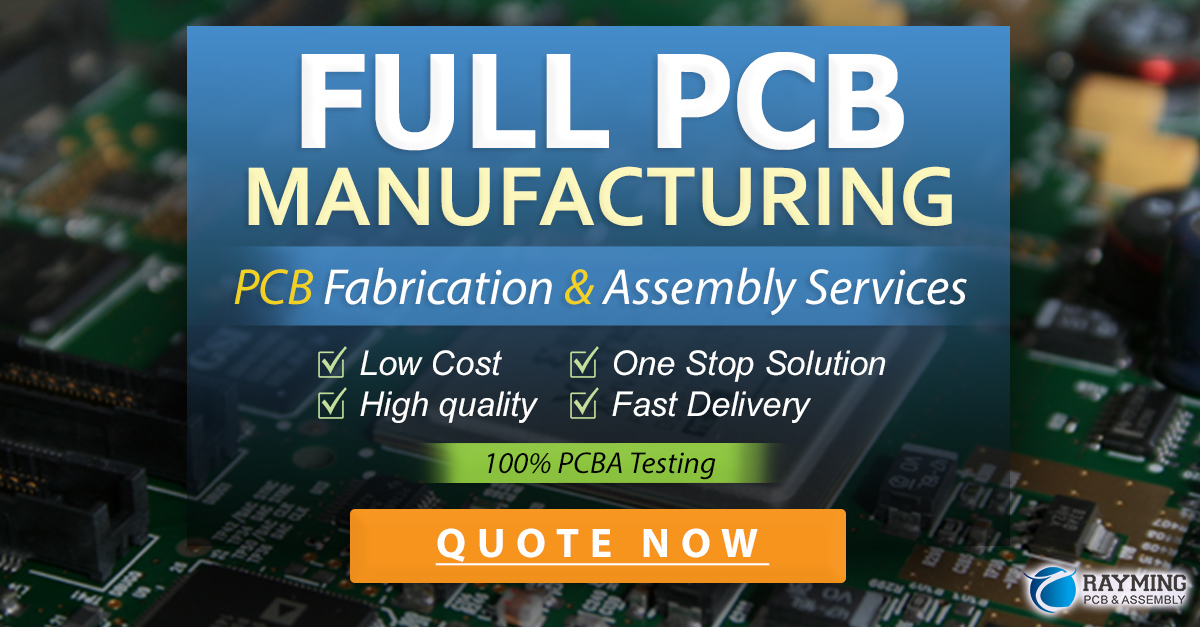
Factors Affecting PCB Tolerances
Several factors can impact the achievable tolerances in PCB manufacturing, including:
- Manufacturing capabilities: Different PCB manufacturers have varying capabilities in terms of equipment, processes, and expertise, which can affect the tolerances they can achieve.
- Material properties: The properties of the materials used in PCB fabrication, such as substrate type, copper weight, and solder mask type, can influence the achievable tolerances.
- PCB complexity: More complex PCB designs with high layer counts, dense component placement, and fine pitch features may require tighter tolerances and be more challenging to manufacture.
- Volume and lead time: Higher volume orders and longer lead times may allow for tighter tolerances due to improved process control and the ability to fine-tune the manufacturing process.
Best Practices for Managing PCB Tolerances
To effectively manage PCB tolerances and ensure a successful product, consider the following best practices:
- Design for manufacturability: Design your PCB with manufacturing tolerances in mind from the outset, ensuring that your design is compatible with the capabilities of your chosen manufacturer.
- Use CAD tools: Leverage CAD tools with built-in design rule checks (DRCs) to ensure your design meets your specified tolerances and to catch any potential issues early in the design process.
- Communicate clearly: Provide clear and comprehensive tolerance specifications to your manufacturer, and maintain open communication throughout the manufacturing process to address any questions or concerns.
- Prototype and test: Build prototypes of your PCB and thoroughly test them to validate your design and tolerance specifications before proceeding with full-scale production.
- Monitor and adjust: Continuously monitor the quality and consistency of your PCBs during production, and be prepared to make adjustments to your design or tolerances if needed to optimize performance and reliability.
FAQ
What are the most critical PCB tolerances to consider?
The most critical PCB tolerances depend on your specific application and design requirements. However, some of the most commonly critical tolerances include:
- Hole sizes and positions for component mounting
- Line widths and spacings for signal integrity and current carrying capacity
- Copper feature sizes for fine-pitch components and high-density designs
- Solder mask registration for proper insulation and protection
How do I know what tolerances my PCB manufacturer can achieve?
The best way to determine your PCB manufacturer’s capabilities is to discuss your specific requirements with them directly. Most manufacturers will provide a capabilities document or design guide that outlines their standard tolerances for different PCB features and processes. They can also advise you on what tolerances are achievable for your specific design and provide guidance on how to optimize your design for manufacturability.
Can I request tighter tolerances than the manufacturer’s standard offerings?
In many cases, yes, you can request tighter tolerances than the manufacturer’s standard offerings. However, this will likely come at an increased cost and may require additional lead time. It’s important to discuss your specific needs with your manufacturer and weigh the benefits of tighter tolerances against the potential impact on cost and schedule.
What should I do if my PCB fails to meet the specified tolerances?
If your PCB fails to meet the specified tolerances, the first step is to communicate with your manufacturer to determine the root cause of the issue. They may need to adjust their processes or materials to bring the PCBs into compliance. In some cases, you may need to modify your design to accommodate the manufacturer’s capabilities or switch to a different manufacturer that can meet your requirements. It’s important to address any tolerance issues as early as possible to minimize the impact on your project timeline and budget.
How can I ensure consistent tolerances across multiple PCB production runs?
To ensure consistent tolerances across multiple PCB production runs, it’s important to:
- Clearly communicate your tolerance requirements to your manufacturer and ensure they are documented in your specifications and contracts.
- Use statistical process control (SPC) techniques to monitor key process parameters and detect any deviations from your specified tolerances.
- Conduct regular quality audits and inspections of your PCBs to verify that they meet your requirements.
- Maintain open communication with your manufacturer and address any issues or concerns promptly.
- Consider using the same manufacturer for multiple production runs to minimize variability and ensure consistent process control.
Conclusion
Understanding and properly specifying manufacturing tolerances is essential for ensuring the functionality, reliability, and manufacturability of your PCB. By considering the different types of tolerances, communicating clearly with your manufacturer, and following best practices for managing tolerances throughout the design and production process, you can minimize issues and ensure the success of your electronic device.
Remember, PCB tolerances are not one-size-fits-all – they must be tailored to your specific application and design requirements. Work closely with your PCB manufacturer to determine the appropriate tolerances for your project and optimize your design for manufacturability. With a solid understanding of PCB tolerances and a commitment to quality control, you can bring your electronic vision to life with confidence.
Leave a Reply