What is PCB tolerance?
PCB tolerance is the acceptable range of deviation from the ideal or specified dimensions and placement of features on a printed circuit board. These features include the size and location of holes, pads, traces, and other elements on the PCB. The tolerance is usually expressed as a plus or minus (±) value, indicating the maximum allowable variation from the nominal value.
For example, if a hole on a PCB has a specified diameter of 1.0 mm with a tolerance of ±0.1 mm, the actual diameter of the hole can range from 0.9 mm to 1.1 mm and still be considered acceptable.
Factors Affecting PCB Tolerance
Several factors can influence the tolerance of a PCB, including:
-
Manufacturing process: Different PCB manufacturing processes, such as etching, drilling, and plating, have their own inherent limitations and variability.
-
Material properties: The properties of the PCB substrate material, such as thermal expansion and contraction, can affect the dimensional stability of the board.
-
Board complexity: More complex PCB designs with higher component density, smaller feature sizes, and multiple layers may require tighter tolerances.
-
Environmental conditions: Temperature, humidity, and other environmental factors can cause PCBs to expand, contract, or warp, affecting the tolerance.
Typical PCB Tolerances
The typical tolerances for PCBs can vary depending on the specific application, manufacturing process, and design requirements. However, there are some general guidelines for common PCB features:
Feature | Typical Tolerance |
---|---|
Hole diameter | ±0.1 mm |
Hole position | ±0.1 mm |
Pad size | ±0.05 mm |
Trace width | ±0.05 mm |
Trace spacing | ±0.05 mm |
Board thickness | ±10% |
Board outline | ±0.2 mm |
It’s important to note that these are just general guidelines, and the actual tolerances for a specific PCB may differ based on the design requirements and the capabilities of the manufacturing process.
IPC Standards for PCB Tolerances
The IPC (Association Connecting Electronics Industries) is a global trade association that develops standards for the electronic interconnection industry. IPC standards provide guidelines for PCB design, fabrication, and assembly, including recommendations for tolerances.
Some of the relevant IPC standards for PCB tolerances include:
- IPC-6012: Generic Performance Specification for Rigid Printed Boards
- IPC-6013: Qualification and Performance Specification for Flexible Printed Boards
- IPC-6018: Microwave End Product Board Inspection and Test
- IPC-2221: Generic Standard on Printed Board Design
These standards provide detailed information on the recommended tolerances for various PCB features based on the board type, class, and performance requirements.
Importance of PCB Tolerance
Maintaining appropriate PCB tolerances is crucial for several reasons:
-
Functionality: Proper tolerances ensure that components fit correctly and make reliable connections, enabling the PCB to function as intended.
-
Compatibility: Consistent tolerances allow for the interchangeability of components and the integration of PCBs into larger systems.
-
Manufacturing efficiency: Well-defined tolerances help streamline the PCB manufacturing process, reducing the likelihood of errors and improving yield.
-
Cost-effectiveness: Achieving the right balance between tight tolerances and manufacturing feasibility helps minimize production costs while maintaining the required level of quality.
Designing for PCB Tolerance
When designing a PCB, it’s essential to consider the tolerances of various features to ensure manufacturability and functionality. Some best practices for designing with tolerances in mind include:
-
Communicate with the manufacturer: Discuss your tolerance requirements with the PCB manufacturer early in the design process to ensure they can meet your needs.
-
Use standard components: Whenever possible, select components with standard sizes and tolerances to simplify the design and manufacturing process.
-
Provide clear documentation: Include detailed tolerance information in your PCB design files and fabrication drawings to avoid ambiguity and misinterpretation.
-
Consider assembly requirements: Ensure that the tolerances of your PCB design are compatible with the assembly process, including the placement and soldering of components.
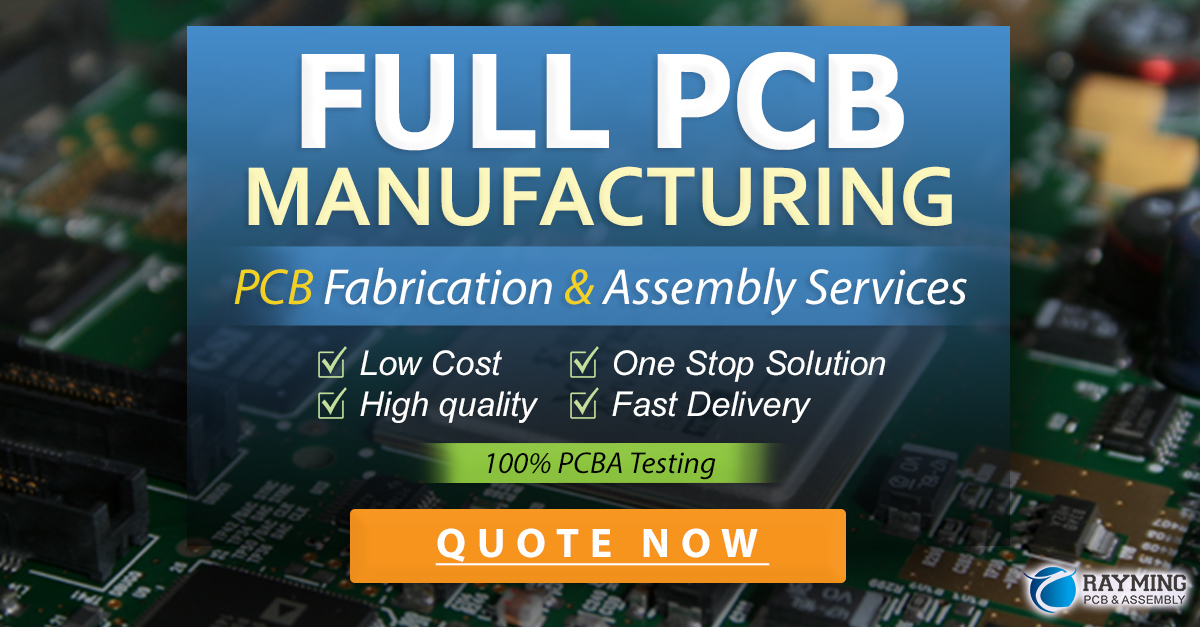
Tolerance Stack-Up Analysis
Tolerance stack-up analysis is a method used to determine the cumulative effect of individual tolerances on the overall dimensions and placement of features on a PCB. This analysis helps designers and manufacturers identify potential issues and ensure that the final assembled product meets the required specifications.
The stack-up analysis considers the tolerances of various elements, such as:
- PCB substrate dimensions
- Copper foil thickness
- Solder mask thickness
- Drill hole size and position
- Component placement
By combining the tolerances of these elements, designers can predict the worst-case scenario and make necessary adjustments to the design or tolerances to ensure proper fit and function.
Tools for Tolerance Stack-Up Analysis
Several software tools are available to assist with tolerance stack-up analysis, including:
-
Altium Designer: A PCB design software that includes a built-in tolerance stack-up analysis tool.
-
Cadence Allegro: A PCB design solution that offers tolerance analysis capabilities through its Constraint Manager.
-
Mentor Graphics PADS: A PCB design software with a tolerance stack-up analysis feature in its Professional edition.
-
Tolerance StackUp: A standalone tolerance analysis software that integrates with various CAD systems.
These tools help designers visualize and analyze the impact of tolerances on their PCB designs, enabling them to make informed decisions and optimize the design for manufacturability.
Frequently Asked Questions (FAQ)
- What happens if the tolerances on a PCB are too tight?
-
If the tolerances on a PCB are too tight, it can lead to increased manufacturing costs and reduced yields. Tight tolerances may require specialized equipment, more precise processes, and additional quality control measures, which can drive up production costs. Additionally, overly tight tolerances can result in a higher rejection rate of boards that fail to meet the specified requirements, reducing the overall manufacturing yield.
-
Can PCB tolerances be adjusted during the manufacturing process?
-
In some cases, PCB tolerances can be adjusted during the manufacturing process to compensate for variations or to meet specific requirements. For example, if a hole is drilled slightly off-center, the manufacturer may be able to adjust the pad size or position to ensure proper component fit. However, such adjustments are limited and may not be feasible for all types of tolerance deviations. It’s always best to design the PCB with appropriate tolerances from the outset.
-
How do I choose the right tolerances for my PCB design?
-
Choosing the right tolerances for your PCB design depends on several factors, including the complexity of the board, the components used, the manufacturing process, and the end-use requirements. It’s essential to consult with the PCB manufacturer and refer to relevant industry standards (such as IPC) to determine the appropriate tolerances for your specific application. In general, it’s a good practice to use the widest acceptable tolerances that still meet your design requirements to minimize manufacturing costs and improve yields.
-
What are the consequences of using components with different tolerances on the same PCB?
-
Using components with different tolerances on the same PCB can lead to compatibility issues and assembly challenges. If the tolerances of the components do not match the tolerances of the PCB features, such as holes or pads, it can result in poor fit, misalignment, or difficulty in soldering. This can cause mechanical stress, electrical disconnections, or reduced reliability of the assembled board. To avoid these issues, it’s important to select components with tolerances that are compatible with the PCB design and manufacturing process.
-
How can I communicate my PCB tolerance requirements to the manufacturer?
- To effectively communicate your PCB tolerance requirements to the manufacturer, you should provide clear and detailed documentation in your design files and fabrication drawings. This documentation should include the nominal dimensions and tolerances for all critical features, such as holes, pads, traces, and board outline. Use standard notation and symbols to express the tolerances, and make sure to discuss any special requirements or deviations with the manufacturer before finalizing the design. Additionally, consider using a PCB design software that supports the generation of comprehensive manufacturing files, such as Gerber files and drill files, which include the necessary tolerance information.
Conclusion
PCB tolerance is a critical aspect of printed circuit board design and manufacturing. It refers to the acceptable range of deviation from the ideal dimensions and placement of features on a PCB. Maintaining appropriate tolerances is essential for ensuring the functionality, compatibility, and reliability of electronic devices.
Typical PCB tolerances can vary based on the specific application, manufacturing process, and design requirements. Industry standards, such as those developed by IPC, provide guidelines for recommended tolerances based on board type and performance criteria.
Designers must consider tolerances when creating PCB layouts to ensure manufacturability and assembly compatibility. Tolerance stack-up analysis is a valuable tool for predicting the cumulative effect of individual tolerances on the final assembled product.
By understanding the importance of PCB tolerance, designing with tolerances in mind, and effectively communicating requirements to manufacturers, designers can optimize their PCB designs for cost-effectiveness, reliability, and overall success in the electronic interconnection industry.
Leave a Reply